Designer chemistries
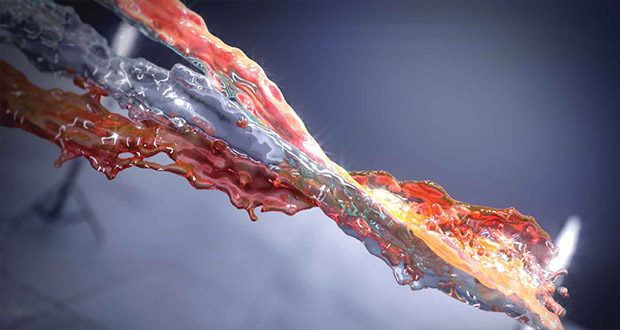
In lower-price environment, drilling fluid formulas aim to provide customized solutions that balance performance, environmental risks, requirements for cost reduction
By Kelli Ainsworth, Editorial Coordinator
Although service companies remain focused on developing ever-more reliable drilling fluids, particularly for challenging environments like deepwater, the fall in oil prices has made it more crucial than ever before that these fluids also help to manage costs. “Through the acute downturn when you’re losing 100 rigs a week, it’s a turbulent environment, and there’s a frenzy around cost,” Phil Vollands, President of North America for Newpark Drilling Fluids, said. “But then we transition out of that, and we have better conversations. Those conversations have transitioned from cost to value, and technology is part of that value conversation.”
One approach service companies are taking to facilitate cost management is by formulating new water-based muds (WBMs). These fluids are generally more cost effective than oil-based muds (OBMs), but in terms of performance they often still lag behind non-aqueous fluids. “It’s tough to beat oil-based muds on their lubricity and wellbore stability,” said Jim Friedheim, Drilling Fluids Marketing and Technology Manager for M-I SWACO, a Schlumberger company. “With water-based muds, you have to think about the chemistry and engineering a lot more closely than with oil-based muds.”

Two other focus areas for fluid companies lie in finding ways to push the temperature limits of existing drilling fluids and to ensure that these fluids comply with increasingly stringent environmental regulations, such as REACH in the European Union.
Getting operators to adopt new fluid technologies in the midst of a downturn can be a challenge, however. Even in the best of times, the industry can be slow to embrace innovation. Now, in a down market, operators are even more likely to stick with proven technologies they know. “Today, operators are primarily focused on reducing costs in their operations, essentially doing what they’ve always done but cheaper,” Julian Coward, Strategic Business Manager for Halliburton’s Baroid, said.
Managing risk to manage costs
This summer, Baker Hughes is commercially launching its newest fluid system, NSURE. The mineral oil or synthetic-based invert emulsion system was designed to manage risk in environments such as deepwater, Brian Teutsch, Product Line Director for Drilling and Completion Fluids, said. “When we look at high-risk environments like deepwater, we like performance. We look for ways to set world records, but the No. 1 thing it keeps coming back to is risk,” he said. “If you can just avoid having any problems, that in itself often leads to performance records.”
NSURE was developed to provide constant rheology from 40°F to 275°F. Baker Hughes classifies the system as “constant rheology defined,” meaning that when it was under development, engineers set specific target ratios for rheologies at both low and high temperatures. “We’re not just talking very generally about how a fluid behaves; we can be very specific in what the design criteria are,” Mr Teutsch said. Because NSURE has a more constant rheology, he explained, it also performs well in cementing operations, helping to maintain the required friction-pressure hierarchy.

Mr Teutsch classified NSURE as a global system due to its environmental compliance and flexibility. The fluid was designed for use offshore in Norway, which has some of the world’s most stringent environmental standards. It can also be used in the UK North Sea, Gulf of Mexico, West Africa and Southeast Asia.
Further, the system was designed to be flexible with regard to base oil. “A lot of times, base oil will dominate the economics of an offshore drilling fluid, which means that you’ve got to be able to operate with a lot of different types of base oil to be viable in various markets,” he explained. The system was subjected to tests at varying temperatures and pressures, oil-water ratios and densities in many major base oils to verify performance would remain constant in each of the oils tested. Each formulation was also tested for its ability to handle contaminants such as seawater and cement. The final formulation of NSURE was created after several iterations of testing and redesigns.
Early in the field trial process, the fluid’s ability to resist barite sag was put to an unexpected test. The workboat transporting the fluid to the rig was unable to offload to the rig for 14 days due to rough seas. “For any mud, that’s a difficult test, but new muds especially tend to sag barite,” Mr Teutsch said. However, the fluid went on the boat at 11.2 lb/gal and remained at 11.2 lb/gal when it was finally brought onto the rig. “It got a very difficult test with regard to sag before it ever even got deployed,” he said.
Looking to the future, Baker Hughes is working on raising the temperature limitations of some of its existing fluids.
The company is conducting research and development on higher-temperature versions of LATIDRILL, which currently works in environments up to 275°F. This WBM utilizes a minimum number of components for ease of use when drilling the upper hole. It eliminates the need to add in a variety of viscosifiers and fluid loss additives separately. The system targets unconventional plays and lateral, deviated and extended-reach wells. Baker Hughes is working to develop a version of this fluid that can be used at temperatures as high as 350°F.
The company is also looking at extending the capabilities of MPRESS, an invert emulsion fluid (IEF) formulated to help boost flow rates on land operations. This fluid currently works in environments up to 275°F, but research is under way to push it to 350ºF, according to the company.
“I’m not seeing that we’re going to temperatures or pressures we haven’t gone to in the past. It’s really more about a demand for more functionality at these temperatures and pressures,” Mr Teutsch said. “They want to go to these temperatures and pressures with the functionality they’ve learned to appreciate at lower temperature and pressure environments.”
Dialing-in performance
M-I SWACO is also focusing on formulating WBMs that rival the performance of OBMs. Dr Friedheim said he expects that WBMs in general will be utilized more frequently due to its environmental advantages, as well as its greater remediation and disposal options. Further, advances to WBMs are making them more competitive with OBMs. “It is the performance limitations of WBMs which restricts their use as compared to non-aqueous fluids,” he said. “With the advances we have seen in WBM and drilling technology over the past few years, this gap is closing.”

This summer, the company plans to introduce a new high-performance water-based drilling fluid, designed for lateral drilling in onshore unconventional wells. The challenge in these wells, he said, is to develop fluids that reduce torque and drag throughout the lateral section. “These are lateral wells through unconventional shale plays which they want to drill as fast as possible yet maintain a stable wellbore,” Dr Friedheim said.
The new fluid, whose name has not been announced yet, was designed so that performance can be customized. If drilling a less reactive play, the shale inhibitors can be minimized. If moving to a more reactive formation, the inhibitors can be ramped up again.
The focus of this new water-based system, according to the company, are the drillability and wellbore stability aspects. These are accomplished by the use of drilling enhancers and specialized chemistries to provide an increased ROP and surface protection of the wellbore to fluid ingression and destabilization. M-I SWACO noted that performance details of the system were not available as of mid-June as the fluid was still completing field trials; a commercial launch is being planned for late this summer.
Another critical effort around drilling fluids is ensuring that all of the company’s existing fluids, such as the ULTRADRIL high-performance water-based drilling fluid system launched nearly a decade ago, are compliant with REACH and CEFAS in the European Union. REACH – the Registration, Evaluation, Authorization and Restriction of Chemicals regulations – will take full effect in 2018, while CEFAS – the Centre for Environment, Fisheries and Aquaculture Science – works alongside government authorities to test and validate the environmental impact of drilling fluid chemicals. REACH originally went into effect in 2007, requiring that any chemicals imported into or manufactured in Europe at specific volumes were tested for degradability and toxicity. The regulations require some chemicals to be replaced with less hazardous alternatives. Initially, chemicals at volumes of 1,000 tons or higher were subject to REACH protocol. In 2010, the regulations expanded to chemicals at volumes of 100 tons or higher. By 2018, all chemicals imported into Europe at a volume of 1 ton or more will be subject to REACH. Some 30,000 chemicals will be affected, which impacts drilling fluids. Several other areas around the world utilize both CEFAS and REACH guidelines to regulate discharges and usage of drilling fluid products and chemistries, Dr Friedheim said.
Although already designed to drill in environmentally sensitive areas both onshore and offshore, the ULTRADRIL drilling fluid system is being reformulated to align with REACH and CEFAS protocol. “We’re trying to create a North Sea version that has all REACH-complaint materials and meets all aspects of chemistries for use in the North Sea on toxicity and degradability but that still has the same performances we’ve had all over the world,” Dr Friedheim said.
The company is also adding a nano-like additive to this fluid system for increased wellbore stability in older shale formations. Dr Friedheim said that nanoadditives have been proven to help stabilize shales by physically blocking the pores, but they have not seen widespread adoption in the industry. “We’ve spent a lot of time, probably five-plus years, looking at nanotechnologies and coming up with nanoadditives,” he said. However, misconceptions remain around the safety and environmental impact of nanoparticles, leading to the lag in industry uptake. “The perception of nanoparticles in the eyes of the general public is based on a mixture of misinformation and lack of knowledge,” Dr Friedheim said. “Certainly some nanoparticles are rightfully of a concern, but others are totally benign.”
All of the nanoparticles M-I SWACO utilizes have been extensively tested from an HSE standpoint, he added. Additionally, some nanoparticles have been used commercially for many years. “The nano-material which we are currently promoting has been used in the cosmetic industry for years in beauty aids that are applied directly to human skin,” Dr Friedheim said.
Looking ahead, the company remains focused on maintaining flexibility to respond to fluctuating industry demands. “We’ve always tried to focus on the industry needs, as well as being sensitive to the environmental challenges wherever our clients drill,” Dr Friedheim said. “Every few years, things change, as they did last year, and it gives us different challenges. The important thing is to stay flexible enough to go with the flow.”
Possibilities of nanotechnologies
Saudi Aramco has also been testing nanotechnologies. In 2014, Dr Vikrant Wagle and Dr Abdullah Yami from Saudi Aramco’s EXPEC Advanced Research Center conducted an R&D project to look at how nanoparticles might affect barite sag in organo-clay-free IEFs. While organo-clay-free IEFs can provide high ROPs and have a high tolerance to contamination, these fluids sometimes don’t provide optimal rheologies, and barite sag can result. Often, low-gravity solids (LGS) are added to increase rheology, but these solids tend to increase plastic viscosity, which in turn can cause an increase in equivalent circulating density (ECD). “Normally in organo-clay-free fluids, we need to add LGS, such as clay-type materials like sepiolite, for barite suspension,” Dr Wagle said. “Even after adding such materials, sometimes we do not get good barite suspension.”
In this experimental project, Saudi Aramco formulated several different base oils at varying densities in a lab under temperature and pressure conditions similar to those in the Red Sea and onshore unconventional wells in Saudi Arabia. These environments are characterized by temperatures between 150°F and 300°F and pressures between 1,000 to 10,000 psi. After fluids were mixed in stainless steel mixing cups on a five-spindle multimixer at 11,500 rpm, they were static aged for 16 hours in HPHT stainless steel cells in a hot rolling oven. The cells were tested in both vertical and at a 45° incline. When static aging was complete, the rheology, sag factor and top oil separation were measured.
In addition, Saudi Aramco engineers added common contaminants, such as artificial drilled solids, seawater increment and lime, to examine how IEFs formulated with nanoparticles tolerate contamination.
The study concluded that nanoparticles were able to reduce barite sag in a variety of base oils. It also revealed that nanoparticles could provide constant rheologies in HPHT environments. Further, the fluids demonstrated their ability to maintain suspension characteristics in the presence of contaminants. Using nanoparticles in place of an LGS also reduced plastic viscosity, which prevented ECD from increasing, in turn providing better ROP, Dr Wagle said. “Higher solid content due to the added LGS can lead to higher plastic viscosity, which in turn leads to higher ECDs and lower ROP,” he said.
Saudi Aramco currently does not frequently utilize nanoparticles in its drilling fluids, Dr Wagle said. However, going forward, the company plans to use nanoparticles in both drilling fluids and cement to address specific challenges, such as barite sag.
He added that Saudi Aramco is planning more R&D projects to address other challenges, such as formulating fluids with optimal rheology for cuttings disposal, stability in HPHT environments, shale inhibitive fluids, and fluids that are more environmentally friendly.
Protecting the wellbore
Halliburton, through its Baroid business line, is focused on developing customized fluid solutions that help to maximize production and minimize downtime. “(Drilling fluids) are an integral component of the well construction and completion phase,” Mr Coward said. “One wrong recommendation could produce a seriously negative result. If you have issues with the fluid, you could potentially lose the wellbore or impair productivity.”
One positive challenge in today’s difficult market, he said, is to offer fluids that are superior to others due to qualities that make them more environmentally benign or are more protective to the environment. Baroid is in the early stages of commercializing a salt-free, clay-free invert emulsion fluid called BaraPure. By replacing salt with a biodegradable internal phase, cuttings can now be disposed of at the rig site, where environmental legislation permits. “Eliminating the salt from the fluid minimizes the possibility of contamination to the groundwater and reduces the potential environmental impact of the waste stream,” Mr Coward said. “It also means cost savings because you don’t have to transport the cuttings to a disposal site. We would much rather treat the waste at the source.”
Baroid is evaluating the potential of formulating the BaraPure system with a more environmentally friendly oil phase. “We’ve taken away the salt element and replaced it with a technically equivalent alternative,” he said. “Now we’re looking at the oil phase and seeing how we can make environmentally protective advancements there, as well.”

Last year, Baroid released a family of lost-circulation materials (LCM) under the BaraShield, BaraBlend and BaraLock names. “In mature fields, these technologies reduce risks and enable drilling with reduced nonproductive time, ultimately reaching reserves that were previously inaccessible,” Mr Coward said. “Each engineered solution is customized to address every distinct lost-circulation scenario.” This family of LCMs was designed to plug fractures of varying sizes, including those with large and unknown widths.
Recently, an operator was experiencing fluid loss in wells drilled in the Beaver Lodge Field in Williston, N.D. The BaraShield-664 solution, which can be applied in a continuous treatment or as a pill, was added to the drilling fluid. According to Baroid, mud loss volumes were reduced by 81% compared with previous wells drilled in the area. As a result, the operator saved 2.5 drilling days and the associated costs, the company stated.
Greater levels of customization
Over the past year, Newpark Drilling Fluids has increased its focus on providing fluids specifically targeted for deepwater wells. Common challenges in this area are salt erosion and the need for fluids to function across a wide range of temperatures. “Each of these problems begs for a specific fluids solution,” said Steve Daniel, Senior Vice President of Technology for Newpark. To address such issues, the company recently launched the Deepwater Initiative. One major component is the $30 million expansion of its Port Fourchon, La., facility. Upon completion in Q1 2016, the facility will have nearly doubled its storage capacity.
The initiative also includes the introduction of a new deepwater fluid system, Kronos. This synthetic-based invert emulsion system was commercially launched at the 2015 OTC. Deepwater operations can have long static times during tripping, BOP tests and logging, Mr Daniel said. So one challenge that the Kronos system tries to address is providing greater static stability during these operations.
The system maintains a flat rheology at temperatures from 40°F to 250°F. As deepwater wells become more challenging, developing fluids with stable rheologies across hundreds of degrees of temperature variance will be a challenge that keeps service companies on their toes, Mr Daniel said. “It’s already challenging enough in 10,000-ft water depth with a seabed temperature near freezing,” he said. “Now you extend those wells down to 30,000 ft below the mud line, and you’re in perhaps 350-400º bottomhole temperature environment. That’s a pretty broad range for which your fluid has to be formulated.”
When developing the system, Newpark identified core chemistries but wanted to leave room for customization. “The product set has been developed to allow for substitutions to carry the performance into different technically challenging conditions,” Mr Daniel said. Performance and testing data were not available for this fluid as of mid-June.
In the future, Mr Daniel said, he envisions the potential for customizing fluid solutions for several individual segments of the same well. For example, future rigs will likely have increased functional storage capacities for liquid mud, he said. “Rather than drilling with ordinary synthetic-based fluid from the top to bottom of the well, operators can select the best solution for each section of the well,” he said. Customized solutions will optimize drilling and decrease nonproductive time.
NSURE, LATIDRILL and MPRESS are registered terms of Baker Hughes. BaraPure, BaraShield, BaraLock and BaraBlend are registered terms of Halliburton. ULTRADRIL is a registered term of Schlumberger. Kronos is a registered term of Newpark Drilling Fluids.