Dissolvable technology enhances operational efficiency of offshore completion operations on the NCS
Use of interventionless packer-setting solution saves 6 days of rig time, $500,000 in equipment costs offshore Norway
By Vijay Kumar Keerthivasan and Tom Rune Koløy, National Oilwell Varco
Various methods have been used to enable setting of a hydraulic production packer in an upper completion string, with typical systems involving temporarily setting an isolation plug below the production packer before pressuring up the tubing to set the packer and test the tubing string.
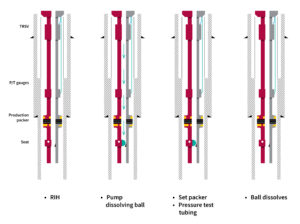
As it is often necessary to circulate as the completion is run to displace fluids or handle unexpected well control issues, traditional methods required intervention operations either during or after the completion has been run. This was necessary to remove both the temporary plugs and the devices protecting the completion tools from abrasive intervention operations.
The challenges associated with this are more pronounced in deeper, more deviated wells. Due to their complexity, they have production packers set out of reach of traditional slickline interventions. In such wells, wireline tractors are necessary to conduct intervention operations, which can incur several days of rig time, require costly specialized equipment and necessitate additional personnel. This can cost hundreds of thousands of dollars.
Due to current economic conditions, it was clear that a more effective solution was necessary. An operator in the North Sea working on the Norwegian Continental Shelf (NCS) sought a way to more simply and efficiently set the production packer versus running pre-installed plugs with check valves. To address this operator’s challenge and to provide the industry with a better path forward, National Oilwell Varco (NOV) developed and implemented a new system using dissolvable technology that allowed for interventionless packer setting and tubing testing of upper completions.
Technology
The new solution is a packer-setting kit that includes a seat profile and a dissolvable ball. The set is run as part of the tubing string below the production packer. After the completion string is landed, the dissolvable ball is dropped from surface to the seat profile below the packer. The system holds pressure from above, which enables the production packer to be set and leak testing of the tubing to be performed. The ball eventually dissolves completely through exposure to downhole packer fluids, which enables production activities to begin.
The primary use of dissolvable balls has typically been for frac-sleeve actuation and zonal isolation during well stimulation operations. As earlier iterations of composite/metallic frac balls experienced challenges with post-stimulation removal, the industry continued to seek alternatives in dissolvable technologies. Numerous studies proved that dissolvable metals outperformed their plastic counterparts in both tensile strength and impact toughness, leading to more innovation in this area.
The new solution is the natural evolution of such dissolvable technology applications, although developing it presented its own set of difficulties. An extensive qualification test program designed to demonstrate that the dissolvable technology was suitable for this application and operational constraints was undertaken for the North Sea operator prior to field implementation.
Qualification
Several factors had to be considered to select the appropriate dissolvable ball for the packer-setting and tubing-testing application, and the operator required a comprehensive qualification program due to the novel nature of the solution. The ball needed to be strong enough to withstand the pressures experienced during packer setting and tubing testing before gradually dissolving in the well fluid after required operations were completed. The ball had to dissolve in such a manner that well production could begin without any obstruction in the wellbore.
The operator had very specific inputs related to the well types and geology of the NCS that were designed to facilitate development of an optimal solution and initiate an effective selection process for the dissolvable ball.
First was downhole temperature, meaning the temperature of the well at the ball-seat system, which was set at 70°C. Packer fluid with a specific chloride concentration was chosen for the downhole fluid. Operationally, the seat size was established as 3.51 in., and the minimum ID in the string was 3.725 in. These considerations were driven by the allowable restrictions and flow areas in the overall completion design for each well.
Low-pressure testing of the tubing was set at 1,000 psi differential, packer-setting pressure was set slightly below 5,000 psi, and high-pressure tubing tests were set at 5,000 psi differential. This requirement directly determined the initial ball diameter necessary to hold a particular pressure. For time period requirements, the ball-seat system had to be able to hold 1,000 psi for 30 minutes followed by 5,000 psi for at least 7 hours. In addition, the ball had to pass through the seat within 24 hours and had to dissolve completely within five to 10 days.
The qualification program was designed to narrow down the dissolvable materials under consideration until an optimal material that aligned with the operator’s design criteria could be identified. The program was divided into four stages:
1. Cylindrical dissolution testing
2. Dissolve simulation
3. Full-scale ball-on-seat pressure testing
4. Full-scale ball-on-seat pressure and dissolution testing
In the first stage, dissolvable cylindrical samples were exposed to the packer fluid in a controlled laboratory setting. While temperature was maintained at the determined downhole temperature of 70°C, the samples dissolved, and their weight, diameter, and length were measured at regular intervals. These tests were carried out on a wide range of dissolvable materials, and steady-state values for rate of dissolution were obtained at the specified parameters.
In the second stage, NOV used a simulator combining empirical and analytical models to identify a suitable dissolvable material candidate for the application. After selecting inputs and placing them into the simulated workflow, a short-listed dissolvable material type that could be used on the NCS was selected as a candidate for full-scale pressure tests.
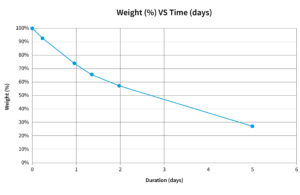
In the third stage, a dissolvable ball made of the material identified was put through a destructive pressure test, conducted at ambient temperature with inhibited fresh water as the fluid medium, to determine its maximum differential pressure rating on a given seat size.
After testing the ball through gradually increasing pressures, the ball pumped through the seat cleanly at 8,600 psi, proving that the ball and seat combination would be able to handle the 5,000-psi differential pressure necessary in this application.
In the fourth and final stage, the differential pressure rating and dissolution behavior of the ball-seat system were tested in the actual well fluid at the correct downhole temperature. This test was designed to closely simulate the conditions and operation of the system in the field.
Once the test assembly reached the correct temperature, 1,000 psi was applied above the ball for 30 minutes, and the pressure was increased to 5,000 psi. This pressure differential was maintained continuously for 18 hours before the ball pumped through seat.
The ball was retrieved, and the test was continued in the laboratory in the same fluid and at the same temperature. After 5 days, the ball had lost 73% of its weight, with a diameter reduction of 1.425 in., from 3.625 to 2.2 in.. Based on the predicted rate of dissolution, the ball would have fully dissolved within eight to 10 days as desired by the operator.
The test was repeated several times, with NOV and the operator ultimately agreeing that this dissolvable ball met the required design criteria and operational conditions.
Field Implementation
After the qualification and validation testing had been approved by the technical group of the operator, the interventionless packer-setting technology was ready for field implementation. The operator’s existing method required the following intervention operations prior to putting the well on production:
• Wireline run to pull a shallow set plug;
• Wireline run to pull the downhole safety valve hold-open sleeve; and
• Tractor run to pull the dual flapper valve in the tailpipe below the production packer.
The packer-setting kit became an integral part of the operator’s intervention-free completions concept and was used on three consecutive wells across a three-month period in mid-2018.
Once the completion string was landed, the dissolvable ball was dropped from surface and landed in the nipple profile below the production packer to provide a temporary plug in the tailpipe. Doing so permitted both setting of the hydraulic production packer and leak testing of the tubing. The tubing test pressure was locked between the dissolving ball and the downhole safety valve, the valve was tested to qualify it as the shallow barrier. Following leak testing, a steel ball was dropped into the well to land on a pre-installed lock in a nipple below the tubing hanger to protect the downhole safety valve against dropped objects during nippling operations.
When all barriers were properly in place, the BOP was removed, and the Christmas tree was installed on the well. The protection lock was retrieved by the BOP crane once the Christmas Tree had been installed. The deep-set barrier plug, a cycle open glass plug, was cycled open after hook-up to production. The dissolving ball and landing nipple performed well on all three wells. Even in highly deviated wells, the balls were landed at low rates of 1 to 2 bpm. After landing the balls, all required pressure tests were conducted according to plan. The testing sequence was as follows:
• Land the ball at a rate of 1 to 2 bpm
• Conduct a low-pressure test to 1,000 psi for 30 minutes
• Increase pressure to the hydraulic packer “start-to-set” pressure and hold for 5 minutes
• Increase tubing pressure up to the test pressure of 5,000 psi and hold it for more than 30 minutes
• Lock the pressure in between the dissolving ball and the downhole safety valve and bleed off pressure below to inflow test the downhole safety valve as the shallow barrier.
As the system functioned as designed and eliminated the need for intervention operations, it was considered a success by the operator. In addition to enabling interventionless completions and well-startup operations, the solution also eliminated the rental cost of dual flapper valves, hold-open sleeves and bridge plugs, as well as the cost of post-completion intervention activities.
The interventionless packer-setting solution also reduced planning time for post-completion activities and allowed the completion to be run open ended, which enabled bidirectional circulation.
Finally, the solution reduced the operational footprint at surface and enabled earlier production startup. The operator estimated a total cost savings of approximately $500,000 through equipment, and six days of rig time versus well operations typically involved with conventionally set production packers. An associated benefit was improved HSE by eliminating risks and required operations. DC