Combination of extended-reach drilling, maximum reservoir contact wells and artificial islands helps ADNOC access offshore reserves with land rig
Wellbore tortuosity and instability, hole cleaning and collision risk among many challenges ADNOC overcame to drill 32,101-ft MD well
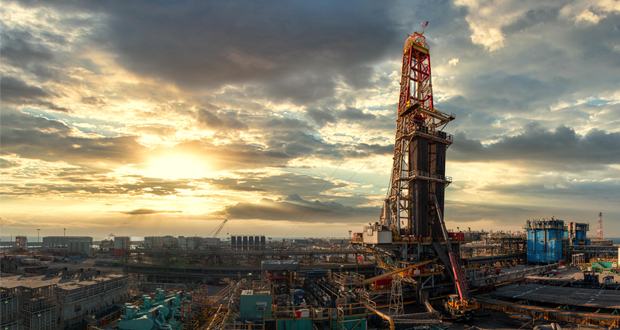
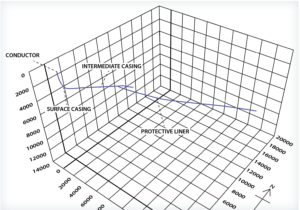
By Stephen Whitfield, Associate Editor
To increase production from shallow-water reservoirs in the Arabian Sea, the Abu Dhabi National Oil Company (ADNOC) has been utilizing a combination of artificial islands and land rigs to drill extended-reach drilling/maximum reservoir contact (ERD/MRC) wells.
Built out of sand dredged from the seabed, these islands can provide a cost-effective alternative to deploying offshore rigs. Then, by drilling multiple ERD sidetrack wells from a single pilot well from that island, ADNOC can explore the far reaches of the reservoir in the ocean without needing to install new subsea infrastructure, said Muhammad Ased Hashmi, Senior Drilling Engineer at ADNOC Onshore. The MRC aspect of the wells, which typically means the well has an aggregate reservoir contact in excess of 5 km, is intended to help the operator achieve higher levels of productivity with each well.
While this approach to accessing offshore reserves has clear benefits, there are also myriad challenges. For one, drilling ERD wells can be extremely difficult, as it requires wellbore stability to be maintained and higher levels of torque to be managed over longer distances. Additionally, because ADNOC uses a cluster drilling approach in order to maximize the well capacity of each island, devising optimal well locations and trajectories can be complex due to space limitations. “With an artificial island, we have a difficult well scheme from a trajectory point of view,” Mr Hashmi said. “In one cluster, we can have several wells being drilled in one area, all going in different directions and into different formations. It’s a planning challenge.”
In this cluster drilling approach, ADNOC first drills a pilot well, which can serve as a reference well for acquiring open-hole data. That data can then be processed to assess and define nearby opportunities, as well as determine the number and location of additional wells to be drilled from the same pad.
Speaking at the 2023 IADC Drilling Caspian Conference in Baku, Azerbaijan, on 8 February, Mr Hashmi discussed his experience while drilling one such well offshore Abu Dhabi. As the target reservoir was shallow, the total vertical depth of the well was only 9,127 ft even though its MD reached 32,101 ft. This resulted in a fairly high extended-reach ratio of 3.52:1, which is well above the 2:1 ratio that typically defines an extended-reach well. This meant that the well would be exceptionally long and torturous, which has implications on the well completion phase. Other difficulties anticipated included high torque, difficulty in hole cleaning, collision risk and subsurface deviation errors.
The well was drilled in six sections:
- a 157-ft, 36-in. hole section using surface casing with an OD (outer diameter) of 30 in.;
- a 2,054, 22-in. section with 18 5/8-in. casing;
- a 7,458-ft, 16-in. section with 13 3/8-in. casing;
- a 5,326-ft, 12 1/4-in. section with 9 5/8-in. casing;
- a 3,772-ft, 8 ½-in. section with 7-in. casing; and
- the 6-in. lower completion section, which was 13,334 ft in length and was drilled with a pre-perforated liner and swellable packers.
Because the well was among the later wells to be drilled in a cluster of 14 wells, not to mention in the presence of other well clusters, congestion in the area was a big challenge. Actions taken to mitigate the related risks included utilizing a real-time gyroscope check-shot survey tool to check for magnetic interference from adjacent wells in close proximity to the cased-hole sections. “We’ve been drilling these types of wells for a long time, but after a while, you don’t have too much space. We need to take the logging data and check the boundaries of the reservoir to see what we can maximize at the boundaries of the reservoir,” Mr Hashmi said.
While drilling the surface hole, ADNOC closely monitored losses vs gains to ensure the hole was full at all times. If the level of fluid dropped due to uncontrolled losses, the drill string would be pulled back to the conductor casing to avoid loose sand being dropped on the BHA and leading it to become stuck.
Because of the presence of multiple depleted aquifers in the well path, which could lead to a total loss of fluid, ensuring good hole cleaning would be critical. Mitigating steps included removing any surplus cuttings so they wouldn’t increase the equivalent circulating density (ECD) on the annulus. Mud weight was also decreased to further reduce the hydrostatic head on a weak formation.
Interbedded shale formations were also present, leading to instability issues. ADNOC alleviated the challenge by decreasing the angle of the drill bit when it drilled through the interbedded formation and then closely monitoring the mud properties. Further, the shale’s reactiveness with the water-based mud meant the well had higher-than-normal torque throughout the drilling process; this increased the risk of a stuck BHA. Mr Hashmi said ADNOC had to closely monitor torque and drag in real time, as well as conduct several short wiper trips to prevent the need for excessive back reaming during final POOH (pull out of hole) operations.
Running casing was difficult, as well. When casing became stuck in the aquifer zone, the operator had to pump 100-200 bbl of freshwater pill, which reduced the hydrostatic head, cleaned the area across the casing and freed the pipes to run to bottom. The use of solid centralizers also helped with cleaning and lowering the casing.
Finally, because the well was closely geosteered across thin layers of reservoir to ensure maximum contact, well tortuosity posed significant obstacles in running the lower completion to TD, Mr Hashmi said. ADNOC’s solution was to run 4 ½-in. tubing to 22,980 ft in the lower completion section, then utilize swellable packers with pre-perforated liners for the remainder of the section.
The packers, which were installed every 500 feet to total depth, helped mitigate potential wellbore instability in the section. The packers swelled on contact with the drilling fluid and sealed the annulus around the drill pipe. The small size of the packers made it suitable for traversing the slim hole in the lower completion section, enabling ADNOC to run the section to total depth.
Overall, the successful completion of the well highlighted the key steps that ADNOC took to manage the increased operational challenges associated with drilling ERD wells in a cluster setup. Mr Hashmi said the lessons learned from this and other ERD wells will help the company to continue exploring the boundaries of its reservoirs. “We have to reach for the edge. We want to see the boundary of the reservoir. When we’re planning the drilling, we have to make sure we have options to diverge from the main area and explore.”
In October last year, ADNOC announced it had set a world record for the longest oil and gas well at 50,000 ft. The well had also been drilled from an artificial island using the ERD concept, at its Upper Zakum Concession.
In announcing the achievement, ADNOC noted that the record ERD well allowed the operator to tap into an undeveloped part of the reservoir, which had the potential to increase the field’s production by 15,000 bbl/day – without the need to expand or build any new infrastructure.
The artificial island concept has already resulted in significant cost savings and environmental benefits, ADNOC said, compared with traditional approaches that typically require more offshore installations and infrastructure.
Upper Zakum is the largest producing field in ADNOC’s portfolio. The company plans to increase the field capacity to 1 million bbl/day by 2024 through a mega expansion project valued at AED 110 billion. The project includes the construction of four artificial islands in shallow water: Umm Al Anbar, Aseeifiya, Ettouk and Al Ghallan. Together, these islands can accommodate 450 wells and 90 platforms, in addition to drilling rigs, processing facilities and other infrastructure.
ADNOC has said the concept was motivated by goals to reduce its environmental footprint while delivering additional energy resources. DC