Drill pipes, BHAs evolve as wellbore geometries push existing boundaries
Industry steps up downhole performance by giving connections greater fatigue resistance and enhancing BHA steering capabilities
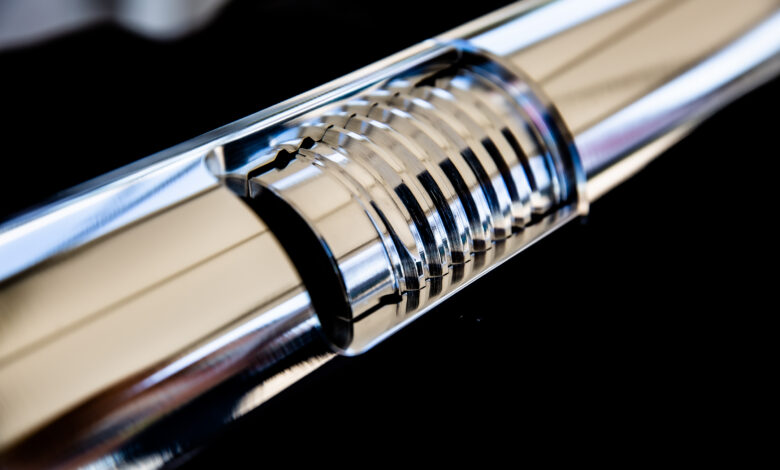
By Stephen Forrester, Contributor
Extended well lengths, deeper well depths and more complex wellbore geometry are leading to the need for higher-performance drill pipe and BHAs. Technology providers are focusing on improving durability and decreasing cost of ownership, through things like better fatigue resistance, the use of steel with a higher alloying content, and integration with drilling software.
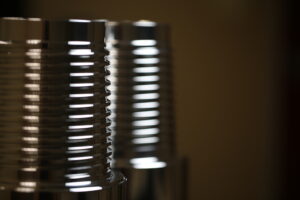
Connection technology for drill pipe, BHAs
In the drill pipe market, innovation cycles do not occur with nearly the same frequency as that of downhole technologies or rig equipment, explained Guillaume Plessis, Senior Director of Technical Support Services for NOV’s Grant Prideco business unit. So the company’s emphasis remains on its Delta drill pipe connection, which Mr Plessis said was designed to provide performance and lower total cost of ownership and has continually delivered on these two fronts over the past six years. Delta 544, for example, offers the option of using a larger 5 ½-in. pipe with a small tool joint outer diameter — comparable to that of 5-in. drill pipe — which allows drillers to drill an 8 ½-in. hole with a larger, stiffer pipe. This can lead to increased ROP.
The company has also worked on giving the connection greater fatigue resistance, which eliminates the need for cold-rolling of drill pipe connections, as well as the capability to use an extended makeup torque — an increase of 17%. Compared with NOV’s previous XT connection, Delta also has a 50% faster makeup speed, yielding up to 4 seconds saved per connection makeup and breakout.
NOV is also working on the development of two other connections. The first is a connection for bottomhole assemblies (BHAs), currently branded as AILM. “The objective is a bit different for this technology, as we want to optimize fatigue resistance,” Mr Plessis said. “The challenge with a BHA connection is that the tools are very stiff, and most bending occurs at the level of the connection, requiring innovative solutions to cope with fatigue.”
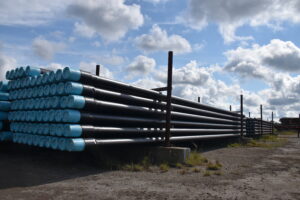
The second technology is a smaller connection being run on a limited basis in niche applications. “The Nano connection is being run on a different type of strings used for clean-out or workover operations, or in through-tubing drilling,” Mr Plessis noted. “These are very specialized operations, and we’re typically competing with premium tubing connections in this category. While ruggedness could be a benefit of implementing Nano, the cost is typically higher, and our customers do a very close evaluation of the advantages of the technology versus the cost of running it.” To address this, NOV is looking at alternative ways to use the Nano connection to, once again, make it more cost-effective and relevant to that type of operation.
Another area of interest for NOV is drill pipe risers. The company recently finalized the qualification of a 20,000-psi connector on a sour service-grade. “This project has been technically very challenging,” Mr Plessis explained. “However, we’re done with the development of this second completion and workover riser to API 17G standard, and the product is currently threaded on a partner company’s product for use in a high-pressure project in the Gulf of Mexico.”
This new connection diversifies NOV’s portfolio of metal-to-metal gas-tight connections, making it the broadest with seven designs.
In the Middle East, sour service-grades for drill pipe and heavyweight drill pipe are more prevalent, and NOV has commercialized a 135,000-psi, NACE Region 1 product that can be used in mild sour H2S environments. The product has been pre-qualified, and NOV said it plans to deliver the first string in 2023.
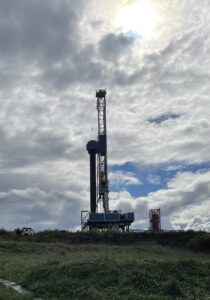
High-torque, high-performance connection
Innovation in the drill pipe market has been accelerating over the past five to 10 years, according to Mark Garrett, Senior Sales Engineer at TSC Drill Pipe, a division of Texas Steel Conversion. “I’ve seen a significant increase in slim-hole drilling, which is when you have a smaller annulus between the drilling tool and the wellbore,” he explained. “We’re also seeing much deeper wells, with wellbores averaging a minimum total depth (TD) of 20,000 ft, and some going to 30,000 ft. This is quite a change from where we were just a decade ago.”
Drilling contractors, in particular, have called for higher performance in the threaded connections that hold the string together so they can reach those deeper TDs. While there is still some limited use of single-shoulder API connections, Mr Garrett noted that most drilling programs now use double-shoulder design connections, with a growing percentage of those being proprietary thread technology from various providers.
“With double-shoulder connections, we can achieve the higher makeup torque necessary in these more challenging wells,” he said. “Additionally, the proprietary double-shoulder connections typically have a larger bore through the threaded connection, which improves hydraulic performance in the drilling program.”
On the heels of drilling projects that are incorporating increasingly advanced BHA technology, like automated rotary steerable systems (RSS) for precise directional control, Mr Garret remarked that proprietary connections have gained significant market share, becoming the new standard to enable newer systems to perform. “If you’re using an API rotary-shouldered connection for your drillstring threaded connection, it typically has a 2-in. taper-per-foot thread form, which results in a smaller diameter in the threaded connection when compared with the manufacturer’s proprietary connections,” he explained. “Most of these proprietary connections have a much slower, more gradual taper on the connection, which is how you achieve the larger inner diameter necessary to improve hydraulic performance.”
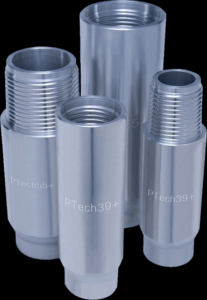
TSC Drill Pipe’s PTECH+ is the company’s most recent entrant into the high-performing connection market. The connection was designed to encapsulate the essential characteristics required for extended-lateral oil and gas drilling: maximized hydraulic performance, increased makeup torque and improved fatigue resistance.
“How do you achieve fatigue resistance on these high-performing connections?” Mr Garrett asked. “When designing PTECH+, testing and analysis proved that a large radius at the root of the thread form reduced peak stresses in the connection. This reduction in connection peak stress mitigates the potential for connection fatigue and failure when exposed to downhole bending.”
Mr Garret also noted that the materials used to manufacture the connection impact performance. “There’s been a step-change in the materials we use, such as steel with a higher alloying content to provide improved toughness with a higher hardness,” Mr Garrett explained. “Typically, in steel technology, the higher the hardness, the more brittle the steel may become. Using better alloying, coupled with precisely controlled heat treatment, we can effectively eliminate this problem. This practice increases the performance capabilities and assures the durability of the PTECH+ connection.”
Although the connection maintains a streamlined geometric design, torque capacities for the connection average 85% to 280% greater than API drill pipe connections of the same dimensions, according to the company. TSC Drill Pipe recognized that a drawback to most higher-torque connections is that they typically require more turns to make up to be shouldered, compared with API drill pipe connections. Accordingly, a critical design criterion was to reduce the number of necessary turns to make up without sacrificing performance. Depending on the connection size, the turns to make up range from 7.5 to 9.6.
Another trend with present-day drilling programs and deeper wellbores is the use of drillstring oscillating programs, which involve alternating clockwise and counterclockwise rotation of the drillstring while drilling. “One problem we are seeing resulting from these oscillating programs is that the connections may have a tendency to break out,” Mr Garrett said. “The PTECH+ connection is designed to provide for higher makeup torques on the threaded connections, and we have realized successes in overcoming that challenge.” As higher torque thresholds are required for drilling programs to achieve deeper wells and longer laterals, a growing number of land rigs are being retrofitted with upgraded components, raising the threshold capability of drillstring connection makeup torque.
The proprietary PTECH+ connection technology has the potential to be utilized in a variety of applications in addition to drill pipe, including subsea tubulars, workover risers and other downhole components. While it is currently used primarily in land drilling, it can also be used for offshore and other specialized drilling programs by incorporating a gas-tight seal feature.
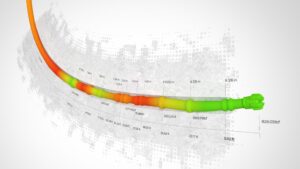
BHA and drilling engineering software
In the BHA segment of the market, Stéphane Menand, Technical Fellow at Helmerich and Payne (H&P), said that, while there have been few true breakthroughs in BHA components over the past few years, there has been a lot of ongoing work refining existing technologies to increase durability and enable more rotating hours downhole.
“We’ve pushed the limit with RSS and high-powered mud motors. We’ve also seen the development of several accessories that go in the BHA to remove friction, dampen vibration and reduce stick-slip. Lastly, we’ve seen more providers with high-frequency torsional oscillation mitigation technology that can be implemented directly inside the RSS.”
For technologies that have the potential to drive step-changes in the future, Mr Menand said he is “intrigued by at-bit steering technology, where there is a drill bit with active pads to allow better trajectory control and more accurate wellbore placement.” Another point of interest, he said, is putting very small sensors along the BHA and in the bit to get better data, which can help to validate H&P’s models.
Mr Menand also highlighted the benefits of drill bit forensics, which use pictures from a scanning device and analyzes them with artificial intelligence-driven algorithms to provide detailed 3D imaging for dull grading. “The idea is to better measure the wear of the bit, and then reduce the time necessary to design a new bit for a new application,” he said. “This eliminates the need to manually measure the type and amount of wear on individual cutters, which would otherwise take a significant amount of time and could be inaccurate. It’s a great process for the bit providers when it comes to iterative design improvements.”
As the industry moves toward true digitization, Mr Menand explained that a focus area of H&P has been integrating the many downhole products and technologies that the company deploys as part of a package that enables automated drilling. “What we’re trying to do at H&P is better control the BHA from the surface with a different level of automation,” he said. “Whether a new or existing BHA, we’re looking at how we can control it in terms of operating parameters, drilling performance and steering recommendations. With more complex wells and increasingly long laterals, we really have to look at combining technologies if we’re going to push the envelope, because otherwise there is a technical limitation, at least for now.”
In 2019, H&P acquired the DrillScan drilling engineering software, which has four primary modules – well planning, well integrity, BHA and bit analysis, and drill string modeling. They leverage modeling and simulations to reduce the time to target, enhance BHA integrity and increase reservoir contact. “We want to integrate software applications from DrillScan software on H&P rigs for automation,” Mr Menand said. “The software’s physics-based algorithms integrate with the AutoSlide technology, for example, working with the equipment at surface to steer the BHA. The idea is to try to predict the amount of friction and find an optimum weight-on-bit RPM given a well trajectory. We want to optimize all of H&P’s machines to drill with the best ROP, experience less vibration and yield a smoother wellbore, and we use DrillScan software to enable the equipment to accomplish those objectives.”
Once DrillScan software successfully integrates with the surface rig equipment and achieves these targets related to wellbore quality and drilling performance, H&P can then focus on another major goal: creating a digital twin to predict and model performance in real time. “We want to provide what I call a true digital twin, which means to have a live, real-time, virtual representation of the condition of the drill string and BHA,” Mr Menand explained. “Having this sort of eye downhole — that is, having a true digital twin of the entire drill string — allows us to better pilot that drill string in terms of ROP in terms of steering and in terms of vibration.” Once a stand is drilled, H&P can quickly analyze its performance to predict that of the next one.
Mr Menand said he believes that having DrillScan software as part of H&P has provided customers with benefits that would have been more difficult to achieve with multiple third-party providers. “We have the rig, we have the people on the rig, and we have the technology, meaning that we can master and control everything from A to Z because we’re all in the same company,” he explained. “When you bring in third-party technology providers, there’s potential for issues with integration or miscommunication, but having DrillScan software as part of H&P’s portfolio helps ensure that we understand what we need to do, and we have the data from H&P’s sensors to back up those decisions.” DC
DrillScan and AutoSlide are registered trademarks of H&P.