Rig design shift would put MPD at the ready
Industry coordination needed to drive rig designs with MPD components built in, more deployments in deepwater
By David Pavel, Weatherford International; Gavin Humphreys, Stena Drilling
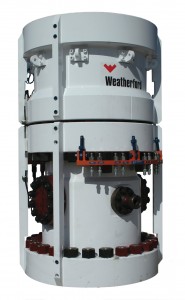
The rocks being drilled today demand more than a better set of tools; they require a different approach to well construction. That change is occurring in the form of managed pressure drilling (MPD), which resolves many traditional subsurface problems with the visibility and control that comes from replacing the rig’s traditional open-to-the-atmosphere circulating system with pressurizable, closed-loop technology.
Nowhere is this ability to minimize and eliminate subsurface problems more important than in the extremes of deepwater drilling. In these applications, where process safety is paramount, narrow-to-nonexistent drilling windows and high-temperature, high-pressure wellbores routinely challenge safety, economics and the ability to drill the well.
Despite its advantages, application of deepwater MPD has been limited. Time constraints drive an array of costs, and people and deployment limitations make it especially difficult to deploy the technology on deepwater semisubmersibles and drillships.
Overcoming these constraints requires a coordinated industry effort focused on the development of guidelines, procedures and standards for equipment procurement, rig modification and design, and training for all stakeholders in the drilling process.
Ready to drill
The goal is an MPD-ready rig. Today, however, “ready” describes a rig that is ready to accept MPD components, not one that has already been outfitted with MPD components. Parameters such as riser IDs, rotary table IDs and deck requirements can accommodate MPD equipment. Readiness also depends on experienced personnel, cost efficiency and the ability to deploy an MPD system concurrent with an operator’s drilling schedule.
There can be many constraints to the deployment of MPD. Fundamentally, MPD is still a niche player in deepwater provinces. Operators and drilling contractors have limited expertise in planning and executing MPD operations. Each application typically begins anew, requiring a lengthy training process for rig and operator personnel on safety and operational procedures. This situation is further complicated by such variables as rig configuration and type of MPD application.
Equipment cost is primarily an issue of scale. Highly specialized marine MPD components, such as Weatherford International’s Sea Shield series of riser-integrated rotating control devices (RCD), are being used effectively aboard deepwater vessels. Still, the relatively small number of applications makes MPD capital equipment expensive and lengthens procurement times even for ancillary equipment items.
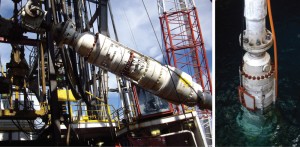
New and existing rigs
The shift to MPD-ready rigs must address both the existing rig fleet and newbuilds. Perhaps the greatest challenge in refitting an existing rig is the general lack of standardization across deepwater rig designs. As a result, it is difficult to deploy an MPD system on an ad hoc basis. Each requires a customized approach.
While most MPD equipment components are familiar to rig operations, an MPD package requires special accommodation that is typically problematic for existing semisubmersibles and drillships. A rig survey is usually performed to establish deck loads and footprints, power and other MPD requirements. Modifications are often required, which can add significantly to time and costs.
In some cases, major modifications must be made to riser components, such as slip joints and tension rings. The long lead times that result can exclude MPD as a potential solution for an operator or a particular well.
Newbuild rigs similarly require special design considerations. However, they present a different challenge. In recent times, many deepwater rigs have been built on speculation, without contracts and by non-drillers who are not attuned to the subsurface demands driving MPD use.
The industry must communicate the desirability of MPD-ready designs along with the required specifications if MPD is going to be available when needed.
Mid-term steps
Making MPD more available for deepwater drilling requires a coordinated effort on multiple fronts to streamline and standardize as much of this process as possible. At stake is an immediate improvement for process safety and the ability to mitigate and eliminate many pressure-related deepwater drilling hazards.
This MPD effort must initially develop a procurement process to reduce the cost and time of acquiring and deploying equipment to location. MPD components and configurations must be clearly specified for various MPD applications to aid planning and shorten lead times. To reduce lead time, drilling contractors will deliver ancillary equipment while service providers will continue to supply MPD-specific equipment.
Rig modifications must also be identified and templated to provide a clear process for implementing an MPD refit. Specifications should be developed for MPD “kits” to match MPD configurations to various rig models. The specs should describe such basics as deck loads and footprints, as well as flow lines, air, electrical and hydraulic connections.
Other factors should be considered as well. For instance, the riser connectors should accommodate MPD riser components, including the flow spool, operational annular preventer and RCD. The riser ID must allow pass-through of the bearing assembly, which involves the tension ring, telescopic slip joint and upper ball joint. The rotary table ID should accommodate pass-through of MPD riser components consisting of a flow spool, operational annular preventer and RCD.
Interface documentation between the MPD process and rig is a necessary objective. In the long term, this document will become an industry best practice. Generic procedural templates can be developed that address about 80% of the MPD process, with the rest customized according to job, rig and well factors.
Efforts by IADC to develop MPD best practices are a welcome step toward this level of documentation. Similarly, IADC provides examples in industry training.
Development of industry training standards for MPD is critical. Safety and performance depends on an understanding of MPD operations that equals conventional drilling operations. Achieving this routine level of MPD requires a thorough training effort at all levels. Training courses similar to existing well control courses must be developed for contractor and operator personnel.
Long-term outlook
The growing number of MPD systems installed aboard deepwater vessels will lead to continuing improvements in process safety as rigs regularly apply MPD to manage wellbore pressures. Time and cost constraints will continue to diminish with increased use and improved processes.
There are MPD-ready deepwater rig designs that provide built-in capability to address the availability issue.
Stena Drilling’s DrillSLIM drillship and semisubmersible designs are smaller vessels aimed at reducing the cost of deepwater wells by slimming down the well design and drilling the wells with a high-pressure riser and surface BOP (SBOP) on which the MPD surface equipment is installed.
The Stena “Advance” semisubmersible design features an independently compensated MPD platform configured to support an inner high-pressure riser, locked into the lower marine riser package (LMRP) and an MPD frame in which the MPD equipment is permanently installed.
The MPD drilling process then takes place through a high-pressure inner riser, with returns fluid being diverted below the RCD, through the choke manifold and finally back to the shale shakers.
With, for example, the main body of Weatherford’s riser-integrated rotating control device permanently installed on the rig, the provision of dual-gradient drilling (DGD) could be achieved. DGD is a deepwater technique in which the riser is displaced with seawater or the riser is partially evacuated to reduce the weight of the mud column from the seabed to the rotary table.
Further, with this equipment, permanently installed pressurized mud cap drilling techniques, which enable drilling in total loss circulation wellbores while maintaining pressure on the drilling annulus, could also be achieved.
Building MPD capabilities into the rig provides a solution from the outset. The “DrillSLIM” or “Advance” designs cut or eliminate lead times because equipment is in place and contractor personnel are already trained. Drilling operations can transition from conventional drilling to MPD methods as and when needed to address wellbore conditions.
The availability of MPD-ready rigs also encourages the incorporation of MPD capabilities into candidate selection and well planning.
As MPD becomes more commonly applied, ownership of critical riser items will transition to the drilling contractor, including the flow spool, operational annular preventer and RCD housing. This will enable MPD deployment as a standard package – a plug-and-play solution.
The development and refinement of industry standards and procedural templates, along with a growing industry expertise, will continue to enhance performance and reduce costs.
These advances, along with the growing subsurface demands and uncertainties, will yield an MPD-ready rig fleet that will write the next chapters in deepwater drilling operations.