Driving change: Organizations share challenges, lessons learned while embracing innovation
People, culture and workforce competency must be recognized as key fundamentals to any modernization, digitalization initiatives
By Jessica Whiteside, Contributor
In the oil and gas sector, transformation is a word that can sound exciting and daunting at the same time: exciting because it promises a better future; daunting because of the layers of planning, pilots and approvals it would likely take to achieve. At the 2025 IADC Drilling Caspian Conference in Baku, Azerbaijan, on 6 February, panelists shared insights into three recent transformation initiatives at their organizations.
A common theme was that transformation requires a lot of work, but it can come with big rewards.
“Implementing change is not easy, because at the same time, you have to deliver the production, drill the wells, and you have to change your system to the modern way,” said Mahmoud Al Mamari, Training and Competency Development Manager for Abraj Energy Services.
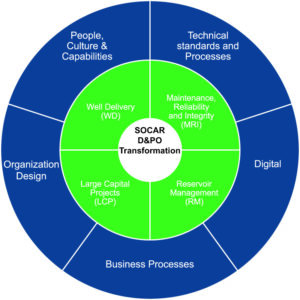
Case #1: Modernizing competency management to secure the fundamentals
Mr Al Mamari described his company’s work over the past few years to develop and implement a new competency management system called Kafa’a, aimed at accelerating employee development. Launched in partnership with the International Human Resources Development Corp (IHRDC), Kafa’a is a cloud-based system that supports a multi-language interface and provides a structured framework for assessing employee competence and addressing gaps in their knowledge, skills and abilities.
The system targets both technical and non-technical competencies, assessing not only functional competencies but also core, leadership and behavioral competencies. Each position at Abraj is represented in the system by a tailored competence profile that includes knowledge assessments, competence maps, linked courses and other learning resources relevant to the position.
An employee’s competence undergoes three levels of assessment. First, the employee logs into the system for a self-assessment. Next is a supervisor assessment. Finally, the employee’s competence is evaluated by an assessor in the field. Employees can also request a re-assessment if they disagree with a particular finding.
If the assessments reveal gaps in required competencies, the employee can access learning resources via the system. Each employee receives an individual development plan, so they know not only which competencies they need for their current role but also which competencies they need in order to move to the next stages in their careers. The system is also linked to Abraj’s succession planning processes.
Mr Al Mamari described Kafa’a as a “powerful assessment tool” that generates reports and analyses and provides a comprehensive understanding of competency management in the organization. It’s having a huge impact on employees and in enhancing trust and transparency within departments, he said.
“It produces the best outcomes of the employees so they can be a better version of themselves. It is really worth it to have a competency management system at our workplace.”
To prepare for the Kafa’a launch, Abraj worked with IHRDC and consulted with internal departments to develop departmental and position competency maps, capability assessments and learning resources (both e-learning and on-the-job). The training team also conducted stakeholder engagement and awareness sessions with employees, supervisors, assessors, department heads and management.
Mr Al Mamari said competency management is a never-ending process, however. “You always have to catch up with the global requirements and needs, and it’s a very fast-changing environment,” he said.
Case #2: Designing a high-performing rig culture
Houston-based The REACH Group helps companies in the upstream oil and gas sector transform their performance cultures through a “culture by design” approach.
“Rig site culture will occur by design or default – so why take the chance?” said Chris French, Business Development Executive for REACH. “What you say and what you do as a leader has a huge impact on how that culture develops in your organization.”
REACH’s culture design process is made up of six steps, typically phased in over eight to 10 months. Step one is to set the foundation for the desired culture through leadership alignment workshops. In the context of an offshore rig, this would mean bringing together offshore supervisors and onshore management directly involved in the operation to agree on expected behaviors for the crew and supervisors. They also need to set clear expectations that align with corporate goals and objectives. These expectations should reflect the unique aspects of the particular rig.
“Each rig has its own personality, and that comes from the crew onboard that rig,” Mr French said.
Step two is to build the team by removing silos and working toward a “one team” approach. This stage includes introducing concepts such as psychological safety to encourage a “speak up” attitude on the rig. It also involves recognizing behaviors by the crew that support the new cultural framework.
Step three is to “walk the talk” of the new culture, with leaders demonstrating the company’s values.
“Leaders must continually reinforce the agreed framework that’s been set, and, over time, people will see that this is recognized and rewarded – and what is not acceptable – and conformity and a positive attitude will form quickly,” Mr French said.
Step four is to communicate and be transparent. This includes activities designed to cultivate a learning culture, such as helping leaders build effective meeting and questioning techniques and avoid ineffective “name and blame” styles of management.
Step five is to help personnel stay on track with their adherence to the new culture, including identifying future leaders and cultural ambassadors who can continue to model and promote the new culture after the initial coaching and engagement stage. A cloud-based cultural assessment tool, with assessments filled out during every crew change, can help organizations quantify the progress of their cultural journey and document qualitative feedback from personnel.
Step six is to indoctrinate everyone in the tenets of the new culture.
“Whether that person’s coming out for a one-day visit to the rig, or whether they’re on a regular crew change, they have to abide by the framework, because that is what that rig will stand for and what’s expected of you,” Mr French said. He advised that rigs hiring new personnel consider not only the candidates’ technical competence but how they fit in with the new culture.
For one REACH client, an operator preparing for a drilling campaign offshore West Africa, the “culture by design” approach was the blueprint it needed to confidently undertake a project with a lot of unfamiliar elements – including a drillship it had never used before, run by a crew with a large proportion of new personnel, in a country new to the client. Another challenge was the diversity of people involved in the campaign, which represented more than 30 nationalities and included individuals from their early 20s to late 60s.
“That cultural mix was a great opportunity to find new ways of working,” Mr French said.
The process for this project focused on providing offshore supervisors with the skills, knowledge and attitude they needed to reduce risk and lead their teams to safely deliver the campaign objectives. REACH held brainstorming sessions to determine what the ideal culture would look like, what behaviors would be needed to achieve it, and what leadership skills supervisors should have to manage this transformation. They facilitated supervisor development sessions with leaders, from the deck supervisor up to the offshore installation manager, to identify their strengths, weaknesses and growth potential. They also conducted cultural surveys on topics such as breaking down silos, building team trust and psychological safety. Supervisors were able to measure their progress in the cultural journey against specific milestones.
As a result of the investment in cultural transformation, “the rig was looked at as world class and matured beyond its years,” Mr French said. The operation ended up being ahead of the planned cost and timeline curve, with no recordables.
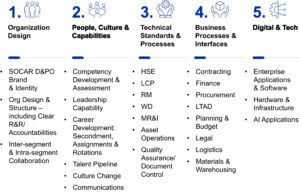
Case #3: Transforming an entire segment
When the State Oil Company of the Republic of Azerbaijan (SOCAR) announced in January 2025 that it had acquired a 10% stake in the Tamar gas field in the Mediterranean Sea offshore Israel, it said the company would be continuing “its efforts to acquire stakes in strategic assets in foreign countries in the future.” This interest in expanding its international upstream portfolio is one of the reasons SOCAR has launched a large-scale modernization of its development and production operations segment that aims to transform activities in four key areas: large capital projects; reservoir management; well delivery; and maintenance, reliability and integrity.
To enable transformation within these areas, SOCAR is introducing changes related to organization design; people, culture and capabilities (including development of a competency matrix); technical standards and processes; business processes and interfaces; and digital and technology. The company has linked key performance indicators to each of these “enablers” to keep the many components of the transformation on track and focus on the project’s mission of driving excellence in domestic and international operations. As a national oil and gas company, SOCAR is working closely with the government on transformation aspects such as the updating of standards.
“To move to the international level, we need to make sure that we’re ready – we’re ready from the people side, we’re ready from the procedure side, we’re ready from the equipment and the processes that we’re operating,” Orkhan Huseynov, Advisor to the CEO, SOCAR Upstream Operations Management, said at the Drilling Caspian Conference. “That’s why we started this long journey.”
The upstream segment is pursuing almost 20 digitalization initiatives as part of the transformation. Among these is a project to combine SOCAR’s vessel request and vessel tracking systems so asset managers can see in real time which boats are covering their area when they want to make an order, leading to faster decision making.
Another major ongoing digitalization effort under the project is to introduce a single online platform for all business units where lessons learned, after-action reports, procedures, and other essential information can be stored. A key goal for this initiative is to ensure that when one business unit captures a valuable lesson learned, this information can be communicated quickly throughout the segment – ideally in days or even hours, Mr Huseynov said.
Some digital initiatives may be in place by the end of Q1 2025, but the broader transformation project is an ongoing endeavor that is being phased in over time, with the large capital projects team among the first to transform.
“We’re starting to transform them because they are the first layer of people who are coming with the ideas and planning and then sending it to the next level,” Mr Huseynov said. “We want to make sure that we plan correctly from the beginning so we’re not facing challenges later on.”
An early consideration for those steering the transformation was how to engage the approximately 13,000 people who would be affected across the segment. One approach was to hold boot camps for select employees from every asset, who can then act as change agents to help deliver transformation messages correctly.
Many employees affected by the transformation have decades of experience doing things in a specific way. Would the transformation be welcome, or would it be seen as a shocking shift out of their comfort zone? To honor the company’s history and past successes while moving forward with modernization, the project adopted the slogan “To a perfect future with valuable heritage.” These words have deep meaning, Mr Huseynov said, conveying that the project is not changing everything from the root but rather building on good practices and ideas created in the field over the years.
“We are just trying to improve them, to add the recent modern techniques and practices that are operated right now globally.” DC