H&P delivers reliability, safety with computerized rig maintenance systems
By Katie Mazerov, contributing editor
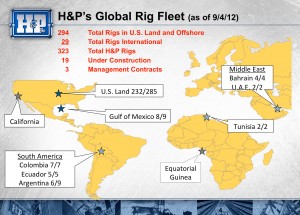
Increasingly complex drilling conditions and advanced well designs that are extending measured depths and stepping up requirements for hydraulics, torque, pressure and downhole motor and surface RPMs are raising the bar on drilling contractors’ rig maintenance and performance systems. That was the message delivered by David Millwee, regional vice president for Helmerich & Payne’s US Land Division, at the 2012 IADC Critical Issues Middle East Conference, 4-5 December in Dubai.
“Over the last two years, industry has reduced the overall well cycle by 15% to 20% and, at the same time, increased well depths by 10%,” Mr Millwee said. “We need to have proven maintenance systems along with established procedures and trained personnel to consistently run equipment at maximum original equipment manufacturer (OEM) design parameters in a safe, reliable manner.”
H&P uses a computerized rig asset management system (RAMS) and network infrastructure to drive down overall well costs and improve economics and growth opportunities for operators. The companywide, web-based system serves H&P’s entire rig fleet, which has tripled over the past decade to 323 rigs, operating primarily in the US but also in South America and the Middle East, including North Africa.
“RAMS incorporates industry-based practices, OEM recommendations and regulatory standards that work in combination to define how we can optimally service and maintain equipment,” Mr Millwee said. “It leverages the technology we have to connect in remote locations and measures how well we’re performing in terms of everything that is in the critical path of the well, including the top drive, drawworks, pumps, blowout preventer (BOP) and motors, especially as we continue to drill longer and longer laterals.”
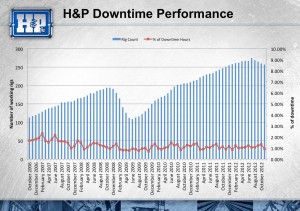
H&P also uses standardized equipment throughout the fleet to simplify the maintenance and repair process for rig crews, who learn one method that they can repeat across the board.
Key features of RAMS include:
- Statistical metrics for measuring ongoing maintenance tests and how effectively workers are using the rig;
- Companywide sharing of lessons learned;
- Up-to-date equipment historical records;
- Standardized technical information for equipment;
- Use of email, Smart phones and tablets to ensure rig crews are receiving information immediately and in ways they can easily access;
- Equipment maintenance planning;
- Documenting knowledge in the training process;
In using RAMS, H&P has been able to maintain a maximum downtime percentage of 1.5% even as the company has increased its rig fleet and footage drilled; significant improvements in safety have also been achieved. “Knowing what equipment is coming up for maintenance allows for better planning in terms of costs, prolongs the life of the equipment and also promotes safety,” Mr Millwee said.
In 2011, the company had 23 incidents per million ft drilled; this year, that number is down to 1.6 incidents per million ft drilled. “This improvement is in light of the fact that, over the last two years, our footage per day has increased by nearly 35% and well depths by almost 20%,” Mr Millwee noted. “Safety also translates to efficiency. By scheduling maintenance, we also can prevent catastrophic failure. In this industry, you can pay now or pay later, but if you pay later, you’re always going to pay more.”
RAMS is a trademarked term of Helmerich & Payne.
I would really appreciate it if Mr. Millwee would contact me regarding casing runnning tools for their rigs. We believe our tools will assist in additional NPT for H&P.