Wired pipe delineates safer drilling margins
Along-string pressure, temperature measurements in real time can lead to earlier detection, management of well control incidents in deepwater
By Daan Veeningen, NOV IntelliServ
In the post-Macondo world, government agencies have promulgated significant new safety standards to ensure the safety of workers, environment and assets. These new safety measures and regulations include enhanced drilling safety, increased inspection and improvements to workplace safety regulations. The US Bureau of Ocean Energy Management (now the Bureau of Safety and Environmental Enforcement) panel report regarding the causes of the Macondo blowout, which was released 14 September 2011, is an example of some of the regulations that could take effect.
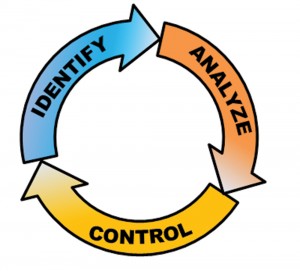
Besides new processes and training for personnel, there is also emphasis on developing and deploying new technology to aid in earlier identification of a wellbore influx, in improved analysis once these well control events unfold and in enhanced ability to regain control. Supplementing surface data with acquisition of downhole data in real time improve the ability to identify, analyze and, ultimately, control events (Figure 1).
Examples of valuable data acquired downhole are annular pressure measurements, downhole sonic and look-ahead seismic measurements. Annular pressure aids in identifying an influx, and acoustic waves may offer insight in pore pressure and trends ahead of the bit. The accurate prediction of formation pressure is not only crucial for casing point selection but most imminently for selecting the optimum drilling fluid density to deliver the hydrostatic density to balance formation pressures.
In particular, downhole sonic and acoustic data represent large data volumes. Transmission to surface relies on wireless protocols, such as mud pulse and electromagnetics. While improvements have been made, the achieved rates are dozens of bits per second (bps) and deteriorate to single bps as drilling depth increases.
Wired or networked drill pipe can offer a step-change in data transmission speed. Networked drill strings incorporate distributed temperature and pressure sensors and have the potential to transform management of downhole incidents, especially in deepwater, where the risks and consequences are significant.
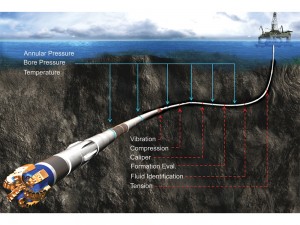
Faster, Bi-directional Data Transfer
A high-bandwidth downhole data transmission system via a wired or networked drill string system, such as the IntelliServ Broadband Network, provides real-time pressure and temperature measurement from discrete locations along the drill string (Figure 2).
Networked drill strings have made significant strides in speed, system integration and the number of measurements afforded. At a data transmission rate of 57,600 bps, the system can transmit data acquired by any of the large service companies and can transmit pressure and temperature measurements from along the drill string by allocation of an additional 57,600-bps bandwidth. This system has been deployed on 90 wells totaling more than 1 million ft.
The bi-directional transfer of information at high telemetry rates through the networked drill string allows for faster update of geology and geophysical information and reduces geological uncertainty. It also provides greater control of the bottomhole assembly while operating rotary steerable tools and conducting formation pressure testing. The ability to send commands to these downhole tools via the broadband network provides instantaneous tool control, real-time tool diagnostics and troubleshooting, replacing the conventional downlinking.
Real-time transfer of high-definition logging-while-drilling information helps subsurface personnel to obtain the facts needed to control placement of the well when it matters most – in real time. Safety – specifically for deepwater operations – may be improved by supplementing downhole information to the existing surface data.
The section below offers examples for each of the “identify, analyze and control” elements of the safety management system.
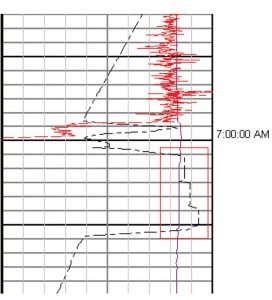
Safe Drilling Margin
In reference to a safe drilling margin, the panel report’s well recommendations suggest the term should be “expanded to encompass pore pressure, fracture gradient and mud weight.” High-bandwidth bi-directional communication with downhole tools allow the three elements comprising the safe drilling margin to be established independently for surface measurements.
Identifying the pore pressure, the first element of the safe drilling margin, is routinely accomplished with a formation pressure test (FPT) tool. The operation of formation pressure testers is highly efficient using the bi-directional communication capability, as the time to conduct a pressure test is reduced on average by 50% in the Gulf of Mexico. This not only reduces the chance of getting stuck through reduced stationary time, but it also offers quality control in real time during drawdown – even with pumps off – instead of relying on communication via downlinking and mud pulse that require flow.
In a recent deepwater well, 54 FPTs were taken. Nine tests were tight while 39 tests were taken, exploiting the ability for real-time quality control similarly to the feedback when testing on wireline. The 12 ¼-in. testing tool with 14-in. extension pad tested successful in five tests in the 14 ½-in. hole at 18° inclination. A seal couldn’t be established in six tests in the large hole with well inclination below 8°.
The series of 54 FPTs were conducted in 7 min per test on average. This equated to a time savings of approximately 8 min per test in this Gulf of Mexico environment, achieved through efficient two-way communication with the downhole tester.
The quality control eliminated the need for a wireline run to evaluate the formation pressures, and additional savings included time for the actual wireline log, as well as the time for a check trip after the log-run. Figure 3 shows the three good tests that were achieved in 17 min.
The fracture gradient, the second element that comprises the safe drilling margin, is routinely measured by conducting a leak-off test. While tools provided by service companies record annular pressure, a networked drill string system makes this data available in real time as the test is ongoing in the absence of flow. Further, the compounding annular pressure and temperature measurements at various network nodes reveal information about the compressibility and difference in fluid densities through the annulus.
These downhole hydrostatic measurements help identify the third element of the safe drilling margin: true mud weight. The hydrostatic column in the annulus may have heterogeneous fluid densities because of temperature and compressibility effects, as well as the presence of slugs and sweeps. The pressure measurements at various positions of the drill string ease the determination of the safe drilling margin and evaluation of effects that may cause U-tubing or distort observations at surface.
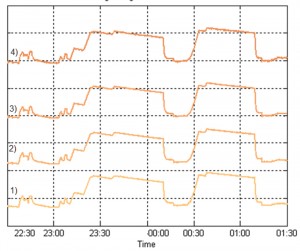
Earlier Kick Detection
Early detection and quick response time is imperative in deepwater operations. Detecting influxes is challenging when the information is based on surface measurements alone and when data is slow to reach surface.
The Macondo panel report stressed that, especially in deepwater, “prompt kick detection is critical in deepwater operations with a subsea BOP stack. … If the kick is not detected until after the hydrocarbons rise above the BOP stack, then well control response options are severely limited and the risks of a blowout are significant.”
The network drill string’s early identification of kicks improves safety margins as corrective actions can be taken while the event is limited in size and more easily managed. Figure 5 shows an example of a well influx occurring at the bit while drilling, as well as the decision flowchart that is afforded by the networked drill string.
At initial conditions (time t=0), the incoming formation fluids are still located below the pressure sensors, and the absolute pressures and gradients remain unchanged. As drilling goes on, the formation pressure continues to exceed the hydrostatic (dynamically exerted) pressure, and formation fluids continue entering into the wellbore (t=1).
The pressure sensor nearest to the bit (Sensor 1) is the first sensor to record an annular pressure reduction. As the influx height increases to the next sensor (Sensor 2), the corresponding pressure gradient is reduced between the two deepest sensors that are the nearest to the bit, while the gradients in the sections uphole remain unchanged. At times t=2 and t=3, as the wellbore influx passes Sensor 3 and Sensor 4, the gradients in these subsequent sections decrease as well.
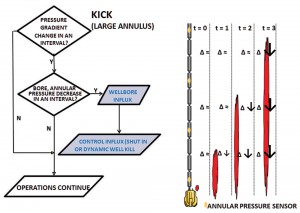
In a kick/loss situation, networked drill pipe running in a fully automated managed pressure drilling system delivers a response time of less than 10 seconds, allowing the system to quickly increase or decrease equivalent circulating densities (ECD) and automatically circulate out kicks while maintaining the desired wellbore pressure profile.
Migration of an Influx up the Annulus
The location of the influx and the type of influx can be determined through pressure measurements independently from surface measurements. Once the influx is identified, maintaining and controlling bottomhole pressure is made possible based on direct downhole measurements.
The network’s ability to take multiple distributed pressure measurements along the length of the drill string allows developing well control issues to be accurately analyzed and characterized. The downhole data, independent from surface data, is available both at stationary conditions with the pumps off, as well as with the pumps on. For example, the network’s processing system can determine if the measured standpipe pressure, measured bottomhole ECD or other measured drill pipe or annulus pressures are increased or decreased relative to the expected values.
Figure 6 shows a phenomena in the annulus initially identified at Sensor 1, which has migrated beyond Sensor 2 and Sensor 3. The pressure responses at each sensor – see insert within Figure 6 – demonstrate the pressure response at it travels the annulus toward surface.
The along-string evaluation is not limited to open hole or within casing. In deepwater wells, the marine riser itself can be thousands of feet, and sensors in that section are helpful in analyzing gas migration in the unfortunate event when gas passed the BOPs. This analysis capability then helps in deciding between lining up the mud-gas-separator or to divert the flow overboard.
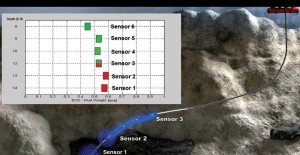
Wellbore Integrity by Negative Pressure Testing
The leading well recommendation in the panel report calls for “regulations that require the negative pressure testing of wells where the wellbore will be exposed to negative pressure conditions, such as when the BOP and riser are disconnected from the wellhead during permanent or temporary abandonment procedures.”
Today’s procedures and interpretation of negative pressure tests rely on surface measurements for verification of wellbore integrity. Adding complexity to the already limited data stream during the test is the possibility for heterogeneous fluid density columns in the annulus and the chance for a plugged choke and kill lines or misaligned surface valve.
Downhole measurements help analyze independently of surface measurements the pressure buildup that may follow once the drill string is displaced with a lighter fluid (typically base oil or water) following stinging into a downhole circulating packer. Alternatively, the pressure build-up can be monitored downhole once the choke and/or kill line have been displaced with lighter fluid and the BOPs have been closed.
In both methods, the bore and annular pressure measurements at the various measurement stations along the string are independent from surface measurements and complement one another to discriminate from false negatives.
Well Control
To regain well control, wellsite personnel must circulate out the wellbore influx and replace the fluid column with denser mud. During this process, constant bottomhole pressure must be maintained to prevent additional wellbore influx. Constant bottomhole pressure is achieved by carefully operating the choke to keep adequate backpressure and is historically achieved based on surface measurements.
With the networked drill string, however, wellsite personnel are afforded high-resolution downhole and annular pressure readings along the string. This additional downhole data is available regardless of flow, providing accurate hydrostatic pressure even at typical kill-rates of 10-20 strokes per min.
A pressure gradient between the various measurement stations along the string provides for monitoring the influx and/or the kill mud as it travels up the hole (Figure 6). This method complements – or replaces – the conventional, manual well kill sequence. The kill-sheet may have to be performed under time constraints and stress by personnel who may have limited exposure or experience with well control events.
The additional high-frequency downhole not only improves safety and accuracy but also allows for the well to be dynamically killed, improving efficiency and saving rig time.
Well Kill Using Relief Wells
Relief-well drilling in the wake of a blowout requires accurate steering to intercept the target well. Steering commands – with confirmation – take seconds compared with minutes without bi-directional wired communication. Additional benefits are offered by the downhole pressure measurements during the dynamic well kill by transmitting data even while experiencing the U-tubing effect at the time of intercepting the flowing target well. The distributed along-string pressure evaluation provides a pressure gradient, which offers additional insights during the well kill and subsequent bullheading operations.
The IntelliServ networked drill string was deployed to drill one of the two relief wells in deepwater Gulf of Mexico in summer 2010. Specifically, experts involved were keen on identifying the downhole pressure upon interception with the flowing well to analyze the pressure. Ultimately, the top kill controlled the well.
Summary
Deepwater operations face new safety standards to ensure the safety of workers, environment and assets. Networked drill strings offer downhole measurements in real time for the identification, analysis and control independently from surface measurements. This redundancy aids the safety in three examples:
• First, the networked drill string provides downhole data independently from surface measurements to identify pore pressure, fracture gradient and effective mud weight that comprise the safe drilling margin;
• Second, the independent along-string pressure evaluation provides early kick detection and improved ability to analyze and control an influx even with heterogeneous mud column; and
• Third, methodologies are offered to conduct negative pressure tests to bolster the conclusiveness of the inflow simulation. An influx can be identified and analyzed even if it has already passed the BOPs into the riser. This methodology helps decide between lining up the mud-gas-separator or diverting the flow overboard.
Recommendations and Future Work
Beside the annular and bore pressure sensors that are currently available, developments are ongoing to determine flow rate at distributed measurement stations along the networked drill string. These flow rate sensors, as well as fluid identification sensors, would provide additional means for kick detection and lead to better well control.