Systematic approach ensures drilling system synergy for deepwater drilling program
By Linda Hsieh, managing editor
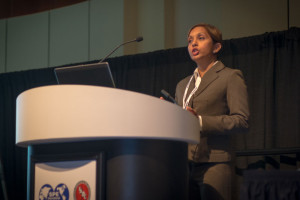
Pre-planning and offset well review were critical factors to a systematic approach taken to improve a deepwater drilling program in the Gulf of Mexico, Reisha Bouska, Project Manager for National Oilwell Varco (NOV) said. In a presentation this week at the 2014 IADC/SPE Drilling Conference in Fort Worth, Texas, Ms Bouska highlighted key steps that were taken to evaluate each phase of the drilling process, from bit to surface. Compared with other similar approaches, this holistic strategy emphasized “the detailed evaluation, engineering, as well as modeling of not just the individual drilling components but ensuring the synergy of the entire drilling system,” she said.
This systems approach was applied to two vertical wells (B and C) in the same field, focusing on the 12 ¼-by-13 ½-in. section that has historically been challenged with shock and vibrations. To begin, the team performed a thorough review of the offset well, well A. “This was to understand the drilling risks, lessons learned and drillstring configuration and behavior within that interval,” she explained.
A series of analytical evaluations were conducted, including rock strength analysis, review of the BHAs, drilling data analysis and FEA-based modeling of drilling dynamics. “Based on the understanding of these challenges, we can now redesign a drillstring and operational environment to successfully improve performance,” Ms Bouska said.
Mitigation measures that were then applied to the project include better reamer selection, increasing the OD of the MWD tools and drill collars, and using an 1/8-in. undergauged pilot hole spiral stabilization below the reamer. Applying FEA-based modeling for drilling dynamics and torque and drag also helped to determine a roadmap of the necessary drilling parameters.
Further, a vibration-reduction technology – the Asymmetrical Vibration Reduction Tool (AVRT) – was applied to mitigate torsional vibrations and stick-slip, and roller reamer technology in the pilot hole helped to minimize frictional contact.
Distributed Drilling Dynamics Recorders (DDDR), which are high-density sensors placed along the drillstring, were used to capture downhole drilling dynamics. “For each of the drilling dynamic sensors, we can actually see if a sensor is placed close to a stabilizer… we can determine the vibration response of those individual components and the impact it has on performance.”
A review of the project KPIs showed across-the-board improvements once the systematic approach was applied, from the number of runs per interval to average ROP to vibration response, Ms Bouska said.
Looking to the future, she added that although this particular project applied the systematic approach to vertical deepwater wells, it can actually be applied throughout the industry. The approach is also flexible, which allows for the easy integration of new technology into the process, she added.
Although advanced tools and technologies, BHA and drillstring design, iterative detailed modeling, and the validation of solutions through the use of high-density drilling data all played key roles in the project, Ms Bouska emphasized that it was the detailed reviews and understanding of offset wells that paved the way to success. “Once you understand the root causes and the impact of the historical control measures applied, we can take this and apply the best-fit solutions.”
For more information about this project, please see IADC/SPE 168016, “An Alternative Systems Approach to the Successful Execution of Deepwater Drilling Programs.”