Noble harnesses nano-KPIs, global equipment data to deliver insights, drive consistency
Integrated performance analyses help to identify operational variations, improve tripping speeds
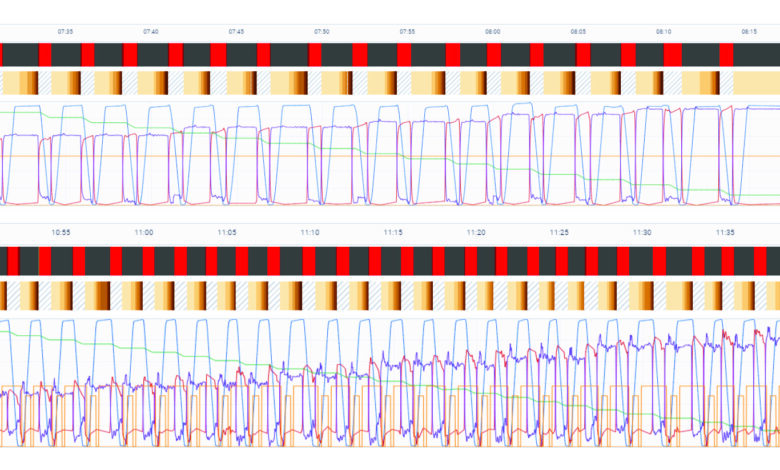
By Bernardo Braunstein, Noble Drilling; John Rigg, TDE Digital
Noble Drilling and TDE Digital have designed and deployed an integrated performance system that uses both raw data sources and human expertise to drive fleetwide efficiency gains for targeted critical-path operations. The combination of large volumes of data, a variety of data sources, the speed of transmission, and the increase in data-processing capabilities enables a myriad of new possibilities to monitor and improve drilling performance.
In recent decades, offshore drilling operations have become substantially more automated, driving continuous improvements and the delivery of safer and more efficient wells. Drilling equipment packages were essentially designed to control drilling operations and operate machinery; therefore, the ability to measure a rig’s operational performance has been limited to the original design intent of these systems.
Continuous performance improvement has always been a key factor in driving competition in the upstream market and ensuring sustainability during extended downturn cycles.
Certain companies developed their own technologies and methodologies to extract data from drilling control systems or to design reports to measure and track performance, while others outsourced this process.
Objective and scope
In conjunction with the design of the enhanced rig-state detection system, Noble and TDE Digital developed and tested nano-level key performance indicators (KPIs) that are aggregated in real time and delivered to key stakeholders within Noble to drive fleetwide safety, efficiency and consistency through a managed rollout program.
Noble identified tripping drill pipe operations along the critical path as an initial opportunity for “flat time” optimization since these operations account for a significant portion of the overall offshore well delivery process.
An established rig-state engine – multi-layered algorithms designed to detect specific operations based on a pre-defined set of criteria – was expanded to implement logic that automatically classifies top drive, iron roughneck and pipe racker movements. A series of sub-states derived from this engine allows for separating between running in and pulling out of hole. Operations classification can be done both in real time and offline as batch processing for historical wells.
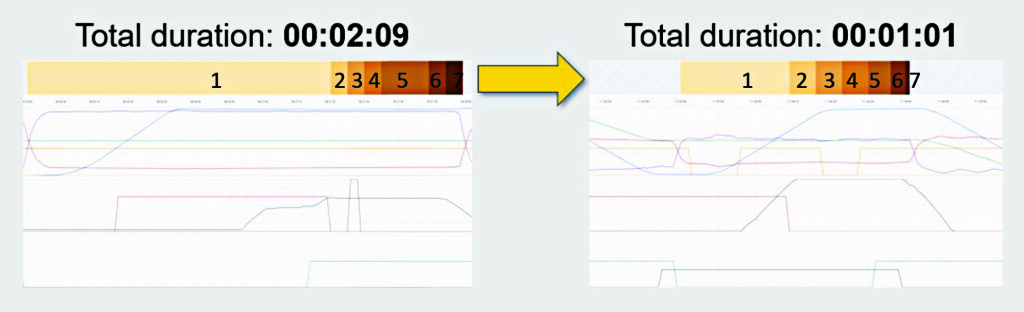
Procedures and implementation
Raw data from operating equipment is captured by surface rig sensors at the rig site and transmitted to Noble’s central data repository. This raw data is then integrated with other data sets and transmitted into TDE’s cloud environment through a custom transfer process. This system handles more than 1 billion data points each month.
The sensor data runs through a multi-tiered quality assurance (QA/QC) protocol with a blend of automated and manual workflows, including checking sensor thresholds, data frequency and time-series checks. This ensures the data can be trusted as accurate before producing metrics.
In addition to the design and deployment of the necessary data flow and QA/QC for equipment monitoring, the project considered several key requirements:
- Deliver real-time KPI metrics to front-line teams to ensure actionable insights;
- Deconstruct tripping operations through the development of critical path sub-steps (nano-KPIs) to allow highly granular data analysis;
- Contextualize data to specifically label restricted vs non-restricted tripping operations, discuss and adopt guidelines for restrictions based on both data and reporting standards;
- Define and apply performance benchmarking to accurately capture invisible lost time (ILT) and track actual savings compared with benchmarking performance levels;
- Integrate data sets to enable Noble business systems and applications teams to build on internal reporting capabilities;
- Deliver a reliable tracking system to ensure accurate and precise performance detection; and
- Design scalable and automated solutions to minimize maintenance and increase uptime.
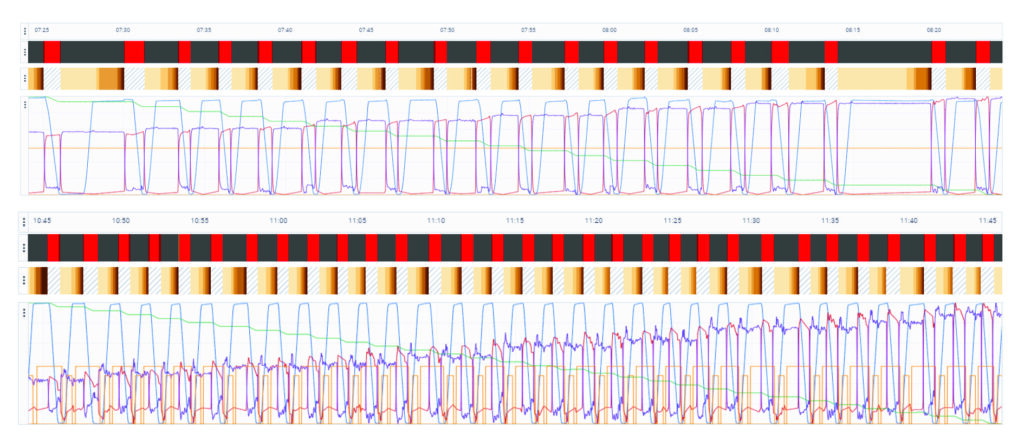
TDE runs its Automatic Operations Recognition (OpRec) system, KPI aggregation algorithms and QA/QC processes in real time against the incoming data and validates activities against daily drilling reporting information. The combination of raw data and human input from the rig-site report allows the determination of restricted vs non-restricted events. Various aspects of tripping, drilling and completions are subject to restrictions, such as well control or mechanical limitations.
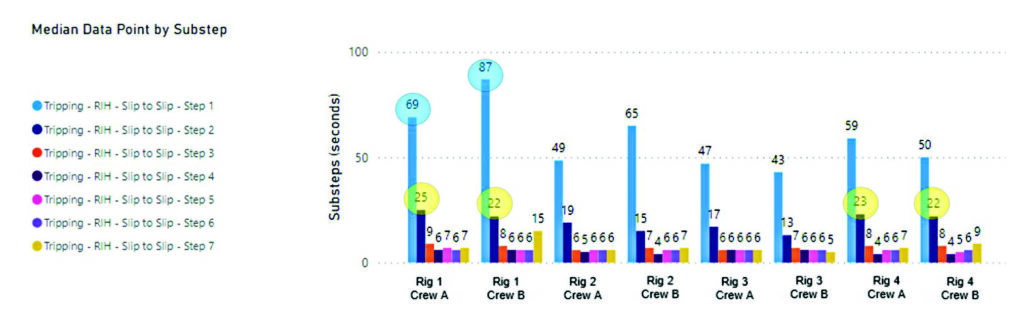
Blending manual classification processes with automated rig-state detection helps drive focus on non-restricted metrics, over which the contractor has full control, to enable performance improvement. Further, this allows the accurate classification of operation-specific KPIs like drilling, tripping, casing, riser, etc, and other non-drilling time operations (i.e., making up/breaking out equipment, wellbore conditioning, NPT, etc).
Prior to implementation, baseline performance levels were established to generate actual savings figures over time. Targets were also set based on best safe practices and rig types for integration into the performance monitoring system to automatically track ILT.
Delivery of aggregated metrics, such as drilling parameters, operational consistency, flat-time efficiencies and equipment performance, are delivered in real time. This enables Noble business and engineering teams to supplement internal analysis via REST API, TDE’s proNova web-based application, and to direct connections to Business Intelligence (BI) applications.
Case studies
Following a trial period, KPIs of focus, comparable rig performance levels, procedural roadmaps and baselines/targets were communicated to rig teams to facilitate knowledge sharing for continuous improvement and ensure successful adoption of updated roadmaps that focus on consistency.
Case Study 1: Designing
best-practice roadmaps
To analyze different operational occurrences and identify the most efficient tripping sequence, a special data exploratory analysis was performed, ranking overall non-restricted tripping slip-to-slip operations.
Having identified the highest ranked (1.01 min) and average (2.09 min) operation, the performance team was able to compare equipment involved in the operation and review underlying factors affecting performance to identify best operational practices. The discussion involved sister vessels, and the results were shared as insights between crews.
Differing operating procedures could be performed and freely tracked between crews and rigs to help build an accurate narrative for a standard operating procedure.
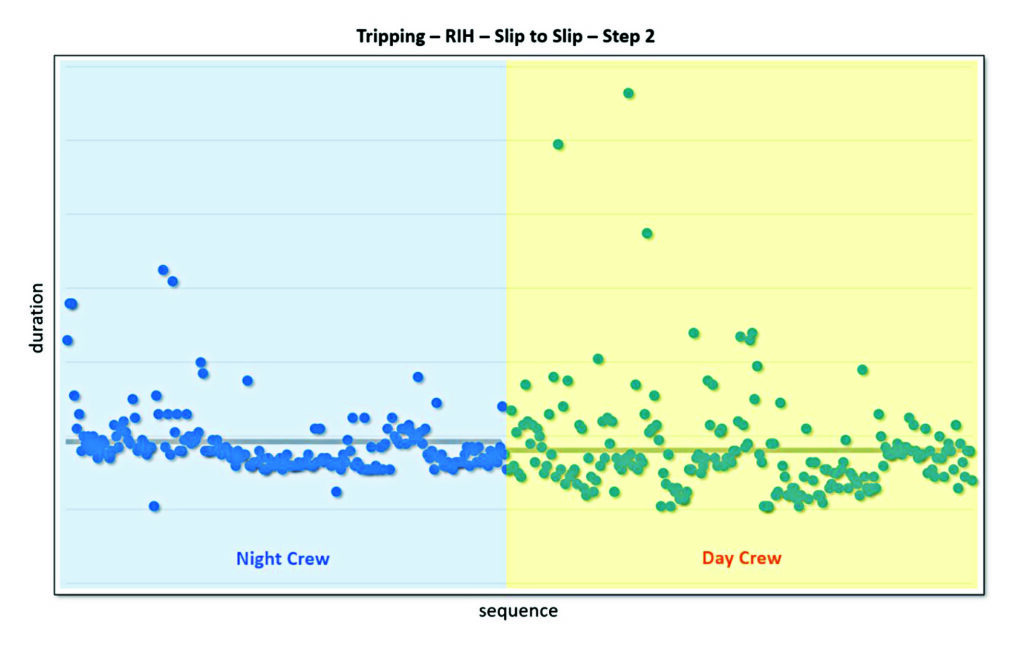
Case Study 2: Remediation planning and strategy
Several cases of inconsistencies went beyond disparate operating procedures and the type of equipment used for the operations.
One example exposed differences between rigs utilizing a new zone management system and those with an old version. Rigs with the new version of the zone management system allowed the operator to use certain equipment simultaneously and more efficiently compared with the old version.
A higher-level KPI – tripping gross running speed – was used to compare rigs with and without the upgrade; however, the performance comparison at this level included several other variables that resulted in an inconclusive analysis. Without a clear measurement of specific sub-steps, the operating teams were unable to correlate and measure the exact aggregated value of this system upgrade.
When comparing specific nano-KPI steps between rigs with and without the upgraded system, the performance team was able to measure the efficiency gains precisely, allowing management teams to assess the time savings and assist in decisions about rig equipment upgrades.
Another savings analysis example allowed the identification of process variations between rigs cleaning threads prior to making connections along the critical path vs those conducting this operation off the critical path.
Case Study 3: Knowledge sharing and real-time learning
Breaking crew-specific operations down to the nano level can highlight consistency around an established target based on safe operating procedure, revealing how crews are using equipment and identifying training needs. Adding this visibility provides drillers with clear knowledge-sharing opportunities.
A comparison between day and night crews for a selected rig on nano-KPI step 2 presented a large process deviation. Analysis indicates both crews increased consistency over time, though the day crew initially presented overall larger process variations. Knowledge sharing assisted in the normalization of the process.
Noble also considered underlying performance factors, since several variables are not visible through equipment signals and real-time data. To help determine the root cause of deviations and outliers, regular discussions with field personnel were conducted to understand and consider potentially limiting factors and apply this to the post-analysis and roadmaps.
Access to granular data enables assumptions based on experience, but the full understanding of operations variables enables some of the most valuable and actionable insights. This is specifically important when comparing crews to one another. Measuring and tracking tripping performance at a high level, such as looking at overall gross tripping speed, can provide performance indicators. Generating granular sub-steps allows for the identification of exact process variations and impactful discussions when recommending realistic actions to improve safety and efficiency.
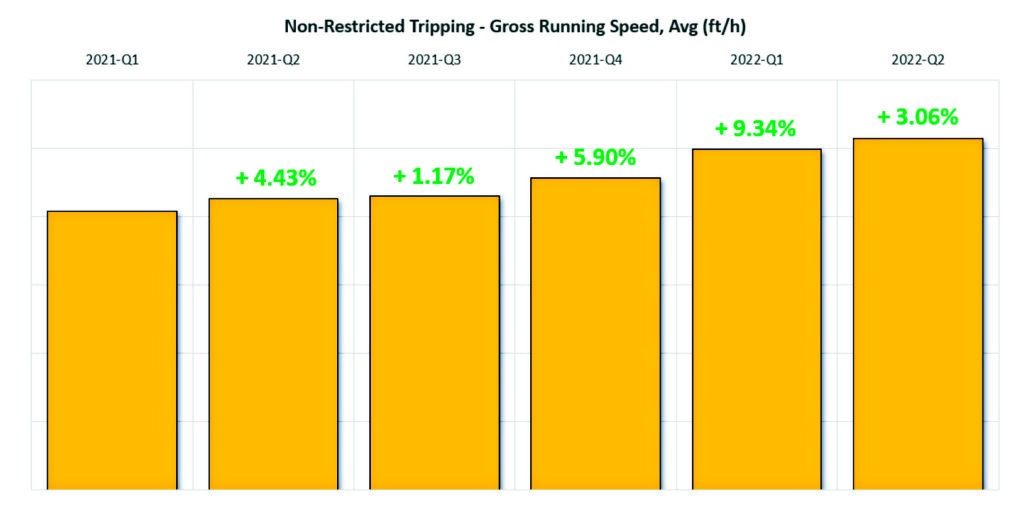
Conclusions and outlook
From August 2021 through July 2022, Noble and TDE implemented a focused performance-optimization process centered on seven tripping and drilling KPIs. Baselines established with the methodology described here equated to a total fleetwide actual savings of 193 hours across 19 offshore rigs. Non-restricted tripping accounted for nearly 66%, or 5.28 days, of total savings — indicating an overall non-restricted gross tripping speed improvement of over 25%. The integration of a performance tool with a focused reporting system and rig team participation contributed to these results.
The mapping of equipment data tags and derived metrics through an industry-proven methodology provides deeper insights for creating procedural roadmaps and, when coupled with a centrally managed performance implementation strategy, drilling rig performance capability can be maximized in a safe and scalable manner.
Noble is continuing its examination of equipment sensors and operator/machine interactions to identify opportunities for continuous improvement throughout the drilling process. In the short term, Noble is applying this technology to detect nano-KPIs from additional operations and to identify further procedure variations derived from other equipment channels.
Combining big data and machine learning is expected to play a major role in automating performance-optimization recommendations and further improving rig efficiency and safety. DC
This article is based on a presentation at the 2022 IADC Advanced Rig Technology Conference, held in Austin, Texas, 30-31 August.