Self-removing EFDAs level stimulation access
Environmentally friendly diverting agents part of optimized approach to plug and perf fracturing method
By Dave Allison, Halliburton
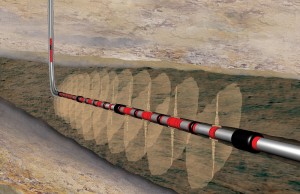
The industry has made great strides to improve the well completion phase of today’s producing oil and gas wells. What used to be considered a unique operation has been transformed into a highly efficient completion process that some equate to a mobile manufacturing process. Compared with completions in the early 2000s, the time and cost to complete wells today has been lowered even as the fracture intensity (number of fractures per well) continues to rise.
The completion technique that has become the mainstay process is “plug and perf” (Figure 2). It consists of gaining entry to the formation by perforating the farthest interval in the wellbore (i.e., near the toe of the lateral), performing the stimulation treatment and subsequently isolating the just-completed interval from the next interval to be stimulated by using a mechanical bridge plug.
By some estimates, the process is being used in more than 85% of today’s horizontal well completions.
In other industries such as automobiles, consumer goods or computer chips, where manufacturing cost and efficiency drive profitability, they wring out even more costs and efficiencies using process evaluation tools with names like “lean,” “sigma” or “continuous improvement.”
These same process evaluation tools and techniques are being systematically applied to plug and perf to improve efficiency and continue to reduce costs. The operational phase of gaining access to the reservoir is one of the primary process steps that is under continued evaluation and evolution.
One efficiency technique is to move process steps off of the critical path. This is being implemented with the utilization of mechanical sliding sleeves (MSS) that are run into the well as part of the casing process of the drilling operation (Figure 1).
A second efficiency technique entails performing similar steps at the same time. This is being implemented by adding more perforation clusters within an interval of a typical plug-and-perf sequence or increasing the number of sliding sleeve assemblies per interval.
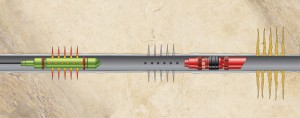
Limiting Constraints
Unfortunately, these efficiency techniques could create poorer-performing wells if carried too far. The additional reservoir access points (perforation clusters) within one interval require proportionally more fracturing energy and materials. The ability to deliver higher fracturing rates and pressure to the new access points may be limited by other constraints, such as casing pressure limitations, pumping equipment limitations or material transfer restrictions.
An engineering calculation often called “limited entry technique” helps strike the balance between too many access points and not enough. Nevertheless, computer modeling and fracture treatment monitoring have shown that relying solely on the limited entry technique does not guarantee that all of the access points are treated equally.
Some results have indicated that most of the fluid and proppant goes into only a small portion of the open perforations or sleeve ports. The consequence when this occurs is a large portion of the reservoir remaining unstimulated.
Combining Technologies
The recent introduction of environmentally friendly diverting agents (EFDA) appears to be a potential key technology (Figure 3) that will facilitate a much fuller implementation of the completion efficiency gains from the additional reservoir access points of the MSS technology and the optimized plug and perf technique.
EFDA materials are the first pumpable, self-degrading diverting agents that can withstand the rigors of fracturing. The material can temporarily block the access points that initially take most of the fluid and proppant and divert the fracturing energy and materials to another portion of the interval. Repeating this sequence will facilitate placing the desired volumes of sand and fluids in all of the access points and ideally result in increased productivity.
Additionally, the EFDA helps ensure that all perforations are stimulated.
The self-removing characteristic of the EFDA is highly desirable. The materials do not require special solvents or surface activities to initiate the degradation of the particles. All of the catalyzing mechanisms required to start the degradation process are available within the bottomhole environment. Typically, once the degradation process begins, the material completely disappears, leaving the access points and wellbore fully open. The reservoir temperature controls the longevity of the EFDA.
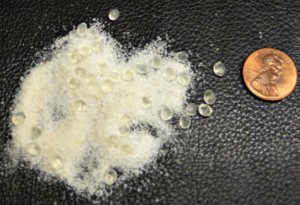
A third characteristic is the improved environmental profile of EFDAs. The material is sourced from the food industry and can be handled and utilized on surface with confidence as it is essentially harmless to humans, animals and plants. Typically, the EFDA has little or no impact on the fracturing fluid system used to place the proppant into the reservoir, so fluid systems tailored to the reservoir mineralogy can continue to be used.
The byproduct of the degrading process is a water-soluble molecule that is readily absorbed back into the environment. The degraded EFDA material does not interfere with future operations, such as the use of production chemicals like scale inhibitors, oxygen scavengers, H2S scavengers and bactericides. It also does not inhibit recycling and reuse of the flowback water.
Minimize Idle Times
The cost effectiveness calculation for the combination of optimized plug and perf with EFDA can be made by examining the operations necessary to complete the well. The individual operations that are required often have times of no productivity while waiting in the work sequence. For example, when the actual fracturing operations are taking place, perforating crews and pump-down crews are typically standing by. When the perforating crew is active, the fracturing crews, surface equipment crews and water management crews are idle.
The optimization process tries to minimize idle times, combine like operations and shorten the duration of the most costly items. Some savings will be offset by the introduction of new technology and techniques, e.g., using EFDAs to reduce the number of mechanical bridge plugs required.
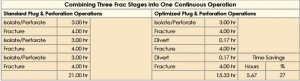
Table 1 provides an example of standard plug and perf operational steps for three intervals within a reservoir. By contrast, the optimized plug and perf operation combines like activities, e.g., perforation and pump-down service, and utilizes EFDA to replace the mechanical bridge plug, resulting in a 27% reduction in the time necessary to complete the three zones. Utilizing normalized values for the services, standby time and materials, it is possible to save $40,000 or more.
As there are very few horizontal wells completed with only three productive intervals, the savings are proportional to the number of intervals completed. For 12 zones, the cost reduction can approach $160,000, and for 30 zones, potential savings approach $400,000. The reduction in time to stimulate the well and the time saved by having to drill out fewer bridge plugs also permits the wells to be brought on line sooner, which can have a significant impact on the net present value calculation for the well and field.
The introduction of new technology like the EFDA and a mind set of continuous improvement can offer new approaches to enhance production and reduce completion costs.
AccessFrac, an EFDA material, is a service mark of Halliburton. RapidFrac, a mechanical sliding sleeve system, is a registered trademark of Halliburton.