Raising the sand bar
Industry innovates in low-cost environment by retooling field-proven technologies, updating recommended practices and devising creative combinations to overcome sand control challenges
By Katie Mazerov, Contributing Editor
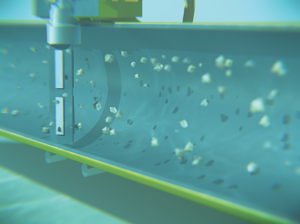
In virtually every well worldwide, operators have to contend with some degree of sand production, a phenomenon that more often than not leads to erosion, sand accumulation, plugging, formation collapse and contamination. These issues have serious financial, safety and environmental implications for operators, often resulting in clean-outs, reduced flow rates and production, and unplanned shutdowns.
“Although some wells routinely experience manageable sand production, these wells are the exception, not the rule,” said Martin Zhang, President of Calgary-based Transmer Energy Services. “In most cases, sand production will result in reduced productivity and expensive maintenance to both downhole and surface equipment. Attempting to manage the effects of severe sand production over the life of the well is not an economically attractive or prudent operating alternative. A large amount of sand may also cause permanent failure of the wellbore and well equipment.”

In some cases, the full extent of the damage is not immediately apparent. In the event of a formation collapse, for example, the sand grains can rearrange themselves to create a lower permeability than originally existed, especially in formations with a high clay content or wide range of grain sizes, Mr Zhang added.
“The collapse of the formation is particularly significant if the formation fills or partially fills the perforation tunnels. Even a small amount of formation material filling the perforation tunnels will lead to a significant increase in pressure drop across the formation near the wellbore for a given flow rate.”
Over the decades, various sand management tools, ranging from low-cost slotted liners to highly advanced gravel pack and sand screen systems, have proven effective in helping companies achieve that desirable balance of optimizing production while controlling sand. Strategies vary based on formation type, grain size distribution and the risk profile of a specific play.
While reliability and efficiency rank high on operators’ lists of considerations, cost is also important in this low commodity price market. These days, innovation isn’t just about developing new, high-end techniques. Instead, the industry is seeing a trend toward unique and creative application of long-used methods, improving on field-proven tools and updating recommended practices to address sand control issues in challenging frontiers, such as deepwater, where costs and the risk of failure are especially high.
Brazilian operator Queiroz Galvão Exploration and Production (QGEP) successfully devised a unique combination of existing sand control technologies for testing a horizontal well design to produce viscous oil from an ultra-deep unconsolidated sandstone reservoir with low burial depth in the Santos Basin’s post-salt Atlanta field.

The project, which involved constructing and testing two horizontal production wells in 2013 and 2014, marked a milestone for producing oil with a viscosity of 228 cP in sandstones at a water depth of 5,085 ft (1,550 m), said Carlos A. Pedroso, Senior Petroleum Engineer at QGEP. Mr Pedroso was also lead author of a paper, “Packing the Unpackable: How the Use of Best Sand Control Technologies Reversed the Marginal Project of Atlanta in a Promising Development,” presented at the SPE Annual Technical Conference & Exhibition, held 28-30 September in Houston.
Experience makes the difference
Previous failed attempts by a consortium of three major operators to test a horizontal well design using conventional sand control methods in the challenging field had deemed the project marginal, Mr Pedroso noted. “However, the use of combined, existing methods, rather than new, expensive technologies, enabled a small operator like us to recover the reliability of the project, showing that knowledge and experience can make the difference.”
After acquiring the block in 2012, QGEP did extensive analysis on the technical and economic viability of the harsh-environment project, with the lower completion, or sand control phase, identified as one of the main challenges. The wells also had to be positioned to accommodate a large and active aquifer on the bottom of the reservoir. “Although risky, the project was considered feasible as the highly skilled interdisciplinary team would be allowed to use the best techniques available,” Mr Pedroso said. “Obviously, the estimated oil in place of 1.5 billion bbl and excellent rock properties, with an average porosity of 36% and permeability in the 4-6 Darcy range, counted a lot in making that determination.”
The team’s plan involved drilling a 2,625-ft (800-m) horizontal section to accommodate the high oil viscosity and pumping a gravel pack for sand control, Mr Pedroso explained. However, the long lateral section, combined with the very low fracture gradient of 0.51 psi/ft, eliminated the possibility of using conventional gravel pack pumping techniques. In addition, the need to maximize the inside diameter of the screens discouraged the use of shunt tubes. “Because of the low fracture gradient, we needed to enlarge the operational window to pump the gravel pack to the desired length,” he said. “This was done by decreasing the critical velocity, or the minimum velocity that the gravel can be pumped to reduce the pressure over the open hole.” To that end, the proppant and density concentrations were decreased. Elimination of the rat hole with a retractable shoe reduced the well diameter, further decreasing critical velocity.
The overall strategy also included performing, in the pilot well, a micro-fracture in the reservoir rock to determine the precise fracture pressure; use of light and ultra-light proppant with a relative density of 1.3 or 1.08 grams/cu cm; reducing the gravel pack fluid weight using equivalent circulating density and adding the proppant weight to compose the final gravel pack fluid weight; reducing backpressure by pumping the gravel pack with the blowout preventer open; reducing the proppant concentration at onset of pumping and using multiple beta waves to reduce the pumping rate. Twenty-four gravel pack screens with six water and six oil tracers were placed at strategic points in the reservoir to monitor flux in the reservoir.

Drill stem tests in both wells confirmed reservoir properties, well integrity with zero skin, no sand or solids production and good well productivity. “The well design and optimized gravel pack operation enabled a good formation test to evaluate the horizontal well concept and prove the economic viability of the entire project,” Mr Pedroso said. The strategy, with some improvements, will be used to develop a definitive production system in the Atlanta field, with 10 wells planned in early 2017, he added.
Expanding the possibilities
Halliburton has also found new ways to use existing methods. The company’s advanced mesh screen, part of the PetroGuard sand screen portfolio, was introduced two years ago for heavy-oil reservoirs with fine sands but has since been expanded for use in non-heavy oil reservoirs.
“We’ve taken a technology initially targeted to a narrow segment of the market and applied it to a wider part of the market,” said Travis Hailey, Product Champion, Sand Control, for Halliburton. The screen has graduated filtration layers that filter increasingly smaller particles from the production stream as flow moves toward the base pipe so that fewer solid particles enter the critical, final filtration layer. In this way, the screen better tolerates reservoirs with non-uniform sands, helping to eliminate the need to pump a gravel pack.
“A mixture of particulate sizes is detrimental to permeability and also more likely to plug the filtration medium than if the sands are more uniform in size,” Mr Hailey explained. “In today’s environment, operators are looking for lower-cost ways to accomplish the same objective. This is a high-end screen, but if we can avoid pumping a gravel pack, it makes the operation substantially less costly than using a lower-cost screen with a gravel pack around it. In deepwater reservoirs, a pumping operation alone can cost $1 million or more per job.” The screen has been installed in 10 fields globally, including Latin America, Asia Pacific, West Africa and Azerbaijan.
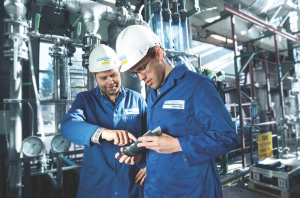
In 2014, the screen was run in an 84° horizontal well with less than 20% fine production in the Caspian Sea, Azerbaijan, where rig and economic constraints permitted only standalone screens. A 6 5/8-in. advanced mesh 175D micron screen was installed in an 8 ½-in., 250-m open-hole section, enabling an initial flow of 2,200 BPD of oil and 42,000 cu m/day of gas, with no water cut. Today, the well is producing 1,445 BPD of oil and 32,000 cu m/day of gas, with a 30% water cut. No sand issues or screen plugging have been detected. The installation marked the first successful standalone screen completion in the Caspian, with 10 more planned in the region.
Halliburton also recently introduced a retooled design of a field-proven method that enhances gravel packing in long horizontal production intervals by providing an alternate path to the borehole screen annulus. The PetroGuard Shunt System resists fluid leak-off to the reservoir while packing the interval, with the ability to bypass collapsed hole conditions and reduce erosion to the borehole wall while pumping.

“We have improved on the operational aspects of shunt technology with a system that is easier and faster to assemble, more user-friendly and provides more pressure,” Mr Hailey said. The system has two larger transport tubes and two smaller packing tubes, all mounted to a standard sand screen. A metal-to-metal sealing oriented thread aligns the design between the sand screen joints. The system is targeted for deepwater unconsolidated sandstone provinces, including Brazil and West Africa. The first system was installed on a deepwater well in Nigeria in May. A second installation in West Africa is planned for Q4 2015.
Updating recommended practices
Effective sand management also involves development of a strategy and adherence to global recommended practices and models, some of which have been in place for years. In September, DNV GL – Oil and Gas issued an update to a recommended practice, RP-0501, which was originally issued in 1996 after the company established models for erosion in piping systems. The 2015 update, in part driven by the current price environment, provides new guidance on the development, implementation and follow-up of a high-level sand management strategy, as well as additional background material for erosion response models.
“Operators are looking to increase production rates to compensate for very low oil and gas prices,” explained Espen Cramer, Global Service Area Director for DNV GL – Oil and Gas. “Sand management is a very complex field, and this new RP captures the combined knowledge we have gained over the last 20 years through assessments, testing and execution of various joint industry projects. The objective has been to help operators enhance production in a safe, sustainable and consistent manner.”
The update takes a holistic approach to sand management by providing a simple set of guidelines to effectively manage sand through the various stages of design and operation of oil and gas production facilities. It emphasizes making the best use of available solutions, rather than addressing a specific method or technology, explained Lars Even Torbergsen, Senior Principal Specialist, Sand Management for DNV GL – Oil and Gas.
“In many older North Sea fields, production systems were designed for zero sand production, with downhole equipment deployed on the assumption of a strong, well-consolidated reservoir,” he said. “Collaboration with operators over the years revealed that, in many cases, they didn’t have a system in place for managing the consequences of sand production and, as a result, took a conservative approach, choking back wells to reduce sand production, which unnecessarily limited hydrocarbon production potential. Some operators lacked the proper focus when it came to the negative effects of sand in their systems, which led to unwanted incidents.”
The updated RP reflects the cooperative effort between DNV GL and Statoil on the operator’s Gullfaks development in the North Sea, which saw a significant improvement in production and revenue after new sand management principles were applied back in 2005. Previously, an estimated 50% of Gullfaks wells had been choked back due to potential sand production.

The implications of producing a certain amount of sand vary depending on the type of reservoir and how a specific sand control system is set up, so the guidance is designed for broad applications, Mr Torbergsen continued. “Some platforms can safely handle several hundred tons of sand annually, while others can only handle a small amount. Operators are encouraged to take a risk-based approach to identify where sand may be problematic and establish sufficient safeguards to ensure they maintain control over operating conditions and sand production in order to take advantage of opportunities, maybe even allowing for more sand. There is a close connection between how much oil and gas you produce and the amount of sand you need to have.”
The update also provides additional guidance on how to use erosion models in the most effective way regarding sand production and establishes a platform to look at opportunities for issues like optimizing inspections, which are important to subsea facilities and maximizing production rates, Mr Torbergsen said.

Enhancing slotted liners
Improved application of long-used methods is also delivering results in the onshore sector. RGL Reservoir Management, a Calgary-based provider of sand control, flow distribution, custom thermal completions and downhole tool manufacturing, has enhanced one of the oldest tools of the trade – slotted liners – for the Canadian oil sands and other heavy oil/unconsolidated sand formations.
The company’s seamed slotted liner (SSL), with a self-cleaning profile that reduces slot plugging, is used extensively in pad drilling-style steam assisted gravity drainage (SAGD) wells and cyclic steam stimulation (CSS) wells in Canada’s bitumen-rich, unconsolidated oil sands and heavy oil formations in the Middle East, Latin America and Africa, as well as coalbed methane wells. SAGD and CSS involve the injection of steam to reduce viscosity so the oil can more easily flow through the unconsolidated sands. In Canada, horizontal CSS wells can extend as far as 7,382 ft (2,250 m).
“We have taken a proven technology and greatly improved on it,” said Brent Fermaniuk, Executive Vice President of Business Development for RGL Reservoir Management. “Advances and better quality control in slotted liner technology have come with the recognition that we need to understand the reservoir and how it interacts with the sand control medium being used and the operational conditions downhole.”
The SSL can be tailored for each reservoir based on the operator’s objectives, the sand control requirements downhole, sand particle size distribution in the reservoir and operating conditions, Mr Fermaniuk explained. The design also takes into account the type of fluid and the amount of fluid the well produces, as well as potential corrosion or abrasion issues.
“The addition of steam in SAGD wells changes the reservoir, especially regarding how it will flow the heavy oil,” he said. “In Canada, the oil viscosity is higher, into the millions of cPs (centipoise), than that of the unconsolidated sand formations in the Middle East, so the thermal energy required to reduce the viscosity is less in the Middle East. The sand in the Middle East can be a little cleaner, with less problematic clay. In this case, sand control may be easier, depending on the well design and operational challenges.” Gravel packs can be used in conjunction with the SSL. However, they are generally unnecessary in low-flowing, heavy oil conditions, he noted.
In November 2014, RGL Reservoir Management introduced the proSLOT coated slotted liner (CSL) for harsh conditions, such as corrosive hydrogen sulfide (sour gas/H2S) and carbon dioxide (CO2), and temperatures up to 275°C (527°F), that commonly occur when injecting steam, heat and water in SAGD wells. The proSLOT properties are being further developed to withstand downhole temperatures up to 330°C (626°F), as is common in CSS applications.
The coating is metal-bonded to the pipe itself to prevent corrosion, abrasion, scale and clay build-up and the potential for erosion from the steam breakthrough and can be applied in various thicknesses. The CSL is in field tests with multiple operators in Alberta and is expected to be fully commercialized in 2016. The company is also working on developing slotted liners and other downhole tools for extreme temperature conditions as high 750° (1,382°F).
Wrapped punch slot screen
An alternative to slotted liners in Canada’s oil sands and heavy-oil reservoirs are wire-wrapped sand control screens, developed in the 1970s, which separate the filtration medium and the body of the screen itself, according to Transmer Energy’s Mr Zhang. “The base pipe of the wire wrapped screen is designed with evenly distributed holes to improve performance under stress. The wire of the screen in the filtration medium is made of stainless steel, which improves resistance to corrosion. The mechanism provides reliable, stable sand control for eight to 10 years.” The cross-section of the wire is trapezoidal, with gaps between wires narrow at the screen surface and wider at the interior for a greater flow area, he continued. The screen is also self-cleaning to prevent plugging.
In late 2014, Transmer introduced the wrapped punch slot (WPS) screen structure, consisting of a perforated base pipe and a stainless steel filtration jacket with a wrapped punch slot jacket and backup ring. The filtration jacket with the punched slot is welded onto the base pipe through the support ring, creating a barrier for formation sand encroachment, while enabling the fluid to flow into the screen through the spaces between the punched slots.
The WPS screen, which has been installed on two pilot SAGD oil sands wells for Canadian Natural Resources in Alberta, combines the advantages of slotted liners and wire wrapped screens, Mr Zhang noted. “Like the wire wrapped screen, the WPS structure separates the filtration medium from the screen body. The use of stainless steel also provides good anti-corrosion capability.” The slot width ranges from 0.20 to 1 mm, matching formation sand in various particle sizes. The integral strength of the base pipe is 2-3% less than that of standard casing or tubing to withstand formation collapse or deformation. DC
PetroGuard is a registered mark of Halliburton. ProSLOT is a trademarked term of RGL Reservoir Management. WPS is a trademarked term of Transmer Energy Services.