NOV applies downhole expertise from oil and gas drilling to drive innovations for geothermal
New motor and pipe coating among tools targeting drilling in hot, hard rock, while optimized bit extends longevity in FORGE well
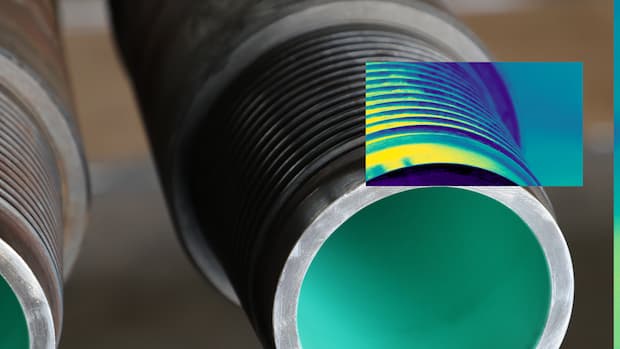
By Alexis Garcia, Danny Perez, Michael Adams and Jessica Stump, NOV
Geothermal energy is not only the largest potential source of renewable energy on Earth but also the least used. However, the geothermal market is rising as the oil and gas industry intensifies decarbonization efforts, and companies are increasingly considering geothermal energy as a crucial part of their emission reduction strategies. Rystad Energy projects that the installed capacity for geothermal power generation will almost double by 2030, reaching nearly 32 gigawatt-electric.
Conventional geothermal production techniques like hydrothermal are geographically limited to areas with natural underground reservoirs. These reservoirs have low temperatures, typically 200°C (392°F), limiting their power generation potential.
Unconventional geothermal resources are produced through enhanced geothermal systems (EGS), which rely on convection, and advanced geothermal systems (AGS), which are closed-loop systems that rely on conduction. These engineered reservoirs are drilled into abrasive granite formations with temperatures above 300°C (572°F).
Technology advancements are a key component to take geothermal energy from a minority player to a mainstream provider of safe, reliable, widely accessible heat and baseload electrical power. Since geothermal drilling costs represent roughly 50% of project development, the industry is looking for more economical ways to get the heat source using the latest technology, knowledge and skills transferred from the oil and gas industry.
NOV is taking a critical role in applying proven oil and gas drilling technologies to help advance and scale EGS and AGS. It is developing technologies that extend the longevity of the bottomhole assembly (BHA) components and sensitive electronics by maintaining drilling fluids at lower circulating temperatures and increasing the rate of penetration (ROP) in hot, hard rock while extending drill bits’ cutting structure durability to minimize bit trips and maintenance.
Insulative drill pipe coatings
Many BHA components and electronic sensors are not designed to endure the extreme downhole temperatures and harsh environments of geothermal and directional drilling applications. NOV’s Tuboscope business unit created a novel temperature control solution for geothermal drilling based on technology the company originally developed for the oil and gas industry. TK-340TC is an insulating drill pipe coating that keeps drilling fluids cooler to protect drilling tools from high-temperature-related failures.
The coating retains the same features that extend tubular life in aggressive oil and gas environments — reliable protection against corrosion, wear and deposit buildup — while improving hydraulic efficiencies to reduce pumping horsepower. It also includes technology that minimizes thermal conductivity, lowering heat transfer rates through the drill string, keeping drilling fluids cooler, and retaining more heat in the pipe on its way to the surface.
In a test well in New Mexico, a geothermal operator drilled 18,000 ft (5,486 m) into a reservoir with temperatures up to 250°C (482°F). With the insulated, coated drill pipe, the drilling fluids never surpassed 95°C (203°F), far below the operator’s target temperature of 120°C (248°F) to prevent BHA damage.
Moreover, the addition of NOV’s Tundra Max closed-loop mud chiller enhances temperature control, further increasing downhole tool life while minimizing HSE risks. The fully automated system features twin-plate pack heat exchangers and air-blast and chiller technologies to cool the drilling fluids continuously in a single pass. Plus, the system does not require a constant water source, increasing the efficiency, reliability and environmental sustainability of geothermal drilling operations.
Protecting downhole equipment
Geothermal applications are prone to downhole vibrations and drilling dysfunctions, which can be detrimental to directional and surveying tools. NOV is investing heavily in R&D as well as engineering development of durable and reliable downhole tools to extend intervals drilled.
Downhole motors with enhanced stator material provide robustness to the BHA by yielding high torque output and reliability. The Vector Series 55 downhole motor provides high weight on bit (WOB) capacity, high off- and on-bottom capabilities, a short bit to bend for better directional control, and high torque/high-temperature power sections.
The drilling motor includes a next-generation universal joint design with a robust mud-lubricated bearing pack, combined with NOV’s proprietary driveshaft design. This driveshaft design facilitates seamless torque transfer from the power section via flat faces at the pivot points for maximum reliability and high torque handling capacities.
The driveline incorporates a high-strength bearing mandrel supported by the mud-lubricated bearing stack. The bearing stack is built with customized spaces, which allow for precise preload on the thrust stack, maximizing the bearing assembly’s capacity to handle axial loads. There is also an option to add near-bit stabilization, which enhances build rates, stability and steerability.
Additionally, this motor, coupled with the new drilling Agitator systems and torsional vibration mitigation tool, boosts efficiency in the BHA by reducing tool failures associated with vibration and extending intervals drilled.
For closed-loop geothermal systems in which one or more laterals connect two vertical wells, NOV’s AgitatorZP system reduces friction and transfers more weight to the bit, increasing ROP and enhancing drilling efficiency. The tool generates friction-breaking axial forces downhole without the need to produce pressure pulses or additional pressure drop to the drilling system. With zero pressure drop across the system, mud pumps run more efficiently, reducing fuel consumption and CO2 emissions.
Its design enables operators to maximize operational flow rates in the deepest parts of the lateral sections while getting maximum output from the tool. Maintaining maximum flow rates provides significant operational improvements in long lateral sections, as they can maximize motor differentials to maintain the high ROP.
Meanwhile, the PosiTrack torsional vibration mitigation tool is designed to absorb and mitigate torsional vibrations above and below the tool while managing WOB. Using a patented pressure-compensated telescoping mechanism, the tool absorbs torsional oscillations and vibrations induced by stick-slip, high-frequency torsional oscillation, drill bit over engagement and inconsistent weight transfer. Rated to 230°C (450°F), the torsional vibration mitigation tool protects rotary steerable systems and measurement while drilling tools from vibrations and potential failure.
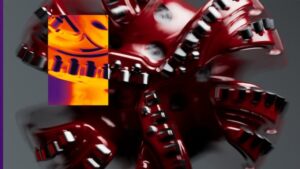
Optimized drill bits
Hard and abrasive formations are the hallmarks of igneous and volcanic rocks typically encountered in geothermal wells. When drilling in these formations, high WOB requirements generate frictional energy that can lead to cutting element damage and inhibit drill bit performance. NOV’s ReedHycalog business unit developed the Phoenix series of high-performance PDC drill bits with ION+ cutters to withstand harsh, high-temperature environments and drill faster and farther in hard rock with higher compressive strengths.
Phoenix drill bits reduce the risk of torsional oscillations through enhanced depth-of-cut control, which enables improved well placement precision while reducing wear and tear on equipment and minimizing the risk of tool failures and instability. ION+ PDC cutter technology comprises application-specific cutter grades that incorporate refined diamond feeds, nonplanar interfaces and thicker diamond tables, with enhanced thermal stability for increased durability and abrasion resistance.
Case study
ReedHycalog tested the drill bit selection process in the US Department of Energy’s (DOE) Frontier Observatory for Research in Geothermal Energy (FORGE) project in Utah. Initial discussions with the DOE on the nature of the geothermal drilling environment and anticipated challenges yielded the optimal drill bit design for the well.
Advanced cutter testing and failure analysis from previous wells helped identify the most suitable shape, diamond grade, bit body and chamfer type for the specific rock composition and drive type used. The resulting systematic improvements helped mitigate similar bit failure risks for more reliable drilling of longer intervals at higher ROPs.
Based on this upfront drill bit analysis and design work, ReedHycalog built a 9.5-in. Phoenix TKC83 drill bit for the FORGE well test. This test well mirrored a previously drilled well with a 300-ft (91-m) true vertical depth offset, a 5°/100-ft (30-m) curve, and a 65° tangent to reach a target zone with a bottomhole temperature ranging from 220°C to 230°C (428°F to 446°F).
Drilling followed a Limiter Redesign Workflow developed by researchers at Texas A&M University to identify and address factors that limit the efficiency of the well construction process. ReedHycalog stayed engaged during this workflow by analyzing digital data and dulls daily and redesigning bits to redistribute cutter wear, increase aggressiveness, and make iterative changes to cutter grade and shape.
This optimized design workflow improved bit longevity and ROP while reducing drilling time and costs. While the previous well logged a total on-bottom time for the drill bit of 312.3 hours, the enhanced Phoenix bit reduced on-bottom time by 63% to just 115.6 hours. Additionally, the new bit drilled through 500 ft (152 m) of granite with an average ROP of 109 ft/hr (33 m/hr) without the need for replacement or repairs.
Conclusion
By channeling resources into researching and developing purpose-built solutions that can perform in hot, hard rock environments, NOV aims to drive greater efficiencies, reduce costs and enable access to more complex unconventional geothermal resources, where precision drilling is vital. The level of investment and engineering efforts focused on pushing the limits of geothermal drilling technology highlights the critical role innovation plays in advancing and unlocking the true potential of this important renewable energy sector. DC
References
Rystad Energy 2023 Energy Transition Report – Geothermal Market Outlook.
“Oil and Gas Drilling Optimization Technologies Applied Successfully to Unconventional Geothermal Well Drilling,” Junichi Sugiura, Ramon Lopez, Francisco Borjas, Steve Jones, John McLennan, Duane Winkler, Matt Stevenson, Jordan Self, presented at SPE Annual Technical Conference and Exhibition, Dubai, UAE, September 2021.
“Drilling Practices and Workflows for Geothermal Operations,” Fred Dupriest and Sam Noynaert, presented at the IADC/SPE International Drilling Conference and Exhibition, Galveston, Texas, USA, March 2022..
Vector, Agitator, PosiTrack, Phoenix, ION+ and Tundra are trademarks of NOV.