PETRONAS designs, deploys drilling fluid to reach 488°F well offshore Malaysia
By Joanne Liou, Associate Editor
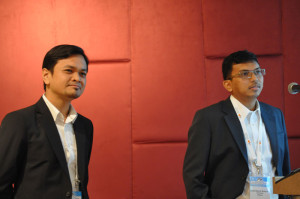
Offshore the Malaysian peninsula, PETRONAS Carigali recently deployed a fit-for-purpose, synthetic-based mud to drill an ultra-HPHT, deep gas exploration well. PETRONAS collaborated with Baker Hughes to formulate a thermally stable, high-density drilling fluid for the well. It was drilled to 14,380-ft TD and reached the highest recorded temperature of 488°F and highest recorded mud weight of 19.1 ppg in Southeast Asia, Mohd Abshar of PETRONAS stated. Mr Abshar and Khairul Nasrudin, also of PETRONAS, shared the operator’s work at the 2014 IADC/SPE Asia Pacific Drilling Technology Conference in Bangkok on 26 August.
Mr Nasrudin defined ultra-HPHT wells as those with reservoirs pressures from 20,000 to 30,000 psi and temperatures between 400 to 500°F. “Generally speaking, the max temperature can cause limitation on chemicals, HSE issues and low equivalent static density,” he said. The key objectives of the drilling fluid design was for the fluid to:
- Contribute to zero NPT;
- Be thermally stable with high density and no barite sag;
- Have no excessive equivalent circulating density; and
- Control fluid loss under HPHT wellbore conditions.
Fluid properties were maintained with a thermally stable emulsifier package. “As a rule, if you use ultra-HPHT fluid, you need a ultra-high temperature emulsifier package so it will last,” Mr Abshar said. A big-bowl centrifuge was used to maintain low-gravity solids below 5%, he added.
“We also used dual-density, weighting agents: barite and manganese tetraoxide,” Mr Abshar said. “This is actually very key in achieving performance in barite sag and stable rheology when it was above 450°F.” The use of the weighting agents yielded lower viscosity for the high-density mud, improving hydraulics and lowering equivalent circulating density. The fluid had high temperature stability with no weighting agent sag and no high-temperature gelation observed after remaining static for five days at bottomhole temperature during wireline logging.
From initial circulation downhole, bottom-up after wireline logs and after logging, the mud was not reconditioned. “That’s how we saved at least three to five days,” Mr Abshar noted. “The biggest success is the cost savings achieved through rig time associated with fluid design and management.”
For more information about the drilling fluid, see IADC/SPE 170557, “Novel Drilling Fluids Enable Record High-Temperature, Deep-Gas Exploration Well Offshore Peninsula of Malaysia.”