S-shaped profile for relief wells may reduce risk of missing target well
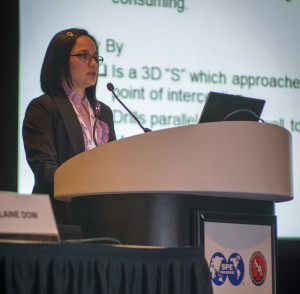
By Joanne Liou, associate editor
Relief well planning has become a required safety measure for the drilling industry to ensure readiness in the event of a blowout. The US Bureau of Safety and Environmental Enforcement (BSEE) requires operators to submit detailed plans for two relief wells to receive a drilling permit, and similar regulations are being adopted by other governments around the world. Surface location, well trajectory planning, drilling considerations and specific service requirements, such as a well control specialist and remote monitoring, must be considered for a successful relief well plan, Baker Hughes’ Vanessa Flores said at the 2014 IADC/SPE Drilling Conference on 5 March in Fort Worth, Texas.
One of the first steps in relief well planning is to identify exclusion zones, areas where rig, boat and helicopter access is prohibited. Predicted weather, loop currents, wind and, specifically, hurricane season in the Gulf of Mexico between June and November must be considered to minimize the positional uncertainties between the relief well and the blowout, which also affects the wellbore position, Ms Flores explained.
Survey management plays an important role in determining the position of the relief well. “The program must optimize and maximize survey accuracy, which is a combination between MWD and gyros,” she said. “It should also contain some methods that demonstrate the survey tools are operating within the stated tolerances.” Increased frequency of surveys can improve accuracy for the wellbore position, and drill string interference helps to ensure there is sufficient magnetic isolation to avoid magnetic influences.
The drilling of the relief well is the same as drilling a normal wellbore, until a ranging tool is used. An S-shaped profile, which includes drilling, locating, ranging, tracking and intercept, is preferred, Ms Flores stated, since it has less probability of missing the target well compared with a J-shaped profile. The drilling tools are selected based on the intersection of the blowout. “A mill and motor are used when intersecting cased-hole or fish, and a bit and rotary steerable system is for intersecting open hole,” Ms Flores said.
Directional work continues halfway to the planned intersection, and once magnetic interference is detected, the directional assembly is pulled out of hole, Ms Flores explained. Ranging tools using wireline are run in hole to verify the exact intercept location. “The process continues until the blowout and relief well are very close, then a liner is set to provide a positive alignment for penetration. After the well is intercepted, ongoing communication needs to be established, and the handover to a well control specialist needs to start.”
For more information, see IADC/SPE 168029, “Relief Well Planning.”