Maintaining pressure key to casing integrity
By Linda Hsieh, Managing Editor
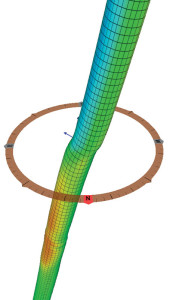
For drilling contractors, asset integrity is most strongly linked to the reliability and performance of drilling rigs and the equipment onboard those rigs. However, many other aspects – particularly downhole – make up critical pieces of the overall well integrity puzzle.
“For casing integrity, the primary concern is pressure integrity – making sure that the casing functions as a pressure vessel that provides a pressure conduit from the surface to the target,” Dr Trent Kaiser, Principal Consultant at Noetic Engineering, said. “The primary challenge is constructing the well – how do you design, assemble and install the casing while maintaining that needed pressure integrity to operate the well.”
A build-up of annular pressure between different casing strings or between the tubing and casing is one potential failure scenario. Drilling wear from inside the casing can also be a problem. “Corrosion is the other aspect of it. Over the life of the well, exposure to wellbore fluids might attack the casing wall and compromise wall thickness and its pressure integrity as a result.”
One of the most common issues surrounding casing integrity, however, is well deformation, Dr Kaiser said. If the operator can’t access deeper parts of the well to service it, the value of the well is quickly compromised. “We’ve seen time and again just how much deformation these wells can tolerate and still maintain their pressure integrity,” he said.
Dr Kaiser cited a casing integrity management program by a Canadian petroleum company where caliper logs are run after every thermal cycle in the well. “They monitor the deformation and have developed criteria that capture the deformation tolerance of the casing. Where in much of the world, you might recognize the deformation and think that’s a reason to shut-in the well, they are actively monitoring that definition and identifying more realistic limits of deformation to guide the management of the well and their choices about abandonment.”
Especially with the high level of activities in unconventional development in North America, casing integrity is a growing challenge. With unconventionals, “they have to really stress up the reservoir in order to make it productive. They stress it by either fracking or, in oil sands, by thermal stimulation. These introduce stresses and deformation on the wells that are quite challenging.”
In most wells, the worst casing loads are imposed during well construction, he said. “But in unconventional wells, the subsequent operation of those wells impose much higher loads than what the installation loads are.”
He believes that the industry will soon have to more specifically address casing deformation as a result of practices required for unconventional resources. “I think it’s something that the industry is just now coming to recognize as an issue. There is a big opportunity here to learn from failures and apply them to future well construction and future casing integrity developments.”