Single-trip stand-alone screens cut rig time, costs in deepwater Nigeria
Shell worked with service providers to develop new completions concept resulting in significant savings on Bonga field
By Jessica Whiteside, Contributor
Why do in two trips what you can do in one? That simple concept forms the foundation for a revolutionary, high-tech approach to deepwater stand-alone screens completion tested at Shell’s Bonga operations off the Nigerian coast. The project team described the evolution of the single-trip pilot in a presentation at the 2019 Offshore Technology Conference (OTC) in Houston on 9 May.
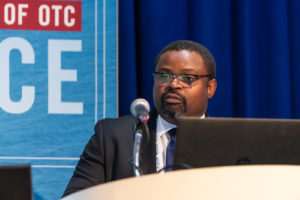
The Bonga field was Nigeria’s first deepwater oil discovery and boosted the country’s capacity by 10% when it launched production in 2005. Shell’s pursuit of the world’s first single-trip completion for deepwater, open-hole, stand-alone screens (SAS) in the Bonga field began with that mother of invention: necessity. The necessity in this case was a drive to reduce completion costs when rock-bottom crude prices left the oil and gas sector reeling in 2015.
“Everybody knew something had to be done, especially in the Bonga project, to be able to improve on the profitability,” said Osehojie Ojeh-Oziegbe of Shell Nigeria Exploration and Production Company (SNEPCo) during the team’s OTC presentation.
Shell uses a single-string upper completion and a subsea vertical Christmas tree for its Bonga wells, which have been drilled across three phases of development over 15 years. The earlier phases were completed mostly as deviated frac and pack producers and injectors or open-hole gravel pack producers, while phase two and three wells feature the open-hole SAS completions. Whatever the type, all required two trips to install the completions – one for the lower and one for the upper.
Shell had already been working on optimization strategies to squeeze inefficiencies out of these time-consuming multi-trip completions. Even with fifth- and sixth-generation rigs with the highest-experienced personnel, the fastest the multi-trip could be done was an average of about 10 days per 10,000-ft well, Mr Ojeh-Oziegbe said.
Objectives
The more dramatic improvements demanded by the unstable oil price environment required a different way of thinking. SNEPCo’s wells front-end completion and well intervention team generated the concept for a streamlined system that would deploy the upper and lower completions in a single trip. The goal was to cut completion installation days by 50% and equipment and service costs by 30%, while reducing personnel exposure to risk. Their technical wish list also included the ability to:
• Provide backup contingency for all remotely actuated equipment;
• Displace the open-hole section to breaker fluid;
• Close, test and open the reservoir valve remotely, without deployment of intervention tools;
• Displace packer fluid and set and test production packers; and
• Land the tubing hanger and pressure test all barrier elements.
Technology Selection
To fulfill these objectives, SNEPCo needed the right partners.
“Our greatest strength is in the service companies, so the first thing we did was to pull the service companies together into a room and give them what our objectives were, what we wanted to achieve,” Mr Ojeh-Oziegbe said, describing that session as a technical show and tell.
“Everybody knew something had to be done, especially in the Bonga project, to be able to improve on the profitability.” – Osehojie Ojeh-Oziegbe, SNEPCO
Following a comprehensive risk analysis and evaluation process, SNEPCo ultimately merged designs and tools from three primary vendors – Halliburton, Weatherford and Schlumberger – to come up with a customized solution that fits the field constraints of the Bonga wells and met the criteria set by the company’s technical and risk evaluators.
“Everybody wanted to be a part of the movement to go from a highly cumbersome, highly expensive system to a more refined – even though it’s a little bit more complex – but a less expensive system,” Mr Ojeh-Oziegbe said.
The resulting design for the single-trip SAS completion featured the following equipment:
• Tubing hanger;
• Tubing retrievable surface controlled sub-surface safety valve;
• Permanent downhole gauge mandrel;
• Annular released polished bore receptacle;
• Upper production packer;
• No-go landing nipple;
• RFID circulation valve;
• Lower production packer;
• Electronic isolation barrier valve;
• Re-settable sealable contraction joint;
• RFID production screens with inflow control device technology; and
• Electronic operated toe valve.
The combination of electronic and interventionless techniques – like the RFID-controlled devices – simplified well operations and enabled improvements in installation speed, efficiency, well costs and safety. For example, the use of the electromechanical remotely operated barrier valves – preprogrammed via laptop – made operations safer and more efficient by replacing traditional wireline plug and prong equipment, reducing or eliminating the need for wireline runs.
The decision to use multiple vendors meant interface management between SNEPCo and the contractors was critical to project success. As detailed in the OTC paper, the team did a “complete the well on paper” exercise and held weekly technical and project planning meetings to mitigate and eliminate potential problems prior to execution. During planning, they also prioritized the understanding by all parties of the technological interfaces among each contractor’s subsystems and their performance boundaries.
Results
Using the single-trip completion, Shell and its contractors met or exceeded their objectives, including an approximately 40-50% reduction in rig days and a similar reduction in costs. An average multi-trip completion on the Bonga project costs about $14 million, Mr Ojeh-Oziegbe said. “That amount was halved by using the single trip,” he reported.
The Bonga 63 well completed using this approach in July 2018 is currently producing. It likely won’t be the last to use the new system: The team’s OTC paper states that “the single trip will be considered first in well completion design for SAS” in wells that meet the selection criteria.
“The system has been proven on Bonga,” Mr Ojeh-Oziegbe said. “We’re still working on the design to make it more cost effective and more efficient.”
However, not all wells would be suitable candidates for this single-trip SAS completions system. The paper notes the strategy would be limited to 2D and simple 3D wells. Because some of the electronic devices and remote technologies need batteries to function, battery life and the impact of certain temperatures on downhole electronics are considerations that could affect eligibility.
Mr Ojeh-Oziegbe noted that the team is also working on developing a design that would take the concept beyond open-hole SAS to enable single-trip completions with a gravel-packed well. DC