Safety tools in the digital age: Intelligent tracking systems provide new methods of keeping personnel out of harm’s way
Wearable alert device keeps humans away from moving equipment, while computer vision can detect safety violations in real time
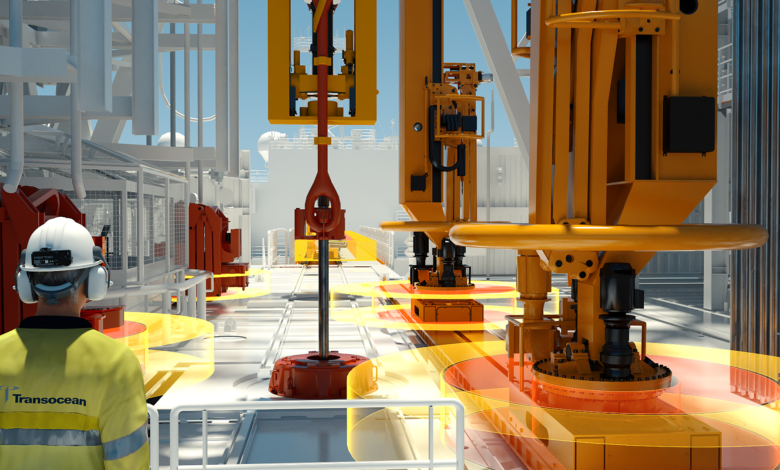
By Stephen Whitfield, Associate Editor
Digital technologies have become an increasingly important part of the driller’s safety toolbox. In particular, companies are looking to AI-based monitoring systems and wearable alert devices to better track and manage crew movement on the rig, enhancing their capability to keep people away from potential hazards.
More and more, leveraging these high-tech devices is also seen as an important part in the continued modernization of drilling rigs – something that is enabling companies to “assemble the crews of the future,” said Travis McGuire, Operations Performance Manager at Transocean. Today’s drilling rigs are changing fast, he said, and companies incorporating augmented learning and digitalization into their protocols are better armed to attract young workers.
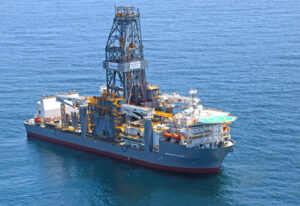
Wearable alarms
The HaloGuard system, first deployed by Transocean in February 2021, consists of a wearable alarm and a real-time location transmitter, worn on coveralls or hard hats, combined with a machine vision system that is designed to pinpoint the position of personnel on the drill floor and key drill floor equipment.
Each day, crew members who need to enter restricted-access zones on the drill floor will receive a wearable device after attending pre-job briefings. Their locations are continuously updated in the system throughout the day as they move around. If they come within a certain proximity of moving equipment, they’re notified by an audible alarm embedded in the wearable device. If that person remains in proximity of the moving equipment, the system will stop the equipment.
“By enabling these machines with the technology to track, sense and – if needed – stop the equipment from running, we’re providing that extra, advanced layer of individual protection to our people on the drill floor,” Mr McGuire said.
Development of the technology began in April 2018 on four separate tracks: wireless location services, machine vision, user interface and equipment stop. Of the four, wireless locating communication capabilities posed the biggest challenge, Mr McGuire said, noting that the amount of steel on the drill floor causes multiple reflections of wireless signals, as well as light. Transocean also recognized that the wearable devices would need to meet stringent hazardous area electrical certifications.
The machine vision scope of the project leveraged work that had already been done by other industries in driverless automation and robotic vision automation. In addition to the challenges related to the steel on the drill floor, adapting the technology for an offshore rig environment involved accounting for changing weather and lighting conditions.
To overcome these challenges, Transocean and its project partners developed filtering techniques and combined them with image-based human detection algorithms to better identify and locate people on the drill floor.
While HaloGuard is only one tool within a comprehensive safety management system, “we view it as a differentiating safety system that others will want to utilize within our industry,” Mr McGuire said. While Transocean helped to develop the technology, it is not exclusive to the company and is being marketed to the wider industry by a third party.
Last year, Transocean deployed the HaloGuard system on the Deepwater Conqueror, Deepwater Invictus, Deepwater Poseidon and Deepwater Thalassa. This fall, an additional installation is planned for the Deepwater Asgard. Two other drillships will be outfitted with the system as the rigs’ work schedules allow.
In addition to HaloGuard, Transocean also launched its Operations Procedure System (OPS) application in February. The app digitizes workflows that traditionally involved paper, including handover notes, daily instructions and the execution of procedures. The app is expected to enable greater proactive monitoring and management of procedures.
Whenever a procedure is completed on the rig, it is archived with time-stamped records of all the verifications performed. Photographs of various issues or concerns can also be uploaded to the app, and if the driller identifies a corporate learning from that issue, the relevant master procedure can be updated within the app. The next time a crew member on a rig of a similar class opens the procedure, the update will already be incorporated.
Transocean is currently testing the app on one rig and has plans for a wider rollout among its fleet. One of the app’s biggest values so far, Mr McGuire said, has been in identifying situations where rig crews cannot complete verification steps as written and cannot progress with a given procedure. In that case, Transocean then works with its subject matter experts to find an alternative verification, which is updated within the app and made available for all rigs of the same class.
“Digitalization like this provides us with valuable insights into what our crews are seeing on the rig throughout their tasks and allows us to promulgate this information fleetwide,” Mr McGuire said.
Another digital tool that Transocean has leveraged to improve safety is training simulators. By replicating exact rig conditions, crews can gain experience in an immersive virtual environment and practice decision making in a variety of potential scenarios.
The importance of being able to make mistakes and learn from them in a simulator “cannot be overstated,” Mr McGuire said. Within the company’s Bridge Simulator, for example, instructors can duplicate the wind, waves and ocean current to create specific impacts on the vessel’s motion and station-keeping capabilities – including scenarios that a crew wouldn’t want to see in real life but for which they should nevertheless be prepared.
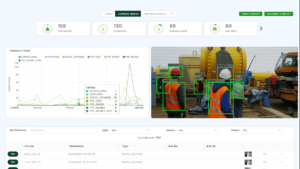
AI-based monitoring
SparkCognition Visual AI Advisor is another system that aims to improve safety on the rig. The technology, which has already been in use at construction sites and in other industrial applications, gathers data from CCTV feeds, drone footage, video from handheld devices and existing camera infrastructure to provide a comprehensive view of rig activity.
The goal is to help drillers better understand how well their crews are following safety protocols.
The software application consolidates video feeds and sensor data into a single interface that can be viewed on the rig’s control system, a smartphone or tablet. It is based on the concept of computer vision, a field of artificial intelligence that enables computers to derive meaningful information from digital images and other visual inputs, then make recommendations based on that information.
Deep learning models built into the app mimic the hierarchical nature of human vision – detecting basic scene and image elements, tracking objects and regions within a scene, and determining what activities are being performed within that scene.
Users can pre-set various parameters relating to HSE compliance or personal protection equipment (PPE) – for instance, establishing that rig crews must wear hard hats on the rig floor, or that they must follow specific protocols around specific equipment. The application then monitors for violations of those parameters and provides real-time alerts via the user interface.
Computer vision inspection systems like Visual AI Advisor exceed human capability to perform quality-control tasks in terms of speed, scale, accuracy and repeatability, according to Phillippe Herve, Senior VP of Energy and Sustainability at SparkCognition.
“With this system, you don’t need someone to be watching the people and checking if they’re wearing their safety glasses or other PPE,” Mr Herve said. “The AI can watch the video screens and record the violations in real time. If the system detects something dangerous or if someone’s going to get injured, it prompts people to take immediate action.”
Reliability is paramount with a system like this, Mr Herve said, noting that his company had to ensure the system doesn’t give false positives or false negatives, even when monitoring “hundreds of different people with different shapes and in different environments.”
SparkCognition is now testing the application using pre-recorded video from various drilling contractors. The company says it expects to confirm that all parameter violations identified by the system will match those identified through human analysis. By Q3 this year, the company will move on to field testing on drilling rigs using live video. The company anticipates the application will be deployed commercially on drilling rigs by early 2023. DC