Islands of automation won’t drive significant drilling optimization; technology must be integrated into rig’s controls architecture
More cross-licensing of intellectual property within drilling industry can lead to more standardization, widespread adoption of new technologies and processes
By Linda Hsieh, Managing Editor, and Alex Endress, Editorial Coordinator

Mark Mitchell is President of Oil and Gas at AFGlobal Corp.
What is the industry doing to make the deepwater market, which has been deeply hit in this downturn, more economically viable again?
We’re seeing much closer alignment – not just between operators and their suppliers but within the supplier base, as well. They’re working more closely together across the board, and some formal alignments have actually resulted in new companies. These are structural changes that will drive the industry toward standardization, which I see as the single biggest opportunity to drive out cost.
Particularly in deepwater, there has always been a preference for bespoke designs – even if the operator was doing something that had been done many times before. You think about things like subsea production architecture, and there’s no reason there can’t be a good template that can be used for multiple projects. However, what gets done on one project always seems to get reengineered and redone for the next one.
In the future, I truly think we’re going to see a sea change when it comes to standardization. This downturn has changed people’s perception of the business. The old thinking that you have to make or design everything on your own is changing. Operators and contractors are much more open to collaborating.
In terms of equipment, where do you see the most opportunities for more standardization?
I see an excellent opportunity to drive more standardization in deepwater MPD. We are still fairly early in the adoption curve, and standards are still being developed. Especially with some drilling contractors looking at fleetwide conversions to MPD, that’s the kind of scale that can really push standardization in the way equipment is designed and deployed. We’re having these discussions with contractors right now.
What is the current standard for MPD conversions?
Right now it’s the riser gas handler with a rotating control device (RCD). The base building block is the riser gas management system, which gives you the means to put in an RCD and then bring a manifold onboard. Of course there’s also a lot of work involved in laying additional pipework on the rig.
What are potential ways to reduce the cost of MPD conversions?
The biggest way to reduce cost is to make those conversions on the contractor’s timetable. Do it when the rig is dockside for repairs and maintenance. Plan the installation so that it doesn’t impact contracting. If contractors plan things far enough in advance, it can be done in a much more cost-effective way.
I also want to emphasize that MPD is not an all-or-nothing concept. We’ve taken a modular approach and developed our kit in building blocks so that a client can tailor it, not only to his tendering needs but also to his capital budget. You can have the entire kit, or perhaps you just buy a riser gas handling system so you’re ready for a service company to go out and perform their work, as needed.
Who’s driving MPD conversions -— operators or contractors?
Most of the conversions to date have been driven by the operator. However, we’re starting to see rig contractors purchase kits on their own so they can be more competitive. There are contractors who already have two to three rigs that are MPD ready in their fleet. Moving forward, I think that will be the majority of what we see – rig contractors buying and installing equipment ahead of time.
Eventually I think every deepwater drilling contractor will earmark a certain amount of rigs in the fleet to be MPD ready. Some contractors are beginning to view MPD like top drives. It’s a game-changing technology for reducing nonproductive time, and it allows you to participate more effectively in incentive-based drilling opportunities.
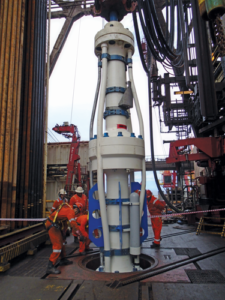
How will the roles of drilling contractors change as they take services like MPD onto their rigs?
It’s not just MPD. I think contractors will continue to take a bigger role in the well construction process, whether in deepwater or on land. On land we’ve already seen some contractors providing services like directional drilling and casing running. In deepwater we’re seeing contractors who want to take on a more active role downhole. Many of the services that have traditionally been provided by service companies could eventually be provided by the drilling contractor.
We’ve seen bits and pieces of this in the past, but we’re now seeing structural changes that will stick around well after this downturn is over.
In terms of MPD specifically, each drilling contractor will have their own ideas about having their own rig crews provide MPD services. It will likely just be a minority of contractors who will want to have the reservoir engineering component of MPD as part of their offering, but there will definitely be interest, especially in deepwater.
More and more automation is being adopted at the rig site. How do you envision MPD fitting into the highly automated well construction process of the future?
MPD is a natural fit into the automation evolution. Automated MPD is already here. A system with automated MPD capabilities can automatically make adjustments on the fly in a closed-loop controls system. We don’t need as much human intervention today, but the majority of the time we are still not running as automated as we could be. This is simply because people are still more comfortable with the human quotient in MPD. As an industry, we have a tremendous amount of technology and real-time data that can be applied to optimize the entire drilling process. To what extent we’re ready to hand over the keys to complex sets of algorithms is yet to be determined.
The human interface is still a challenge. As an industry, we need to agree on the decision-making process and where the hand-offs should occur, which means we need to create rules around those interactions.
Will that be driven by the operator?
It has to be accepted by the operator, but it really goes back to the drilling contractor. The rig is the nexus where all these things come together, and I think you will see the contractor taking much more interest in these processes. We’re going to see a trend where the operator will set the objectives, but it will be the drilling contractor out there fulfilling those objectives. It’s my belief that contractors are going to step up and take a much bigger role going forward.
What we can’t have are islands of automation on a rig. It all needs to be integrated into the rig’s controls architecture. Even if some bit of kit is technically fully automated, if it doesn’t fully interact or talk to any other kit, you won’t achieve much with it. MPD systems currently have their own separate controls on the rig. You try to get it as close to the driller as you can, but it’s not integrated into the chair. We’re working now to get the kit integrated into the rig itself so you can put all the benefits of MPD at the fingertips of the driller. That’s the point of MPD integration where we will see real drilling optimization benefits.
What are the challenges to this type of integration?
In terms of MPD, a lot of new technologies from OEMs and service companies are proprietary. Each company designs the equipment a bit differently, and you end up with a lot of varied offerings. This means MPD kits can be quite disparate. What will drive standardization is this current trend of manufacturing and selling the big capital pieces of MPD equipment to contractors. The service companies will be able to go out and work in a lot more places more quickly, and it places the capital intensity where it needs to be.
Technology development and adoption is still slow in our industry, as we can see with MPD. What can be done to speed up that cycle time?
One of the biggest impacts that can be made is through intellectual property (IP) sharing. As an industry, we need to be more willing to license IP where it makes sense, especially where it can lead to more standardization and more widespread adoption of new technology and new processes. We see a lot of other industries that are very good at cross-licensing. They’ve recognized that it’s very difficult for deep market penetration and to arrive at a standard if everyone keeps their IP locked up. In our own industry, there are many technologies that would be a much more widely adopted if licensing played a bigger role.
I’m not implying that cross-licensing is the answer to all of our technology issues. I just think we can be a bit more open and thoughtful.
So where do you think R&D investments should be directed right now?
It goes back to integrating more equipment and services with the drilling rig. We need to think about the rig and everything that goes on it as a drilling factory. We need to reduce hand-offs – interfaces that are disruptive to the drilling process. There’s an interface every time an activity has to be stopped and rigged down before another activity can start. If we can reduce such hand-offs, we can make the drilling factory more efficient. That’s where we need to concentrate R&D.
For instance, our engineering group is not trying to invent the next great widget that no one has seen before or that will operate independently of all of these things. All of our engineering is focused on enhancing and improving activities on and around the rig and how our kit interfaces with the rig.
Automation and closed-loop systems have been the focus of what we’ve discussed here. If that’s the future of our industry, how do you think the role of humans at the wellsite is going to change?
Humans are not in any danger of being displaced with a fully automated rig where there’s no human interaction. However, we will continue to take crews out of hazardous situations using automation. I think we all agree on this point.
The challenge is that we have an urge to stop an automated process so that a human can make a decision that may already be made in the automated system. We just don’t trust the system to make the decision. We build all these great digital machines, yet we keep putting an analogue filter in between all of them. The biggest change in people’s roles will be where and how we allow decisions to be made. DC