Automated fluids monitoring helping to unlock value and efficiency in deepwater drilling
Advances in real-time fluid measurement deliver greater certainty, safety and efficiency in Norwegian Continental Shelf wells
By Jon Bartholomew and Charles Thompson Jr, Baker Hughes
The pace of deepwater exploration and production has advanced significantly in the past few decades, driven by the growing global demand for hydrocarbons and dwindling onshore and shallow-water reserves. However, developing deepwater subsea reservoirs is a high-cost, high-risk and lengthy process, necessitating technological advancements to ensure drilling operations safely reach target depth in the shortest time and at the lowest cost.
Drilling fluids play a crucial role in deepwater drilling, acting as the primary barrier against well control incidents. Fluid design and application are essential for optimizing drilling operations while addressing challenges such as narrow pore/fracture pressure gradient windows, wellbore instability, gas hydrate formation, lost circulation, formation damage, stuck pipe and cuttings transport. Safety and environmental considerations further emphasize the need for effective fluid management.
Key fluid properties, particularly density and rheology, are crucial to maintaining well integrity and optimizing drilling efficiency. Any deviation in these properties can lead to operational risks, increased costs and potential nonproductive time. The importance of continuous and precise monitoring of drilling fluids in the deepwater environment cannot be overstated.
Manual measurements limit optimization opportunities
Traditionally, drilling fluid monitoring and control have been “hands-on.” A fluid engineer manually collects and analyzes mud samples every four to six hours. If the analysis finds discrepancies in density or viscosity, the fluid composition is adjusted to bring these properties back into specification.
This process has several limitations:
Manual sampling requires engineer training to help ensure consistent and repeatable results. Even then, sampling variance persists depending on the individual taking the samples and measuring the fluid.
The sampling process introduces risks by exposing engineers to potentially hazardous materials and raising the potential for spills and accidents.
Given the limited sampling frequency and long intervals between measurements, critical fluid property changes affecting well stability or drilling efficiency may go undetected for hours.
Because real-time hydraulic calculations and drilling optimization software rely on periodic fluid property measurements as inputs, undetected drifts in these properties can lead to calculation errors.
These challenges highlight the need for a more efficient, accurate and continuous fluid monitoring solution to improve drilling performance and safety in deepwater.
Operators and service companies are increasingly adopting automated fluid monitoring (AFM) systems to provide continuous, real-time fluid property measurements and help minimize downtime, mitigate risks and optimize drilling performance.
This article reviews one such system, the i-Trak Automated Fluid Monitoring unit, which helped an operator on the Norwegian Continental Shelf of the North Sea collect real-time data to enhance the efficiency of daily deepwater drilling operations.
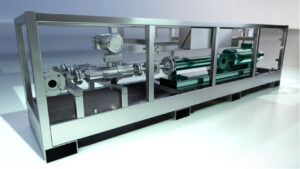
Enhancing safety and efficiency with automated measurements
Baker Hughes needed to implement automated fluid measurements to fulfill the operator’s contract requirements regarding fluid quality, increased sampling intervals and overall improved drilling safety and efficiency.
The AFM system selected for the operator’s drilling program is a fully contained module that takes continuous fluid property measurements of a flow stream diverted from the primary fluid flow path.
The system includes a pipe rheometer with two sets of differential pressure (DP) sensors to measure the pressure loss inside the straight section of the rheometer. It also includes a Coriolis meter to measure fluid density and flow data, replacing conventional mud balance measurements. Additional features include temperature and pressure sensors and a dedicated pump that circulates drilling fluid through the module.
Traditional Couette-type viscometers and mud balances, which have remained unchanged for decades, require manual operation and are prone to human error. By automating these measurements in the mud system, the AFM system significantly reduces errors and improves measurement accuracy and consistency.
The AFM module also includes two systems to minimize the risk of overpressure — a primary automated shutdown software solution and a secondary rupture disc mounted after the pump.
The full-open borehole design allows for the free flow of fluid and lost-circulation materials (LCMs) without the risk of plugging or the need for additional maintenance and personnel on-site.
Unlike Couette viscometers, the system provides accurate measurements and a truer picture of the fluid entering the wellbore, even with a high concentration of LCM. The system is also unique in that it measures fluid and LCM in situ, thus reducing the number of additional measurement steps required.
The AFM system reports fluid rheology, density and temperature measurements in 10-minute cycles, taking up to eight shear rate and 16 pressure readings per cycle. All data readings adhere to API RP 13B-1, an industry standard for drilling fluid analysis. This ensures faster implementation of the data into existing drilling systems.
The readings are automatically analyzed and transmitted to remotely stationed fluid experts, who can verify the data at any time by comparing it with manual rheology and mud weight data recorded by the rig crew. The experts use the verified data to engineer any necessary adjustments to the fluid system.
Once the operator has reviewed and approved these recommended adjustments, rigsite personnel implement the changes. This process detects the slightest fluid changes with greater precision and in a fraction of the time of manual methods, helping to maintain optimal drilling safety and performance.
Avoiding downtime with rapid barite sag detection
The AFM system has helped the operator identify mud weight changes early and avoid other remediation measures that add time, cost and complexity.
The system proved particularly helpful in overcoming significant barite sagging challenges while drilling wells with an invert emulsion fluid (IEF) system. During barite sag, the barite particles added as a weighting agent to increase fluid density settle out and accumulate at the bottom of the wellbore. As a result, the drilling fluid at the bottom of the hole becomes much denser than the fluid at the top, which raises the risk of poor well control, stuck pipe and formation blockage leading to lost circulation.
While the IEF’s rheology remained within specifications during dynamic drilling operations, prolonged static conditions at high downhole temperatures and pressures raised the risk of barite dropping out of the IEF.
Prior to implementing the AFM service, rig personnel analyzed fluid rheology and density every six hours. This might have caused barite sag to progress to the point that lengthy fluid recovery actions and hours of circulation time were required.
The AFM system’s real-time monitoring and automated analysis gave the rig crew and onshore fluids experts a faster and far earlier indication of barite sagging. The system measured and continuously streamed live fluid weight data while updating the rheological data in 10-minute intervals, a significant time savings compared with conventional measurements. As a result, the system identified the onset of a barite sag issue within 30 minutes of its first occurrence.
The real-time data was delivered to key wellsite personnel on the drilling job, fluid experts stationed remotely, and other support personnel in the onshore office. These teams jointly analyzed the results and discussed the optimal course of remedial action. By treating the fluid early to bring its density and rheology back into spec, the fluids team avoided the lengthy circulation process and allowed drilling to continue without issue.
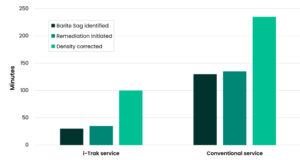
Providing optimization benefits beyond fluids
In addition to affording real-time oversight from remote fluids engineers, the AFM system’s continuous fluid measurements can be incorporated into the rig’s drilling automation service. Such services aggregate real-time surface and downhole data to populate hybrid physics-based and data-driven models. These models are combined with automated standardized operating procedures and checklists to automatically control key drilling activities.
Fluids measurements from the AFM service can play a critical role by providing automated analysis and advice on determining optimal tripping speeds, ensuring proper pressure control, maintaining adequate hole cleaning, and mitigating torque and drag.
Conclusions
The automated fluid monitoring (AFM) system discussed offers significant benefits for deepwater drilling operations. By providing continuous, real-time measurements of key fluid properties such as density and rheology, it enhances drilling safety and efficiency. It reduces the risks associated with manual sampling, such as exposure to hazardous materials and human error, and ensures consistent and accurate fluid measurements. The system’s ability to detect issues like barite sag early allows for timely corrective actions, minimizing downtime and maintaining optimal drilling performance. Overall, the AFM system represents a valuable advancement in drilling technology, enabling operators to drill wells faster, safer and smarter. DC