RFID technology provides cementing solution in drilling with liner applications
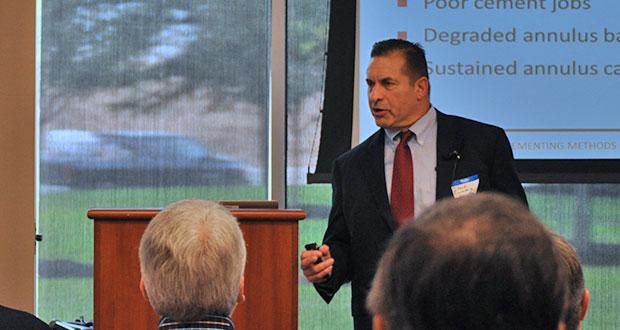
By Kelli Ainsworth, Editorial Coordinator
A radio frequency identification (RFID) cement port collar could prevent pressure surge and help maintain the wellbore integrity in challenging fields, such as Norway’s Valhall field, Steve Rosenberg, Global Drilling Reliability Manager for Weatherford, said at the IADC Drilling Engineers Committee Technology Forum on 11 November in Houston. “RFID port collars are versatile,” Mr Rosenberg said. “They’re remotely operated and closed with a contingency mechanical option. They remove the need for primary work string intervention, can be deployed for narrow pressure windows and long casings and liners.”
Drilling challenges in the Tor and Hod formations in the Valhall field include compaction, subsidence and depletion, Mr Rosenberg said. The pressure drops within the formation due to a shale overburden and chalk interface, which can cause stuck pipe when conventional drilling techniques is used. These challenges can be addressed using a drilling with liner installation. “Nine times out of 10, we see less fluid loss in the liner drilling applications, or for that matter, casing drilling applications, than when trying to drill the problem zone with conventional methods,” he commented.
Cementing in these formations has also been challenging. Cementing through the bit has caused lost circulation in the past, he said. Weatherford has adapted its fuse-based RFID activation system, which operates on hydrostatic pressure, to create RFID cement port collars to complement the company’s drilling with liner system. Cement is pumped through the RFID port collars, which are deployed above the depleted zone. “We’ll bypass the conventional primary cement job,” Mr Rosenberg said. “Instead, we’ll open some port collar above the depleted formation to get some cement, which could give you the wellbore isolation and hydraulic integrity to prevent sustained gas pressure seep.”
The total cementing solution Weatherford has designed for the Tor and Hod formations includes the RFID port collars, a casing swivel that rotates the liner during the cement job, and metal expandable annular casing packers. The system involves drilling the liner into the lost zone, until losses are sustained or the liner becomes stuck. At that point, the shut-off plug ball is dropped and displaced to the float collar. Then, the pressure is increased in stages to 4,500 psi. A predetermined pressure cycle is sent to open the port collar. When the collar is opened, there is no initial pressure surge to the formation, Mr Rosenberg said. This differentiates the RFID-operated port collars from other stage tools, he added. “Typically in mechanical and hydraulic stage tools, you’re going to see some residual pressure to the formation upon opening,” he said. “In tight pore pressure windows, this could compromise the formation.”
Once the port collars are opened, cement is pumped through the collars, rather than cementing through the bit.
The port collars can be positioned strategically within the formation “so you get the cement where you need it,” Mr Rosenberg said. “Instead of pumping three or four stage tools and having to do plug management and ball management, you can just operate everything from the surface.”