CT finds niches in data retrieval, plug drill-out
Recent applications also pushing coiled-tubing capability to extend well reach, enhance production life
By Katie Mazerov, contributing editor
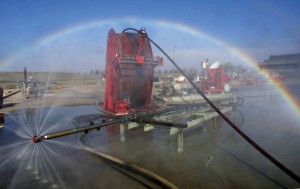
As one of the oilfield’s most flexible and versatile workhorses, coiled tubing (CT) continues to push the technology envelope with new applications in more sophisticated operations. Beyond its traditional use for clean-outs, milling, fishing and retrieving, CT is delivering expanded services for drilling, real-time data monitoring, temperature sensing and greater reach in laterals with devices such as tractors. Once a trouble-shooting solution deployed only to fix problems, CT is increasingly being considered in initial well designs.
And although it is still used primarily in North America, coiled tubing is expanding its global reach as well, particularly in Latin American, European and Asian regions where the horizontal well market is growing.
“Coiled tubing has been one of those technologies that has always had many applications,” said Bruce McIninch, worldwide completions manager for Marathon Oil. “A lot of that work has been on the well-service side of the business, but we’ve seen that expand to drilling and to integral aspects of the completion phase.”
Mr McIninch believes the biggest growth area in North America has been the drilling out of plugs along the horizontal wellbores after plug-and-perforation operations. Marathon Oil is active in the Bakken, Eagle Ford and Anadarko/Woodford shale plays and in 2010 entered the Denver-Julesburg Basin of the Niobrara Shale.
“It’s the age-old chicken-and-egg battle,” Mr McIninch said. “We’re asking drilling contractors to drill farther and then expect the well-service companies to get the coil to these new depths. Generally, we are getting CT down to about 19,000 ft in the Eagle Ford, but the longer we go in the horizontal sections, the more difficult it is to get the coil to bottom.”
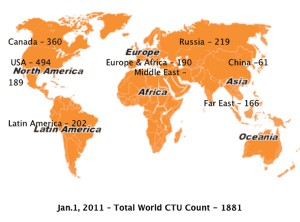
Improvements in friction-reducing chemicals and technology, such as agitators, have allowed the industry to gain an extra few thousand feet. That push is creating a challenge for suppliers to understand the limitations and fatigue threshold of the coil itself, he added. “They need to track the number of cycles they have on that coil and monitor the deformation to identify when it needs to be replaced.”
Coiled tubing is increasingly being used to extend production life when used for velocity strings or retrofitting artificial lift systems to facilitate a lower point of gas injection in wells.
“Instead of spending a lot of money pulling the completion and downsizing the tubing, we’ve been able to go in and hang off CT and actually increase the life of our wells at a relatively low cost,” Mr McIninch continued. For workovers in sensitive formations, CT can be deployed while the well is still flowing, thus minimizing the need to use weighted fluids that could damage well productivity.
The industry is also looking at uses for CT beyond its problem-solving capabilities, considering its potential when evaluating various completion design options, such as casing sizes and CT removable or shift-able equipment. “We are doing a better job of integrating coil-friendly well designs for better long-term productivity,” he said.
Related Article:
Xtreme Drilling introduces 23,500-ft capable land coiled-tubing well intervention unit
Conveying Real-Time Data
Coiled tubing is also being used to deploy more reliable and precise tools that can measure downhole parameters (weight on bit, torque, pressure and temperature) and store or pulse this information back to the surface.
“Historically, drillers have pulsed information to the surface with measurement while drilling (MWD) and other tools that provide an understanding of what’s happening at the bit,” Mr McIninch said. “But coil has not had a reliable real-time downhole sensing capability, so we’ve had to rely on very experienced operators and good modeling to predict what’s going on downhole.”
While these upgraded tools can enhance efficiency and reduce runs into the hole, Mr McIninch also sees them as a way to more quickly train new equipment operators by allowing them to see real-time feedback and compare that with what they are seeing at the surface to understand what is occurring downhole. “It’s a great opportunity to accelerate skill development, which is what we need in the industry right now,” he said.
That ability to acquire real-time surface read-out data of what is going on downhole during a stimulation or clean-out operation is one of the newest applications of CT, said Brian Schwanitz, vice president of Welltec, an international provider of well intervention services. The company manufactures coiled-tubing tractors that provide
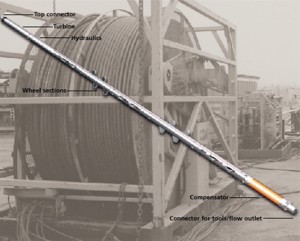
extended reach in CT operations.
Fiber-optic cables pumped through the coil, the way electric line cables have been for several years, is providing a distributed temperature sensing (DTS) measurement of the temperature of the coil as the well heats up following a treatment.
“Fluids are cooler at the surface than downhole, and the entire length of the fiber-optic cable inside the coil will sense the changing temperature distribution along the cable,” said Mr Schwanitz, who is also board vice chairman of the Intervention & Coiled Tubing Association (ICoTA), an organization aimed at improving communication and technical awareness in the well intervention industry. The SPE/ICoTA Coiled Tubing and Well Intervention Conference & Exhibition will be held 27-28 March in Houston.
“Processing the DTS data allows the operator to detect the cooling anomaly, which shows where the majority of the fluid went during pumping,” he continued. “However, as wells start to flow back, the temperature change can be either a cooling or a heating anomaly, depending on whether it is a gas- or an oil-producer.”
Electric line and pressure-pulse telemetry also are being used to convey data to the surface through coiled tubing. “This ability to put data-monitoring devices at the bottom of the coil is great for deviated wells, sidetracks and unconventional drilling,” Mr Schwanitz said.
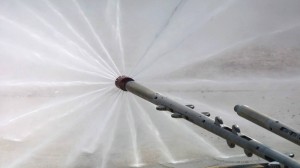
Extending the reach
While new technologies have allowed CT to extend farther into wellbores, operators are still looking for more reach beyond where the coil normally locks up – helical buckle or friction lock-up – to lateral depths of 10,000 ft or more. “One way to extend coil’s reach is with bigger, stiffer coil, but there is a limit to how much coil can be put on a reel and transported safely without exceeding load limits,” Mr Schwanitz said.
CT tractors, long, thin hydraulically powered devices, pull the coil considerably deeper into the well by providing traction against the casing or borehole wall. Another method is an agitator, which has a flapper that creates the vibration and breaks the friction, allowing the coil to slide farther. Friction-reducers, slick chemicals that allow the coil to push out farther, are a third option.
Tractors come in four sizes, ranging from 2 1/8 in. to 4 ½ in. and can be fitted on any size coil, although they have never pulled CT heavier than 2 3/8 in. “A tractor can easily extend the CT out to 10,000 feet, depending on the amount of pull required to go farther and how smoothly the well is drilled,” Mr Schwanitz explained. “If the well is particularly deviated, with several changes in direction, there will be more friction, which will require more pull force.
“A big application for tractors is in actually providing weight on bit to drill or mill hardware, cement or rock,” he continued. “Recent examples of this involve milling out the frac plugs, used in multi-stage fracturing operations, that are too far down the hole for the CT to reach by itself without a friction lock-up.”
The tractor also offers the added benefit of providing control to the reactive torque, caused when the coil rotates inside the pipe due to the milling action.
Beyond drilling operations, CT tractors also have been used to carry electric wirelines with logging tools and perforating guns, and to set straddle packers in horizontal and extended-reach wells.
Creating vibration
Thru-Tubing Solutions (TTS) has provided CT and snubbing products and services since 1997, including fishing and retrieval and plug-and-perf services. The company has completed more than 5,000 operations with its X-tended Reach Vibratory (XRV) technology, decreasing the drill-out time on plugs and reaching depths beyond computer model predictions. The technology creates vibration to reduce friction lock-up and helical buckling while drilling horizontal or deviated wells, explained Jenna Robertson, technical sales representative.
“Reducing friction allows the drill string to reach deeper or farther out laterally,” she said. “The system is ideal for deviated wells or extended lateral sections where the vibration between the work string and the casing allows the tool to keep creeping down the hole and create the momentum needed,” she said.
Equipped with a high-power motor and proprietary carbide mills, the system can work through harsh conditions in horizontal wells to mill plugs, frac ports and cement. Because the tool was designed without any elastomeric components, there are no temperature limitations, fluid compatibility issues or risk of circulation loss due to plugged bits or other bottomhole assembly components.
TTS is seeing increased global demand for its snubbing and CT services. The company, headquartered in Oklahoma City, has established an office in China and will be opening an office in Oman.
The company has expanded the XRV technology to launch a drilling solutions division. The centerpieces of the new application are the 4 ¾-in., 4 7/8-in. and 6 ½-in. outer diameter tools affixed to the drill string. It was designed to create minimal MWD interference and improves both sliding rates of penetration and steering, Ms Robertson noted. The patent-pending drilling tool is being used for two operations in Western Canada and the US.
XRV is a trademarked term of Thru-Tubing Solutions.