Where simple is never simple, operators aim for simplicity in deepwater, deep-well completions
By Jerry Greenberg, contributing editor

Applying completion technology to a well for optimal production is never simple, even if the plan calls for only “basic” temperature and/or pressure sensors. Designing and installing a completion system requires an enormous amount of planning to account for a seemingly infinite number of variables, even when developing a field with multiple similar wells.
Most multi-well fields are similarly completed. However, even in the same field, various subsurface features such as faults, dips and multiple reservoirs can mean that some wells require different completion systems for optimal life and production.
Not that long ago, the industry was completing wells with little or no downhole communications systems, no temperature- and pressure-sensing systems, and no way to choke off a zone that was producing too much water. The smart well technology that the industry relies on today, even for the “simplest” of completions, wasn’t developed yet.
Even with state-of-the art downhole communication systems, sliding sleeves for closing and opening various formations, real-time data transmission, fiber optics, and sensors and gauges for every conceivable purpose, operators still strive to keep completions as simple as possible, with only the right level of intelligence necessary to manage an optimally producing field.
There is no need to go overboard with the technology just because it’s available, as complexity increases well construction costs and reliability risks.
Operators are constantly looking for ways to make completions simpler, less costly and more reliable. That includes taking equipment typically installed downhole, such as electrical submersible pumps (ESPs), and moving them to the seafloor or higher.
Two such field developments are Shell’s Parque das Conchas, also known as BC-10, offshore Brazil, and Murphy E&P’s Azurite field offshore the Republic of Congo.
OPEN-HOLE GRAVEL PACKS, ESP BOOSTING SYSTEMS
The goals for the deepwater, shallow-depth, heavy oil BC-10 wells, with highly faulted reservoirs just above or adjacent to subsurface salt domes, were three-fold. First, they had to produce at high rates. Second, they had to be completed in a way to minimize interventions. Third, the wells had to contact as much of the reservoir as possible to produce for 20 years or longer.
“Because of the faulted nature of the BC-10 Phase 1 Ostra field, the long 1,000 m-plus horizontal open-hole gravel-pack wells were not only required to deliver high production rates, they enabled production from the different fault blocks,” said Wouter Bode, Shell’s BC-10 lead completions engineer in Brazil, “especially since it was unknown in the planning phase whether these faults identifiable on the seismic would allow for communication.”
Phase 1 of the field development included nine horizontal producing wells, one deviated producing well and one vertical injector well. Phase 2 completions will be similar, Mr Bode said. “We are looking at seven more producers and four water injectors to develop an additional field located to the north, named Argonauta O-North. The producers will again be horizontal gravel-packed wells executed similar to the successful low-skin Phase 1 wells.”
Shell announced the launch of Phase 2 in mid-October 2010; the drilling and completions campaign is expected to be executed in 2012 and 2013.
The horizontal gravel-packed wells will include premium sand-control screens, a ball valve-type fluid loss device and permanent downhole pressure and temperature gauge for production and reservoir management. The pressure and temperature gauge will measure data to indicate downhole conditions, allowing Shell to anticipate changes in the well and reservoir and to minimize potential adverse events that could affect production rates or longevity. Data from each well are displayed and stored in Shell’s real-time operations centers onshore during the entire life of the field.
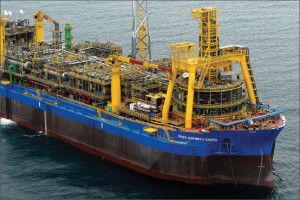
A major conceptual design decision taken for Phases 1 and 2 was to move the ESP from its typical downhole location to a manifold on the seabed, allowing Shell to boost pressure at the mudline and push the separated oil to the floating production, storage and offloading (FPSO) vessel. This eliminates the challenge and possible damage to the wells’ inflow system during change-out or workover operations on the ESPs. The boosting system also includes a caisson fluid separation system, as well as the ESP, so it is not as “simple” as installing an ESP onto a manifold.
A separate 100-m deep well was drilled for installation of the modular boosting and separation system. Full-scale onshore testing of the system was conducted for several years before it was implemented on the BC-10 field. It consists of a 100-m long caisson, which acts as a cylindrical cyclonic gas-liquid separator installed vertically in the shallow well, and a 1,500-hp ESP housed inside the caisson.
The oil enters the caisson through a top end assembly and flows into the separator through an angled tangential inlet spool. The liquid and gas separate as the flow stream travels downward 100 m in a spiral pattern, with additional separation occurring by centrifugal force. The liquid then flows down to the caisson sump, where it is pumped back upward by the 1,500-hp ESP into oil flowlines to the FPSO.
During Phase 1 development, four modular boosting systems were installed on one manifold and two on a second manifold. The plan for Phase 2 is to install an additional four modular boosting systems.
BC-10 CHALLENGES
“The main challenges in Brazil,” Mr Bode said, “is to achieve the productivity in deepwater from low-temperature medium- to heavy-oil fields, such as Ostra (24º API) and Argonauta B-West and O-North (17º API), that are hydrostatically pressurized and in a shallow-below-mudline setting with low available frac gradient.
“This makes delivery of high-rate wells in comparison to, for example, deep, warmer and geopressurized wells challenging. This type of well in the Gulf of Mexico has many challenges themselves, such as the casing design, number of casing strings required, depth, high temperatures, unconsolidated nature of the reservoirs and, not the least, compaction.
“So for BC-10, two enablers are drilling and completing very long horizontals and developing and working out the modular boosting systems for pressure boosting and separation,” Mr Bode continued. “It is no longer new technology for BC-10 Phase 2, however. To get them done right the first time requires a lot of detailed planning and careful execution.”
Another enabling technology is rotary steerable systems for drilling the reservoir section of the wells. “Rotary steerable systems provide a smooth wellbore, facilitating running of the sand-control screens and placement of the gravel pack in these long horizontals, the longest of which was 1,160 m,” Mr Bode explained.
He also noted that, without rotary steerable capability holding angle in the horizontal sections, they might not have been possible due to the unconsolidated nature of the BC-10 wells and the need to clean the hole continuously to manage ECDs below the frac gradient.
Looking toward Phase 2 development, Mr Bode noted that Shell will continue with similar technology and completions used during Phase 1. “However, what we did in BC-10 Phase 1 and what we will do in Phase 2, including the ESP systems, remains challenging.
“It is also clear that we are not planning a lot of smart well technology with distributed temperature systems or other gadgets,” he continued. “It does not provide value for money on BC-10 Phase 2 and would just add unnecessary complexity to what we need to achieve.”

MURPHY’S AZURITE FIELD
Murphy’s Azurite field offshore the Republic of Congo produces from multiple zones and fault blocks at different reservoir pressures to the industry’s first floating drilling, production, storage and offloading (FDPSO) vessel. The field presently includes four producing wells and two water-injection wells. Four additional wells – two producers and two injectors – are planned. The remaining wells, being drilled by a Nabors rig installed on the FDPSO, are scheduled to be completed by the end of Q1 2011.
Some of the completion technology employed in the Azurite wells includes vertical tree slim-bore (13.4-in. OD) hanger and wellhead systems; single-trip perforation and frac-pack systems; downhole pressure and temperature sensors; and dual choking smart valve systems. The smart valve system allows Murphy to commingle oil in the wellbore from two reservoirs, both producing, and to control the reservoirs individually. Presently, the smart valve systems are installed in two producers and one injector. One of the remaining injector wells yet to be drilled will contain a smart valve system.
The wells also contain sensors to measure temperature and pressure above and below the smart valves, with a triple gauge pack, one for each of the reservoirs and one for the commingled production. Each gauge pack consists of three pressure and three temperature sensors.
“This technology has been used previously, so it is not new,” said Brian Joslin, staff completion engineer for Murphy. The use of the slim-bore system on the Azurite project is new, and it is another step forward for completions, as it required making the subsea completions compatible with the smaller-ID marine risers by decreasing the completions’ running diameters.
“There are the standard gauges on the annulus and production side of the tree upstream and downstream of the chokes,” explained Jeremy Lochte, staff consultant for Deep Sea Development Services and subsea adviser to Murphy. “We have acoustic sand detectors on the producers and a flow meter at the choke in the injector wells because we have a common supply to all of the injection wells, and the flow meters indicate the amount of water injected into the different wells.”
DOWNHOLE INTELLIGENCE
The goal for the Azurite wells was to design the completions to avoid interventions or workover operations. That took into consideration that the rig on the FDPSO would be removed after the final well was drilled and completed.
That is also the reason Murphy installed downhole sleeves and valves for choking off individual reservoirs, as well as surface-control capabilities for every function of the field.
Murphy believes it has just the right level of intelligence in its Azurite producers and injectors. The company is using smart well systems to adjust the flow from the producers and the flow into the injectors to balance the water flood.
“Reliability of the equipment is very important,” said Scott Bennett, Murphy’s completions team leader. “We are not using any new technology in our downhole equipment; we wanted to use systems that are going to work.”

“Reliability (of selective well completions) historically has been low,” Mr Lochte said. “I would say around 50%. It’s still a risk/reward, where you spend money upfront, and, if it works and the valves remain functional, you save yourself a workover.”
“When you get into subsea wells, the cost is so high that it is more economical to run a smart system,” Mr Joslin added.
On the other hand, companies touting light riserless intervention systems that can perform workovers and other downhole functions without using an expensive semisubmersible could influence the completions market. Vessels with light intervention equipment could be used to open and close downhole valves, competing to some degree with smart well systems by reducing operators’ costs to perform a workover at a later date. This would allow operators to forgo smart well costs upfront.
Some operators will be more willing to use light intervention systems more frequently as confidence builds. “My philosophy is that the second mouse gets the cheese,” Mr Lochte said. “It’s so much better to be the second to do something because they benefit from all of the lessons learned.”
“That’s an open question in the industry,” Mr Joslin said. “Can we reduce our costs by reducing the complexity of smart well completions based on light intervention systems?
“The industry is going to see two markets,” he continued. “It is going to see complex completions become more reliable, and costs will drop as more companies compete in that market. The other market is for light intervention systems that will find a market for unforeseen workovers.
“There will be an increasing number of subsea wells, more unforeseen workovers will be required, and there will be a drive to locate the least expensive method to perform that intervention,” Mr Joslin added. “As that market grows, costs will fall as well.
“Meantime, the industry will continue to install smart completions to avoid interventions in the future, resulting in a double push for technology.”
When asked if there is any technology available today that wasn’t available in 2009 when the initial Azurite wells were being drilled, Mr Joslin said, “I think everyone wants more information, better information and more reliable information, and that could come from fiber-optic technology downhole. For example, I want real-time data from downhole gauges while I’m fracking a well.
“I know companies are working on such systems. I don’t think the technology development is stagnant,” he continued. “The industry is going to see incremental changes over the next several years. And cost-wise, fiber-optic technology is going through the same iterations that smart wells and valves have gone through.”
Despite technologies that are under development, the conversation always turns to reliability, which perhaps tops the industry’s wish list. “We use a lot of technology in these wells,” Mr Joslin emphasized.
“None of it is brand new; it’s all been used in some way, but a lot of the technology is not commonly used, and sometimes the technology is not commonly used in conjunction with other technology.
“Look at the technologies comprising a single-trip system, where you perforate, frac pack and then trip out of the hole,” he continued, “and you combine that with smart valve systems, slim-bore systems, pressure and temperature sensors and gauges and so on to provide the ability to see above and below the smart valves. There are not a lot of those systems around the industry where all of that technology is combined.
“What we want is reliability,” Mr Joslin concluded. “We want what we have to work.”