Going the distance: Drillers push innovations to drill extended laterals
Extreme depths necessitate solutions to handle high torques and lateral vibrations, ensure accurate horizontal wellbore placement
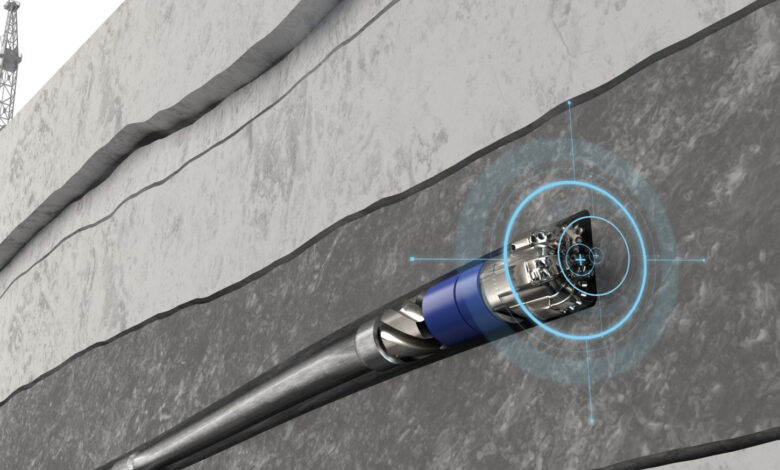
By Stephen Whitfield, Associate Editor
Extended-reach drilling has become not only more common in recent years but also more extended than ever. Operators are drilling longer and longer laterals in order to access previously untapped hydrocarbons, often from existing offshore platforms or from one single pad location. The value propositions are clear: Fewer number of wells have to be drilled to achieve the same production goals, and there is lower cost per foot.
“We’re seeing dramatic increases in lateral levels in many of the areas we’re working,” said David Millwee, VP – Drilling Performance at Patterson-UTI. “The 7,500-ft laterals are kind of going away, and we’re seeing more of a 10,000-ft standard, with some companies pushing 12,000 or 15,000 ft. For the operator, that additional 2,000 or 3,000 ft of lateral wellbore gives them better paybacks than trying to drill another well.”
On the flip side, extended-reach wells are notoriously challenging and require specialized planning to execute. It can be difficult to hit target zones. Lost circulation and wellbore instability risk is higher. Downhole tool reliability is also challenged. “As we’re drilling deeper laterals, we’re seeing that the current tools we have are hitting their technical limit,” said Chris Jones, Field Service Manager at Helmerich & Payne (H&P).
Addressing these challenges will require companies to consider both operators’ short-term production demands and long-term needs to reliably handle downhole stresses. In this article, DC speaks with Patterson-UTI and H&P about recent efforts to enable better drilling of extended-reach wells.
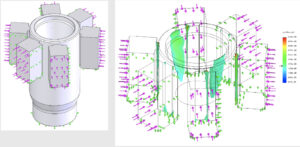
Handling excessive torque downhole
In recent years, H&P has made significant upgrades to its rig equipment to help handle the challenges associated with longer laterals in extended-reach wells. These include an engine package to increase the rig’s power output, upgrading top drives from 800 hp to 1,200 hp, as well as mud pumps with higher pressure capacity to handle the increase in fluid pressures and flow rates.
More recently, the company has also been focused on new ways to address challenges around the surface torque limit on drill pipe and couplings. Longer lateral wells typically require drill pipe connections to be exposed to extreme torques that may render them ineffective in getting the drill string to location; sealability can also be compromised.
The two points of contact that a standard torque wrench has with the drill pipe can create a slight bowing effect on the drill pipe, and the wrench can sometimes relax its grip on the pipe as it moves downhole. These two variables increase the likelihood of inaccurate readings of the torque value on each connection, which can lead the driller to apply an excessive amount of torque. “If you over-torque downhole, you’re having to rig up manual tongs to break your connections, which slows the whole well cycle down. Additionally, you’re damaging pipe and making it unusable. That’s added costs and added time we need to avoid,” Mr Jones said.
To combat this challenge, H&P worked with a third-party equipment manufacturer to develop the HexGrip 120 automated floor wrench, which can handle higher torques than a conventional torque wrench. Rather than using two dies to make contact with the drill pipe like a conventional wrench, the new wrench contains six dies, creating a concentric gripping effect where the dies grip around the circumference of the drill pipe. The improved gripping of the six-point torque wrench also translates to less connection deformation on the tool makeup and improved torque accuracy.
The new wrench also contains sensors so it can provide an exact reading of the back-off torque inputs, or the torque needed to break a given drill pipe connection. This gives the driller a more accurate view of how much torque is being applied to the drill pipe at any given time.
“With the type of downhole environments we see, there will be sections where you’re adding torque, so you need to know exactly how much is going to break out,” Mr Jones said. “If you’re not correct, you’re going to see a lot of problems when you have to go downhole and break the connections loose. Having that functionality to adjust and make sure our torque loads are exactly what we want them to be and what we need for the hole conditions – that helps to avoid a lot of the problems we face.”
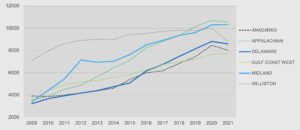
H&P has been field-testing the floor wrench on a Permian rig since early 2022, and a second wrench was added to a rig in Oklahoma this year. The company foresees adding more of these tools across its rig fleet this year.
The extreme torques seen in extended laterals can also increase the possibility of encountering damaging lateral vibrations, resulting in stick-slip, whirl and overall downhole tool failure. This can lead to longer drilling times, higher costs and even increased emissions and safety risk from the need to retrieve stuck pipe. H&P introduced its Failure Prevention Package in mid-2022, comprised of three solutions to better tackle this issue: FlexB2D 2.0, FlexTorque and StallAssist technology.
The main components of the Failure Prevention Package work together to counteract problems commonly seen in long laterals. The FlexB2D 2.0 software automatically and consistently stages drilling set points after tagging bottom; FlexTorque mitigates stick-slip and bit whirl; and the StallAssist technology detects, mitigates and recovers from downhole stalls.
According to H&P, over the past six months, rigs in the Delaware Basin of West Texas running the Failure Prevention Package experienced 37.1% fewer unplanned vertical trips and 37.3% fewer unplanned lateral trips per rig per month. Those rigs also saw 9.6% more vertical footage drilled and 17.7% more lateral footage drilled between unplanned trips.
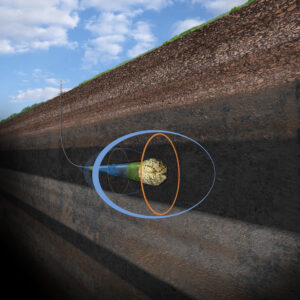
Improving bit guidance
At Patterson-UTI, a guiding principle while drilling extended laterals is the value of keeping downhole tools in the hole as long as possible, as it helps to minimize the number of runs needed. “The longer you push your footage, the longer you’re going to be in the hole. You’re going to have an exposed wellbore before you can get the casing set. The better we can get with managing our downhole tools, the better we have assurance of getting casing to bottom in one run,” Mr Millwee said. “We want to try to get as many one-run laterals as we can, so that we can have less of that exposed wellbore before we have to change the BHA for the customer. Being able to stay longer in the hole mitigates everyone’s risk.”
Recognizing that downhole tools have to stay in the hole for longer and longer distances, Patterson-UTI has been focusing on improving the accuracy of horizontal wellbore placement in the wells it drills. In extended laterals, the risk of missing the target zone increases as the BHA moves further downhole; the risk is even higher if the target is thin and the subsurface varies greatly within a short distance. If drillers have to course-correct with the BHA, well productivity may be reduced. “When you go from 10,000 to 15,000 feet, that window of uncertainty may stretch a multitude of feet. When we’re being told to hold the pay zones in narrow windows at extended depths, the uncertainties can be more concerning and impactful,” Mr Millwee said.
Over the past five years, Patterson-UTI and two of its subsidiaries – Superior QC and MS Directional – have worked to develop HiFi Guidance, a software program that utilizes proprietary AI algorithms to refine the calculation of rotational tendencies and motor yields in real time, allowing for forward projections and optimized slide scheduling through each well section. When combining this cloud-based software with rotary steerable systems, it can enhance and reduce change sequencing, thus reducing overall downlinking times.
The forward projections provided by the software enable the system to maximize footage placed within the window, Mr Millwee said. “When you’re drilling these long laterals, you need to be as efficient as possible. If I go off in the opposite direction from the plan, I could be leaving hydrocarbons in the wellbore,” he said. “When you can accurately place and reduce the risk of uncertainty with the well, we get better at drilling the well.”
The technology development was enabled by Patterson-UTI’s 2018 acquisition of Superior QC, a provider of software focused on wellbore placement and data analytics.
Upon its launch in 2022, HiFi helped Patterson-UTI see a 27.8% increase in the amount of lateral footage placed in the drilling window compared with its average in the previous year. After the system was rolled out to the company’s APEX rigs, it saw an 8% increase in average daily footage drilled from 2021 to 2022, and an average well depth increase of 500 ft in the same time span.
In one Eagle Ford project, Patterson-UTI deployed the software system in an area where high ROP was common, so there was an increased need for precise lateral targeting and deliberate steering decisions. The company determined that reducing the sliding percentage and the overall number of slides could yield a reduction in drilling time, resulting in a smoother wellbore.
A pre-job analysis of directional drilling in offset wells revealed an average of four slides per 1,000 ft, with a 35% variance between the day and night directional driller. For this project, the operator had the directional drillers follow their standard operating procedure for four offset wells on the pad, and a fifth well would utilize the HiFi Guidance system to make all steering decisions in the lateral. Results showed the four offset wells had an 8.6% average slide percentage, compared with just 3.3% for the fifth well – this marked a 62% reduction in sliding percentage in the lateral.
Additionally, the number of slides was reduced by 46% when comparing the directional drillers versus the HiFi Guidance system in the lateral. Drilling time was reduced by 17 hours, resulting in a direct savings of $35,000. DC