Number of rigs to be converted has increased since start of project due to increased demand, number of candidate wells for MPD
By Marcos Coradini Tolfo, Emmanuel Franco Nogueira, Andre Alonso Fernandes, Felipe de Souza Terra, Guilherme Siqueira Vanni and Luiz Genaro Filho, Petrobras
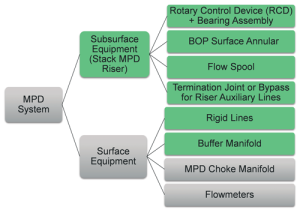
Since 1998, Petrobras has been conceiving, developing, testing, field-proving and commercially applying managed pressure drilling (MPD) technologies. This effort is coordinated by the Corporate Engineering and Research and Development Divisions through a number of technology projects in Petrobras’ well engineering R&D portfolio.
To support the corporate drilling strategy and to put forth specific development plans in the pre-salt area, Petrobras launched the “Drilling in Areas Prone to Severe Loss Circulation” initiative in 2013. It consists of the conversion of a significant amount of its offshore drilling vessels to MPD-ready. This initiative is part of a corporate cost reduction project called PRC-Poço, created with the objective of converting, in a period of three years, 15 rigs to MPD ready, with minimal or no impact on normal rig operations.
From the IADC Underbalanced Operations and Managed Pressure Committee: “Managed pressure drilling is an adaptive drilling process used to precisely control the annular pressure profile throughout the wellbore. The objectives are to ascertain the downhole pressure environment limits and to manage the annular hydraulic pressure profile accordingly. It is the intention of MPD to avoid continuous influx of formation fluids to the surface. Any influx incidental to the operation will be safely contained using an appropriate process.” Petrobras has selected three MPD techniques – surface backpressure (SBP), pressurized mudcap drilling (PMCD) and floating mud cap drilling (FMCD) – depending on the requirements and conditions of the well.
Petrobras established the PRC-Poço program to focus on cost reduction without overlooking safety principles as defined by the company’s rules. It targets wells where conventional drilling technologies are not recommended or indicated, such as those with a narrow window between pore pressure and formation fracture gradient curves, or scenarios with severe circulations losses that result in high NPT. Many complex prospects had been postponed until after MPD installation.
To date, Petrobras has drilled 20 deepwater wells with MPD techniques, proving the importance of MPD systems and reaffirming the success of the path chosen three years ago. By the end of 2016, 15 rigs from five drilling contractors will have been converted to MPD ready. The original number of MPD-ready rigs has increased based on demand variations since 2013, giving Petrobras flexibility to allocate MPD equipment.
One of the challenges to overcome was the adjustment of the number of rigs to be converted to MPD ready versus the number of candidate wells to apply MPD technologies. The solution was to classify wells into two major groups: MPD mandatory and MPD recommended. The mandatory wells were related to a tight window between pore pressure and fracture gradient and to a high probability of severe losses, based on correlation wells and statistic models that predict the chances of a well experiencing severe losses. Recommended wells were related to small to medium probability of severe losses and to exploratory wells where there was little information about the locations to be drilled.
Rig conversion to MPD ready

The MPD-ready rig customizations require an enormous amount of rig modifications and a group of appropriated equipment to make the operation possible. For a better understanding and project management, two major subgroups were created to classify the MPD system. The equipment may be divided into surface equipment and subsurface equipment, and these two categories each face different challenges.
Surface equipment
Some surface equipment needed to be installed at the rig. New rigid lines were necessary to allow different alignments necessary to the operation. Even though each rig has its particularities, Petrobras developed a common standard with the minimum requirements for a safe operation. Figure 2 represents the generic piping and instrumentation diagram (P&ID) applied to MPD-ready rigs at Petrobras.
Important features of the system include:
• Despite the fact that the rotating control device (RCD) and riser equipment are limited to 2 kpsi, the whole surface system is designed to work with 5 kpsi, anticipating future improvements;
• All the alignments have redundancy available to permit continuous operation in case of failure;
• The system allows the continuous monitoring of the bearing assembly seals by the trip tank;
• The system allows PMCD operations by pumping fluid through the annulus;
• The system allows alignment to the mud gas separator (interlocked valves); and
• PRVs are used for piping protection.
Subsurface equipment
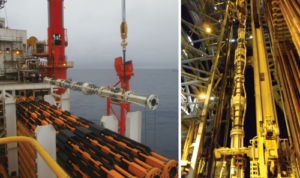
To perform the MPD operation, some equipment needed to be added to the drilling riser with the intention to divert the well returns to the MPD system. These modifications needed to preserve riser auxiliary line functions. The original approach was to modify the conventional telescopic joint, introducing a termination joint below the MPD riser stack, to guarantee that riser auxiliary line flow hoses were correctly installed. This solution initially had a down side of a longer lead time due to the telescopic joint modification and procurement and manufacturing of a termination joint. An alternative approach was to fit rigid pipes for riser auxiliary lines around the MPD riser stack. This would keep the conventional telescopic joint unaltered. The second option was chosen for the majority of Petrobras MPD-ready rig conversions. This concept had the advantage of being delivered in a shorter time. However, there are some negative points, notably the total weight of the configuration and the total time to run the MPD riser stack.
Operators or drilling contractors to manage MPD?
One major discussion was who would be responsible for the equipment – operators or drilling contractors?
Petrobras considered multiple configurations, from the drilling contractor owning only the surface piping and equipment, excluding the MPD manifold, to the operator supplying only the MPD manifold.
The MPD manifold is the heart of MPD operations and is considered by Petrobras as something to be addressed by the operator as a drilling service. The experience shows that the remainder equipment, including the RCD, should belong to and be managed by the drilling contractor.
Petrobras has made major investments to steer the industry toward making MPD systems a common tool. An MPD-ready rig is a desirable feature at the time of negotiating a contract extension or awarding a new contract. At least the capability to install an MPD manifold in a short time frame is expected to be standard in the near future.
The process to adapt and operate an MPD rig

Petrobras experience shows that 18 to 24 months are required to complete the conversion of a conventional drilling vessel into an MPD-ready unit. That’s the main reason an MPD-ready rig will be differentiated in the market. It offers flexibility to the drilling team to decide to use or not use the technology. The amount of work to be done before the rig gets converted is as follows:
Technical specifications → P&ID definition → Rig survey → Workshop (interface matrix) → Detailing the project
Follow-up activities: Action tracker → Implementation schedule → FAT and SIT → Hazid/Hazop → Training → Operation
A dedicated group worked on the rig conversions and was a key participant in all stages of the project, from negotiations with drilling contractors to the end of the first operations for each rig. This guaranteed bridging of procedures and conducting hands-on training at the rig site. This team was responsible for integrating all companies involved in the process.
Since there was no internal Petrobras guideline, many discussions were carried out while the project was being detailed. This showed the importance of having a thorough plan in place, based on the technical features and requirements for the installation of equipment.
Lessons learned
During the project, several lessons were learned relating to the rig preparation and to perform the MPD operation itself. Two of these lessons are discussed in this article.
The first lesson is related to flowmeter positioning. Petrobras had issues with coriolis readings for low flow rates with applied SBP. After performing field tests in onshore facilities, it was determined that this failure was related to the flow pattern of well returns through the meter. Free gas/air and pressure/hydrostatic head at the meter cause cavitation impaired flowmeter readings. It was determined that there were three possible solutions: a) Install a manually actuated valve or pressure setpoint valve downstream of the flowmeter, maintaining minimum pressure at the meter; b) Place flowmeter skid in elevation below the flowline elevation; and c) Place flowmeter skid upstream of the MPD choke manifold so that the coriolis is always working under applied surface pressure.
Shortcomings with the subsea BOP had to be addressed, as well. When drilling with hydrostatically underbalanced mud, the BOP test must be performed with a wellhead pressure equal to the SBP. Petrobras worked on three solutions to perform the BOP test: a) using a test ram; b) developing procedures to do the test with pressure in the riser; and c) modifications in the test plug (ITT) to seal with wellhead pressure from below. When working with FMCD, the BOP must support a differential pressure up to 2,500 psi from outside (riser might be partially/completely empty). All major BOP manufacturers developed solutions to this issue, and the drilling contractors are updating their BOPs. Another major concern, related to not being able to maintain a mud level at the rotary table, is the stiffening of the subsea BOP flex joint to reduce the rig’s maximum allowable drift and riser inclination. This demands a proper riser analysis.
Improvement opportunities
Despite the good results of the operation, opportunities for improvement exist relating to both surface and subsurface equipment. These primarily involve infrastructure and performance while handling the equipment. One important issue is the time spent running the MPD riser stack, which was heavy and difficult to be handled. The industry should aim to:
• Reduce the dimensions/weight of the MPD riser stack (47 ton/21-23 m);
° Run in a single joint; easier to transport, store and handle;
• Develop quick coupler for the hydraulic valves;
• Consolidate standard business model: Figure 4 shows the time consumed to run the MPD riser stack during operations on four rigs. The first rig has the modified termination joint, which is easier to run, resulting in faster operations. However, despite bad results in the first operations of the other rigs, it became clear that it’s possible to achieve good performances with the bypass configuration, as well. That is another reason to support the idea of the drilling contractor taking these equipment, except the MPD manifold, into its responsibility. It’s expected that would result in a better learning curve and a better performance to run the MPD riser stack.
The main idea is to reduce the majority of the impact of MPD to the well construction schedule so that the technique may be used in a broader number of applications (for instance, as early kick detection mode only). When the drilling contractor offers standard packages – everything but the MPD manifold – it will be easier and faster to make the technique available in a shorter time, which will allow more flexibility to the industry and differentiating MPD-ready rigs in the market.
MPD training
MPD is a non-conventional technique and, as such, it is mandatory that specific procedures are prepared by the operator, drilling contractor and service supplier. All documentation must be coherent and aligned.
Competence development on MPD well design and MPD operations was divided into basic, intermediate, advanced and hands-on levels, according to a training matrix, and included in an internal procedure. To date, more than 500 Petrobras employees, as well as all related drilling contractors and third parties in all the rigs involved, have been trained.
The roles to be trained were defined as: operator (companyman, mud engineer, directional driller, LWD, cement engineer, mud logger and geologist); drilling contractor (OIM, toolpusher, driller, assistant driller, derrickman, assistant derrickman, captain, safety); drilling services (fluids, LWD, directional drilling, mud logging, cement operations). The companyman onboard the rig checks that all training requirements have been met to guarantee that procedures are being followed and the people involved are capable of performing their jobs.
Future challenges
MPD is a reality in Petrobras operations. All the operations that have been performed so far have proven that the technology has come to stay and has become more and more common in the industry. Of course, there are some major points to be addressed to consolidate the technique. Regarding the operation, the industry should look for an increase in reliability of the equipment and software updates to make the whole process safer and cheaper. The main challenge is to get to the point where the decision to use MPD can be made faster (with more rigs available) and cheaper (better performances with less additional time and costs). DC
Click here to view a video interview with one of the authors of this article.