Digital tools streamline design, testing process during drill bit selection
Digital twins, in-bit sensors among innovations shortening the iteration cycle to help operators get bits into the field faster
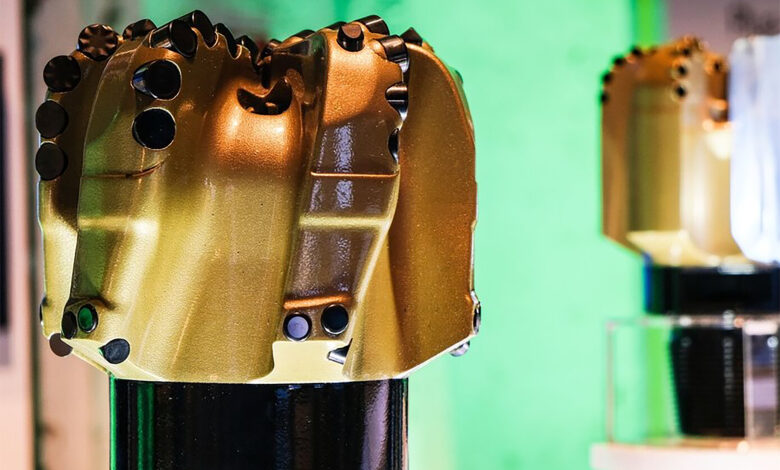
By Stephen Whitfield, Associate Editor
There is a lot that goes into a service company’s process when helping operators to select the right drill bit for a given hole section. They need to work with operators to understand the plan for drilling the section. They need to measure the dynamics of the rock to be drilled, typically through rock strength data provided by the operator. They need to determine the amount of customization a given bit design and a given well might need in order to help the operator achieve its objectives. Often, they have to deploy simulation software to gather information about multiple aspects of the bit’s potential downhole performance. That’s typically followed by field testing, which can sometimes yield different results from the simulations, sending everyone back to the drawing board.
On top of the challenges in managing these variables, bit manufacturers are constantly looking for ways to push the limits of their products’ performance, recognizing that operators are always seeking to reach deeper target depths at faster speeds.
“Because the bit business is so competitive, if you’re not in the background trying to figure out how to beat your own prior performance, you’re going to be displaced pretty quickly,” said Matthew Jennings, Product Line Director – Drill Bits at NOV. “We have to constantly beat ourselves and improve on our performance with the bits we design. If we don’t, someone else will.”
Making even small incremental performance gains is critical right now as drilling activity continues to ramp up around the world. “A lot of times our customers are seeking a quick solution,” said Derek Nelms, Product Line Manager – Drill Bits at Baker Hughes. “Our goal is to find that optimal solution to push the performance of the bit to the level the customer needs, and to do it in the quickest way possible. Our expertise in the formations they’re drilling in, our understanding of how our bits perform and the technologies we need to deliver that best outcome – all of that is so important to the process.”
In this article, DC speaks with Baker Hughes, Halliburton and NOV to discuss steps they’re taking to enhance their simulation software. Better software not only provides better understanding of how a given bit will interact with the target rock formation, but it can also shorten the time required for bit design and field testing, allowing operators to get the bits into the field faster so they can start drilling and producing.
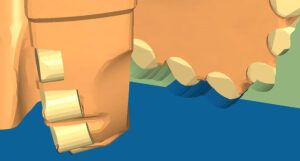
A digital twin of the bit
Like with most other processes in the drilling of a well, companies are always striving for more efficiency in the bit selection process. Baker Hughes has an assortment of tools available to help operators find the right drill bit for their applications. For instance, at its office in The Woodlands, Texas, it has a surface rig that can drill with full-sized drill bits in test situations. It also has a pressure vessel that can take a rock core and simulate drilling conditions in a downhole environment.
However, to streamline the process while still providing an accurate analysis of a drill bit’s performance, Baker Hughes says it is not only continuing to invest in better software but also finding ways to better leverage its decades of field data from various product lines.
“Our customers are drilling into more challenging lithologies, but we know going into the bit selection process what our toolbox is and how we can design bits to solve very specific challenges,” Mr Nelms said. “We can shorten the design process because we know how our technologies behave downhole.”
One of the key pieces in Baker Hughes’ bit design process is its proprietary bit drilling simulation software, which can create a digital twin of the bit and the target formation. It then evaluates cutter and bit body interactions of the bit and the rock using proprietary cutter force models. This software is used to evaluate the performance of various design concepts and customizable solutions using customer inputs to model performance-limiting challenges from their drilling applications. These can be anything from formation variation to optimizing the drill-out operation of cementing float equipment.
After the user inputs well parameters and rock properties, the software conducts a simulation that can determine the drilling behavior of specific designs to predict aggressiveness and loading conditions on the cutting structure. This type of digital twin capability allows for greater flexibility in modeling drill bit behavior because it can also make predictions based on the performance of similar rock formations and similar bit designs using previous digital twin data.
This capability provides Baker Hughes with a more comprehensive picture of how the bit will perform. In some cases, having a digital twin has led to the need for fewer or even no field tests, shortening the iteration cycle by days or weeks.
“As we’ve created these models, built out the digital twins and built out a library of simulations, we can answer customer questions much faster because we can take previous models we have already built and modify them to meet current needs. Because a lot of the upfront work has already been done, the whole process is streamlined,” he said.
Baker Hughes said it still runs field tests, but it finds that some of its long-time clients now favor using digital twins in place of field tests. This approach requires a higher level of trust between customer and supplier, however. “We spend a lot of time calibrating our digital capabilities with past field data and lab data, and when you add that to having strong relationships with your customers, that means we can really work together to streamline the process.”
In some cases, digital capabilities have been effective in helping operators set performance records without the need for field testing. In 2021, for example, a company in the Permian Basin had reached a ceiling with its ROP while drilling the 12 ¼-in. intermediate hole section. Using computer simulations, Baker Hughes pinpointed cutters as the primary ROP limiter and then lab-tested different cutters and their placement across the bit face. Ultimately, the company recommended the Prism shaped-cutter technology with its Dynamus drill bit because the simulations showed that the point-loading on the Prism cutter would be ideal for maximizing ROP in the ductile pressurized shale formations of the hole section.
In the field, the Dynamus bit with Prism cutters drilled the entire intermediate section from 1,405 ft to 5,200 ft in 16.3 hours, resulting in an average ROP of 232.8 ft/hr. This was 37% above the operator’s target and even set a record for the hole section, according to Baker Hughes.
Mr Nelms said the next step with its digital twin modeling is to use machine learning to automate the building of the digital twin once the drill bit design and field data have been input into the system.
“A lot of digitalization efforts are centered around manually creating the models and building out the digital twins, but over time we’ve built out a library of simulations,” he explained. “This means we can have a faster process because a lot of the upfront work has already been done and we can adjust and modify previous models to help build out new models. Automation can help us reduce that setup time even further. We’re putting a lot of our focus into making that process even faster.”
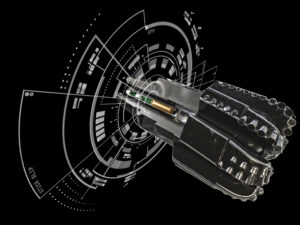
Insights from in-bit sensors
Halliburton had previously relied on data captured at the surface to feed into its drill bit designs, but with the introduction of its Cerebro Force in-bit sensors in 2020, the company says it can now better understand and document the motions of the drill bit from well to well.
Cerebro Force captures weight, torque and bending measurements directly at the bit, allowing the company to map the downhole motion of the bit and any associated drilling dysfunctions. This can prove valuable when it comes to improving future bit designs.
“Cerebro is all about understanding the subsurface conditions,” said David Sostarich, Strategic Business Manager at Halliburton. “Surface data is gathered thousands of feet away from the drill bit, but in-bit sensing allows us to see what’s happening from a downhole perspective. It gives us a clearer picture of what’s going on at the bit-to-rock interface and provides us with better insights into design. We’re looking at where lateral vibration, axial vibration, stick-slip and whirl are happening, and then marrying that information with bit design, selection and implementation.”
In one Williston Basin project, data from the in-bit sensors helped the company to design a Cerebro drill bit. Field test data showed the bit achieved the fastest ROP, while minimizing torque, at points when the rolling element engaged with the formation. As the rollers engaged, the torque was minimized, thus increasing ROP. However, the sensor data also showed that rollers were only engaged for small percentages of each test run.
Halliburton then decreased the depth of cut at which the rollers were engaging, a move that enabled the rollers to engage for a greater percentage of the run and increase ROP. Whereas the highest ROP prior to the change was 113.0 ft/hr, ROP post-change maxed out at 160.2 ft/hr.
More recently, Halliburton added another tool to its bit-design toolbox – Oculus, which is an automated software program that serves as bit dull grading system. Launched in 2021, the software uses machine learning algorithms to capture precise dull information for individual cutters on a bit. The program analyzes images taken of the bit after it has been pulled out of hole and catalogues the data in a cloud database. It then automatically grades the wear on each cutter.
By automating the dull grading process, the subjectivity of visual examinations by human inspectors is eliminated, and Halliburton gets more precise measurements and classifications of bit dulling. It also becomes easier to utilize the dull analysis over a large number of bits, including during the testing phase of the design process, Mr Sostarich added.
“When we would evaluate drill bits previously, we would see a lot of subjectivity, even utilizing the IADC code. One individual might grade a bit a 1-2, another might grade it a 1-3 and another might grade it a 2-3. What we wanted to do with Oculus is take a digital image of each cutter, input it into the system and give it a more specific and objective grade, so we can take these very subjective things and turn them into objective data,” he said.
Oculus is utilized at Halliburton’s service centers globally for fixed cutter dull analysis. Its newest Hedron fixed cutter platform, launched in 2022, utilizes Oculus as a key component of design for more efficient and durable PDC bits.
In one project last year, the company worked with a directional driller in the Middle East that was looking for a bit to help increase ROP. Halliburton, using historical data of similar formations, picked its Hedron PDC bit with Geometrix shaped cutters in the shoulder area as a starting point. In subsequent simulations and testing, it was found that decreasing the diamond volume negatively affected the bit’s stability and exacerbated minor breakage seen in the shoulder during formation transitions. This finding led Halliburton to look for ways to alter the design profile to increase cutter efficiency and minimize the potential for instability.
Based on data provided by the Oculus system, the company kept the same profile and cutter positions as the reference bit, but it introduced an optimum back rake scheme to increase efficiency and lower susceptibility to impact damage. After a test run in Halliburton’s proprietary modeling software, the cone, nose and shoulder were examined before adjusting the back rake regime. No changes were made in the cone area of the bit, as design simulations performed in its bit design software indicated that such changes might lead to over-engagement of the cone cutters, which could lead to aggravated vibration levels and increase the potential for downhole dysfunction.
A final test run in the modeling software saw a 26% increase in bit efficiency compared with the reference bit. Then, a field test of the updated bit set a field record for ROP – 81.2 ft/hr, nearly 12 ft/hr higher than the previous record of 69.6 ft/hr.
“Oculus has really helped us in terms of understanding – at scale – how cutters perform in many different applications, whether that’s abrasions, impact environments or thermal-type environments,” Mr Sostarich said. “We’re able to make better selections on introducing new technologies to our customers.”

Collaboration and performance
NOV uses a wealth of software programs to help operators find the right drill bit. Terra-Scope, the company’s long-standing downhole seismic monitoring system, analyzes rock strength data and outputs the most likely failure mechanisms for the target formation. For example, it can determine whether the bit is more likely to fail under stress – which would require 3D-shaped cutters – or more likely to fail under strain – which would require full round cutters. The company then uses its Orbits software to run simulations showing how a given bit design might perform with rock properties specified by the operator.
Despite the sophistication of software like Terra-Scope and Orbits, there’s still a lot of work required from field engineers to “sort through all the different things that can happen on a rig or happen to a bit while drilling a well,” NOV’s Mr Jennings said, adding that looking at all the data available and making sound recommendations requires a lot of coordination.
This is why NOV Engineer Brice-Herve Benie said he believes the drill bit selection process is actually all about collaboration with the operator. Choosing a profile to run in the Orbits simulator, for example, is typically a back-and-forth process, with the operator providing its performance targets and outlining the limiters it has identified while drilling the formation in previous runs. “It might take two or three iterations for us to come up with the right profile for the operator to maximize value from the application,” Mr Benie said.
Especially in basins like the Permian, where operators drill a variety of hole sizes in every rock formation imaginable, drill bit designs need to be more customized. In these cases, initial field testing often proves extremely valuable. While the simulation software provides a good estimate of how the bit will perform – providing theoretical potential for vibrations and aggressivity, for example – a physical run is still often required to get a clearer picture of specific elements of drill bit performance. For instance, NOV runs add-on applications to its simulation software that analyze the potential for downhole dysfunctions like whirl and stick-slip, but the models that are programmed into those add-ons can only provide estimates.
While the process of selecting a drill bit has remained relatively unchanged over the years, NOV says where it has made the most progress is in terms of using bits to improve operators’ drilling performance. This includes taking the insights gained from previous bit designs to achieve efficiency gains in future projects – in particular, the company has been focused on improving cutter grades and cutter shapes to help make the bit more stable and increase its durability.
“The way that operators are going to save money is by reducing the amount of days to drill a well,” Mr Jennings said. “ROP in single intervals has reached a critical point, so now we’re looking at how we can do more intervals with the same bit so we don’t have to trade for the same set of tools. That presents a unique challenge for the cutters because now you’re going through different types of rock failures in the same run. We’re looking at how can we build a cutter array that will go through an abrasive shale, back into an abrasive sand, then back into a shale – all in one interval without needing different bits to drill independently.”
In March 2022, NOV launched its ION+ 5DX cutter, which incorporates a working ridge that is designed to withstand sudden impacts while imparting high compressive loads into the formation. The goal with the layout of these cutters is to minimize impact damage while maximizing ROP. The company said that the 5DX has shown a 60% increase in material toughness – or the amount of energy per unit of volume that a material can absorb prior to rupturing – over the average of commercial cutters.
“The cutter group is constantly working on new cutter grades, trying to improve the cutter shape and the array,” Mr Benie said. “As we make cutters that are more impact-resistant, we can be more aggressive on the design side and help our clients exceed their targets. If an operator can drill 9,000 ft of lateral in 24 hours, we can help them drill the same distance in less time tomorrow.” DC