20k technology enables first production from Chevron’s Anchor project
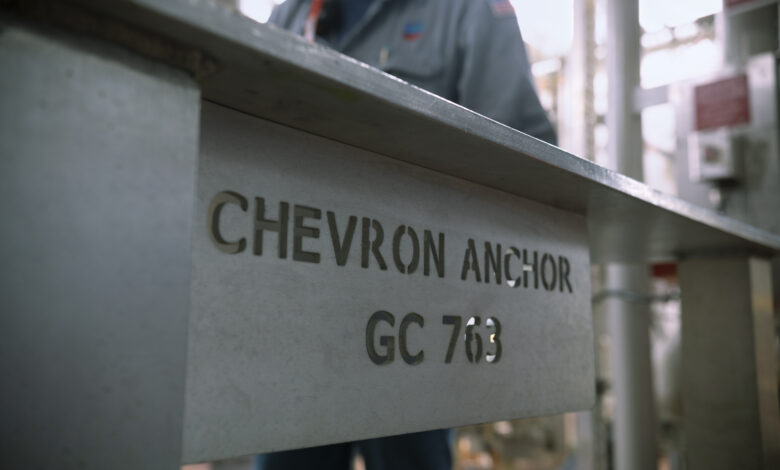
Chevron announced it started oil and natural gas production from the Anchor project in the US Gulf of Mexico. Anchor production marks the delivery of high-pressure technology that is rated to safely operate at up to 20,000 psi, with reservoir depths reaching 34,000 ft below sea level.
“Application of this deepwater technology allows us to unlock previously difficult-to-access resources and will enable similar deepwater high-pressure developments for the industry,” said Nigel Hearne, Executive Vice President, Chevron Oil, Products & Gas.
The Anchor semisubmersible floating production unit (FPU) has a design capacity of 75,000 gross barrels of oil per day (bopd) and 28 million gross cu ft of natural gas per day. The Anchor development will consist of seven subsea wells tied into the Anchor FPU, located in the Green Canyon area, approximately 140 miles off the coast of Louisiana, in water depths of approximately 5,000 ft. Total potentially recoverable resources from the Anchor field are estimated to be up to 440 million bopd.
The Anchor FPU is Chevron’s sixth operated facility currently producing in the US Gulf of Mexico, one of the lowest carbon intensity oil and gas basins in the world. The company is the operator and holds a 62.86% working interest in the Anchor project. Co-owner TotalEnergies holds a 37.14% working interest.