MPD-enabled real-time pressure testing helps Shell improve safety in ‘conventionally undrillable wells’
Results from dynamic pressure tests during drilling enable selection of optimal strategies for safer well construction in deepwater GOM
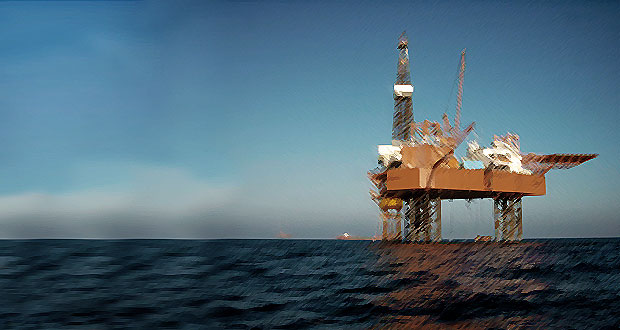
By Stephen Whitfield, Associate Editor
Shell has registered a ton of experience with managed pressure drilling (MPD) in the US Gulf of Mexico (GOM) over the past four years. Armed with 27 wells and more than 300,000 ft of hole drilled, the company believes it has set a new standard in deepwater safety by leveraging MPD, including using the technology’s capability to conduct real-time dynamic pore pressure assessments, dynamic formation integrity tests and dynamic leak-off tests.
These tests not only helped Shell with pressure management and early kick detection, but they also allowed the operator to redefine target depths while drilling, trip and kick margins, well-balancing methods and the cement design.
“Most wells where we use MPD are already challenging from a safety and economic perspective,” said Nathan Tuckwell, Wells Engineering Team Lead – Deepwater MPD at Shell. “Although the well planning process includes detailed formation pressure predictions, there are still levels of uncertainties during the actual drilling. Real-time MPD tests have been proven throughout our campaigns to improve the management of the process safety risks associated with these wells.”
Speaking at the most recent SPE/IADC Managed Pressure Drilling & Underbalanced Operations Conference in Kuala Lumpur, Mr Tuckwell outlined how two specific tests – the dynamic pore pressure test (DPPT) and a combination of the dynamic formation integrity test and dynamic leak off test (DFIT/DLOT) helped the operator to balance various GOM wells, run casing and then cement. The DFIT/DLOT is the MPD version of the more conventional formation integrity test and leak-off test.
Mr Tuckwell discussed the use of MPD, DPPT and DFIT/DLOT on a pair of wells drilled as part of a drilling campaign that began in 2018 using Transocean’s Deepwater Thalassa drillship. This was Shell’s first MPD application in the deepwater GOM for what it called “conventionally undrillable wells” – specifically, wells that could not have been drilled without incurring severe circulation losses during drilling, tripping and cementing while simultaneously elevating the risk for safety issues during the well construction process.
Key among the MPD system’s components were an annular surface pressure control system that communicates with the MPD equipment and the rig’s control system. The surface pressure control system utilizes the capabilities of a centralized, programmable automation controller with an integrated human-machine interface screen. It also allows users to run an integrated hydraulic software model that enables real-time management of the annular pressure profile and monitoring of well construction parameters.
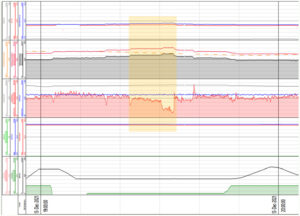
Completing hole sections safely
In his presentation, Mr Tuckwell talked about one well where the DFIT/DLOT provided real-time information that allowed the operator to determine the maximum kick intensity that the MPD system could handle without exceeding formation limits. In the 14 ¾-in. hole section, for example, Shell was able to determine the safest strategy for drilling the section, tripping out, running casing and then cementing, Mr Tuckwell said.
The test began with the MPD choke operator increasing the surface back pressure (SBP) in small increments. The flow balance behavior (flow-out vs. flow-in) and the rig active pit level were then observed. In instances where the balance was preserved and the target equivalent mud weight was not reached, the operator proceeded with a subsequent pressure increment, repeating all observations until an agreed DFIT value was reached or when a slight loss was detected. This helped to establish a DLOT point.
At that final maximum pressure stage, the reading from the pressure-while-drilling (PWD) tool was defined as the confirmed or new limit. The SBP then returned to the original value observed before the start of the test.
Before displacing the kill-weight mud into the drill pipe, Shell performed a DFIT test. That test revealed the formation was beginning to leak off and showed losses at 14.3 lb/gal – the presence of leak-off meant that a DLOT test had to be run. For that test, the well was displaced to a 14.1-lb/gal surface intensity, with the MPD system maintaining a minimum 14.1-lb/gal bottomhole equivalent circulating density (ECD).
The displacement was completed in two stages. First, the drillstring pumps were used to get the 14.1-lb/gal fluid up to the riser. After that, the displacement was finished with the boost only. The BHA was stripped out of the well with the MPD holding the SBP to offset swab. The RCD bearing assembly was retrieved, and the BHA was pulled out of hole conventionally.
The DFIT test allowed Shell to identify the point at which the losses started. This was set as the weakest point in the wellbore, providing an actual reference point that otherwise, if not spotted, could have led the operator to overdesign the balancing method for the well, inducing more losses that could have triggered unsafe conditions.
“In this case, we just stopped drilling at a certain point and ran the DFIT and DLOT. We saw that the limit was not where we thought it was, and it had actually started leaking off at a point earlier than we expected. We had to make a decision. Where are we going to set our casing? How are we going to adjust the mud weight? Can we keep drilling? We found that this was the best strategy for completing the well safely.”
Determining real-time pore pressure
Shell has also conducted several DPPTs with the same MPD system. These tests are conducted with returns through the MPD system while pumping downhole through the drillstring with slow rotation. The returns are lined up to a single pit system or a pit with the smallest possible surface area, in order to make it easier to identify and measure any changes in mud volume during the tests.
The pore pressure is determined by a real-time PWD measurement. The well is constantly measured, and the volume of any potential influx is measured by a Coriolis flow meter.
The test is performed once the bit is at depth. With the MPD system lined up, the rig mud pump section is isolated and the returns are directed to a single pit system. Once the flow rate and all other MPD and rig parameters are stable and the returns are clean, the MPD hydraulic model is calibrated to account for fluid expansion during each pressure decrease step. The SBP is reduced at small intervals, and all MPD and rig parameters are recorded at each interval.
These pressure decreases continue toward a planned target until the MPD system detects a gain. Once seen, the PWD at that point is recorded as an initial flowing pressure, and the SBP is increased to the value required to obtain the same standpipe pressure recorded just before the start of the DPPT.
If the SBP amount is within the parameters established in the well’s MPD Operating Matrix and Influx Management Envelope when inducing the influx and its volume, the influx circulation can then be performed with the MPD system – through the riser, at full circulation rate, with returns aligned to the rig’s mud/gas separator.
DPPT tests have helped Shell define the safest strategy to determine the formation pore pressure in real time. In fact, the first such test that the operator performed in the deepwater GOM is used as a reference case to safely optimize all well construction processes in the region, Mr Tuckwell said.
This first test was performed using a surface mud weight of 10.3 lb/gal while flowing at 700 gal/min down the drillstring. The test began with MPD targeting an approximately 11.1 lb/gal ECD, which required a 560-psi SBP. The SBP was reduced in small incremental steps during the test.
When the ECD reached approximately 10.75 lb/gal while holding 260-psi SBP, the formation pressure was reached and fluid began to enter the wellbore. SBP was increased, overbalance was reestablished, and the influx was stopped, followed by removal of the influx in the well by circulating through the MPD equipment while concurrently displacing the well to a 10.8 lb/gal fluid.
After further analyzing the data collected from the DPPT, the formation pressure was estimated to be closer to 10.77-10.81 lb/gal. The influx was circulated out of the well and up through the riser using the MPD system to maintain a constant BHP. During the influx circulation, a displacement from 10.3 lb/gal to 10.8 lb/gal surface mud weight was also conducted.
The DPPT showed that the influx expanded once at the surface. Mr Tuckwell said this was not typically seen in cases where the Coriolis flowmeter was installed downstream of the MPD choke manifold. With this particular well, the Coriolis had been installed upstream of the MPD chokes, and the test revealed that this was an effective solution to determining formation pore pressure. DC
For more information, please refer to SPE/IADC 210541, “Real-Time Downhole Pressure Environment Determination During Managed Pressure Drilling, Tripping and Cementing Operations to Improve Well Construction Safety Standards in Deepwater Gulf of Mexico.”