MPD opens door to new well control options in deepwater
Closed-loop systems build track record in floating rig applications, reduce uncertainty in high-cost operations
By Bhavin Patel, Weatherford
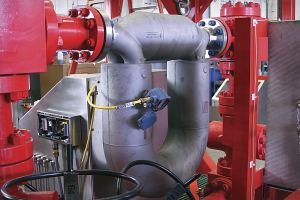
Managed pressure drilling (MPD) is recognized as a key enabling technology for drilling challenging wells. The ability to monitor and control volume in increments smaller than a barrel can help to resolve a wide range of downhole problems, such as kicks, losses, wellbore stability and drilling through narrow drilling windows.
The development of specialized marine rotating control devices (RCD) has extended the deployment of MPD methodologies to deepwater environments, where dynamically positioned floating drilling vessels present unique well control challenges.
Deepwater challenges
Deepwater equipment and the nature of the downhole environment can create well control complications. Many system elements, including subsea BOPs, riser limitations and high choke line friction, have a significant impact on well control procedures.
In addition, heave amplitude of the floating rig can add uncertainty to conventional kick detection methods, such as pit level monitoring, flow check and trip tank monitoring. This uncertainty is problematic in deepwater wells, where the narrow drilling margins between pore pressure and fracture gradient result in a lower kick tolerance and require that the volume of any wellbore influx is minimized as much as possible.
With increased water depths, longer choke and kill lines are needed to connect surface rig equipment to subsea BOP systems. Consequently, higher choke and kill line frictions limit the amount of pressure that can be applied on the surface. Higher choke line friction may cause circulation to slow and may result in more nonproductive time (NPT) related to well control operations. Additionally, higher choke and kill line friction can adversely affect the kick tolerance of the well.
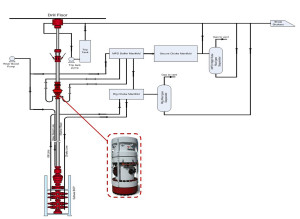
MPD technology
IADC defines MPD as “an adaptive drilling process used to precisely control the annular pressure profile throughout the wellbore. The objectives are to ascertain the downhole pressure environment limits and to manage the annular hydraulic pressure profile accordingly. MPD is intended to avoid continuous influx of formation fluids to the surface. Any influx incidental to the operation will be safely contained using an appropriate process.”
MPD methodologies are based on closed-loop circulating systems, which provide a unique capacity to better understand formation parameters, such as pore pressures and fracture gradients, and to better control the annular pressure profile. A closed-loop system circulates drilling fluid within a contained pressurizable system, in contrast to conventional drilling circulating systems that are open to the atmosphere. The loop is closed by an RCD installed atop the BOP or integrated below the tension ring as part of the marine riser system. The RCD contains and redirects the annular flow away from the rig floor and through an automated MPD choke manifold.
Weatherford’s SeaShield Model 7875 Below-Tension-Ring (BTR) RCD has been working to enable deepwater MPD. It is the first RCD made up below the tension ring and integral to the riser to support operations from dynamically positioned vessels.
Closed-loop advantages
Within a closed-loop system, changes in the wellbore pressure environment can be easily detected and managed. Real-time pressure and flow measurements can be used to manipulate surface backpressure to ascertain the desired annular pressure profile of the wellbore. The result is the ability to understand and manage downhole pressures.
The various MPD methodologies that have evolved from this ability have been further enabled and enhanced by the development of specialized software to monitor, analyze and control wellbore pressures. One of these, the constant bottomhole pressure (CBHP) method, can be particularly advantageous in deepwater wells where precise wellbore pressure control is required to walk the line between pore pressure and fracture gradient.

The ability of CBHP methods to dial-in and hold a specific downhole pressure without changing mud weight provides a high degree of control and a new first response to an influx or kick. The option to increase mud weight is still there, but backpressure can be applied precisely and long before a mud weight increase response can be implemented.
While conventional well control capabilities remain fully functional, MPD enables a response that may preclude their use and provides data for a more informed well control response. This improves safety and reduces the risks and costs associated with fighting kick/loss cycles, wellbore instability, stuck pipe and riser gas.
Automated detection and control
Automated influx detection and control using MPD is beneficial precisely because it detects influxes while they are very small and mitigates them quickly before they can escalate and create a larger problem. Unlike conventional well control, the automated MPD system does not entail the lengthy process of stopping circulation after an influx is detected, interpreting pressures and circulating the kick out of the well. Automated MPD systems enhance conventional well control systems on the rig, which remain in place and can be used when needed.
On land and offshore wells with surface BOP systems, automated MPD influx detection and control has proven effective in mitigating well control problems and the associated NPT. Similar successes can be replicated in deepwater environments where the RCD is integrated with the riser system. In these operations, MPD presents new capabilities and options, which involve planning to address design of components like the riser and slip joint, which may have a lower pressure rating.
Vital to this real-time influx and loss detection is the use of Coriolis mass flow meters and the principle of mass balance. These identify downhole events by measuring and comparing the volume and density injected into the well and returned from the well. In this process, a kick is indicated by outputs (annular returns) that exceed the volume of fluid pumped down the drill string; a loss is detected when output (returns) is less than the input. The flow meters provide mass flow rate, volumetric flow rate, fluid density and return mud temperature.
Benefits of automation
While MPD kick detection and control can be performed conventionally, automation provides the rapid response needed to mitigate small oscillations in downhole pressure that are often precursors to kicks and well control events. This is particularly critical in narrow deepwater drilling windows.
Accuracy and reliability are enhanced by using an automated MPD choke manifold integrated with instrumentation and a computer-based monitoring and control system. Using specialized algorithms, the control system can identify and distinguish between cyclic flow variation due to rig movement and influx entering.
Where uncertainty is high, this early kick/loss detection capability provides a significant advantage in the immediate detection and control of downhole geopressure events, including the well control risks presented by riser gas. In the closed loop, MPD provides a more informed well control response based on faster detection and mitigation.
The capabilities allow drilling operations to employ a flexible set of operational procedures that are more responsive to wellbore conditions. Based on better, timelier information, adjustments to drilling plans such as changes in mud weight can be performed at the drill site.
The MPD procedure applies new options to both prevention and mitigation procedures. To prevent an influx, the system adds real-time data for early event detection and identification. Annular pressure control provides a means of proactively managing pressure variations to prevent them from developing into a well control event.
Well control procedures
MPD reduces the occurrence of well control events and pressure-related wellbore problems by addressing two key challenges associated with conventional methods – the uncertainty of the pre-drill model and the inflexibility of the resulting well design and mud regimes. Uncertainty is reduced by very precise measurements of wellbore pressure in real time. This information is complemented by equally precise real-time control.
In conventional well control, once a kick is detected, the BOP is closed and the well is shut in. Pressure is interpreted, and the kick is mitigated and circulated out of the well. In contrast, an automated MPD system quickly detects the kick, immediately increases pressure sufficiently to stop the influx and safely circulates the kick out of the wellbore at normal drilling rates.
In land and platform applications where a surface BOP is used, the fully automated MPD response has proven effective in detecting, controlling and circulating kicks out of the well. In these applications, the driller’s method is typically implemented to circulate the kick out at normal rates. Maximum allowable annular surface pressure (MAASP) is determined by the formation’s fracture limit or the RCD’s pressure rating.
At normal circulation rates (during drilling), bottomhole pressure (BHP) is higher than BHP while circulating at slow circulation rates (SCRs). Higher BHP caused by frictional pressure losses helps maintain a downhole pressure profile above pore pressure. It also means that lower backpressure on surface (to maintain same BHP value) provides bigger margin to keep it under MAASP.
Automated well control in deepwater
Automation of deepwater MPD operations has several advantages. First, the closed wellbore eliminates inaccuracies due to pit level changes caused by factors such as crane movement. Second, aboard drillships or semisubmersibles, flow variations due to rig movement may make influx detection harder. Third, sophisticated algorithms can help analyze flow anomalies despite flow variations due to rig movement. Additionally, precise choke control ensures minimum variation in bottomhole pressure. The MPD system employs sophisticated algorithms to screen out false alarms and accurately detect and control influx.
Due to narrow drilling margins and tight-clearance casing programs typical of deepwater wells, the kick tolerance is considerably smaller. During conventional well control, after the kick is detected, the well has to be shut in on the subsea BOP. Under this situation, the effect of choke line friction imposes increased limitation due to higher choke line friction.
With an MPD system, influx can be circulated out at the full drilling circulation rate. This minimizes the requirement of excessive surface pressure as annular frictional pressure losses are used to attain required BHP. Closed-loop technology enables effective use of wellbore hydraulics to ascertain required downhole environment.
Figure 3 demonstrates a kick tolerance plot for a deepwater well. The X-axis has kick intensity (in ppg equivalent) while drilling, and the Y-axis has kick volume (in bbls). As seen from the plot, volume of a kick that can be circulated out at a given kick intensity or kick tolerance is lowered due to choke line friction. With application of MPD, smaller kicks can be safely circulated out through the riser. This provides better kick tolerance due to the elimination of choke line friction.
Existing equipment in deepwater applications can pose challenges to applying automated influx detection and control. Riser slip-joint limitations might have a lower rating than the MAASP. This could limit the amount of casing pressure that can be applied during influx control and circulation. Due to advances in riser technology, risers with higher pressure ratings are becoming more readily available.
Successful deepwater MPD applications
Deepwater MPD, although a relatively new application, already has a history of 19 successful wells drilled from floating drilling vessels. In many of these applications, automated kick detection and control have successfully mitigated deepwater pressure challenges.
The development of specialized RCD technology that integrates with the riser system clears a significant hurdle in applying MPD to a broader scope of deepwater wells. As drillships and semisubmersibles are fitted to provide closed-loop drilling capabilities, the deployment of MPD will play an increasing role in enhancing process safety and efficiency and providing the ability to drill increasingly difficult deepwater wells.
SeaShield is a trademark of Weatherford.
Improved safety through enhanced influx detection of formation fluids.
Powerful Ultrasonic sensors for flow measurement and influx detection are here to find:
http://de.slideshare.net/fmj2/experimentalstudy-measurement-of-sonic-speed-of-drilling-muds-under-shear-stress