Aluminum alloy drill pipe helps navigate complex well offshore Brunei
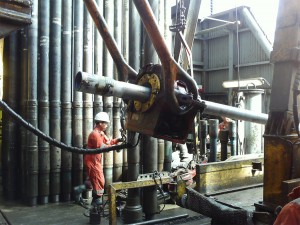
Alcoa Oil & Gas has deployed 1,800 meters (5,905 ft) of aluminum alloy drill pipe (AADP) in the Iron Duke Well C offshore Seria, Brunei. The Brunei Shell Petroleum (BSP) well is considered among the most complex and deviated in the BSP system, with three S curves and a long horizontal section of approximately 5,000 meters (3 miles). It was drilled to a total depth of 7,485 meters (4.6 miles) in about 60 meters (197 ft) of water.
“The AADP, which is produced in 30-ft (9.1-meter) aluminum tube sections and joined together using standard steel connections, is about 40% lighter than all steel pipes and has the potential to significantly reduce drill string hook load and related drilling torque and drag,” Jay Grissom, marketing director of Alcoa Oil & Gas, said.
Alcoa’s pipe starts with a tapered, high-strength, aluminum alloy tube that is coupled with a steel tool joint using a proprietary thermal connection technology that allows steel tool joints to be attached to the aluminum pipe body. Alcoa produces the aluminum tubes at its Lafayette, Ind., facility and assembles the finished drill pipe at its facility in Houston.
“We are constantly challenged to push the drilling envelope further to maximize recovery and minimize cost,” Shayne Dustin, senior well engineer for BSP, said. “Light alloy pipe was listed as a performance opportunity to help us tackle some of the challenges we face with reduced cantilever loading, high torque, high drag, high sideforce and casing wear concerns. Without a light alloy alternative, the furthest reaches of the platform would require a modification to well design.”
BSP plans to use AADP on additional wells in Brunei. Shell is also planning a drilling project using AADP in New Zealand.
AMRTUR, Alcoa’s service partner in the project, led the staging, inspection, maintenance and deployment of the aluminum drill string.
AADP is a registered trademark of Alcoa Oil & Gas.
can you participate on tender to supply drilling pipes