Marcellus project demonstrates potential to power land rig using fuel with up to 20% hydrogen
By Stephen Whitfield, Senior Editor
From using dual-fuel generator solutions to utility power to battery energy storage systems, onshore rigs have become a hotbed of innovation as both E&Ps and drilling contractors strive to decrease their emissions footprints. Now, hydrogen is emerging as another potential solution to eliminate Scope 1 greenhouse gas (GHG) emissions from drilling.
In 2023, Patterson-UTI, EQT and Cat Oil & Gas demonstrated the use of hydrogen fuel in a dual-fuel engine on a land rig in the Marcellus Shale. The project proved that existing dual-fuel engines can support a blend of up to 20% hydrogen and 50% natural gas, along with diesel, without requiring any additional hardware modifications or adjustments to the rig’s control system.
“We’re starting a conversation around taking hydrogen and putting it into a drilling application,” said Will Kernan, Oil and Gas Product Strategist at Cat. “As we move forward, there’s going to be a continued effort to look for new ways to decarbonize our rigs, but we need systems that will allow us to do that while not sacrificing productivity on the rig, the mobility of the rig, or the ability to provide the significant amounts of power that a rig needs.”
Mr Kernan discussed the project, as well as the effects of hydrogen gas on engine emissions and performance, at the 2024 IADC/SPE International Drilling Conference in Galveston, Texas, on 6 March.
“Hydrogen is not some new-age fuel. It’s been around for a long time, but it’s a new way to reduce carbon. We should think of it in the same vein as a carbon capture system, or any system that allows you to reduce your fuel consumption or your run time. While there are significant challenges to storing hydrogen and moving it, once it’s on site it has the potential to meet all the requirements for powering a rig. That was really the foundation for this demonstration.”
The rig selected for the demonstration was a super-spec 1,500-hp land rig with three Cat 3512C dynamic gas-blending (DGB) engines rated for 1,476 hp. While all three engines were equipped with dual-fuel systems capable of blending up to 70% natural gas, only one engine would be used with a hydrogen blend in this test. The goals of the project were to test the engine’s performance with the hydrogen blend to understand the capabilities and limitations of existing equipment and quantify any changes in exhaust emissions and fuel efficiency.
While it was expected that the GHG emissions would decrease by at least an amount proportional to the percent of diesel fuel displaced, Mr Kernan said that it was unclear whether adding hydrogen would result in additional efficiency gains through the improvement of combustion within the cylinders.
Additionally, the project represented an opportunity to learn about the transportation of hydrogen and its safe handling on a rig site. Given that hydrogen is highly combustible – it requires only 10% of the energy required for ignition compared with natural gas – Patterson-UTI and Cat undertook several safety measures to prevent leakage.
The test’s maximum blend ratio was set at 20% hydrogen by volume to limit the amount of hydrogen on site. Hydrogen tape, which changes color when exposed to hydrogen, was used on all seals to detect leaks. The engine was operated outdoors with no enclosure, mitigating the risk of ignition. A hydrogen gas detector was also installed in the engine’s crankcase to monitor for any accumulation of hydrogen resulting from blowby gases.
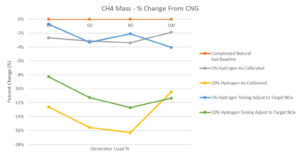
Offsite demonstration
Before conducting the rig demo, a pre-test demonstration took place over three days at a Cat dealership encompassing 22 hours of engine run time. The tests utilized approximately 34,000 standard cu ft of natural gas and around 5,150 standard cu ft of hydrogen. Testing began with a performance comparison of gas displacement with dual-fuel engines, contrasting diesel blended with natural gas and diesel blended with both natural gas and hydrogen.
In anticipation of hydrogen’s extremely low ignition energy, which makes it ignite inside the cylinder earlier than other fuels, the team had made a change in the combustion timing for all fuel components. The engine was monitored to determine if additional calibration was needed due to the increased hydrogen volumes. Other than the combustion timing, no other adjustments were made to the engine’s components or operations.
The dealership, Cleveland Brothers, test utilized two blends of natural gas and hydrogen. The first, a blend of 20% hydrogen, 50% natural gas and 30% diesel, achieved a 50% maximum gas substitution rate during the demonstration. The second, a blend of 5% hydrogen, 65% natural gas and 30% diesel, saw a peak substitution rate of 70%. Performance for each blend was measured against a baseline performance with a fuel blend of 70% natural gas and 30% diesel. These blends were the same as what was later used in field testing.
The emissions impact of the hydrogen fuel was also evaluated during the pre-testing. Compared with the baseline performance of diesel blended with natural gas, CO2 decreased by 2% to 4%, depending on the generator load. Mr Kernan said this decrease was roughly equivalent to the energy displaced by the hydrogen.
Additionally, the 5% hydrogen blend achieved a 3% reduction in methane emissions compared with the diesel/natural gas baseline, while the 20% hydrogen blend resulted in a 12% reduction in methane. Mr Kernan credited these drops to hydrogen’s high flame speed. “Hydrogen is a very fast-burning fuel. It is very easy to ignite, and that helps remove the combustion fuel in the harder-to-reach parts of the cylinder, as well as some of the methane that gets trapped in those parts. You’re also using less gas, so there’s less of an emissions impact there.”

Results from field testing on the rig
The engine used in pre-testing was then installed at the rig site and integrated into the rig’s power management system alongside the existing generators for a three-week field test. The main goals were to confirm that the rig could operate with the hydrogen fuel and to measure the economic impact of using hydrogen on the rig.
The operator, EQT, chose “Battle Phrog” in Greene County, Pa., as the test site because it was a newbuild site without existing production, Mr Kernan said. To further ensure secure onsite operations, EQT equipped a generator with a hydrogen monitor with an audible alarm. Certarus Energy, the hydrogen and CNG supplier, installed hydrogen and CNG monitors inside their respective processing skids. These monitors would initiate an emergency shutdown in the system if any issues were detected.
Two wells were drilled for the field test, with one of the rig’s three Cat 3512C DGB engines using fuels consisting of hydrogen blended with CNG – the Battle Phrog 4H with a 12% blend and the Battle Phrog 2H with a 5% blend. Those two wells were measured against Battle Phrog 6H, which utilized the same engines, but with all of them using a blend of diesel and natural gas.
The field test confirmed the performance of hydrogen as a viable fuel across a series of steady-state and transient operational test points. The use of hydrogen did not negatively impact the rig’s operations at any point during the field test, Mr Kernan said. However, data from 2H and 4H indicated that hydrogen contributed between 2-3% total energy to the rig for each well, which also indicated a 2-3% decrease in CO2 emissions compared with 6H. A negligible change in engine efficiency was also observed during the test.
A financial analysis conducted after the demonstration showed there was a noticeable increase in daily fuel operating costs, however. “Hydrogen is a much more expensive fuel compared to natural gas, especially in the United States where natural gas is relatively abundant. A kilogram of hydrogen can be five to eight times more expensive than a kilogram of natural gas. It has a very large impact on the total fuel cost,” Mr Kernan said.
Since the demo’s completion, the companies have been reviewing potential marginal adjustments that could be made to reduce other costs associated with using hydrogen on the rig. For instance, he noted the high cost of the equipment needed for processing and blending the natural gas and hydrogen. The companies are looking at the viability of using a pre-mixed natural gas/hydrogen fuel that can help reduce that equipment cost.
“How you’re bringing the hydrogen to site has a very large impact on what your total fuel cost is going to be. You’re making a significant impact to your truck traffic when you look at how much hydrogen you need to transport, but also, we need to look at things like the vaporization and the onsite storage for liquid hydrogen, which both have a significant equipment costs.” DC