Extreme drilling drives drill pipe innovations
Advances target higher-strength materials, improved hole cleaning, wear life, hydraulic performance
By Katie Mazerov, Contributing Editor
Drill pipe, like everything else in well construction, is rapidly evolving to match an ever-expanding operational window. Whether operators are drilling longer laterals in resource plays, launching high-stakes exploration drives into ultra-deepwater or venturing into extreme environments characterized by H2S, high pressures, high temperatures and permafrost, drill pipe remains the fundamental enabler. Stronger tubulars, tougher, higher-torque connections, and hardbanding designed with properties and metallurgies for greater robustness and longevity are all in high demand.
Market conditions, including cost and supply constraints, are driving a healthy used drill pipe business in some sectors. At the other end of the spectrum, adoption of wired drill pipe continues to edge up, primarily in the North Sea and in US unconventionals.

“The past decade has seen an extension of the drilling envelope, with more projects involving extended-reach wells and ultra-deep reservoirs where torque and drag and tensile capacity are a significant concern,” said Vincent Flores, Global Product Line Manager for Vallourec Drilling Products. The company is a part of Vallourec Group.
“From a manufacturing perspective, we have responded by developing high-grade steel with minimum strength that exceeds what existing standards mandate, as well as high-torque connections,” Mr Flores said. Advances include development of heavy-duty landing strings for the growing ultra-deepwater market. In those environments, 12,000-ft water depths and increasingly longer well profiles are requiring larger and heavier landing strings and slips with hookloads approaching or exceeding 2.5 million lb.
“Conventional landing strings can’t withstand the higher hookloads due to slip-crushing, a phenomenon that can cause the pipe to crush or collapse, reducing the axial tension load of the string,” he explained. The CrushFree landing string, commercialized late last year, is designed with more tension capacity (165 ksi specified minimum yield strength) to resist slip-crushing by increasing resistance on the pipe where slips are set. The string, which offers resistance up to 2.5 million lb, is particularly suited for ultra-deepwater basins, including the pre-salts of Brazil and Angola.
For the onshore unconventionals market, new products are being designed for improved hole cleaning and wear resistance, as well as enhanced hydraulics to drill the lateral sections. “Tools that improve hole cleaning and hydraulics, such as 4 ¼-in. drill pipe or other innovative hole-cleaning technologies used in shale development, are a priority for operators,” Mr Flores said.
Vallourec has targeted much of its drilling-product development to extreme environments, including the Arctic and the growing H2S market. “The biggest challenge in low-temperature environments is ensuring products can resist low temperatures during storage and handling, not necessarily while drilling when fluids are circulating,” he said. “We have designed drill pipe with new chemistries and grades that have high-impact resistance at permafrost temperatures, and we are developing similar products for bottomhole assembly (BHA) components, which are prone to the same issues.”
New sour-gas grades
The growing number of H2S-prone reservoirs also has spawned new steel grades over the past 10 years. “With demand for domestic oil and gas increasing in several regions, especially in the Middle East and Asia, we are seeing a lot of exploration in fields with a high content of sour gas combined with HPHT conditions,” Mr Flores noted. Since 2013, Vallourec has developed two high-strength steel grades with enough tensile capacity to drill complex well profiles, including extended-reach and deep wells, in sour-gas environments.

Particularly in the Middle East, Asia and Canada, he added, H2S content in some reservoirs can top 20%, pushing the limits of existing steel grades. Vallourec is testing a new sour-service grade, VM 105 DP SS+, in various corrosive environments. The grade is designed with enhanced safety margins, such as additional NACE testing to reduce the risk of sulfide stress cracking (SSC) failure in case the drill string is exposed to sour gas, Mr Flores said. The product, which will be introduced later this year, is being tested under tension and exposed to varying thresholds of sour gas for a month at a time.
The company is also ramping up service support, as this is often the greatest factor that can lead to project success, he continued. This is especially the case in remote regions like the Arctic. Vallourec continues to expand its worldwide licensing network by certifying local repair shops to provide after-sales support, such as re-cutting connections.
Looking ahead, Mr Flores said the growth of the ultra-deepwater market will drive development of landing string capacity above 2.5 million lb of hookload. “We also will need to look at many other onshore needs, including how our products can be used in an efficient way on automated rigs, as the industry slowly but surely moves in that direction.”
National Oilwell Varco (NOV) Grant Prideco is focusing R&D efforts on connections and metallurgy, two areas where there has been significant advancement in the past decade, said Michael Jellison, Senior VP of Engineering. “Strength is a big issue, especially in the deepwater market, where the operational envelope is evolving quickly.”
Several years ago, Grant Prideco introduced a material with a minimum yield strength of 150,000 psi for specialized, higher-strength strings required to land long, heavy casing or install subsea trees in deepwater wells. The company has since developed a material with 165,000-psi yield strength for 6 5/8-in. outer diameter (OD) strings with a wall thickness of approximately 1 in. and tension ratings around 2.5 million to 2.6 million lb. Other ODs and wall thicknesses can be provided with 165,000-psi minimum yield strength. “We’re already pushing the limits of the 165,000 yield strength materials,” he said. “There are ongoing projects where operators are planning jobs in excess of 2 million lb of hookload.”

Connections for deepwater, pad drilling
Deepwater is also a target market for Grant Prideco’s eXtreme Torque (XT), TurboTorque (TT) and the new uLtimate series of high-performance connections that provide increased torsional strength and enhanced capability to run pipe more quickly. “The connections are designed with a slimmer profile that allows us to open the inside diameter of the pipe and reduce the outside diameter to provide better hydraulic performance to drill wells more efficiently,” Mr Jellison explained.
The connections are being used in shale and other unconventional formations as operators push to drill wells in as few days as possible. Pad drilling campaigns, for example, can cause more wear on pipe and connections. “Economics is driving the trend, but we focus on the total well cost, not just the cost of the drill pipe. By using advanced drill pipe with the XT and our other high-performance connections, we can drill wells faster and maintain a safe operating environment,” he noted.
XT and TT connections provide the capability to run 4-in. drill pipe as part of well designs that normally would be relegated to 3 ½-in. pipe. “The connection has the same outer dimensions as used with 3 ½-in. drill pipe. This, combined with the higher torsional strength of the connection, allows it to be used on 4-in. pipe for faster drilling,” Mr Jellison said. “The larger internal diameter (ID) enables better hydraulics and the ability to enhance cuttings removal from the well, resulting in better penetration rates. For a lot of the shale plays, the 4-in. drill pipe size combined with XT39 has been the drill string and connection of choice.”
Micro-alloying, the process of adding minute amounts of specific elements, such as Niobium and Titanium, to the steel, can deliver significant improvement in performance without a huge cost increase, he continued. “It’s also important to make materials with good toughness, using the correct composition of alloy components and proper heat-treating process to improve toughness and reduce brittleness. As steel becomes stronger, there is a propensity for it to become brittle and subject to cracks forming and spreading. A lot of pipe failures are the result of fatigue and cracking problems.”

Grant Prideco manufactures three designs of heavy-weight drill pipe – standard, for general applications, as well as Tri-Spiral and Spiral-Wate – to reduce differential sticking tendencies, improve hole cleaning and promote better circulation in difficult drilling environments.
“Heavy-weight drill pipe designs have properties that are not as stiff as the drill collars yet are stiffer than conventional pipe and, therefore, serve as a transition section to reduce fatigue failure in the pipe,” Mr Jellison said. “For directional drilling, operators may run heavy-weight pipe higher up in the string for added weight to help push the bit through the curved and deviated/horizontal sections of the well and stabilize the drill string.”
In unconventional wells, drill pipe will often buckle in the lateral sections because it is under compression, rather than tension, from the force being applied. “With the emergence of unconventional plays and the explosion of horizontal drilling in the last 10 years in the US, we are seeing drill pipe positioned closer to the bit and heavy-weight pipe used in the vertical and build sections to put more weight on the bit, with few, if any, drill collars,” said Jorge Bejar, VP of Sales, Marketing and Business Development for Rotary Drilling Tools (RDT), a manufacturer of API-certified and premium drilling and completion tubulars. “This practice of trying to cram as much weight as possible to the bit from the surface can be very detrimental to the drill pipe, causing damage and premature wear to the OD of the pipe.”
Click here to read related article, “Hardbanding alloys, application methods evolve to meet demands of intensive pad drilling campaigns.”
Extending wear life
Premature pipe wear was the driver for the development of RDT’s Wear-Knot Drill Pipe, designed to function under compression and tension conditions downhole. The pipe is built with an extra inch of wall thickness, or a knot, welded onto the middle section, creating a stabilization point that minimizes buckling and reduces drag and friction forces. The extra thickness also extends its service life by preventing premature wear that occurs frequently with conventional thin-walled pipe when it scrapes against the wall of the hole, Mr Bejar explained.
Since it was introduced 2 ½ years ago in the Bakken, Wear-Knot has been applied across US shale plays and soon will be deployed onshore Colombia. The technology also recently received its first offshore contract, for a pre-salt well in Brazil. In the Bakken, a play characterized by hard, abrasive formations, the same Wear-Knot pipe, used in conjunction with premium pipe connections and heavy-weight pipe, has been used to drill more than 15 20,000-ft wells with minimal loss. The pipe is still in use, according to RDT.
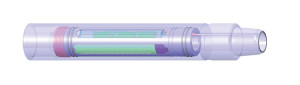
Because it eliminates the helical buckling seen in conventional pipe, the pipe also reduces wear and tear on mud motors, Mr Bejar added. For wear protection, this pipe uses only casing-friendly hardbanding material on both pin and box tool joint areas and in the Wear-Knot sections, he said.
More corrosive environments
TSC Drill Pipe, a division of Texas Steel Conversion, plans to introduce new drill string products over the next three years as part of a capital expansion program. The expansion target drill pipe and connections for extended-reach drilling, harsh-environment shale plays and even conventional drilling markets where operators are looking to optimize overall project economics, according to Mark Garrett, Senior Sales Engineer.

“Every wellbore presents its own challenges. However, trends increasingly common to all regions include exposure to corrosive environments and a market demand on drillers to reduce the cost per foot drilled,” he said. “Today’s drill pipe must be able to perform under higher torque loads in both tension and compression, withstand longer exposure to abrasive and corrosive environments and perform with high durability and long wear life to minimize the need for frequent field inspections and repairs. Assurance of this high level of performance requires products to be manufactured from high-quality engineered materials and controlled processes.”
He noted that TSC Drill Pipe is seeing a significant increase in demand for high-performance premium connections, especially the company’s high-torque PTech+ connection, in slim-hole production designs. “As operators drill longer laterals, going out 12,000 to 14,000 ft, more torque is required to turn the bit, BHA and directional drilling equipment from the surface,” said Danny Cruzan, Sales Manager.
The PTech+ connection provides increased torque while maintaining a streamlined geometric configuration with a smaller OD and larger ID, making it suitable for highly deviated trajectories, including doglegs. The design results in fewer repairs, reducing overall drilling costs, Mr Cruzan said.
Besides the US, the Middle East has been another strong market for this connection, fueled by sour-gas reservoirs, Mr Cruzan said. For sour-service applications, the company manufactures three products for H2S-bearing formations: controlled yield (TSC-CY), sour service (TSC-SS) and industry-recommended practice-compliant SS for Canada.
Each design incorporates a different level of SSC testing, and all include specialized materials and controlled heat treatment processes, Mr Garrett explained. “SSC failures in steel drill pipe can occur in environments where stress and H2S gas are present. SSC occurs when atomic hydrogen diffuses into the steel, promoting localized increases in stress and a degradation of material properties. Although there are many related environmental factors, it is generally recognized that higher-strength, or higher-hardness, steels have higher susceptibility to SSC.”
Depending on the formation and type of drilling, pipe and connections typically last from two to eight years, with periodic inspection, re-threading of the connections and hardbanding, Mr Cruzan said. Over the past two years, TSC Drill Pipe has doubled the number of its licensees in the field offering repair services for both standard and proprietary downhole products, he said. Currently, licensees are located throughout the major shale plays in North America, as well as in Australia, Indonesia, Oman and Qatar.

Drive for efficiency
With the industry’s drive for improved efficiency, wired drill pipe (WDP) is seeing increased uptake. “In the past, WDP was used primarily for applications where conventional telemetry was unfeasible, or where high-definition downhole information was required,” said Andrew Craig, VP of Business Development for NOV IntelliServ. “Now we’re seeing greater adoption of this technology as the industry drives for greater efficiencies due to high offshore rig rates and competitive economics in the onshore sector.”
IntelliServ commercially released the second generation of its WDP system in Q1 this year. IntelliServ2 delivers improved data communication reliability and increases the robustness and durability of the inductive coils, which are placed in each connection of wired tubulars. The new coils are mechanically decoupled from the connection, enabling signal transmission even if the connection becomes damaged. The coils are also removable and re-usable, which eliminates the need for replacement with each connection re-cut, reducing overall maintenance costs.
Using signal repeaters called DataLinks placed along the drill string, WDP can transmit up to 57,600 bits/sec of downhole data to surface in as little as 200 milliseconds across a 10,000- to 20,000-ft well. This compares with 4-10 bits/sec transmission over as much as 30 seconds with conventional mud pulse telemetry, according to IntelliServ. The company is now developing a new DataLink to deliver up to 500,000 bits/sec by next year.
Faster data retrieval allows for timelier optimization of drilling parameters and for the capture of high-risk conditions, such as increased pressure resulting from a wellbore packoff, Mr Craig said.

North Sea operators are using WDP to bring development wells online faster. Maersk Drilling is installing WDP on a high-efficiency jackup under construction, the first such installation on a new rig, and has installed WDP on an older jackup currently working in the North Sea. Compared with offset wells in the North Sea, WDP has saved an average of 2.3 days of rig time per development well by providing instantaneous communication with LWD and rotary steerable system (RSS) tools, Mr Craig said, enabling effective real-time vibration mitigation and early detection of high-risk conditions. “With well costs at $1 million or more a day, that is a considerable savings, especially when multiplied across multi-well projects.” Additionally, a major independent Norwegian operator will begin WDP operations in November, he added.
In the US unconventional market, Precision Drilling is using WDP in the Eagle Ford in conjunction with NOV’s automated drilling control system. Similar operations with WDP are expected to start in the Permian Basin and the Bakken this year. “High-speed data is a necessity in closed-loop drilling automation systems, where machines are responding to the data without a human in the loop, and are continuously optimizing drilling parameters and performance,” Mr Craig noted.
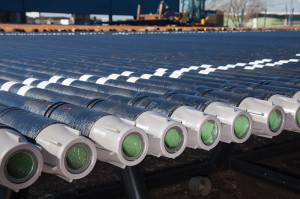
WDP can be retrofitted on any rig, ideally when a new drill string needs to be installed. Existing MWD and LWD tools can transmit high-definition, real-time data and receive data from surface using an interface sub that connects these tools to WDP. IntelliServ’s BlackStream tools can be distributed at multiple points along a wired drill string to provide real-time information from the entire well. “In the past, downhole parameters were only measured at the BHA,” Mr Craig said. “In a 20,000-ft well, however, we want to see what is happening along the entire drill string, as critical events are not limited to near the drill bit.”
Healthy market for used pipe
As more extreme drilling environments drive development of high-end materials, the used drill pipe market is also growing due to conventional, vertical drilling in some markets. Another factor is supply constraints, according to Michael Meldrum, President of John Lawrie, a buyer and seller of new and used pipe. “The headlines always seem to focus on premium high-torque drill pipe and connections, which we sell a lot of and are in high demand, but that is only part of the picture,” he said. “People sometimes forget there are a lot of companies out there doing conventional land drilling in the US and globally.”

He estimates the global used drill pipe market at approximately $1 billion annually, mostly from onshore drilling. Key growth regions are the US, Africa, Mexico and South America. “As long as pipe exceeds industry standard DS-1 CAT 5, it is marketable,” he said.
Oftentimes, a contractor will have a surplus of pipe that was never actually used or has lost its mill certification, meaning it doesn’t have full traceability. Sometimes, a contractor may be relocating to a play requiring a different-size pipe.
“Typically, a contractor will drill a well and, based on an inspection, will either keep or dispose of the pipes. Most used pipe is only good for construction applications, not for drilling. The key is to find surplus pipe rather than pipe being disposed of for quality issues.”
Traceability is especially important in the offshore sector, where regulations require drill pipe to have 100% traceability, including mill certification from the original pipe manufacturer, Mr Meldrum explained. “Only about 15% to 20% of used products come with that certification. The North Sea is almost exclusively a new, high-end drill pipe market for that reason.
“In many cases, contractors buy used pipe because they can’t get what they need, when they need it,” he continued. “Delivery times for specialty high-torque connections are three to four months or more, and in recent months, delivery times even for generic API connections have increased to six to eight weeks or longer.”
That trend is in part due to the US unconventionals, where the fast pace and high volume of drilling is putting more wear on drill pipe and connections. “The key market indicator has always been rig count,” Mr Meldrum said. “However, while the rig count has stayed quite steady, the amount of drilling being done per rig has increased significantly. With the increase in pad drilling and use of walking rigs in the unconventionals, work that was previously done by two or three rigs is now being done by one rig.”
He also sees contractors shifting from using specialized high-torque connections to more generic and conventional double-shoulder connections for the 4-in. pipe commonly used in directional wells. “There is about a 5% loss in performance but more than 400% savings in repair costs,” he said. “Also, drillers are often using mud motors to drill, which don’t require as much torque because the mud motor is doing all the work at the bottom of the hole. An RSS requires high torque for rotation.”
There is also an increasing demand for US-manufactured pipe from other parts of the world. “Operators want US-manufactured products both for quality and the ease of use without having to overcome regulatory hurdles,” Mr Meldrum said. “A lot of countries have import duties and tariffs on non-US-manufactured tubulars. If an international drilling company has tubulars from China, for example, and needs to move those tubulars to another country, the contractor often has to pay a high import duty.”
As unconventional drilling activity ramps up in other countries, such as Argentina, demand for drill pipe will increase, he added.
CrushFree is a trademarked term of Vallourec. eXtreme, XT, TurboTorque, TT, uLtimate, Tri-Spiral, Spiral-Wate and BlackStream are trademarked terms of NOV. Wear-Knot is a trademarked term of Rotary Drilling Tools.
It makes sense that, as well drilling progresses, pipes would have to change as well to accommodate. I’m glad to see that re-using pipes is also becoming more common, however, since it is good for the economy and environment. It’s interesting to read about this tension between the future and past of well drilling. Thank you for an interesting read on the industry!