Centralized start-stop system helps reduce fuel consumption, emissions from idling engines in hydraulic fracturing operations
Field testing in Permian last year showed promising results, with significant decreases in engine idling hours and emissions levels
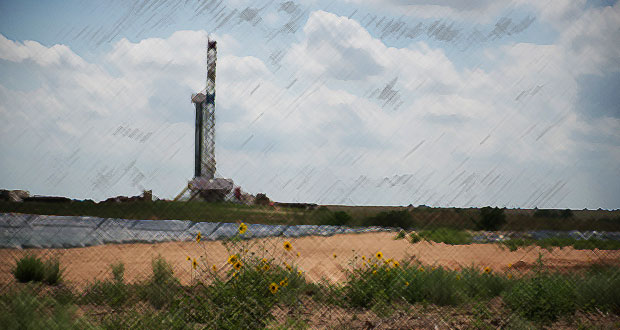
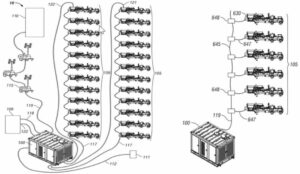
By Stephen Whitfield, Associate Editor
As the industry continues to deploy innovations like battery energy storage systems, dual-fuel and natural gas engines to lower fuel consumption and mitigate emissions during hydraulic fracturing operations, another source of NOx, CO2 and particulate matter emissions is getting more attention on the sustainability radar: idling frac engines.
“These engines that we’re using on frac sites were never designed to idle. They were designed to run very efficiently at 50%, 60%, 70% power. The more load they have on them, the better their lubrication systems and radiation packages work. But that means they’re consuming a lot of fuel,” said Robert Fulks, VP of ESG Technology at MGB Oilfield Solutions. “Frac engine emissions have come way down because of the technologies applied by manufacturers, but they’re not as efficient in their fuel consumption as you’d like them to be.”
Speaking at the 2023 SPE Hydraulic Fracturing Technology Conference on 2 February in The Woodlands, Texas, Mr Fulks outlined the development and field testing of a new start-stop system designed to mitigate fuel waste from idling engines.
Industrial diesel engines rely on permanently mounted batteries to drive electric starters. When a start-stop system is added, it automatically shuts down the engine when it’s not being used and restarts it when it’s needed. This reduces idling time and, therefore, fuel consumption. The technology has been used in the automotive industry for decades and was adopted into the frac industry within the past five to six years.
Last year, MGB launched its version of the start-stop system with the addition of a centralized power unit. This made a significant difference as it meant that each start-stop system would not have to be manually activated on each individual engine.
By installing the start-stop system inside the centralized starter unit, an entire fleet of frac pumps can be started from a single power source, or be shut off when the pumps are not needed. This reduces the time needed to stop/restart a frac fleet to less than 10 minutes, compared with around 45 minutes for a start-stop system without a centralized starter function, according to MGB.
“The big holdup with adopting start-stop systems has been the amount of time needed to restart an entire fleet,” Mr Fulks said. “But now you can press a button and start-stop an entire frac fleet. You don’t need to do the old way of having two people go out to charge the hydraulic pump on each tractor. This is a big deal if you want to talk about efficiency.” Additionally, the start-stop function can be performed either remotely or autonomously, if used with third-party automation software.
Different configurations for system setup
MGB’s start-stop system can be laid out in two configurations. One is the “daisy chain,” where the main hydraulic supply line runs from the hydraulic start-stop unit to the first pump on a row of frac pumps. Another hydraulic hose connects to this first pump and runs to the adjacent pump. This process repeats for all the pumps on that row, and the same process repeats for the other row. The other potential configuration is a manifolded distribution layout, where hydraulic power from the start-stop unit runs to a manifold system with a set number of outlets, which then provide power to the connected frac pumps.
The layout of the individual frac pumps determines the flow of the hydraulic fluid to the frac pump starter. Either of the two standard configurations of the frac pumps can be deployed with the MGB system, either with the daisy chain or the manifold setup. The closed center configuration means that, as hydraulic pressure is applied to the starter circuit, the actual frac pump starter motor will not engage until a start signal is transmitted. When a signal is received, the solenoid valve on the starter sends hydraulic fluid to the starter to start the engine.
For the other starter configuration, the open center, when the hydraulic fluid flows to the starter circuit, the fluid bypasses the solenoid valve and returns to a tank. When enough fluid has passed to start the engine, the solenoid valve activates and sends the fluid to the starter motor. An open-center setup requires additional ball valves to control the flow of the hydraulic fluid to each frac pump and eliminate flow when it is not needed. In a closed-center setup, no additional control valves are required – the solenoid valves control the flow to each frac pump.
The MGB start-stop system, and the centralized power unit, also reduce the need for auxiliary equipment – like tractors, air compressors, generators and diesel-powered light towers – that is typically needed to power individual frac pumps. Mr Fulks said this reduction in equipment provides an added benefit to frac operators by reducing the number of potential points of failure on a frac pad, lowering maintenance costs. “The single central unit is basically providing all the power we need on location. So, we don’t need all the generators, light towers and compressors we have out there. You won’t see any tractors on location. You can daisy-chain everything to the unit.”
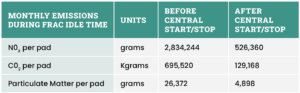
Field testing in the Permian shows positive results
Last year, ConocoPhillips tested the start-stop system on a frac pad in the Permian Basin, using a real-time data analytic software developed by Corva to measure frac pump diesel usage, engine idle times and emissions generated from the frac pad. Use of the centralized start-stop system took place during a three-week period in mid-summer 2022. ConocoPhillips then measured these totals against the average idle time and fuel usage for the same pad from a separate three-week period without the centralized system.
The operator found that, with the centralized system, an average of 135.78 idle hours were removed per pump over the three-week period. This led to a savings of 1,962.07 gallons of fuel per pump, or a total savings of 35,317.32 gals for the entire pad, which used 18 active pumps. Assuming an average diesel price of $3.80/gal, this meant a fuel cost savings of $134,205.83.
When factoring in the reduction of generator usage and light tower usage, as well as the reduction in maintenance costs enabled by the reduction in auxiliary equipment, the operator determined it achieved a total cost savings of more than a half-million dollars.
From an emissions standpoint, the MGB system also recorded savings in NOx emissions, CO2 emissions and particulate matter (see graph above).
“You’re not going to eliminate all the idle time because you’ve got to get the engines up to speed and then bring them back down – that takes time. But you can eliminate a lot of the idle time, and you can eliminate a lot of fuel consumption. The field tests showed a dramatic difference,” Mr Fulks said. DC
More information can be found in SPE 212357, “Reductions in Emissions and Fuel Cost with Start-Stop System Technology for Diesel Frac Fleets.”