IT, nanotechnology innovate Shell’s drilling process
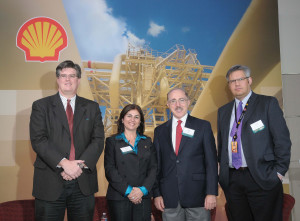
By Joanne Liou, associate editor
From nanotechnology to information technology (IT), Shell is bringing the fruits of collaboration and research to their drilling operations, on which the company spends approximately $7 billion to $8 billion per year, Jonathon Crane, VP wells technology deployment, said at the Shell Technology Center Houston during its recent Innovation Summit. “We have 150 rigs globally, and the trick is not to have one brilliant rig and the rest of the fleet be lousy, but to have every rig operating at their peak performance around the world.”
Other Shell leaders at the event echoed how collaboration, both internal and external, are delivering solutions. “It isn’t just around delivering technologies that are developed in this building. It’s about leveraging things that are available in the marketplace,” said Scott Meyers, general manager of IT innovation and center of expertise for Shell’s technical and competitive IT (TaCIT) group. “It’s also researchers, engineers and business people. We think of ourselves as a hybrid organization because we bring that combination of skills together.”
Information technology, for example, is playing an increasingly critical role in the energy industry by enabling more innovation opportunities. In 2009, Shell established TaCIT, a group of professionals from the downstream, automation and wells disciplines tasked with developing and delivering solutions based on IT. TaCIT uses three key principles to maximize opportunities: leverage more, deploy more and create more. For example, Mr Meyers explained, to leverage more, the company is using one of the industry’s leading software packages for capital project designs. “You do a 3D model of your facility so you can see it as you build it. Next, you make a 4D model so you can look at it in a time-lapse view,” he said.
“We’re taking it even further in 5D and 6D, which actually helps us plan the materials and the costs. That has made a significant difference in some of our more recent projects.”
Technology that is developed but sits idle does not have much value, which stresses the importance of deployment, Mr Meyers said. Shell’s SCADAdrill system, developed in 2009 for low-cost land wells, is an example of how the company has successfully deployed a new system in the US and around the world.
Creating differentiated solutions and technologies is another key to maximize opportunity. “For example, we have our own proprietary seismic processing software that has been developed over a period of time,” Mr Meyers explained. “It helps us to smooth the path of research into our business and so our researchers that are working on the latest geophysical technology can very quickly deploy those technologies into our business units that are processing seismic data and imaging to subsurface.”
High-performance computing, or supercomputing, helps bring the raw seismic data to geoscientist to use to understand the subsurface, to understand the size of the reservoir and the best ways to develop it. “The next generation of science needs a lot of computing and creates a real demand and importance for supercomputing. The energy industry in general is one of the largest users of supercomputing globally,” he added.
Nanotechnology also is having a more prominent impact on finding hydrocarbons safely and efficiently, particularly through the use of nano-enhanced particles. “To monitor how well our infrastructure is doing, we have a million channel sensors,” Sergio Kapusta, Shell’s chief scientist materials and corrosion, said. “One of the promises of nanotechnology is it can make those sensors smaller, faster and cheaper so we can deploy millions or more of those sensors all at once.” As a result, knowing how pipelines and wells are working increases their integrity while increasing safety of operations, he added.
Reiterating the importance of collaboration, Mr Kapusta explained how his company is working with academic institutions and other research companies. “Consistently we are working on mobility, nanomaterial from sensors, filtering and contrast agents, which increases our visibility of seismic and other exploration techniques,” he said.
Shell also continues its journey in automation. “The research was done years ago, but only recently has both the computing power and control-automation come together in a confluence,” Mr Crane said. Referring to an operation from October 2012, Mr Crane explained how Shell needed to quickly move a rig. The team had a choice between either using the automated SCADAdrill system to finish the well or relying on the 30-year experience of a human directional driller. The team decided to use the automated system for the final section of the well because it could drill faster. “It was a real milestone in the drilling business. Here’s something that we thought was an art that we turned into a science,” Mr Crane stated.
Frank Sesno, chief executive of Face the Facts USA, moderated the panel, which also featured Selda Gunsel, Shell VP global commercial technology.