Low-ECD fluid facilitates deepwater, high-angle GOM well
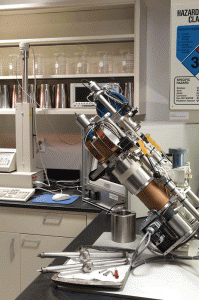
Fluid designed to increase barite sag resistance even with reduced viscosity
By Bill Shumway and Mike Breland, Halliburton
Modern wellbore design continues to become more complex. Many wells designed today, especially deepwater wells, contain significant challenges to effective wellbore pressure management. These challenges manifest themselves as a narrow window between the pore pressure and fracture gradient. Applications exhibiting such a narrow margin require improved management of equivalent circulating density (ECD) for operational and economic feasibility.
Primary drilling challenges associated with these types of wells include depleted zones, suspension of solids at high angles, naturally occurring weak rock strength and slim hole. In many such wells, target reservoirs lie beneath the original field, which has long been exploited. As a result, the depleted reservoir must be penetrated to reach assets previously undetected.
Depleted zones are typically an ECD challenge but often also create a lost-circulation hazard because of the regression of pore pressure and fracture gradient compared with the surrounding strata. In addition, depleted zones may be a stuck-pipe hazard because of overbalanced mud weights resulting in extreme differential pressure in relation to depleted reservoir pressure.
At first glance, high-angle drilling may not appear to be a significant pressure management issue. Highly deviated wellbores can lead to poor hole cleaning, which has an adverse effect on ECD. In deviated wellbores that exceed 30°, cuttings beds may form due to an insufficient pump rate. This can lead to excessive ECDs, pack-offs and stuck pipe.
Issues with hole cleaning in high-angle wellbores are exacerbated by slim hole and narrow margin because of pump rate constraints mandated by ECD requirements. High angle also increases the likelihood of encountering barite sag. Density differentials within the fluid column may lead to significant differences in pressure exerted on the wellbore. Resultant fluctuations in pressure increase the potential for fracturing the formation, as well as inducing an influx of formation fluid. Low-ECD fluids by nature should be designed to be resistant to barite sag and address fluid stability, ECD and hole cleaning in highly deviated wellbores.
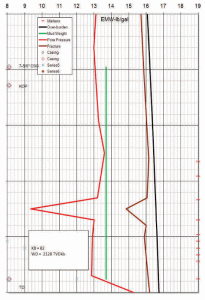
Naturally occurring narrow-margin drilling can come about, for example, through pressure regressions, unconsolidated formation beneath salt or deepwater drilling operations.
Finally, slim-hole drilling represents an ECD challenge because of the pump rates required to transport cuttings through the wellbore. Because of fluid-friction factors, increased fluid velocity leads to more pressure being exerted on the formation in the slim-hole section, thus increasing ECD. Additionally, slim-hole wellbore geometry is more prone to barite sag than larger-diameter wellbores. This is because, under static conditions, the bulk of the fluid column is disturbed by running pipe and/or wireline tools in and out of the hole.
Low-ECD fluid can address these pressure-management challenges. The use of such a fluid may not eliminate pressure-management issues but may ease them to an operationally acceptable level. Use of such a fluid can provide an increased margin of safety.
Designing and Building
Engineering a successful low-ECD fluid is not necessarily straightforward. To reduce the ECD of the drilling fluid under circulating conditions, the overall viscosity profile of the fluid must be reduced. In addition, high gel strengths and excessive pressure to break gels may induce ECD spikes and should be avoided. Reducing the fluid viscosity of conventional fluids may increase the likelihood of encountering barite sag. Therefore, the fluid must be designed in a way that the resistance to barite sag is increased, even as the fluid viscosity is decreased. This is the crux of a successful low-ECD fluid. If barite sag resistance is increased, the fluid viscosity can be decreased. However, if barite sag resistance is low, the only viable option to avoid a sag incident becomes increasing the viscosity of the fluid, which negatively impacts ECD.
Likewise, if a fluid’s viscosity is reduced too greatly, particularly the low-shear rheology, the fluid may be ineffective at hole cleaning. Therefore, what is needed is a fluid that is resistant to barite sag with reduced viscosity but with adequate hole-cleaning characteristics to lift cuttings out of the wellbore. The fluid must also remain stable and suspend weighting material as well as cuttings while static.
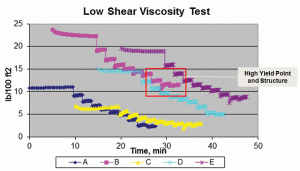
Recognizing an industry need, Baroid, a Halliburton business line, set about designing an improved low-ECD fluid to help address these pressure-management issues. The goal was to improve sag resistance while reducing the rheology of the new fluid compared with the company’s existing Gulf of Mexico offshore, high-performance invert emulsion fluids. While meeting these criteria, maintaining the logistical and operational ease of use of existing fluids was paramount. This would help ensure that the new solution would be compatible with current drilling capabilities and make it easy for operators to adopt the new technology.
Baroid’s existing high-performance, synthetic-based invert emulsion drilling fluids were used as the platform for this formulation. A new approach to assess barite sag potential was the first challenge. The occurrence of barite sag is often difficult to predict, and the exact parameters that cause a fluid to sag are not well understood. Current testing makes it fairly easy to distinguish fluids with a high likelihood of sagging but does not do a good job in differentiating mediocre sag resistance from truly exceptional sag resistance.
To better differentiate the sag potential of a fluid, Baroid decided through investigation that first performing extended aging and stressing of the fluid samples before performance testing was beneficial. In conjunction with 62- and 120-hr static aging, a battery of traditional and new test methods was employed to evaluate the sag potential of fluid samples. These tests included static settling tests, low-shear rheology, fluid-structure evaluation and settling under dynamic conditions. The aggregate results of these tests show a much clearer picture of a fluid’s sag potential.
From this testing, meaningful changes were made to the fluid formulation. To improve the sag resistance, multiple technologies were incorporated, including a higher emulsifier concentration, a new rheology modifier and a unique blend of non-organophillic colloidal solids. These modifications allowed the viscosity of the fluid to be reduced in order to achieve the desired reduction in ECD while maintaining necessary hole-cleaning properties and improving resistance to sag.
Formulation changes were not the only modifications made to the fluid. The need to precondition freshly built fluid at the mud plant prior to load-out was recognized early on. Numerous mechanical shear devices have been employed over the years with only moderate success. Rather than rely on mechanical shear, Halliburton developed a proprietary high-pressure hydraulic shearing device to improve the drilling fluid’s overall properties. The results have eliminated the need to use seed mud when building drilling fluid from scratch.
The hydraulic shearing device delivers fluid properties similar to those seen after multiple passes through the drill bit while drilling.
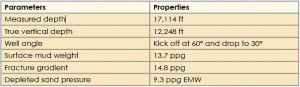
Operator Challenge
In late 2011, an operator needed to drill a technically challenging deepwater sidetrack. The well had several key pressure management challenges, including high angle, a slim-hole drilling configuration with a reamer and a depleted reservoir to be drilled through with a narrow 1.10-ppg difference between pore pressure and fracture gradient. The specifications of this well appear in Table 1.
An analysis of the expected ECDs for the proposed well by Halliburton’s DFG hydraulics software indicated that the given fracture gradient would be exceeded by a significant margin without the use of a low-ECD fluid. This same hydraulics model was used to determine the maximum allowable fluid rheology required to remain within the safe operating window.
Lab pilot testing was then conducted using Baroid’s new low-ECD enhancement package to design a fluid with the reduced rheology necessary while maintaining effective sag resistance. Lab testing indicated a successful fluid meeting the specified criteria could be built.
From there, the fluid was in the mud plant, and the high pressure shearing device was employed to fully condition the fluid prior to load out. The fluid was a scratch-built fluid and contained no previously used seed mud. Table 2 shows the fluid properties before and after application of the high-pressure shear. The post-shear result was a fluid with rheology nearly identical to the properties specified by the hydraulics model.
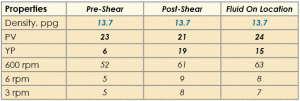
The fluid was loaded on a workboat and shipped to the rig site, arriving on location 10 days later. This was the first test of the fluid’s overall stability. Once on location, the fluid was pumped from the workboat to the rig. While in transit, the fluid received only 30 min of rolling every six hrs, yet maintained its load-out weight and rheological properties. Part of the fluid volume was then pumped down into the rig pontoons for storage and later use.
A window was milled out of the existing 6 5/8-in. inside diameter production casing. Drilling began at 60° using a 6.5-in. pilot bit in conjunction with a 7.5-in. near-bit reamer. Angle was built to 64°, returning to 30°, which was held to TD. A severely depleted permeable sandstone was drilled with approximately 3,000-psi overbalance. The ECD was maintained below the fracture gradient, and no fluid was lost while drilling. By a combination of effective fluid-loss control, sweeps of lost-circulation materials and low ECD, stuck pipe was avoided.
During the drilling phase, the fluid remained extremely stable, giving similar rheology throughout. PWD data verified the hydraulics model, which proved very accurate, with an average variance of 0.05 ppg between the model and actual downhole readings. Following successful drilling, the well was logged on drill pipe for four days.
Through drilling and logging, no indication of barite sag was observed. Multiple trips were made during that time. Flow-line fluid density was monitored by a real-time Coriolis meter, and wireline log-pressure sampling indicated that the sag-resistant character of the fluid had been maintained throughout the wellbore.
After logging operations, 30 bbls of fluid losses were induced when the bottomhole assembly was run to TD before circulating the fluid. Staging into the hole, breaking circulation, as well as circulating at the shoe prior to going into open hole, would have likely avoided these losses. While cementing the liner in place, an additional 188 bbls of fluid were lost; however, partial returns were regained, and zonal isolation was achieved.
Conclusions
This well was a testament to the utility of a low-ECD fluid. The well contained several drilling challenges that benefitted from the reduced viscosity and enhanced sag resistance of the low-ECD fluid. Ultimately, the well was drilled and completed with minimal losses. No indication of barite sag was observed.
Hydraulics modeling indicated that the application of the low-ECD fluid reduced ECDs by 0.47 ppg, compared with conventional Gulf of Mexico synthetic drilling-fluid solutions. As this technology becomes more refined, future incarnations of this fluid may see even greater reductions in ECD.
DFG is a trademark of Halliburton.
Great insight into the evolving challenges of wellbore pressure management. The push for low-ECD fluids that balance sag resistance, stability, and efficient hole cleaning—especially in high-angle or depleted zones—is essential for safer, more cost-effective drilling. Exciting to see innovations like Baroid’s approach addressing these critical needs.