Operators double down on Permian, seek solutions to operational, downhole and reliability challenges
Companies push for production growth while addressing equipment failure-related NPT, water sourcing, well complexity and cost management
By Kelli Ainsworth, Associate Editor
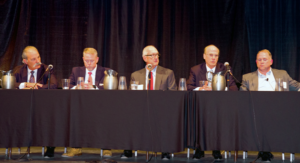
If the rising rig count has made US shale the brightest spot in the global exploration and production market, then the Permian Basin has been the supernova. Of the 916 rigs working in the US onshore market as of late September, 385 were in the Permian. No other US basin even comes close – the Cana-Woodford in Oklahoma sits in a distant second with only 62 rigs. In fact, the Permian has been a major driver of growth in US oil production since 2010, Joe Wright, Executive Vice President and COO for Concho Resources, said during a panel session at the IADC Shale Energy Workshop in Midland, Texas, on 13 September. He pointed out that US oil production grew by 4 million bbl/day from 2010 to 2017, and 40% of that growth came from the Permian. “You can see that it’s very much been a revolution,” he said.
This kind of growth has prompted many operators to zero in on the Permian, with some even divesting assets in other plays in order to redirect resources to this area. Occidental Oil and Gas, for example, has sold off assets in California, South Texas, Colorado and the Williston Basin over the past few years to double down on the Permian. “The Permian is a really important area to Occidental,” John Willis, Drilling and Completions Manager for Occidental, said. “We’re the largest producer here, and it’s been our only area in the US for the last several years.”
The growth in the Permian kicked off in earnest when operators started shifting toward horizontal drilling here in 2011, Mr Wright said. In that year, only 17% of the 380 rigs running in the Permian were drilling horizontal wells; the remaining rigs were drilling vertical wells. Today, he said, 90% of all rigs in the Permian are drilling horizontally, adding that horizontal drilling has generated a compounding annual growth rate of 14% per year in the past six years. “It’s really been a catalyst for production growth in the Permian.”
For Concho specifically, 10 years ago, all 2,400 of its Permian wells were vertical. Now, the company has 19,000 horizontal wells in the play. “We’ve ramped up our activity to where we’re 100% horizontal for the last two years,” he said.
Lateral lengths also continue to grow at an astounding rate in the Permian, with 2-mile laterals now commonplace across the basin. In some parts of the basin, 2.5- and even 3-mile laterals are regularly drilled, and Mr Wright said he expects such lengths to become more widespread in the coming years. Concho itself is now averaging 8,300 ft (1.57 miles) in its laterals, which represents a 55% increase since 2015.
The abundance of horizontal wells that Concho has drilled since 2011 has also allowed the company to collect more well data, providing the capability to analyze the impact of multiple variables on well performance and to create a robust, real-time feedback loop. Well data is also providing better understanding of reservoir characteristics, leading to better well designs and greater recovery across multiple targets. “Your knowledge grows with every well that you drill,” Mr Wright said. “We’ve used that knowledge to drive our gains in efficiency. It drives our capital allocation program. It defines our resource potential out there, as well.”
Complex challenges
The Permian’s rapid growth and development has not come without associated technical challenges. “The way we drill wells today is much closer to deepwater than to the old Permian vertical wells,” Mr Willis said. Occidental currently operates 11 rigs in the Permian.
First, almost every well in the Permian experiences either flows or losses. Although traditional well control principles discourage tripping while the well is flowing, “if we tried to get a well to stop flowing before we tripped out of the hole, we would never finish a well,” he said. “It’s really walking a tight rope on the control of fluids in the wellbore in the Permian. It’s much more complicated than just about anywhere we drill.” The operator is now working to formulate a wellbore strengthening mud with the proper particle size and distribution in the mud to prevent the loss of returns. It will also provide a saturated brine across the salt.
A second major challenge is vibrations, due to the hard rocks in the Permian. “Out here, if you get vibrations, it will tear up your downhole equipment,” Mr Willis said. “You’ll see a tremendous number of motor failures, downhole tool failures and bits damaged beyond repair.”
Occidental mitigates bit damage due to vibration by running a very high weight on bit (WOB), Mr Willis said. For instance, he said, the recommended WOB for a specific bit might be 55,000 lb-ft, but the operator might run it at 70,000 lb-ft. “We’ve had cases where we’ve pulled bits out after running with that kind of load, and they look brand new.”
Vertical integration
Water sourcing is another challenge in the Permian. Pioneer Natural Resources currently runs eight frac fleets in the Permian and sources more than 400,000 bbl/day of water. “We’re very proud of the fact that more than 50% of that is from non-fresh water sources,” said Joey Hall, Vice President of Permian Operations for Pioneer. To further reduce the use of fresh water, the company entered agreements with the cities of Odessa and Midland – in 2014 and 2016, respectively – to purchase effluent water for use in Pioneer’s Permian operations. Presently, the company receives 100,000 bbl/day from Odessa. The agreement with Midland takes effect in 2020, at which point the operator will start to receive 200,000 bbl/day of effluent water from that city.
Pioneer is also increasingly adopting a vertical integration model to help manage the overall well costs in the Permian. For instance, in 2012 the operator acquired a sand mine in Brady, Texas, that produces more than 100,000 tons of sand each month. Each day, 500 loads of sand from this mine are delivered to Pioneer’s well sites in the Permian.
The operator also owns Pioneer Pumping Services, which has approximately 450,000 horsepower of fracture stimulation equipment and provides fracture stimulation, coiled tubing and support services to Pioneer’s operations in West Texas and Colorado. Further, there is Pioneer Well Services, based on Midland, which operates a 12-bay maintenance shop. It includes heavy- and light-duty mechanics, shop supervisors, service writers, parts delivery drivers and shop and field welders.
Pioneer is currently operating 18 rigs in the Permian but believes that number could increase to 70 by 2026 as it pursues the “Million in Ten” initiative, which the operator announced in 2016. Under this initiative, Pioneer aims to quadruple its current overall production by 2026 to 1 million BOED. This will require Pioneer to grow its production by 15% each year until 2026, much of it supported by the Permian. Just this year, the operator expects its Permian production to grow by between 30% to 32%.
Automation could help operators grow their Permian production in an efficient and cost-effective manner, he noted. However, automation must be adopted in a strategic, purposeful manner. “Automation has to come, but we have to make a real differentiation between what is cool and what is something that’s really going to make a difference. Automation is expensive,” he said.
Need for reliability
For Diamondback Energy, a pure-Permian operator with 191,000 acres in the Midland Basin, the operator is placing its focus on downhole tool failures as it works to reduce flat time. In Q2 2017, the largest contributor to the company’s nonproductive time (NPT) was downhole equipment failure – including motors, MWD equipment and rotary steerable tools, according to Mike Hollis, President of Diamondback.
So far, the solution has simply been to operate BHAs or drill bits for longer than dictated by normal practice – if that particular BHA/bit is operating reliably. This avoids the risk of failure that comes with putting in a new BHA or bit, he said, because quality is so uncertain.
“It got to the point where we were afraid of what was sitting on the rack,” Mr Hollis said, urging equipment suppliers to reexamine their quality assurance processes. Diamondback is also engaging in more conversations with both suppliers and contractors to ensure that equipment is designed, built and used correctly. “We’re always trying to figure out how we can run them better, engineer them better and then have the reliability in the shop to bring something out that’s consistent.”
Personnel reliability is also going to be a focus in the Permian going forward, Mr Hollis said. When the onshore rig market was at its low point in this cycle, the crews that remained were the best of the best, from top to bottom. Now that onshore contractors have been reactivating rigs and hiring or rehiring employees, the talent pool is becoming diluted. “We’re going to have to manage that talent pool such that we can keep our execution level up and maintain high safety standards,” he added. “We want every person that goes out to these locations to come home safe.” DC
Click here to view a video with Luke Crownover, Chairman of the IADC Permian Basin Chapter.
Without a doubt, personnel responsibility and reliability is paramount when it comes to safety in energy companies throughout Texas and beyond.