Metal-seal dissolvable frac plugs use simplified design to improve reliability during plug and perf
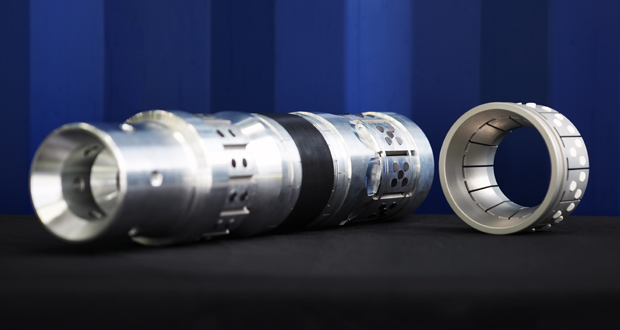
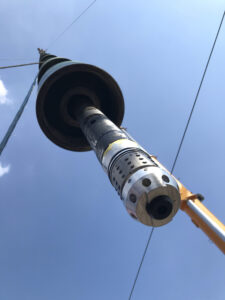
By Jinlu Wang, Vertechs Group
Compared with composite frac plugs, dissolvable frac plugs currently only have less than 20% of the market share of the plug-and-perf completion method. Frequently cited disadvantages include casing erosion and issues with dissolving too fast or too slow, leading to increased costs and longer completion times. However, newer and more simplified dissolvable frac plugs could help to address these challenges and have the potential to achieve efficiency and cost savings in major unconventional plays around the world.
One source of limitation with frac plugs is the elastomer. The oil and gas industry has used elastomers as a material for frac plugs – both in traditional composite frac plugs and dissolvable frac plugs – in zonal isolation for years. However, recent research and observations made through the use of downhole cameras indicate that elastomers can sometimes fail or extrude, leading to leakage and casing erosion. The chemical nature of elastomers tends to cause them to extrude under high pressure and temperature conditions.
Still, elastomers can provide reliable isolation when properly designed with anti-extrusion mechanisms. These can be made of overlapping plates or rings that are compressed and flattened into a disc-like shape, blocking the elastomer from slipping through the gap of slip segments. In complex downhole conditions, however, these anti-extrusion mechanisms can sometimes fail or not deploy fully, leaving weak points that allow for extrusion to occur.
To address the issues associated with elastomers, metal-seal dissolvable frac plugs have been developed. These plugs use a metal-to-metal seal to provide reliable isolation under high pressure and temperature conditions, eliminating the need for anti-extrusion mechanisms. As a result, the design of the plug is simplified, requiring fewer components and materials. This can also make clean-out runs faster and more efficient. In addition, metal seals can eliminate running risks in high annular velocities.
In challenging situations, hybrid seals can also be used; it combines both an elastomer ring and a metal-seal mechanism. The elastomer serves as the initial pressure barrier during stimulation, while the metal seal undergoes plastic deformation and fully engages with the casing wall as the pressure increases. This not only provides reliable isolation of the casing, but the metal seal also serves as a robust anti-extrusion component
Compared with these newer and more simplified plugs, traditional dissolvable frac plugs are typically made of complex components that can be prone to failure risks. These components may be sensitive to temperature, pressure and other factors, which can make it difficult to predict and control the rate at which the plug dissolves.
Another potential limitation of traditional dissolvable frac plugs is that they are often heavily customized to dissolve at specific rates, which can be difficult to predict and control. This can make it challenging to use these plugs in a wide range of wellbores and production scenarios, as the specific conditions and requirements of each well can vary significantly.
Using dissolvable technology can be both beneficial, but it does comes with its challenges. To customize plugs that are suitable for different conditions, a thorough understanding of both application challenges and engineering are necessary. The tool supplier must consider all operational details, including the conditions and requirements, to design, simulate, validate and optimize the plug in order to achieve optimal performance and results for end users. This requires a careful balance between tool performance and dissolvability. Striking a balance between the trade-offs in different applications and scenarios is crucial for success. DC