Real-time force monitoring improves CT drillout efficiency
Interactive tubing force analysis models, real-time data overlays reduce stuck pipe, NPT
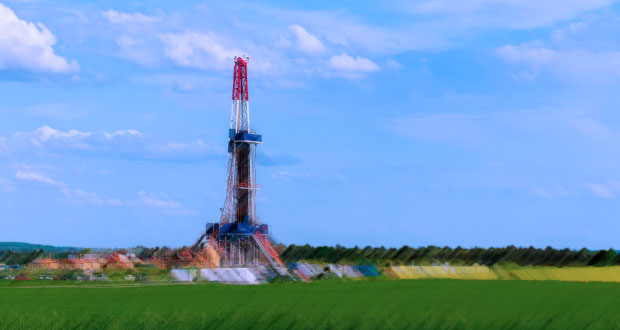
By Jessica Stump, Travis Thomas and Colt Ables, NOV
Considerable progress has been made in advancing methods and procedures for well intervention operations with coiled tubing (CT). However, stuck-tubing events are still common in post-fracturing drillouts. Most analysis happens after these incidents have occurred, despite technology allowing for real-time viewing and engineering analysis of these operations.
Between 2005 and 2010, horizontal drillouts became common in the Barnett and Haynesville shale plays. The industry rapidly standardized the operational procedures for horizontal plug-and-perf operations. The main standard operating procedures (SOPs) transferred over were weight checks to determine that CT was safe and free. However, CT technology used to analyze the operations in real time did not follow suit at the same pace.
CT modeling software and data acquisition systems (DAS) were used specifically to track string fatigue and record data for post-job analysis. Most field operations directly transferred vertical well SOPs to horizontal well applications. As horizontal well interventions became common, each operation was pre-modeled with a tubing force analysis (TFA). However, the TFA was used to determine if the CT could reach total depth (TD) but was not shared with field operations.
Engineering tools like force monitors have been available since 2014. However, their use in North American operations have been limited because multiple short-cycle downturns removed engineering resources from the field. The online migration capabilities of these engineering tools have improved as the well site transformed from largely remote to a data-connected environment. The connection of the subject matter expertise, which has moved out of the field and into the office, has allowed the most informed resources to access critical operational data and provide real-time engineering feedback without ever having to be at the well site.
NOV’s CTES Cerberus intervention modeling software for planning and performing CT operations now features cloud connectivity to provide field operators, management and engineers with real-time access to the same data. This enables quick and inclusive operational decisions to be made before potential issues occur.
Interactive TFA models in the software, combined with real-time data overlays, improve the efficiency of post-fracturing intervention of horizontal wells with CT and prevent problems currently analyzed only after operations have been negatively affected. Operational efficiencies can be achieved with the following proactive real-time engineering approaches:
Use Cerberus to:
Create a digital twin of the CT string for calculating fatigue;
Create a digital twin of a wellbore so expected variables, such as dynamic friction, pressures and temperature, can be considered when applying calculations in the TFA; and
Create an Orpheus Force project (TFA) to generate the expected weight versus depth;
Run the Orpheus project to determine the coefficient of friction (CoF) reduction needed to reach plug back TD;
Using historic basin data, determine the acceptable deviations from the modeled run in hole (RIH) and pull out of hole (POOH) weights to ensure there is an agreed-upon stopping point;
Upload the Orpheus TFA into the CTES Live Real-Time Force Monitor so the live data can be overlaid on the model and deviations can be seen before operational issues arise; and
During the live job, adjust the model to account for current well conditions.
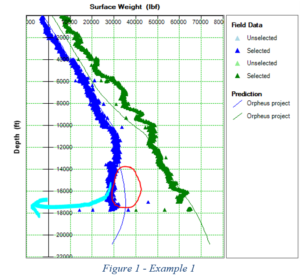
RIH deviations
If the RIH values are less than the planned values by the predetermined offsets, there is either debris in the wellbore, an underperforming extended-reach tool (ERT), weight indicator calibration issues, or the model needs to be updated for actual well variables, such as pressure and ERT friction reduction value.
Before moving farther in hole, determine the cause of the deviation. If the modeled data’s inputs have not deviated from the actual well conditions and the actual data previously matched the modeled data, the model did not cause the deviation.
If the measured depth is less than the 0.30 CoF lockup depth, an ERT performance issue did not cause the deviation. Bottomhole assembly (BHA) performance issues are indicated when there is an apparent friction increase prior to the 0.30 CoF lockup depth and the CT can still progress in the hole with clean weight checks, indicating no debris in the well.
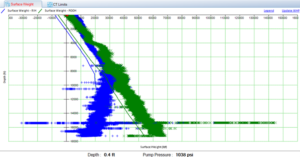
If debris is causing the deviation, a torque differential may be noticeable on the BHA, divergent pressures indicate bridging behind the BHA, or the CT continues to move in hole but only with increased set-down force and overpulls on weight checks.
For instance, during a job, a service company believed the CT was reaching friction lockup or a hard tag. The CT was pulled out of the hole to the surface, and the BHA was function tested. The CT tripped back in at normal speed and experienced the same issue at the same depth. The CT was pulled out of the hole again, and the BHA was changed. On the third run, the CT progressed to the bottom and completed the job with the replaced BHA. If the company used the TFA as shown in Figure 1, the underperforming BHA, specifically the ERT, causing the deviation would have been apparent. If the tools were changed on the first run, multiple trips could have been eliminated, reducing nonproductive time (NPT) and costs.
POOH deviations
If POOH values are greater than the planned values by more than the predetermined offsets, there is debris in the wellbore or weight indicator calibration issues.
To determine the deviation cause, verify the weight indicator readings versus the hydraulic calculations. If the weight indicator varies from the hydraulic calculations, calibrate the weight indicator and reevaluate the operation. If the weight indicator does not deviate from the hydraulic calculation, debris is in the wellbore. Pulling heavy can result in debris bridging and stuck pipe. Stop and circulate the well clean. If possible, RIH to assist in static friction reduction of the debris to increase removal.
For example, a 7,000-ft horizontal well with 5.5-in. 20-lb/ft casing and a 2.635-in. CT string was modeled before arriving on location. Data suggested that the approximately 17,000-ft TD could easily be reached with an ERT and a 0.30 CoF while pumping 5 bpm through the CT and taking 6 bpm returns.
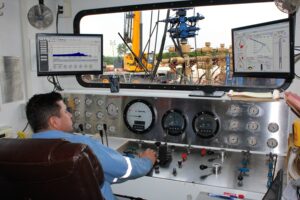
As shown in Figure 2, this well began with the weight data being offset from the TFA RIH line. The operator should have checked the TFA to ensure the input parameters matched the actual job conditions. A weight indicator issue could have also caused this offset. However, the weight was consistent compared with the TFA RIH line until they entered the horizontal. As the CT continued in the wellbore, the weight data deviated from the expected weight from the TFA, even though it was making excellent progress to TD. The weight crosses over the expected TFA line and remains on the “light” side of the line, which indicates more weight is required to RIH than expected. The most likely cause of this is excess sand in the wellbore. The CT made it to TD in 12 hours without issues.
After circulating for 20 minutes on bottom, the service company began to POOH at 35 ft/min. The circulation was too short, and the POOH speed was too fast. When looking at the force monitor, sand was most likely present. After 1,800 ft, the CT began to pull heavy and became stuck. After five days of circulating and pulling up to 140,000 lb, the CT was freed and removed from the wellbore.
The wellbore was cleaned during the five days, so little or no sand remained in the horizontal section. After the CT was freed, the POOH weight matched the expected POOH TFA line, although the offset from the beginning of the job remained. In a clean wellbore, the POOH weight data runs parallel to the expected POOH TFA plot.
The future of automation
Analyzing the data in real time to make operational decisions is a foundation for the future of CT, but not the goal. As real-time force monitoring becomes common, NOV is applying the same real-time force data to develop automated CT operations in the future. The TFA will be the roadmap to keep the operation on path and ensure it does not deviate from the plan. Automated CT will be able to streamline well interventions, capture lessons learned, apply improved processes, reduce the potential for human error in operations, and enhance efficiency and safety for all personnel.
Conclusion
While CT operations in horizontal shale plays have become standardized, the increased use of interactive TFA models and real-time data overlays will reduce stuck-tubing events, NPT and costs. Today, the tools to analyze and act on TFA deviations are available in most CT units. Real-time force monitoring improves drillout efficiency. DC
This article is adapted from SPE 208999, “Optimizing Drillouts Using Live TFA,” presented at the SPE/ICoTA Well Intervention Conference, 22-23, March 2022.
CTES, Cerberus, Orpheus and CTES Live are NOV trademarks.