Sharpe: Let’s innovate the innovation process itself
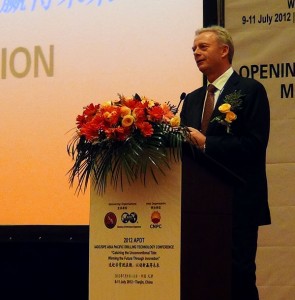
By Linda Hsieh, managing editor
Rather than simply looking to technological innovations, the drilling industry may need to start innovating the innovation process itself, Peter Sharpe, Shell executive VP wells, said at the 2012 IADC/SPE Asia Pacific Drilling Technology Conference on 9 July in Tianjin, China. Organizations tend to be linear, where the innovation process is like a one-way pipeline. “There’s not really any real feedback loops, and they tend to be quite slow,” he said.
With the opportunities the industry has, for example, in unconventional resources, the industry will have to make significant changes in the way innovations are adopted. “We can take 20 to 30 years in our technology maturation. That’s just not going to be acceptable if we’re going to meet the energy challenge of the next century,” Mr Sharpe said. “While R&D plays a key role, it in isolation won’t deliver the pace of change that we’re going to need. We need not only faster research efforts but faster development, deployment and replication of that technology.”
Particularly in the areas of automation and control systems, Mr Sharpe sees a significant opportunity for more open innovation – such as collaboration between academia, contractors and operators. He cited one open innovation project under way at Shell related to the automation of BOP control systems, where the goal is to eliminate the possibility of human error.
“Innovation today in our industry is done on a proprietary basis. I think there’s a real call-out there for a more open innovation. In many other industries, that’s really provided a much faster pace of progress than we’ve had,” Mr Sharpe continued.
He believes that no business can rely solely on its own proprietary efforts to solve its problems, and companies must work more together collaboratively. “That’s the challenge I’m putting out there, is how can we innovate innovation itself?”
The second challenge is to look at how technologies can work with one another in a more integrated fashion. “Technology tends to add value as part of an integrated system, but it rarely operates in isolation. Again, looking back at the R&D process, how do we get more system thinking into the equation?” Mr Sharpe asked.
Deployment and replication also must be part of the early thinking in the innovation process. “Otherwise you get this very slow pace of technology development that we’ve seen historically in our industry,” he said. This will require employees in the front line to be much more involved earlier in the technology maturation process.
Referencing Shell’s joint venture well manufacturing project with China National Petroleum Corp, Mr Sharpe noted that, in order to develop the world’s natural gas supplies in a sustainable fashion, “we’re going to have to do much better than we are today.” Automation will be needed that can mass produce wells, that can control the downhole process and that can improve operational performance. “No matter how skilled humans are, they’re always going to make mistakes,” he said. Using machines to help eliminate vibration, minimize doglegs, maximize mechanical specific energy to drill faster using fewer bits and rigs with less environmental impact – that will all be part of the next step-change the industry must make, Mr Sharpe added.
This also will facilitate the transfer of knowledge and information from one project to the next. “This is about how quickly we can replicate technology,” he said. In Shell’s Pinedale operations in North America, for example, it took a decade to reduce the number of days per well from 60 to 20. “In Groundbirch, it took only three years to achieve the same learning curve. In Sichuan, China, we actually achieved that same learning curve in one year,” Mr Sharpe said. “We need to produce more energy for the growing population of the world. Technology and innovation will be absolutely critical. We must find ways to speed up the development, deployment and replication of technology in our industry.”