Novel cutting technique helps with recovery of stuck drill pipe, BHA in Colombian well
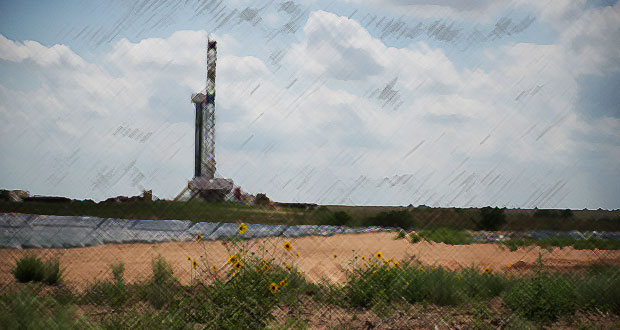
The 2023 SPE/ICoTA Well Intervention Conference in The Woodlands, Texas featured a presentation, given on 21 March, covering an operational challenge Proshale, Frontera Energy and Estrella International faced with uncontrolled well in which the companies utilized an abrasive cutting technique on coiled tubing to recover a stuck drill pipe and bottomhole assembly (BHA).
The well, which was drilled in the middle Magdalena Valley onshore Colombia, was planned to be drilled and completed in three sections, a 17 ½-in. hole with 13 3/8-in. casing down to 3,882 ft measured depth (MD), a 12 ¼-in. hole with 9 5/8-in. casing to 4,980 ft MD, and an 8 ½-in. hole with 7-in. casing to 5,377 ft. The drilling BHA of the last section included an 8 ½-in. PDC bit, eight ¼-in. float valves, a 6 ½-in. drill collar, a 8 ¼-in. stabilizer, float sub, and 6 9/16-in. drill pipe.
While drilling in the production formation at 5,123 MD, circulation was lost and the pipe became stuck. After several attempts to control the well, another issue appeared when the pumping pressure increased due to a plug in the inner of the drill pipe, possibly because of large debris in the control fluid.
“You’re drilling a well, you reach the formation and you get stuck. You’ve got to stop. You start seeing gas infill on the surface. Now you’ve got two problems – you’re stuck in the BHA and you’ve got a well control issue. Then, when you try to control the well, you get some lost control material that blocks your BHA. So now you can neither control your well nor get your pipe free. That’s the scenario we had to figure out,” said Nestor Mesa, Country Manager – Colombia, Ecuador and Guyana at Proshale.
Frontera and Estrella first attempted to free the drill pipe and BHA by cleaning out the lost control material inside the drill string and establishing circulation between the drill pipe and the open hole. When that did not work, the companies opted to use an abrasive cutting technology consisting of a slurry made of lineal gel and sand pumped through a motor that provided enough velocity and pressure to wear the steel on the drill pipe and ultimately erode it.
For the cutting operation, the BHA was placed at 4,716 ft, the theoretical depth of the middle of the last drill pipe of the drilling BHA. Due to the uncontrolled environment in the annulus, the choke at the surface needed to be actuated every time a pressure change was observed so that the overbalance could be conserved. Since the overbalance was needed, the selected rate for the job was 1.1 bbl/min.
The abrasive fluid was then pumped at 1.1 bbl/min, with pressures between 5,200 and 5,700 psi. Then the slurry was displaced with water until clean returns were observed. The BHA was pulled out of the hole and, once at surface, was inspected. Mr Mesa noted that a wear was seen in the cutter, resulting from the splash back of the slurry.
The rig then started to work the string with overpull and torque, getting the string free after 1.2 hours.
For the full version of this story, make sure to check out the upcoming May/June issue of Drilling Contractor.