Access to data, enhanced tool designs drive new efficiencies downhole
Fiber optics, wired pipe improve understanding of reservoir, wellbore, while an innovative design streamlines cased hole re-entries
By Stephen Whitfield, Senior Editor
The industry is always looking for ways to improve the performance of the tools it sends downhole to drill and complete a well. With the emergence of digitalization, intelligent systems have become a popular area of focus, with original equipment manufacturers (OEMs) offering increasingly sophisticated solutions to operators and drillers looking to access as much data as possible about the health and performance of their tools.
Wired drill pipe continues to serve as a valuable system in providing distributed real-time pressure, vibration and temperature data downhole, enabling drillers and operators to make important decisions right away. Developing new smart tools and adding third-party solutions that can connect to wired drill pipe, and the associated broadband telemetry network, has been a priority for NOV.
“We can provide increased bandwidth that allows the driller and the directional drilling providers to access more data from downhole,” said Mats Andersen, VP Global Sales – Downhole Broadband Solutions at NOV. “Visibility to high-resolution, real-time downhole data is helping our customers to decrease operational days, reduce their risk and produce more hydrocarbons.”
Fiber-optic cable-based systems are allowing operators to gain new insight into their completions and reservoirs, helping them improve well performance. Baker Hughes has continued building on its portfolio of smart completions tools with a recently launched wet-mate connection system that can connect fiber-optics to the lower completions, enabling real-time insight into the reservoir during production, which can improve efficiencies and increase ultimate recovery.
“Now that we have tools that help us better understand the reservoir, we can manage the production phase more intelligently,” said Ricardo Tirado, Global Director – Intelligent Production Systems at Baker Hughes. “Previously, it was like trying to fly an airplane, or drive a car, without a dashboard. We now have tools that show you all relevant information so that your recovery is going to improve.”
While intelligent systems and networks are key tools in driving better performance downhole, OEMs are also working to improve the hardware itself. One area of focus for Weatherford is to reduce the risk present in cased-hole sidetracking. A new single-trip casing-exit system eliminates the source of premature shearing while running in hole, an inherent hazard associated with conventional whipstock systems.
“Historically, when tripping in and out of the hole with conventional whipstock systems, we’ve had to move very cautiously. But we now have the technology to help change that thought process,” said Jacob Wright, Global Product Line Champion at Weatherford. “Similar to tripping drill pipe or tubulars, we now have the ability to push, rotate and work through downhole obstructions without fear.”
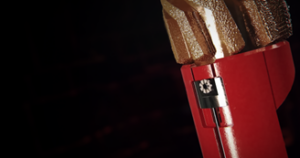
Casing exit without need for shearing
Whipstock systems are common tools in cased hole re-entry, helping operators and drillers access new sections of a wellbore or a different reservoir without the need to drill a new well from surface. However, they often require several trips in and out of hole – a trip to prepare the wellbore for sidetracking, a trip to set and mill the window, and then drilling a sidetrack hole. While these trips are generally less time-consuming and less costly compared with drilling a new well entirely, OEMs have focused on developing technology to help further reduce operational time by reducing the number of trips needed.
One such tool, launched in 2023, is Weatherford’s AlphaV single-trip casing-exit system, which is designed to eliminate the need for a dedicated wellbore preparation run while also doubling trip speed capabilities.
Typically, with a conventional whipstock system, the whipstock and a milling bottomhole assembly (BHA) are deployed into the hole as two separate string members connected by a single bolt with a preset shear value. Once the whipstock system reaches the desired setting depth, an anchor is set and the bolt is sheared, releasing the milling assembly from the whipstock.
This setup requires drillers to, as Mr Wright said, “trip in the hole with caution.” This is because any obstruction downhole, or any unforeseen circumstance like bad weather or rig heave, can potentially cause premature shearing of the bolt, which could result in total loss of the whipstock and further costly intervention work.
Where the AlphaV differentiates from other whipstock systems is the removal of the shearing event. Instead, Weatherford developed a patented hydraulic mill release (HMR) device, consisting of a retractable pin housed within the lead mill and a hydraulic release feature housed within the whipstock. Instead of two BHA components connected by a shear bolt, the system operates as a single unit with the mill release mechanism built in. Once the system reaches the desired depth and is anchored, a hydraulic piston activates the HMR to release the milling assembly from the whipstock.
The system also contains an integrated gauge mill and scraper assembly positioned below the whipstock anchor. Conventional whipstock systems do not have a scraper attached to it, so drillers must engage in a separate run to clean out the wellbore prior to anchoring the whipstock. The internal gauge mill and scraper assembly eliminate this run, as it cleans and scrapes the inner diameter of the casing as the system reaches the desired setting depth downhole.
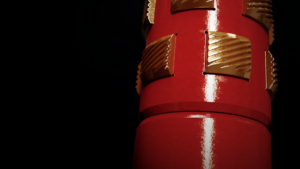
Mr Wright said the combination of the HMR and the integral scraper assembly can lead to significant time savings.
“The wellbore cleanout run is a separate run completed just before deployment of the whipstock assembly,” Mr Wright said. “We’ve found a way to eliminate this run, and that’s a huge time-saver. On a typical North Sea well where one round trip is nearly 20,000 ft, this may take a day to properly clean and scrape the ID of the casing. So, where can we save time? First, we eliminate the wellbore prep run completely by incorporating the gauge mill and scraper assembly in the whipstock BHA. Second, we can trip in the hole at double the trip speed of a conventional system by having a hydraulic mill release system.”
The AlphaV system is being run in Indonesia, Norway, Kuwait and Mexico, and Weatherford says its clients have experienced significant time savings in whipstock installations.
In 2024, the tool helped an unnamed operator save 30 hours of associated rig time by eliminating one round trip from the casing-exit sequence for an onshore well in Kuwait. Weatherford had been tasked with eliminating a dedicated wellbore preparation run on the well by combining scraping and cleaning processes with the casing-exit operation.
Following an examination of the well’s parameters – setting depth of 6,126 ft, 8½-in. hole size – and operational needs, Weatherford recommended the use of the AlphaV, which was mobilized to the rigsite and run to the target depth. Once the whipstock was set and the milling assembly released, a sidetrack window was successfully milled.
The integral scraper in the AlphaV tool allowed the operator to clean and scrape the setting area in the same trip, prior to setting the whipstock. The retractable pin within the HMR system allowed the operator to safely run in hole to target depth by delivering the high-torque and load-bearing capabilities needed to perform cleanup operations in the same run. The drilling BHA successfully passed through the window without any restriction or interference, which ensured the quality and reliability of the sidetrack.
“When you look at what we did in Kuwait, the customer recognized the overall annual OPEX and invisible lost time savings potential that the AlphaV system would provide across their other wells in the area,” Mr Wright said.
In another well in the North Sea, completed last year, AlphaV helped an operator save 14 hours of rig time by enabling a dual-casing exit in one run. The tool performed a single-trip, dual-casing exit in a deviated well to accommodate an 81/2-in. RSS drilling assembly. The time savings helped the operator reduce personnel exposure to the red zone, while also reducing the number of BHAs handled onsite. By successfully milling a full-gauge window and rathole in a single trip, the operator was able to immediately deploy a stiff RSS assembly, removing the need for a mud motor assembly and any additional trips.
Leveraging downhole broadband network for new efficiencies
Wired drill pipe capable of transmitting high-bandwidth data from downhole sensors – and also sending surface control signals back to those sensors – is not new. NOV has provided high-speed drill string telemetry services through its IntelliServ broadband network for the past 20 years. To advance the capabilities associated with the high bandwidth and address evolving customer challenges, the company is currently developing several new tools that are enabled by the network to further address downhole efficiencies.
The downhole broadband network runs through wired drill pipe that incorporates a coaxial cable along the length of the drillstring from the BHA and its sensors installed near the drill bit.
Signal boosters distributed in the drillstring create a telemetry network, which enables bidirectional transmission while also adding multiple along-string measurements for pressure, vibration, temperature and RPM data between the surface and downhole tools at speeds up to 57,600 bits/second, compared with 48 bits/second for conventional mud-pulse telemetry systems. These high speeds allow for near-instant communication to downhole.
Mr Andersen of NOV noted one value of using wired pipe and the associated downhole broadband network is that data-driven activities – like surveys, downlinks and slide orientations – can be performed in a few seconds, rather than a few minutes with a mud-pulse system. But the benefits to wired pipe go beyond telemetry time savings. Because the pipe is hardwired to the drillstring, it can continue measuring even in the absence of sufficient fluid flow downhole.
“A mud pulse system needs flow – without it, it would shut down so you can’t tell what’s happening downhole. With wired drill pipe, you will still be able to see your downhole pressures as you’re trying to mitigate that event. If there’s a pack-off or if it’s a lost-circulation event, we’re also able to identify the location of that pack-off and lost circulation. Because it’s obviously going to be between two sensors in the string, you will see the difference in pressure, so you can then narrow in on where your potential weak zone or troublesome interval would be,” he said.
One of the benefits NOV touts with its wired pipe system is the ability to connect additional tools to the network, such as its enhanced measurement system. It is a collar-based downhole drilling dynamics measurement tool that acquires downhole weight and torque at tool, temperature, annular and internal pressure, rotational velocity, bending and three-axis vibration data at high frequencies. This data can help identify potential dysfunctions, such as stick-slip, and issues with borehole quality in real time.
Lately, the company has been working to add more tools connected to the network, both internally and by supporting external partners. One area the company has focused on together with an external partner is caliper tools, or tools that allow drillers to measure the shape of the borehole as they’re drilling and tripping out, using acoustic data measured by wired drill pipe. “The caliper tools would allow you to see the change in borehole shape over time, creating a 4D caliper,” Mr Andersen said.
Parts are currently being ordered for a trial version of the caliper tools, and field testing is scheduled for later this year.
Another technology under development is a smart tool activated by a signal on the wired pipe that would replace the ball drop-activation used for many mechanical downhole tools in all types of drilling- and completion-related activities. The traditional ball drop systems require a metal ball to be pumped from surface into the ball seat of the downhole tool to trigger an open, close or release function.
This new tool would be installed in several different tools in the string, an example being the circulation sub. It would use a signal on the downhole broadband network sent from surface, which would then activate a mechanism in the specific tool that would open and close nozzles embedded within the tool to allow for sidewall flow, which would then clean the casing or wellbore.
“With ball drops, you have to wait for the ball to reach a certain point before you are allowed to open or close a circulation sub, taking time and being dependent on flow and well trajectory. We want to develop a smart tool that can just activate that mechanism by a simple signal on our network,” Mr Andersen said.
Field testing on the smart tool is anticipated to begin in 2025, and Mr Andersen said the company expects to have the tool commercially available by the end of this year.
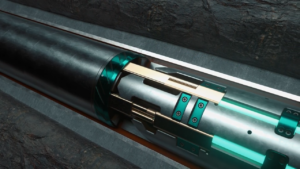
Intelligent completions with added sand control capabilities
Multi-trip completion designs – which are commonly used in offshore wells, subsea and other complex wells – can help reliably get the completion assembly to the desired depth in extended-reach wells. However, while these designs help address the risks involved in getting the assembly to depth, they also restrict the ability to run fiber-optic cables across the full wellbore. Normally, a company runs fiber-optic cables in the upper completion, but that does not give them access to real-time data in the reservoir.
Baker Hughes’ SureCONNECT FE system was designed to make multi-trip completions with fiber-optic and electric capability a commonality. The system is comprised of a series of wet-mate connectors, attached to the production string, and fiber-optic and electric cables that can provide distributed temperature and acoustic sensing, as well as electric valves and sensors.
“If completing in two trips is the only way to get to the desired depth, then you need a tool like this to get the fiber cable down to the lower completion,” Mr Tirado with Baker Hughes said. “If you just run the upper completion with fiber, you’re only monitoring the upper completion. There’s no reservoir measurement. If you only monitor the upper completion, you can see things like pipe leaks or gas life functionality, but you cannot see the reservoir. In order to see the reservoir, you have to deploy the fiber in the lower completion.”
A separate tool connected to the fiber-optic cable at surface – called an interrogator – sends laser pulses down the cable to measure the temperature along the production string, as well as the frequency and amplitude of acoustic data. Subsurface engineers can then read this data to get a comprehensive understanding of reservoir performance in real time for the life of the well.
The information gathered is processed at surface and turned into actionable insights. These includes actions like shutting off water and gas-dominant zones through remotely actuated interval control valves to optimize production in real time.
“The fiber itself is a long sensor,” Mr Tirado said. “It provides a temperature profile, and it’s a very long microphone that’s listening all the time. We can do analytics at the surface and interpret the data. For example, we can tell you that this sound you’re listening to may indicate water breakthrough, or maybe you’re getting gas. You can infer what’s happening with the data we collect and make decisions based on that.”
The system also allows workover operations to be completed without retrieving the lower completion, such as installation or retrieval of an electrical submersible pump or repairing a safety valve. This significantly decreases rig time, safety risks and equipment costs.
The first-generation downhole fiber-optic wet-connect system was initially deployed offshore in the Gulf of Mexico in 2011. Since then, different versions have been run in the North Sea.
In January 2025, Baker Hughes launched the latest version of the system, SureCONNECT FE. This new version will run concurrently with a gravel-pack system – fiber-optic cables will be attached to the sand control screens to measure, in real time, the migration of reservoir sand into the wellbore.
“Now, with this new iteration, you can preserve your sand control system and just make sure that you’re producing at the right rates, that you’re also managing the production the way you want. It’s the same benefit you got with our previous iterations, but now you can get it with sand control. It’s expanding the application envelope of the system,” Mr Tirado said.
Baker Hughes delivered the first SureCONNECT FE system to a client in 2025, and Mr Tirado said the company has received a lot of traction from operators in potentially using the system. However, those operators are “waiting for us to have that first installation” before implementing the system on their own wells.
Looking further out in the future, Mr Tirado said SureCONNECT could provide value in new energy domains, including geothermal wells. Fiber-optic sensing does not require downhole electronics, which could potentially suffer damage in the kind of high-temperature environments often found in geothermal wells. However, the company is examining a number of special coatings that can be used to enhance the life of the fiber at extreme temperatures, he said.
“We feel that this system can be used across all these different applications,” Mr Tirado said. “SureCONNECT is basically enabling a connection. If you want to run a completion in two trips and you need some sand control applications, it can provide value. That’s the beauty of a downhole tool like this – you just connect and reconnect the cable again and again.” DC