Rig injury spurs collaborative development of elevator strap for pipe laydown operations
Project brought together contractor, manufacturer, distributor along with input from field employees
By Tim Callais, Sidewinder Drilling; Paul Liberato, Billy Pugh; and Mike Bienvenu, Dooley Tackaberry
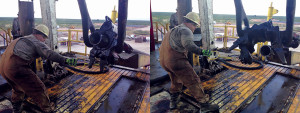
The oil and gas industry has a history of collaboration between organizations, including operators, contractors, manufacturers and distributors, in efforts to continuously improve efficiency and safety. Incidents are often triggers that lead to this type of collaboration. This article highlights an example where an incident led to a drilling contractor, manufacturer and distributor to work together to design, produce and put in place a tool that will greatly reduce the chances of similar incidents reoccurring and, thus, improve safety on the job.
The incident occurred in April on a Sidewinder Drilling rig in Oklahoma during a routine operation. It was 9:30 p.m., and the crews were pulling out of the hole and laying down drill pipe at the end of the well. The drill pipe elevators were fitted with a piece of rope approximately 3 ft in length for the purpose of tripping the elevators open. There were scattered thunderstorms at the time with gusty winds and occasional rain and hail. The rig is equipped with a top drive with a link tilt system and a hydraulic catwalk machine.
After breaking one of the connections in the rotary table, the driller picked up on the joint, and the floormen pushed the pin end of the joint in the trough of the catwalk. The driller then started to lower the joint into the trough. After lowering the joint approximately 8 ft, the elevators tripped open, causing the joint to fall into the trough, bounce up over the V-door post and fall to the rig floor between the V-door post and stands of pipe racked back in the derrick. The floorman was standing near the setback area and was struck by the joint of drill pipe, resulting in a restricted work case injury.
An investigation revealed that the wind caused the rope, which was tied to the elevator, to be blown between the rotary hose and top drive service loop and become trapped between them. As the driller lowered the joint, the drape in the hose and service loop moved away from well center, applying tension to the rope. This eventually tripped the elevator open, which allowed the joint to fall.
It has been an accepted practice in the drilling industry to use ropes on elevators for the purpose of tripping them open while laying down drill pipe. The length and configuration of the rope varies widely from company to company and often from rig to rig.
As a result of the incident, Sidewinder began searching for an alternative to ropes as a means of tripping the elevators open for this task. During this search, the company found that a casing company employee had constructed some homemade straps out of old fall protection lanyards. He offered one of the straps to the crews on a Sidewinder rig. The company’s risk assessment matrix and MOC process were used and determined it was safe to proceed with testing it on the contractor’s elevators. The general concept appeared to be a good starting point for an alternative to ropes.
Sidewinder created a drawing of this concept with some modifications and contacted Billy Pugh Co and Dooley Tackaberry for assistance with designing and manufacturing a prototype for testing on the rigs. The first prototype, which was a strap with flexible loop style handle and swivel snap hook, was sent to the field for testing. Once feedback came in from the rig, Sidewinder and Dooley Tackaberry reviewed the findings. The information in the report was then sent to Billy Pugh for modifications, and a second prototype was assembled for testing. The new design included a strap with large plastic ring and swivel snap hook.
After the second prototype was sent to the field for additional testing, rig employees provided additional feedback, and more modifications were suggested. The third prototype consisted of a strap and a rigid metal ring and rigid snap hook.
With one more minor “adjustment,” again based on surveying employees in the field, a fourth and final design was developed. The final design change was simply to add a stronger metal ring for strength and durability of the device. This new safety product has ultimately become Part Number ELS-1A and is the standard elevator strap for use on all Sidewinder rigs.
Sidewinder’s operating procedures have been revised to include the use of the elevator strap for all drill pipe laydown operations. Ropes are no longer allowed on elevators.
Benefits of the tool include:
• The short strap greatly reduces the chances of momentum or wind causing it to hang up in the service loop;
• The ring on the end of the strap allows the elevators to be tripped open with one hand;
• Using a ring instead of a loop in the strap reduces the chances of the strap cinching up on a person’s hand; and
• The safety hook allows for quick and secure attachment (no knots required).
In conclusion, the collaboration among Sidewinder, Dooley Tackaberry and Billy Pugh was a great example of bringing together the best resources for a common goal. By creating this new product – where employees in the field had the majority of the input in its creation – there will be multiple benefits. First, it creates a safer work environment. Second, it demonstrates to employees that their input is critical. Third, it shows that the company takes safety on the rigs very seriously. The goal is to reduce incidents to zero, and collaborations like this fit this goal and Sidewinder’s culture perfectly.