150 ksi nickel alloy materials among new innovations for sour service
Other advances include adoption of compressive stress relaxation evaluation method and capability to use 3D printing for corrosion-resistant nickel alloys
By Linda Hsieh, Editor & Publisher
To reduce well completion costs in environments with H2S, Baker Hughes is working to develop innovations that span materials, manufacturing, evaluation and testing. DC recently spoke with Darren Bane, Product Line Director, about recent and upcoming technical advances for sour service.
High-yield sour-service nickel alloy materials
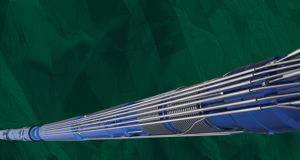
As operators continue to drill and complete wells in sour-gas environments with increasingly higher pressures and higher temperatures, the demand is also increasing for materials with higher minimum yield strengths. Over the past few decades, the highest available yield for nickel alloy materials had risen from 120 ksi to 130 ksi and finally, about 10 years ago, up to 140 ksi.
Now, Baker Hughes has partnered with its materials suppliers to develop 150 ksi sour-gas nickel alloy materials. “Over the past 10 years, as we continued to optimize what was available at 140 ksi, we realized the only option we had to go beyond that was to go to a Hastelloy type of material or a cobalt-based alloy, both of which would be extremely expensive and typically aren’t available in large bar sizes,” Mr Bane said.
By offering sour-service nickel alloy materials with minimum yield strengths of at least 150 ksi – while still complying with NACE MR 0175 – Baker Hughes believes that operators will be able to further optimize their completion operations. Higher yield allows for safety valves with smaller ODs, enabling smaller and more cost-effective casing sizes to be used. It also allows for larger IDs on the safety valves, enabling higher flow rates and more efficient production.
“Getting to 140 ksi was a really big step in the late 2000s, and now we’re able to get to 150 ksi. It means continual optimization for our customers,” Mr Bane said.
High-strength low alloy steels
In the Gulf of Mexico (GOM), liner hangers for sour service are typically manufactured using low-alloy steels with a yield strength of 110 ksi or 125 ksi. “But we realized that if we could develop a 140 ksi material, it would give us the capability of making the liner OD smaller, which would give us a more efficient cementing capability around the liner in the long run,” Mr Bane said.
To develop a C140 grade for the liner hangers in this project, Baker Hughes worked with a GOM operator to conduct corrosion testing in their specific well environment. The new material, which was just launched earlier this year, passed fit-for-purpose testing, he noted. Further, “not only did we have a smaller OD, but we had a smaller OD with higher ratings, which gave us a higher bypass area on the outside for cementing.”
The company is now working to roll out the new material across its portfolio.
Elastomeric evaluation tools
Baker Hughes is continuing to implement compressive stress relaxation (CSR) to evaluate long-term sour-gas effects on elastomeric materials. The method – which is used in industries like aerospace, automotive and medical – is slowly being adopted in oil and gas, Mr Bane said. But Baker Hughes pioneered its use a few years ago while developing packers for a high-profile deepwater GOM project. The operator needed assurance that the elastomers being used would last for 25 to 30 years, minimizing risks for costly subsea well workovers.
“CSR gives us the ability to simulate a sour environment of polymers and gives us an accelerated aging test capability that estimates material life up to 30 years,” he explained.
CSR is not a destructive test – it measures the residual sealing force and compressive modulus in a seal specimen that has been compressed over time at elevated temperatures. “It gives us a degradation evaluation of how a seal is going to perform over time, and so we can determine how the elastomer will work over 30 years using life predictive models.”
While operators are usually skeptical of this method at first, results from several deepwater projects in the past few years have begun to bring them around, Mr Bane said. Baker Hughes has also been able to corollate CSR results with finite element analyses, proving the accuracy of CSR. “For sour environments, this new evaluation technique is really an advanced method that I think will be the next phase of the industry for sour service.”
Additive manufacturing
3D printing of metals had previously been adopted only for materials to be used in non-sour environments. Materials made with additive manufacturing (AM) were not rated for sour service because H2S could induce cracking in the materials.
However, over the past year, Baker Hughes has developed additive manufacturing of corrosion-resistant (nickel) alloys, “which now lets us manufacture 3D metal components that can be evaluated against certain customer well applications for use in a sour-gas environment,” Mr Bane said.
With traditional manufacturing methods, a component may require three separate machine components to be assembled together. But with 3D printing, that component becomes just one single component. “So you eliminate two threaded connections with seals, reducing the number of parts and the number of sealing connections being placed on the tools. That eliminates leak paths and increases reliability,” Mr Bane said.
Baker Hughes has been experimenting with different geometry configurations over the past year, and now it’s starting to be able to apply the printed stainless steels to, for example, backup rings on packers.
If the packer could only be used in two casing weights previously, the new additive manufacturing backup rings will allow the packer to be used in five casing weights, Mr Bane explained. “It lets us standardize with our customers so they’re not stocking as many different packers for different casing weights. It also helps us maximize our inventory for customers, so it keeps our costs down, as well.
“When we started developing this technology about a year ago, we realized that utilizing AM nickel alloys wasn’t straightforward, since our customers had not utilized it before, particularly in aggressive environments,” he continued.
Baker Hughes has conducted sour testing of AM 718 to better define its application envelope in downhole tools. DC
This article includes reporting by DC Contributor Joshua Baethge.