Hydraulic vs electrical rig designs: pros and cons on floater heave compensation systems
By Rium Tapjan and Hege Kverneland, National Oilwell Varco
Oil exploration today has moved into more extreme environments, forcing technological advancement in drilling equipment. Increased stringencies regarding environmental protection introduce yet another challenge.
One of the greatest changes in rig technology came with the transition from all-hydraulic rigs to electrically powered equipment. Then came the choice between AC-powered rigs and DC-powered rigs. This article will discuss the pros and cons of hydraulic versus electrical rig solutions, focusing on three heave-compensation systems used on floaters.
Floaters require the use of a heave-compensation technique to ensure that the drill string is fixed in relation to the seafloor and the bottom of the well. To keep a constant weight on bit or land a BOP safely on the seabed, the drill string must be compensated by limiting the range in vertical movement. This inhibits the “up and down” movement of the bit, preventing it from being pulled off of and slamming into the bottom of the hole, thereby prolonging the life of the bit.
An early type of heave-compensation method began with the use of a standard derrick with a hydraulically compensated system installed on top of the derrick. This system, the crown-mounted compensator (CMC), uses a standard drawworks installed on the drill floor to hoist the drill string up and down.
Another heave-compensating system is the cylinder rig solution. Here, the whole derrick is replaced with a mast, and the drawworks is replaced by hydraulic cylinders used to lift the drill string up and down. A third compensating system is the active heave drawworks, where a standard derrick is used, and the heave compensation is done by electrically controlling the drawworks. These systems will be discussed in detail here.
HYDRAULIC VS ELECTRIC
Drilling equipment was traditionally designed using mechanical or hydraulic compensating solutions, but use of fully electric-powered equipment has become more and more common. Most modern rigs today have a combination of electrical and hydraulic equipment because it is difficult to replace all machinery and functions with an electrical solution.
Hydraulic
One main advantage of a hydraulic system is the power-to-size ratio of the actuators. A hydraulic cylinder or a hydraulic motor is small and compact compared with an equivalent electrical solution. This makes the equipment itself smaller and lighter and is therefore preferred in most pipe-handling equipment available today.
The hydraulic cylinder, which is a simple but extremely compact and effective linear actuator, is especially difficult to replace with an electrical solution. The market does not offer a good technical solution for an electrical linear actuator.
Another advantage with a hydraulic solution is its energy-storing capability. Gas accumulators are a compact and cost-efficient way of storing temporary energy fluctuations, which also works in case of a power failure on the rig.
A disadvantage with hydraulic solutions is the need for a relatively large and heavy hydraulic power unit (HPU) to power the equipment. Although the HPU can be placed relatively far from the busiest areas on the rig, it still adds space and weight, which is especially disadvantageous on floaters. Placing the HPU in an area different than the equipment itself also requires a lot of piping. This increases installation and commissioning time. High-pressure pipes need to be installed, cleaned (flushed) and pressure-tested, a time-consuming task. Installing (flexible) electrical cables and testing the connections before start-up is not as time-consuming.
Hydraulic systems are highly temperature-dependent. Temperature changes the physical characteristics of the hydraulic fluid and therefore the performance of the system. This reduces the accuracy and speed of the equipment and introduces a huge challenge when rigs are moved to colder environments, such as Arctic areas.
Experience has shown that a common root cause of failure of hydraulic systems is contamination of the hydraulic oil in the form of water, debris particles or both. This can prevent valves, pumps, etc, from operating as intended, which can cause the whole system to fail.
Electric
The overall efficiency of an electrical system is better compared with a hydraulic system. The average efficiency of a hydraulic system is approximately 70%, compared with an overall efficiency of 85% to 90% for an electrical system. This is one of the main reasons why electrical systems are preferred over hydraulic solutions, especially for high-powered equipment such as mud pumps, drawworks and top drives.
Another main driver for electrical systems is its ability to control both torque and speed very accurately. In addition to these functional improvements, electric systems also offer a more environmentally friendly solution by eliminating the risk of hydraulic fluid leaks.
However, electrical systems see limitations when it comes to energy storage. In order to store excess energy, electrical batteries can be used, but these batteries are very large and heavy – a notable problem when space and weight is limited. During short-term energy storing – for example, for heave compensation – the energy can be transferred back into the power distribution system on the rig.
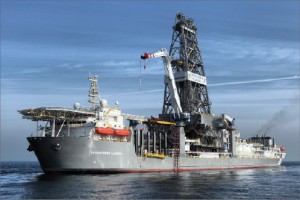
DERRICK WITH CMC
The crown-mounted compensator (CMC) is a hydraulic system that consists of cylinders attached to a rigid frame mounted to the top of the derrick. The CMC is connected to the sheave block via wires, and by extending and reducing the stroke of the cylinders, the block (and the top drive) moves up and down in the derrick corresponding with the heave of the rig. The use of cylinders inflicts the least amount of load on the derrick structure, but the heave-compensation ability is limited to the maximum stroke of the cylinders in the CMC.
Another drawback of a CMC system is its heavy-weight distribution at the top of the derrick. It therefore affects vessel stability and reduces deck load capacity.
CYLINDER RIG
The cylinder rig design, powered hydraulically, combines passive and active compensation techniques. This solution does not require a derrick to support the load of the drill string but instead uses a mast for guiding movement up and down only. All vertical loads are transferred directly down to the drill floor via the lifting cylinders.
This substantially reduces the weight of the tower and lowers the center of gravity. However, the length of heave compensation is limited to the design of the compensating cylinder. Another disadvantage is that this system requires a large HPU, adding substantial weight.
However, since this HPU is installed beneath the rig floor, the orientation usually lowers the rig’s overall center of gravity, thereby improving rig stability. The use of a mast instead of a derrick opens up the drill floor, making it easier to move equipment to and from the drill floor.
The cylinder rig also provides redundancy in case of a failure. If one lifting cylinder fails to operate, it can be disconnected and replaced while operation continues with reduced capacity. The use of multiple wires also introduces redundancy in case of wire failure. In addition, since the drawworks is not used in this solution, much of the noise on the drill floor is eliminated.
DERRICK WITH AHD
The active heave drawworks (AHD) is a fully electric solution where the drawworks is used both for normal hoisting operations and for heave compensation. The AC-type motors provide accurate control of the drawworks in all four quadrants. Typical compensation accuracy is less than 2%. When braking, the regenerative power can be fed back into the rig and used by other power consumers.
Another benefit of using AC motors compared with DC motors is that they do not impose reactive electric load to the generators. Since no additional equipment is installed on the derrick, the AHD design boasts a lower weight and lower center of gravity compared with the traditional CMC system. In addition, the AHD is not limited in terms of compensation length. However, the use of an AC-powered drawworks introduces a loud working environment, and similar to the CMC, the derrick structure creates a more confined workspace.
CONCLUSION
Today’s drilling environment pushes the limits of traditional rig design, demanding technological advancement in areas such as power distribution systems and heave compensation. The customary hydraulic rigs of the past are now combined with electrically powered equipment to optimize the power supplied throughout the rig.
Hydraulic rigs have the advantage of energy storage, using lightweight gas bottles and accumulators instead of large electrical batteries. However, the extreme temperature environments that most drilling applications are exposed to now require the stability of electrical systems. An additional demand in the industry today is the focus on “zero emissions” to the environment. Electrical systems do not require hydraulic fluids to power equipment; therefore there is no risk for spillage.
This article is based on a presentation at the IADC Advanced Rig Technology Conference & Exhibition, 18 August 2010, Houston.
You shared some really interesting points in this article. I had never thought there was so much involved with well drilling. It’s true, technology is always changing and advancing. This really helps us to be able to drill in all different kinds of environments.