Industry looks to new materials, integrated and intelligent solutions for deeper multizone completions

By Joanne Liou, associate editor
When it comes to sand control, a misstep comes at a high price. The industry is increasingly realizing the significance of investing time and resources from the very beginning. “It’s very important that you get the optimal sand control for each completion right in the first place,” Asaf Nadeem, Chief Completions Engineer at BG Group, said. “When you go back in, it’s very expensive to intervene and fix a well in which sand control has failed. It is challenging from an intervention point of view, especially when it comes to tackling interventions in subsea wells with failed sand face completions.”
Companies are approaching the challenge holistically, beginning with understanding downhole conditions and looking beyond the equipment. “The overarching, most common and most difficult to recover from failure point in sand control is not fully understanding the total downhole system,” Randy Simonds, Director of Sand Control, Well Completion Technologies for Weatherford, said. “You have geomechanic considerations, the tendency of the reservoir to sand and all these things that build up on one another.”
To improve reservoir management, intelligent completions are enabling operators to monitor and control reservoirs remotely. In the deepwater arena, the industry is stepping up from two-zone intelligent sand control completions to three or more zones. “Moving this technology into the deep- and ultra-deepwater arena is the next frontier,” Ricki Jannise, Senior Product Champion for Halliburton’s Completion Tools Product Service Line, stated.
BG Group: Ceramic screens
While sand control challenges have increased along with operational complexity, sand control equipment and solutions have largely remained constant, Mr Nadeem said, pointing out that they still mostly rely on metallic components. “We keep trying to make metallic components stronger, or we try to change the geometry of the metallic components. We never looked at alternative materials, and that’s where the evolution hasn’t happened,” he explained. “The evolution has predominantly changed the actual geometry and strength of the material as opposed to actually changing the material itself.”
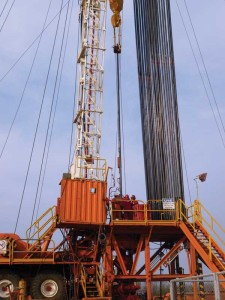
In Bolivia, where BG Group deals with potentially complex and highly depleted gas wells, the company was challenged with producing sand-prone wells to full capacity. In fact, the company found that 80% of its sand face completion equipment was failing because of erosion. The velocity of sand particles from the formation erodes metallic components, Mr Nadeem explained. In collaboration with ESK, a 3M subsidiary, BG Group began to look beyond metallic components in 2010 to develop a ceramic screen. The initial design of the ceramic technology was tailored to a Bolivian well, with the intention of spreading the technology to existing fields in Trinidad and possibly Egypt.
The first ceramic screen was installed onshore Bolivia in September 2012 and has since been producing sand-free. “The cost was a third of the equivalent of a cased-hole gravel pack, and we recouped the cost of the whole intervention that we did within several months,” Mr Nadeem noted.
The ceramic material has a pressure rating exceeding 5,000 psi and has been lab-tested to 300°C. “In terms of acid, the material has also been tested with aggressive acid treatments, which are commonly used in the industry and has withstood every test. The (ceramic) properties we found were much more superior than metallic-based components,” Mr Nadeem said.
BG Group is cautiously testing the technology because it doesn’t want to rush into it too quickly, Mr Nadeem said. “Each well has to be individually analyzed for the optimal solution, and this takes time.”
BG Group plans to install its second ceramic screen in a well offshore Trinidad in March. For the past five years, the well has struggled with production due to sub-optimal sand management in the completion. This installation will serve as a test for the ceramic screen in the offshore environment, with higher gas rates and an 800-ft producing section.
Testing prior to the Bolivian well involved both laboratory and simulations running in dogleg severities encountered in demanding well trajectories. The screen was run 36,000 ft through a purpose-built simulator at 80 ft/min with 5°/100 ft dogleg severity.

BP: Chemical components
BP is approaching sand control by integrating three types of solutions: mechanical, predictive or digital, and chemical. With more than 60% of its production coming from sand-prone reservoirs, the company aims to always be prepared for the worst scenario: “You always have to say to yourself that if there’s a spot that sand can come through, then it will come through,” said Hans Vaziri, BP Distinguished Advisor in Sand Management – Upstream Technology. Several of BP’s key operating areas – Angola, the deepwater Gulf of Mexico (GOM), Azerbaijan, Trinidad and the North Sea – are in soft formations. “We expect those wells to last a long time – 20 years. We expect them to produce at a relatively high rate, but each region has its own specific issues.”
On the mechanical side, open-hole gravel packs are most commonly used in BP’s completions in Trinidad, Angola and Azerbaijan. Given the commonality of open-hole gravel packs across different regions, BP is taking learnings and successes from one area and applying it to others. “We learn more, optimize and transfer the learnings from region to region. For example, lessons learned from Angola are being used in Azerbaijan and Trinidad and vice versa,” Mr Vaziri said. “It’s a continuous conveyor belt of improvement around the common issues.”
The key is to keep the solution simple. “The more complex you make your sand control, the greater the risk of something going wrong. You don’t want to overcomplicate what we’re working with. It’s about optimization,” Mr Vaziri stated. The predictive capabilities play a part in determining how complicated – or simple – the completion should be, followed by the chemical solutions that serve as a contingency. “If things don’t work out as planned, what do we do about it? From everything that we have learned, we are trying to find out what are the issues in the reservoir that could cause problems during the life of the well.”
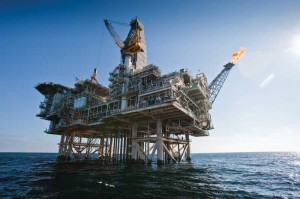
BP is assessing multiple chemicals for different conditions in a variety of regions. “We try to understand what the root cause of the sanding is for a given problem and which chemical would best fit the solution that we have in mind,” Mr Vaziri said. He added that BP is still in the learning phase with chemical solutions and has tried different chemicals with varying success. “We understand the underlying reasons that have made some of the chemical applications successful. Where there is room for optimization, we are learning and directing the technology to deal with the challenges.”
In reservoir stimulations, proppants that are pumped in can loosen up and flow back into the well, potentially leading to sand production. Offshore Egypt, BP has applied chemical consolidation in one well that was experiencing sanding issues. “The chemicals basically stopped the sand production, and the well has been producing sand-free for several months now. It has shown good longevity and good response to the chemical consolidation,” Mr Vaziri said.
In some reservoirs that need to be treated for sand production, BP is looking at adapting treatments for longer intervals. “The chemical needs to be diverted into the right regions, and if you have a reservoir that is 1,000-ft long, how do you assure that the chemical is going into the right place and stays there?” Mr Vaziri noted. Ensuring effective and reliable diversions in these longer intervals will be the next step, he added.
A missing link in sand control remains in areas where industry still lacks measurements, like water injection wells. “We have some data but not to the abundance that we would like,” Mr Vaziri explained. “In water injectors, we cannot actually tell how sanding takes place because the sand goes down into the well rather than up the well. Presently we just do not know how those events take place.” While the physics and mechanics of sand control are understood, “what we are looking for is the validation. Advanced sensors and communication of the data in real time from those sensors would help us to maintain and actually accelerate the technology in this area,” he added.

Baker Hughes: Single-platform crossover tool system
Some companies estimate as much as 25% year-on-year growth in the number of wells that require sand control, Suzanne Stewart, Product Line Director – Sand Control at Baker Hughes, said. “As that global market increases, the demand for competent individuals to be able to service that becomes a real challenge.”
Although there is no one-size-fits-all solution to sand control, one driver behind Baker Hughes’ SC-XP system is to standardize crossover tools to a point where training, maintenance and operating procedures are essentially for one platform of tools. “We’d be able to standardize the tools on location and still be able to perform different types of jobs,” from cased-hole fracturing applications to open-hole completions, Ms Stewart said. A focus area for this approach is deepwater, where the goal is to simplify sand control operations and minimize the risk of costly downtime.
The SC-XP system is a gravel- and frac-packing system suitable for temperatures up to 400°F, treating pressures of 15,000 psi and a proppant volume of 1.5 million lbm at 60 bbl/min while preserving casing. The system incorporates field-proven ZXP element technology from the company’s liner-hanger group. The ZXP packer element technology enables faster conveyance while maintaining the ability to retrieve.
“As we move into areas where operators want to pump in excess of 1 million lb of proppant, erosion of the tools and casing becomes a critical factor,” Ms Stewart said. Features, including newly designed gravel-pack ports, have been incorporated to help to minimize erosion in the tools while pumping such high-rate jobs.
The system allows horizontal, open-hole gravel packing without disturbing the filter cake. “The gravel pack version of the SC-XP maintains hydrostatic overbalance throughout the complete operation, maintaining integrity of the filter cake,” Ms Stewart explained. “If you don’t maintain that differential across that filter cake, the formation may start to collapse and/or the well may go on losses.”
Three field trials have been completed with the SC-XP on the Gulf of Mexico shelf, and the operators have been “extremely happy with the system. The simplicity of the operation and the extreme capabilities are really the exciting parts for them,” Ms Stewart noted. “The tools are much easier to operate with less risk of operator error.” Baker Hughes expects to commercially launch the system in the coming months.

Weatherford: Self-mitigating screen
Screen failure remains a risk to completion integrity and continuous production. As well costs continue to rise and as industry ventures to more complex environments, operators are seeking a combination of high functionality and reduced complexity. “The environment isn’t necessarily harsh as much as it is inhospitable,” Mr Simonds said, referring to deep, subsea wells. Even when the operator isn’t certain that sand control will be needed in those wells, more often than not they’re installing the equipment. “The cost of being wrong far exceeds the savings of trying to be value conscious, ” he added.
Weatherford, in partnership with ExxonMobil, developed the self-mitigating MazeFlo screen initially to address loss of sand control due to erosional failure of the screen. In a typical screen, there is a single layer of filter – a wire-wrapped screen or a mesh screen. “If something damaged that single layer, you would lose sand control,” Mr Simonds explained. “MazeFlo requires the flow to come in through the primary screen, and underneath it is an unperforated base.” The fluid then travels up the base pipe annulus and through a ring that distributes the flow evenly around the pipe. The fluid continues through a secondary screen, which is inside a housing, into the base pipe and up to surface.
The maze design constrains local sand ingress that can result from screen damage. The system has the same operating and installation parameters as conventional screens and does not have any moving parts. “Because it heals itself, you’re not taking the well offline,” Mr Simonds said.

The screen’s first run took place in a sanded 1,445-ft horizontal liner completion offshore Nigeria in September 2012. ExxonMobil cleaned out the sand and ran MazeFlo inside a 4 ½-in. slotted liner. “We worked with the available real estate to clean it out and basically put a screen inside of the slotted liner,” Mr Simonds said. “We installed 48 joints of 2 3/8-in. MazeFlo with three compartments per joint.” Weatherford said well production has been higher than initial production since it was brought online in December 2012, though it could not disclose production numbers.
This spring, Weatherford plans to conduct its second MazeFlo installation off the east coast of Canada. Due to limitations on the platform, the 5 ½-in. screen will be installed in a completion that would normally suggest performing a gravel pack. MazeFlo is not meant to be a replacement for gravel packing, but an alternative solution was needed in this case. “Because the secondary chamber can provide insurance through the self-healing function, the operator said, ‘OK, we’re going to see if it can deliver in lieu of a gravel pack in this particular instance.’”

Halliburton: Intelligent sand control offshore
Two-zone intelligent sand control completions have become commonplace in deepwater wells over the past decade, but efforts are shifting to completions designed for three or more zones. Multizone sandface completion designs coupled with the intelligent completion will enable operators to complete, remotely monitor and control more than two reservoirs in real-time conditions in a single deepwater wellbore, Mr Jannise explained.
A hydraulically controlled production sleeve for each zone, temperature and pressure gauges, and flow meters comprise the intelligent equipment, while the sand control completion equipment is sized to allow an ample internal dimension of at least 4.75 in. to allow installing 2 7/8-in. control valves for a segregated production flow path.
Halliburton’s fourth-generation Enhanced Single-Trip Multizone System is designed for high pump rate fracturing treatments, which has led to opportunities to complete more than two zones in deepwater wells. The multizone systems have mechanical sleeves within the screen assemblies for each zone, and the sleeves open as each zone is treated and then closes to provide zonal isolation and fluid loss protection, Mr Jannise said. “The mechanical sleeves are re-opened when desired to provide a production flow path for each zone.”
In the Asia Pacific, 10 recent intelligent multizone sand control installations used the fourth-generation systems with both dry and subsea production trees in water depths less than 500 ft. Between three and six zones were completed with a mixture of high-rate fracture and pack treatments and high-rate water pack treatments. “This completion design placed the hydraulic production sleeves within the zones themselves,” Mr Jannise noted. “Placement of the sleeves within the zones means that the sleeves must pass through, and into, the sand control completion system. This limits the size and flow area of the sleeves. However, there is a great increase in the number of accessible zones.”
To control more than two zones in deep- and ultra-deepwater intelligent completions, the hydraulic production sleeves will need to be placed within the zones as in the recent Asia Pacific completions, Mr Jannise said. “However, the conventional space-out methods are not feasible in deep- and ultra-deepwater completions. The water depth will require pulling thousands of feet of tubing to install the tubing hanger.”
Instead of using tubing for installation, service companies are looking to use a sealing telescoping joint to provide the space-out results. “The space-out adjustment would be made while running in the well without pulling any tubing back to surface,” he explained. “This means that the telescoping joint must accommodate a bypass of the hydraulic and electrical lines without causing damage to them.” Development of sealing telescoping joints with hydraulic and electrical feed-through capability is ongoing, according to Halliburton.
SC-XP is a trademark of Baker Hughes. MazeFlo is a trademark of ExxonMobil Upstream Research Company.
Click here for the latest advances in well completions at DC’s Completing the Well microsite.