Swellable packers qualified for Valhall
North Sea field redevelopment drives design of new high-pressure oil-swelling packer
By Jeroen Nijhof, BP Norge; Tom Rune Koløy and Kristian Andersen, Halliburton
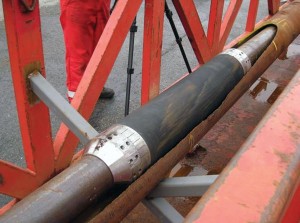
To redevelop the Valhall Field in the North Sea to enable continued production until 2050, BP Norge is increasing the reservoir pressure by waterflooding. To protect the field from associated damage and minimize cost in the next phase of production, different strategies were evaluated, including the application of swellable packers (SEPs).
The operator wanted a zonal-isolation method that would leave the annulus void of cement. All producing wells on Valhall are stimulated with proppant fracs; hence, the open-hole zonal isolation between the zones must be capable of withstanding high differential pressure during stimulation and in case of screen-out. Oil-swelling SEPs were identified as a potential solution.
Full-scale testing was done under the conditions that would likely be experienced in the field.
Additionally, to reduce the uncertainties associated with water injection and mitigate their consequences, a decision was made to include capabilities to monitor flow between reservoirs and wells and to enable control of this flow. This led to the development and qualification of high differential pressure (∆P) SEPs for a particular application in prop fracture stimulation in Valhall production wells.
Qualification
The requirements in Valhall call for a maximum differential pressure of 10,000 psi for propped fracturing across the SEPs. In addition, the SEPs have to withstand a long-term differential pressure of 4,000 psi during production. The SEPs would require a high-pressure sealing capacity and be capable of withstanding a wide temperature variation.
During the test, a critical requirement was to establish the pressure at which the oil-swellable packer would fail and determine how it would react to the type of temperature cycling that would be experienced.
Centralizers would be used to ensure an even swell in the packer when deployed in the horizontal well section and to provide stand-off for the packer while running in hole.
Solids-laden, oil-based mud would be used to drill the reservoir section, and the SEP would use this as fuel to swell and provide the high-pressure seal.
An 8.5-in. open hole is typically drilled through the reservoir, followed by the installation of a 5.5-in. liner. The SEP was to be designed with the same ID as the 5.5-in. pipe to seal inside the 8.5-in. open hole. Following are the details of the conditions that prevailed.
Producer wells
• Maximum differential pressure for propped fracturing is 10,000 psi (tip screen-out: 12,000 psi to 13,000 psi at liner with reservoir pressure of 3,000 psi).
• Maximum long-term differential pressure is 4,000 psi (6,000-psi injection finger with 2,000-psi bottomhole foundation pressure).
Injection wells
• Maximum differential pressure for hydraulic unpropped fractures is 3,000 psi to 4,000 psi.
• Long-term differential pressure is similar, with intra-zonal pressure of 3,000 psi to 4,000 psi.
General
• Reservoir pressure is 2,700 psi to 4,000 psi.
• Reservoir temperature is 95ºC, bubble point 3,350 psi, gas/oil ration is 914 standard cu ft per stock tank barrel.
• Fracture fluid temperature is 20ºC.
• The hole drilled is 8.5-in., but the SEPs need to cope with potential washouts of up to 9.5 in.
Other design considerations for open-hole zonal isolation are:
• Frac tip screen-out pressure;
• Strength of chalk formation;
• Open-hole/run-in-hole constraints; and
• Acceptable leak rates past zonal isolation.
Suitability
When designing SEPs for dynamic downhole conditions, it is critical that the SEP be designed with the capability to hold the expected differential pressure, considering the cool-down experienced during stimulation or injection.
Compared with mechanical packers that will be ready for fracking after they have been set, SEPs require time to swell and to build up internal swelling pressure before they are ready for fracturing to commence. Depending on the design and required differential pressure, this can range from less than a day up to weeks.
SEPs can be designed with a continuous 30-ft long element, ensuring optimal coverage in fractured and washed-out formations. Long elements also offer additional anchoring forces over a shorter packer to prevent liner movement in dynamic downhole conditions.
Further, SEPs remain flexible for the life of the wells, being able to swell in the wellbore fluids if washouts or borehole breakouts occur in the packer-setting area over the life of the well.
In stimulation applications, SEPs also exert minimal stress on the borehole during setting. Exerting significantly higher stresses on the borehole during setting can result in fracture initiation points near the open-hole packer.
Elastomer, packer design
Various types of swelling elastomers have been developed for different applications and downhole conditions. Elastomers that swell in either hydrocarbon or water are dominant, but some types will swell in both media. During well planning, the well, formation and fluid properties are evaluated to select the appropriate elastomers and the appropriate SEP design.
Two main categories of SEPs exist – bonded-to-pipe packers and slip-on-type packers.
On bonded-to-pipe packers, the swellable elastomer element is chemically bonded onto casing or tubing that will run in the well. For slip-on-type SEPs, the swellable elastomer element is manufactured as a sleeve that can be installed on the casing/tubing in the pipe yard or at the rig site. Bonded-to-pipe packers typically are used where higher differential pressure is expected or where there is a need for a long sealing element because of hole/formation conditions.
Based on testing and field experience, metal end rings are used on all SEPs on both sides of the swelling elastomer element to protect, centralize and guide the SEP assembly while it is run in hole. The rings also limit the extrusion gap available to the swelling element of a set SEP, for increased differential pressure capability.
Several tests had been conducted to qualify an SEP to 10,000 psi for the Valhall application, but none had been successful. A new type of SEP design was developed featuring a proprietary end-ring system and special elastomers to be deployed against the formation – resulting in an SEP system where the swelling elastomer is confined between the backup rings. This increases the working envelope of the SEP.
Based on in-house testing of the new design, a packer design was created to hold the required 10,000 psi during fracturing stimulation operations with the associated temperature changes. It was built on 5.5-in. base pipe with a 5 meter-long rubber element and an OD of 8.2 in.
As this new design had been subjected to only limited testing, there was a risk of packer failure early in the test program. To minimize this risk, two packers were tested in series. The test was set up to perform the pressure test across the individual packers, as well as the whole two-packer system.
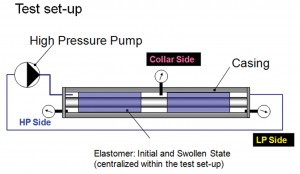
Test setup
A custom-built test fixture was designed to be 690 bar/10,000 psi (Figure 2).
The test was set up with two 5-meter swellable packers in series. Two high-pressure pumps were connected to the test fixture; one at the HP side and one between the packers. The cooling was performed by flowing water through the base pipe from the HP side to LP side.
Three pressure transducers monitored the pressure while external and internal temperature sensors controlled the temperature. All transducers and sensors were connected to a real-time logging system.
Cooling effect on SEPs
Pressure has always been one of the main parameters for any SEP design, but for a stimulation application, the impact of temperature on the differential-pressure behavior of the SEP must be taken into account. Proper estimation or description of the downhole conditions, therefore, is crucial to the design. As with any material, the swellable elastomer element of the SEP will contract during a drop in temperature.
The thermal expansion/contraction of the elastomer is approximately 10 times larger than the coefficient for steel. This means that, with increasing temperature drop, contraction effects will be more severe. The contraction will lead to a drop in internal element pressure; ultimately, it will result in a physical shrinkage, and the pressure seal will be lost.
To be able to link the temperature drop to SEP performance, laboratory and full-scale tests have been performed. Results show that an SEP can handle a certain temperature drop if given sufficient time to swell. However, the differential pressure holding capacity is reduced if the temperature drop is too large to handle at that particular point in time.
From the experiments, it is possible to quantify the additional amount of time required to allow the SEP to build up sufficient internal pressure so that the temperature drop does not affect the performance of the SEP. Therefore, it is critical to use accurate input numbers and a realistic model to predict the temperature drop that the packer will experience.
The engineering/service company developed an SEP design simulator to accurately predict the working envelope of SEPs in hydraulic fracturing and injection applications.
In these tests, two approaches were made to simulate hydraulic fracturing:
• Cool-down based on steady-state heat conduction. After infinite time of pumping, the temperature in the SEP will reach a steady state regardless of the amount of fluid pumped. This is based on constant heating from the reservoir and cooling from the frac fluid inside the tubing.
• Full cool-down of the packer and reservoir. Temperature dropping from 95°C to 20°C, where 20°C is the estimated surface temperature of the fracturing fluid.
Piston effect
During the testing in tandem of the two packers, a piston effect was seen. As pressure increased on the HP side, the elastomeric element on the first SEP flexed toward the collar. This led to a pressure build-up between the two SEPs inside the autoclaves. On the pressure charts, this can look like a leakage over the first SEP.
Test data
The two packers were exposed to more than 65 days of testing – to extensive temperature cycling, high differential pressure and rapid bleed-off, both controlled and uncontrolled. The packers did not fail. At 64°C and 95°C static temperatures, 690 bar/10,000 psi differential pressure was achieved on each of the single 5-meter packers.
Swelling of the packers
The swelling of the packers commenced on 14 January, when oil-based mud was pumped into the autoclave and the heating was switched on at 95°C. The mud circulated for the first 48 hours to simulate the running-in-hole operation from the LP side to the HP side. In addition, the second packer, and especially, the end ring on the LP side, was more or less centralized since the packer was fastened to the autoclave end cap. Two centralizers were used on the HP side and between each packer.
Time to seal was verified with the HP pressure pump on day three. In preparation for the test, the behavior of the packers had been estimated. Although the BP requirement of the test was achieved – 10,000-psi differential pressure capability within 45 days, the estimated 13 days to 690 bar/10,000 psi was not achieved.
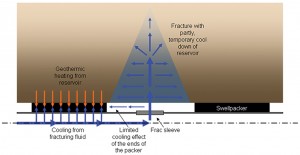
The packers were treated during the pressure build-up, meaning that pressure increases were done at a slow rate in agreement with BP. In addition, delays were experienced that resulted in a relatively slow time to reach the 10,000-psi pressure rating.
If the same trend from day three to day nine is linearly extrapolated, it will take 27 days to reach 690 bar/10,000 psi. This is a more realistic time to maximum differential pressure in these conditions.
Cool-down effect
A design methodology was established for swellable elastomer packers in fracturing operations (Figure 3) based on three main assumptions:
• Steady-state heat conduction through the rubber element;
• No cooling effects at the ends of the rubber element; and
• Tubing/liner wall is at fluid temperature.
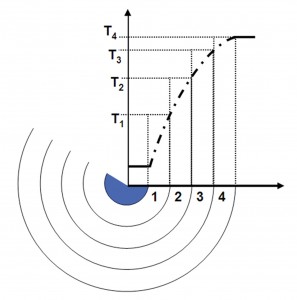
Based on the above equations and well information from Valhall, the following were calculated:
• The average rubber element temperature Tavg is 64°C; and
• The temperature drop, ΔT, is 95°C – 64°C = 31°C.
For fracturing operations where pumping times are limited to days, the cool-down effect on the formation is not significant, and the profile in Figure 4 would apply. Figure 5 shows the temperature profile through the swellable packer with the dimension used in this test during a fracturing operation. When cold fluid is injected for long intervals (for example, water-injection wells), there might be a near-wellbore cool-down effect resulting in a lower temperature at the element/wellbore (EWB) interface.
Flowing water at 6°C simulated the fracturing process for two hours from the HP side to the LP side through the 5.5-in tubing. The packer was then pressure-tested until leakage. Because of the test setup, the first packer was also exposed to cold fluid at the end of the rubber element on the HP side, resulting in a severe situation.
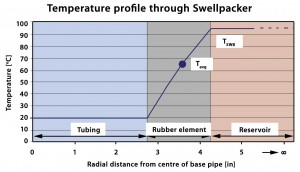
The cool-down process was repeated two times; the first time after 35 days and the second after 42 days. In the first cool-down, 280-bar differential pressure was achieved and the pressure test stopped before leakage occurred, indicating higher capability than 280 bar.
In the second test, 592-bar maximum differential pressure was achieved, and there was a small leakage to LP side. Several comments can be added:
1. After two hours, the water flow was stopped, and Clairsol NS replaced the water. The change took time, which meant the temperature in the test fixture increased before pressurizing of the packers started. The pressurizing can be seen as small drops in temperature on the internal HP side. The temperature of the Clairsol NS was about 20°C.
2. The temperature over the packers was constant at 95°C, indicating that fracturing will not influence the temperature at the EWB interface.
3. Temperatures at the internal and external high-pressure side were dropping when the water started flowing and stabilized at 15°C to 25°C.
4. Water-flow first test: 40 to 50 liters/min. Water-flow second test: 11 to 50 liters/min. The water supply in the lab during the second test was fluctuating for an unknown reason, which resulted in a higher external temperature at the HP side.
5. The temperature sensor that controlled the heating pads at the collar was changed from external to internal, from the first test to the second test. This resulted in heating on the collar and an almost zero temperature drop internally at the collar in the second test.
Full cool-down
In the full cool-down approach, it is assumed that the reservoir will obtain surface fracturing fluid temperature; i.e., 20°C. This approach is regarded as the most conservative since the swellable packer will see a larger temperature drop, from 95°C to 20°C, and therefore, it was expected that the differential pressure capacity of the packers will be lower. The main reason for this is that a larger temperature drop will induce a larger contraction of the rubber element and therefore a lower internal element pressure against the formation.
In this test, the full cool-down was simulated by lowering the temperature from 95°C to 20°C. The test fixture was then left to cool down. This process was performed two times; the first after 44 days and the second after 57 days. The first time, the test fixture was left to cool down for four days, and the second time for seven days.
From the test, it can be summarized that the first packer started to leak around 150 to 200 bar, and the second packer started to leak around 300 bar to 370 bar, stabilizing at 320 bar.
Pressure logs from the pressure testing of the second full cool-down show:
• The first packer started to leak around 150-200 bar;
• The second packer started to leak at approximately 630 bar;
• The pressure at the LP side was bled off. 690 bar was reached without leakage to the LP side. After several attempts to obtain stable pressure, a small leakage to the LP side was obtained;
• There were rubber particles in the return fluid when bleeding off pressure; and
• Obtained differential pressure was higher because of longer swelling time in combination with earlier performed temperature cycles.
Differential-pressure capacity at 64°C and 95°C
As part of the reheating step, one differential pressure test was added to gather more data from the test. The Tavg = 64°C was chosen as the test temperature.
After 690 bar/10,000 psi was reached over the total system, the pressure at the collar was bled off in steps down to zero to verify 690 bar/10,000 psi differential pressure over the first packer. Since higher differential pressure was achieved at 64°C, the cooling of the side of the packer could have had an effect. In addition, the longer swelling time will influence the results. The test was performed at day 35 and day 42 while the 64°C test was done at day 51.
During the bleed-down, it was noticed that the return fluid contained small rubber particles, also visible on the pressure log from the collar.
When the pressure on the HP side bled off, the end rings could be heard moving in the autoclave. Calculations indicated that the 9 7/8-in. casing would increase its length at maximum load (690 bar/10,000 psi) by approximately 23 mm while the 5.5-in. tubing would be compressed by approximately 15 mm. When the pressure is bled off, the casing and the tubing will relax, and the end rings will move back approximately 8 mm.
690 bar/10,000 psi was also reached when the system was reheated to 95°C. The second packer was holding more or less all the differential pressure, and after holding 690 bar over the system for a period of time, the pressure on the collar was increased. This was done to verify 690 bar differential pressure capacity over the second packer.

Differential pressure distribution
Table 1 shows the distribution of the differential pressure over the first packer, second packer and the total differential pressure over the entire system. Until the 64°C (147°F) test, the behavior of the packers was almost equal. After that point, the second packer was holding more or less the total differential pressure. This indicates that the first packer had been damaged during the 64°C test.
Overall, the first packer experienced the worst conditions during the test, during both swelling and pressure testing.
Failure mode
The two packers were exposed to 65 days of testing. They have seen:
• High differential pressure in combination with large temperature variation;
• Compression and expansion forces of packers and test autoclave during pressurizing and bleed-off – approximately 8 mm of movement. Most of the movement was seen on packer 1; and
• Rapid bleed-off.
After the 64°C/147°F test, rubber particles appeared in the return fluid when bleeding off, mainly from the HP side and collar.
To investigate the failure mode of the packers, the casing was to be split open. Two approximately 1-meter elements of the test fixture with the packers inside were split open to investigate possible mud channels between the packer OD and the ID of the casing and packer failure mode. During splitting of the second packer, the compression force in the rubber was so high that four saw blades became stuck and were broken. An angle grinder was used to cut through the test fixture and the second packer.
These observations were made:
• Packer 1 was damaged with a failure channel going through the length of the packer on the top side of the casing. The rubber element was held in place by the backup rings.
• Packer 2 was virtually undamaged. There was an indication of a failure channel on the HP side, but it did not go through to the LP side.
• A thin layer of mud was covering the inside of the 9 7/8-in. casing. No clear pressure channels were visible either on the surface of packer or the ID of the casing. The 5.5-in. tubing was still half-filled with mud through the length although the pipe had been flushed with water for several hours.
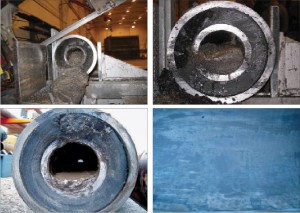
Conclusions
This test proved that the new high-pressure packer concept would be suitable for the challenging conditions at Valhall. Multiple temperature cycles were run to simulate hydraulic fracturing stimulation, and results show the packer will have high differential-pressure capacity. The test results also show that differential pressure above 10,000 psi is possible on the new design.
Parts of the casing were split open to investigate the failure mode of the packers. Although the packers did not fail in the test, the first packer had damage to the swelling elastomer element. A failure channel went through the length of the first packer, but the rubber was held in place by the new backup ring design, and the packer maintained pressure integrity. The second packer was more or less undamaged. This confirms that the design is able to hold high differential pressure even after the element is damaged.
SPE/IADC 130062, “Case History: New Swellable Elastomer Packer Design Improves Operations in 10,000-psi Differential Pressures in the Valhall Field in Norway,” was presented at the SPE/IADC Middle East Drilling Technology Conference & Exhibition, 24-26 October 2011, Muscat, Oman.