Baker Hughes builds mud motor for high-temperature geothermal drilling
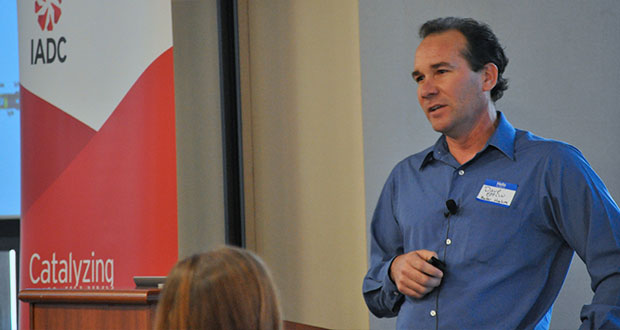
By Kelli Ainsworth, Editorial Coordinator
Baker Hughes has completed lab and field testing of a mud motor designed to operate in geothermal wells with temperatures up to 300°C, Dave Epplin, Project Engineer for Baker Hughes, at the IADC Drilling Engineers Committee Technology Forum on 11 November in Houston. The US Department of Energy (DOE) had asked Baker Hughes to design a steerable mud motor that could operate in a 300°C environment, drill through granite and complete a 50-hour mission, plus trip time. “Usually 200°C is considered high temperature for us,” Mr Epplin said, “so we’re looking at quite the leap to 300°C.”
The company eventually created the motor by changing design components in an existing mud motor. “We thought about what we needed to do to upgrade this to a higher temperature and what components need to be changed out,” he said.
The stator and rotor were the major motor components that were altered. The existing motor’s stator component was made from rubber, which does not typically withstand very high temperatures. So the design team decided to make the stator from metal, Mr Epplin said. “Now we have metal-to-metal contact between our rotor and stator,” he added. “However, if you don’t treat it, it’s not going to last very long.”
One of the important considerations in selecting a heat treatment was achieving a uniform hardness throughout the stator. “We really had to concentrate on uniformity,” he said. “Eventually we found a suitable heat treat that we could use where the hardness was uniform and it was efficient.”
Because both the rotor and stator in the motor would be made from metal, careful attention was paid during the rotor’s building process to make sure there was no bending; this ensures a uniform fit along the rotor/stator combination. Finding a sufficient rotor coating was also a challenge, Mr Epplin said. “With the metal-to-metal contact, it’s important that we have good wear properties on both the rotor and stator.” Baker Hughes tested more than 40 coatings at its technology center in The Woodlands, Texas, evaluating each for adhesion properties, abrasion and wear. In the end, the team narrowed the 40 coatings down to 10 for further testing in the field.
After the design phase, the motor was tested in a high-temperature test stand. The testing allowed the design team to examine the wear on the rotor and stator and how that wear impacted performance. The remaining 10 rotor coatings were tested in the test stand, as well.
The motor then underwent flow loop testing at Baker Hughes’ facility in Celle, Germany. “What they did was a flow range between 250 and 750 gal/min, which is about the range we’re looking at for our flow,” Mr Epplin said. The test generated 7,000 ft-lb of torque, well beyond the 4,000 ft-lb that the team had hoped to generate. “That was very encouraging,” Mr Epplin said.
An additional flow loop test, using a flow rate of 660 gal/min was conducted for 50 hours, the length of the target mission time. This test indicated that some of the coating characteristics and speed were lost over time. In addition, some chipping of the rotor coating was observed. “We knew we had to investigate a little more on this,” Mr Epplin said.
Following the flow loop test, the motor was tested in granite formation at a Baker Hughes facility in Oklahoma. Two vertical wells were drilled, one reaching 190 ft in 17.5 hours and another that reached 41 ft after five hours. Although chipping was observed, these runs were considered successful. To prove the motor was steerable, an additional run was done, and which a buildup rate of 6°/100 ft was achieved. “With the field testing, we were able to prove the steering and the durability through granite.”
Baker Hughes is currently working with the DOE to arrange a geothermal test of the motor, along with a drilling fluid and bit that are being configured for higher temperatures. “We have tools on the rack ready to go, the drill bit guys are ready, the fluid guys are ready. All the product is here,” Mr Epplin said.