Offshore drilling evolves with closed-loop controls, MPD, vibration mitigation
Innovations in digital systems, riser joint design and downhole tools being adopted in offshore drilling projects to reduce NPT and cost
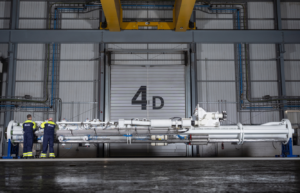
By Stephen Whitfield, Senior Editor
Digitalization and automation have become critical developments in offshore drilling in recent years, as OEMs work with operators and drillers to develop technologies that can improve rig operations. But even as digital software and apps are taking greater precedence in the tech space, advanced hardware and their associated systems are also primed to deliver time savings, performance boosts and safety improvements.
One area that looks to define the offshore space in the coming years is managed pressure drilling (MPD), an adaptive drilling process used to precisely control the bottomhole pressure. As drillers and operators continue to work in more challenging offshore basins with narrow pressure windows, these systems will likely continue to grow their presence on offshore rigs. For their part, third-party manufacturers are already delivering MPD systems with easier installation and more operational efficiency.
A simplified design of the riser joint, for instance, is a key part of Oil States International’s (OSI) recently released MPD/Riser Gas Handling (RGH) system. The company says the joint can help significantly reduce nonproductive time (NPT) during installation, furthering its aim to streamline MPD adoption.
“We see MPD as a growing requirement for more difficult wells,” said Garry Stephen, Group VP – UK and Asia at OSI. “It’s become more of a standard practice for the customers we’re talking to. They’re intending to put MPD systems on all their drilling vessels, semisubs and drillships. So we’ve focused on developing a system that can help make that process more efficient.”
Some offshore operators are also finding value in adopting technologies that had primarily been used for onshore wells previously. Neo Oiltools’ Neotork vibration mitigation tool, for example, had seen increased use in several onshore basins over the past three years before being deployed recently for an operator working offshore Thailand; significant increases in ROP were achieved in the project.
“If Neotork is minimizing vibrations, the operator doesn’t have to pull out of the ground due to potential failures. If we can stay downhole because we don’t have failures, we can drill faster, and time is valuable,” said Robert Borne, CEO of Neo Oiltools. “That gives the operator options: Do I want to drill the same number of wells faster, or can I potentially drill more wells with my current budget or current time allocation? There are opportunity costs in everything.”
Even as physical tools redefine the offshore space, new frontiers continue to be pushed in the digital realm. Last year, Halliburton and Sekal, a provider of digital systems for drilling, partnered with Equinor to deploy the first automated on-bottom drilling systems with the integration of LOGIX automation and remote operations, Sekal’s Drilltronics and the automation control system of a rig in the North Sea.
As operators and drillers increase the use of third-party digital systems on the rig, ensuring that all systems can effectively communicate with one another has become more important. A key component of the Halliburton/Sekal partnership is the use of an orchestration platform that ensures various systems on the rig can easily collaborate on making optimal decisions given the downhole data available.
“Interoperability is extremely important,” said Moray Laing, Director of Rig Systems and Automation for Digital Well Construction at Halliburton. “But, if you provide interoperability without orchestration, which system is in charge? If you give everybody the ability to drive the boat, who drives the boat? You need an orchestration system to resolve that. It helps us to agree on the data we’re getting from different systems, so we have definitions and defined decision-making.”
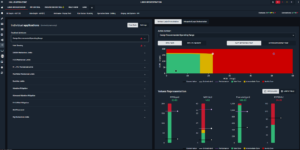
Ensuring interoperability of automated systems
Halliburton’s digital well construction software, LOGIX, played a crucial role in a North Sea well with Equinor. LOGIX includes well placement, integrity, steering controls and collision avoidance. It also features an autonomous drilling platform and acts as a propeller of all LOGIX components, running them concurrently and analyzing downhole data in real time through machine learning algorithms.
Halliburton’s LOGIX Orchestration capability was the critical component that enabled all of the services to run concurrently in real time with minimal human interaction, and provide a combined set of instructions to the rig process automation system to close the loop between subsurface and surface automation into a single system with combined objectives.
Last year, the Halliburton/Sekal partnership delivered a well for Equinor on the Norwegian Continental Shelf with an integrated closed-loop control solution. This solution orchestrated autonomous directional drilling with automated wellbore hydraulics and dynamic surface rig equipment control.
The solution developed for Equinor used the LOGIX platform to integrate several specifications – the well plan specifications, the well placement requirements, vibration mitigation and hole-cleaning optimization – with Sekal’s automated procedures and dynamic safeguards. The integration of these systems allowed Equinor to optimize drilling parameters in real time and achieve precise well placement through real-time advanced models of subsurface, wellbore fluid and pressure systems.
Mr Laing described the integration as a delicate balance, in real time, of systems that operate at differing levels of fidelity. Some systems operate at intervals of less than one second, while others may only provide updates in batches every 15 minutes. The key capability provided by the LOGIX Orchestration software is the ability to effectively automate the management of this from both downhole and surface systems.
This capability made LOGIX a key component for the integration, as it enabled interoperability with the engineering system and the drilling process control layer. Mr Laing said the orchestration software ensures that the operational needs of all systems are effectively managed into a single set of operational instructions for automation.
“Instead of having three main chefs cooking different dinners, we can have one chef – the orchestrator – assisted by multiple sous chefs – the applications – providing the individual ingredients that go into that dinner,” Mr Laing said.
For the North Sea well, Equinor’s objective was to reliably and consistently automate on-bottom automation to increase the efficiency of drilling operations. During deployment, the system was initially run in an advisory mode, making recommendations to the driller as the management of change process between the system and driller was completed. Once all critical metrics for the system operation were met, the system was then activated by the driller and went into active mode, where the system acted autonomously.
The system has proven to be successful in meeting all the initial metrics and is now running on its third well, with additional deployments being planned for other regions. Halliburton plans to publish a detailed analysis of the performance outcomes from these operations at a later date.
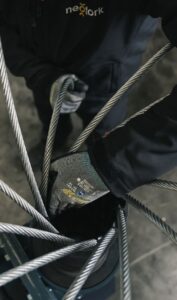
Reducing vibration downhole
While the Neotork anti-vibration tool has been around for nearly a decade and was designed to be used in both onshore and offshore settings, it only started seeing more widespread use in the past couple of years and mostly in onshore environments. Then in Q4 2024, the tool saw further expansion with an offshore deployment in the Bay of Thailand.
In that mature well project, the tool helped an operator eliminate downhole tool failures and improve ROP by more than 30%. The project has become a springboard for the company to build a larger offshore portfolio.
“Over the last year, we’ve made a big push to demonstrate Neotork’s viability and impact offshore. We’ve had a lot of good conversations with operators about the challenges they’re facing in exploration and development wells, and we’re confident we can help overcome those challenges and expect to see Neotork increasingly used in offshore applications this year,” Mr Borne said.
The tool uses cables guided around an internal mandrel and a spring pack to respond to torque changes. Once downhole torque exceeds a preset limit, a system of disc springs and steel cables automatically contracts to reduce the bit depth of cut. The excess torque stored in the system is slowly released as the drilling structure drills off. The bit remains engaged in the formation at all times so that drilling is uninterrupted.
“We mitigate all types of vibrations downhole, axially, horizontally, laterally through depth-of-cut management. When we reduce vibrations, we keep the drill bit from failing or becoming dull or slowing down the drilling,” Mr Borne said. “We help protect the downhole tools and the BHA from failure or nonproductive time, having to come out of hole because they break due to vibrations or drilling dysfunctions. Reduced vibrations means you can drill longer between required maintenance on those tools.”
The work in the Bay of Thailand came through an international oil company (IOC) that had been using the Neotork tool on its US unconventional wells for the past three years. The IOC had four offset wells that it planned to drill on a mature basin in the Bay of Thailand. Though it had successfully drilled thousands of wells in that basin over the past couple of decades, it recently began drilling in an extremely high-pressure field that was leading to severe vibration issues and multiple tool failures. On average, Mr Borne estimated, the operator had been using one bottomhole assembly per well on this field.
“The Bay of Thailand is a very high-pressure environment,” he explained. “The operator needed to be productive and safe and needed to find a way to keep from having to pull out of the hole to replace failed tools. Moreover, they wanted to drill longer between maintenance cycles – you can imagine the cost every time you have to put tools on boats, go back to port and import parts and pieces for maintenance and refurbishment.”
The NeoTork tool was used initially on a trial basis on four shallow-water offset wells in the field; the IOC wanted to see if it could drill more than one well without having to replace the BHA, which had become customary for the operation.
Once the tool was deployed, the operator managed to drill all four offsets with a single BHA and no bit trips. “When you eliminate tool failures and bit failures, and you can reuse your tools well within the limits and parameters of your maintenance cycles, that is a huge win,” Mr Borne noted.
Additionally, the operator saw a 39% increase in average ROP for the four offset wells compared with the historical average seen on wells drilled in the same field.
“ROP increases aren’t necessarily a surprise to us, because we know that if you can minimize vibrations, you’re drilling a smoother wellbore and keeping more energy on the bit. If you have proper depth-of-cut management, you’re going to drill faster, evidenced by that significant increase,” Mr Borne added.
Since completion of the trial in late 2024, the operator has agreed to deploy the NeoTork on all 120 of the remaining wells it plans to drill in the same field.
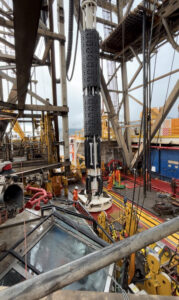
Integrated MPD system
As MPD systems continue to become more commonplace offshore, third-party tech developers and OEMs are looking at tools that can help streamline some of the trouble spots that come with installing and maintaining these systems. These tools can help save costs, reduce NPT and improve safety.
One such development came out in 2022, when OSI introduced an integrated MPD/RGH system that is now being used in several offshore markets around the world, including Australia, Brazil and soon in the US Gulf of Mexico and the Norwegian North Sea.
Mr Stephen said the MPD/RGH system deviates from conventional MPD system designs. In conventional designs, it is necessary to disconnect the lower marine riser package (LMRP) to perform maintenance. This requires pulling the riser joint to surface, creating significant NPT. OSI’s system features an integrated riser joint that is fitted with twin retrievable stripper packers and bearing assembly.
This makes it the first riser system completely serviceable from the well’s center. The stripper packers are run and retrieved by the drill pipe tool, removing the need to pull the joint from the string or return onshore to replace the annular seals. Further, the OSI joint is approximately half the length and weight of a conventional riser joint, which also reduces the time that’s needed to rig-up.
“The problem area with conventional MPD systems has always been the installation of the MPD joint itself,” Mr Stephen explained. “We were taking existing designs that were used on surface wells with large flanges and heavy equipment, and we were trying to install that equipment in a moonpool underneath the drill floor. That is very difficult to do, and it could take as much as two days to install this equipment. That’s why we focused on making a system that’s easy to handle – we can install a joint in less than seven hours now.”
The riser joint’s instrumentation system is also integrated with each riser function to relay information to the surface. Its electro-hydraulic controls are connected to the joint through a hands-free, pull-in bridle system, allowing remote joint plug-in without manual intervention. This functionality can have a significant impact on reducing NPT and improving safety.
“With this pull-in bridle, all the connections are already made up,” Mr Stephen said. “By literally pulling a wire, we pull all these connections that are made up to the joint itself. It doesn’t require people in all these spots where we could see bottlenecks, making up connections in the moonpool area. We don’t need a bunch of complex robots to do this process either. It’s a design that allows this process to be simpler and safer.”
While OSI’s MPD system can be integrated with existing risers, it can also be combined with the company’s automated Merlin marine drilling riser. The riser features a two-part connector with no moving parts that uses a series of non-helical teeth. Being non-helical, the connector cannot back-off while in service.
The riser system also includes an automated spider, which ensures that the joints are correctly aligned prior to stabbing, reducing the potential for damage in the auxiliary line. Once the joint has been made, the clamp reverse-pushes with pre-set load, confirming the joint is correctly made up. Automation of the spider allows a run/pull speed of 10-12 joints per hour, according to OSI. Laboratory testing on the Merlin connector showed an average connection makeup time of 42 seconds, while conventional riser connectors ranged between 5 to 10 minutes.
“The thing with Merlin is that there’s no bolts on the system. It’s just a pin and box design. It’s not a threaded design like we see with a lot of risers,” Mr Stephen said. “We apply pressure between the pin and box, which effectively snaps that connection together. That’s how you get these fast connection times.” DC