Advanced modeling, simulation, data-driven engineering pave path for revolution in bit designs
Solutions-based approach, enabled by digital tools, is allowing for expedited optimization and rapid delivery of application-specific designs

By Derek Nelms, John Fairbairn and Nicholas Lyons, Baker Hughes
Drill bit technology has been driven by the need for robustness and efficiency since the early days of oil and gas drilling. As drilling environments have changed, engineers have focused on improving durability in challenging formations and maintaining directional control without sacrificing rate of penetration (ROP).
To capture efficiencies, innovation has focused on finding ways to reduce trips and bottomhole assembly (BHA) changes by developing bits that can drill efficiently in challenging applications and perform reliably in harsh conditions. Using bits optimized for different well sections improved results, but planning wells based on the requirements for a specific interval can deliver only so much in terms of improvements. To capture truly significant gains, the industry needs to look at drilling challenges in a different way.
Today, digitalization is pushing bit technology into a new era, with advanced modeling and simulation providing critical insights that are allowing engineers to take drill bit technology to the next level.
Current conditions
One of the biggest considerations driving drilling improvements is project economics.
To achieve efficiencies and increase production, many operators have turned to more powerful rigs and motors, as well as advancements in BHA design, to drill more footage with a single BHA at higher ROP and with more directional work being performed. These changes require bits to do more today than they have done in the past, which demands precise design improvements.
In recent years, drillers have enhanced bit performance by testing new bit designs in successive field trials. Using relatively simple engineering tools to evaluate bit behavior in a particular drilling environment, bit providers can make modifications to extend bit life. But working only with surface data and the final dull bit condition to make design changes is limiting. Without a way to capture the nuances of a complex application, there is restricted scope for better understanding of bit performance.
Although this process has made it possible to capture some performance gains, because of the iterative nature of development and testing, progress is slow and limited.

Solutions-based design
To make appropriate, demonstrable bit design improvements, there must be an understanding of the bit behaviors that are required in the environment in which it is deployed.
There is no point in simply tacking on features with the hope of producing a better bit. A superior solution employs an advanced process that solves for desired bit behaviors using digital simulations that model the complex application, with the goal of delivering the right bit the first time. This “model-and-make” process is straightforward:
1. Identify the drilling challenges
2. Define performance limiters
3. Align challenges with the bit behaviors needed to resolve them
4. Develop designs that contend with the challenges
5. Validate designs in controlled conditions to identify shortcomings
6. Redesign to address issues (and repeat steps 4 and 5 until all the issues are resolved)
7. Send the new bit to the field and gather and analyze data to improve performance.
The process follows a solutions-based design approach — defining application challenges and the behaviors the bit must exhibit downhole, including aggressiveness (i.e., reactive torque in different rock formations and operating environments), torsional and lateral stability, cleaning efficiency, side cutting capacity, durability, abrasion resistance, thermal stability and impact resistance.
Application changes can be simulated in a digital environment, where the expected performance outcome is evaluated. This expedites the creative process and delivers deeper insights into performance that can be applied rapidly to new designs.
Understanding design changes and their repercussions underpins development, giving designers more confidence in their expectations for bit performance. To accelerate development, a digital platform must replicate physical trial and error by allowing iterative “build-and-break” scenarios. This puts end users in a position to encounter less risk when introducing a new variable into the drilling environment.
Leveraging technology
Baker Hughes uses a proprietary bit drilling simulator to characterize behaviors, reducing the number of physical iterations required for a new bit design and rapidly delivering a viable solution.
The 3D Tetrahedron bit drilling simulation software uses a digital twin of the bit and the drilling environment to simulate vertical, deviated and extended-reach well geometry with multiple drilling environment inputs. The model is calibrated to the downhole environment using full bit runs in an onsite drilling laboratory and is continuously validated with field data to remove as much uncertainty as possible from the design process.
The software draws from an extensive library of real-world formations, which allows testing in parameters that accurately simulate the conditions the bit will encounter downhole to capture bit behavior. Engineers can change the way the formations are overlaid so the bit is drilling through homogeneous or interbedded layers, alter the angle or motion of the drill bit, modify weight on bit (WOB) and RPM, and simulate a rotary steerable system (RSS) or bent motor BHA to evaluate PDC and hybrid drill bits. The software predicts drilling responses such as ROP potential, directional responsiveness and aggressiveness, and captures rock-bit interaction, as well as thermomechanical wear rate.
Based on the computer model, application-specific bit prototypes are manufactured for extensive physical testing using specialized tools and test equipment. Testing with proprietary equipment in a controlled environment allows designers to test performance parameters in specific formation conditions.
A visual single-point cutter test is done in a pressure vessel fitted with a rapidly spinning turntable. This allows a cutter mounted on the test rig to cut into rock core under conditions that replicate the downhole environment. Load cells measure the force on the cutter, and a high-speed camera records the test. Engineers can view test results frame by frame to understand exactly how the cutter engages the rock, what happens to the rock as the cutter makes contact and what the cuttings coming off the rock face look like. This makes it possible to isolate the effects or behaviors of different cutter sizes, geometries and orientations in rock under drilling conditions to provide better resolution in composite drill bit simulations.
Additional specialized equipment is used to conduct full-bit tests at downhole conditions to create a comprehensive picture of bit performance and provide engineers with the data necessary to analyze and improve designs.
In short, digital tools allow engineers to shorten the design cycle, enabling advanced simulation to rapidly test bit performance in a range of applications and identify the optimal configuration for any drilling scenario.
This unique modeling capability is the enabling force behind the shaped-cutter designs that are improving performance in drilling applications around the world.
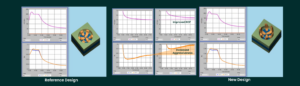
Applying the methodology
Digital technology is making it possible to address a range of performance issues across drilling environments by enabling bit design enhancements in the midst of a drilling program.
For example, when an operator encountered a problem with a bit that was performing with low ROP in interbedded sand and shale, a decision was made to use advanced simulation to improve bit behavior. The proprietary simulation software allowed engineers to select the correct cutter geometry and correct cutter location and orientation on the bit and to rapidly evaluate its performance. When tests revealed that the new cutter shape was experiencing premature damage, engineers used the data from the tests to design and evaluate an enhanced cutter shape that allowed the cutting structure to remain intact through the run and drill at higher ROP.
Metrics from the field
The bit designs made possible with digital technology have already delivered substantial performance gains in the field.
In the Vaca Muerta shale in Argentina, PRISM shaped-cutter technology was applied in a long, slim-hole lateral section where WOB limitations resulted in premature BHA failures. Limited power input from the rig systems was restricting penetration rates in offset wells, and the operator wanted to find a solution that would enable longer and more productive drilling runs.
Following advanced simulation modeling to identify the optimal bit and shaped cutter combination for the drilling environment, Baker Hughes employed an extended-life PDC bit with PRISM shaped-cutter technology on an RSS. This solution allowed the driller to increase WOB for higher ROP without having to worry about tool damage. The section was drilled in a single run, delivering a 29% improvement in ROP compared with offsets.
Based on the performance of the shaped-cutters, the decision was made to use the specialized design in comparable sections in the Vaca Muerta, achieving consistent performance results.
A similar approach was used to optimize a drill bit to address challenges an operator in Colombia encountered while drilling a 14 ¾-in. well section with a standard PDC bit. The abrasive, interbedded formations consisted of sandstone, siltstone and claystone, with unconfined compressive strengths ranging from 5 to 25 kpsi. The torque and vibrations generated dulled the bit, requiring multiple bit replacements to drill the section.
To address these challenges, Baker Hughes suggested replacing the PDC bit with a design that combines roller cone and PDC cutting elements to minimize vibrations. The Kymera design improved the average distance drilled by 17%, reduced torque variation by 46% and reduced the mechanical specific energy by 44%.
To further optimize the bit for the project, simulation software was applied. The objectives were to increase ROP and improve the reliability of the bearing and seal, as well as increasing aggressiveness while maintaining torsional stability and durability. The new design also improved load balance between the PDC and tungsten carbide insert cutting elements of the bit to provide enhanced bearing and seal reliability.
In the next well, the optimized bit drilled 50% more footage at 39% higher ROP compared with the average PDC bit results. It drilled 26% more footage at 33% higher ROP than the standard hybrid bit and reduced cost-per-foot well construction costs by 23%.
Capturing full value
with broader applications
Representative drilling performance improvements demonstrate the effectiveness of simulation software for enhancing bit designs, but the potential value of simulation technology has yet to be fully realized.
The 3D Tetrahedron bit simulator has much broader applications. Applying it to other scenarios will make it possible to develop more capable tools that address other real-world industry challenges by using data for qualitative observation and quantifying improvement.
Using a science-based “model-and-make” methodology rather than the conventional “build-and-break” approach minimizes design iterations in tool development and removes guess work from problem solving to deliver rapid, reliable and customized solutions for a broad range of issues. DC
Tetrahedron, PRISM and Kymera are trademarks of Baker Hughes.