Industry seeks ways to understand and fight elusive downhole enemies
Dysfunctions like HFTO can be hard to detect, but companies are identifying mitigation solutions through sensors, bit studies, predictive software
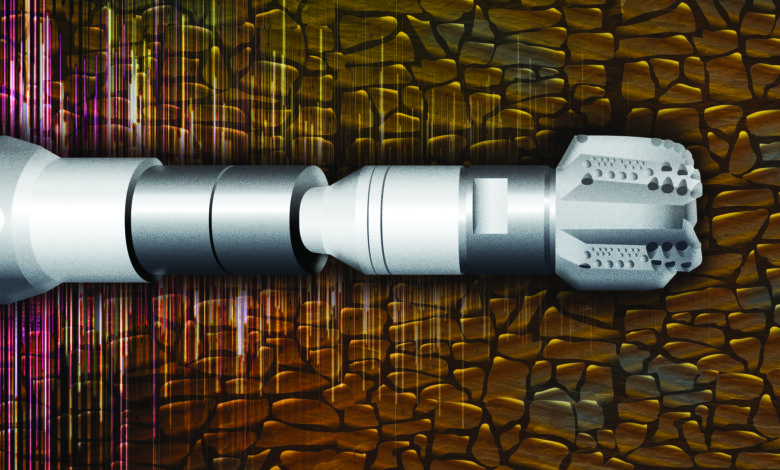
By Stephen Whitfield, Associate Editor
In operators’ quest to maximize the value they get from each well by drilling longer and more complex bores, they’re also having to deal with a higher risk of encountering downhole dysfunctions, such as high-frequency torsional oscillation (HFTO) or lateral shock. Such events can potentially lead to damage in the BHA and other downhole tools, adding time and cost if they have to be pulled prematurely. Understanding the nature of these dysfunctions has, therefore, become more important than ever.
“In the industry, we’re always chasing ROP, trying to get the best drilling performance we can. But getting the best performance is not always tied to ROP,” said Raju Gandikota, Co-Founder and Chief of Innovations at MindMesh, an engineering software and technology development company. “It’s about managing the tool life, having vibration control and maintaining the effectiveness of your tools so that you can actually reach total depth.”
To better anticipate downhole dysfunctions and stave off their more destructive effects, some companies are testing different sensor types and various placement to see how they can more effectively detect HFTO, while others are studying the relationship between different bit designs and HFTO. Predictive software is also poised to provide the industry with more information needed for better decision making to prevent or mitigate downhole dysfunctions. While these approaches differ, the common goal is to understand the source of damaging vibrations so that downhole tools can become more durable and stay in the hole longer.
“How many times does a customer come to us and say, hey, we are losing expensive downhole tools?” asked Prabhakaran Centala, Engineering Manager for PDC Cutter Technology at NOV. “If they bring these failures to the table, then we have to figure out the best way to mitigate that. There are so many intricate details that can help us bring about a different level of performance altogether.”
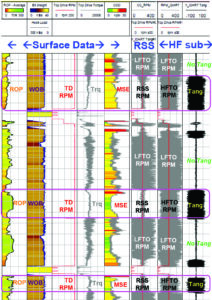
Understanding and identifying HFTO
HFTO, which is characterized by torsional oscillations of the drill string or BHA that fall within the 100-300 Hz frequency, can be particularly difficult to measure and quantify compared with other types of vibrations, like stick/slip and bit bounce.
If left undetected, HFTO can lead to downhole tool failures, such as twist-offs, connection cracks in the BHA, washouts and premature bit dulling. “Nowadays, rotary steerable tools are much more sensitive, with moving mechanical parts and electrical components. Because of this sensitivity and their complexity in nature, we’re more susceptible to tool failures because of HFTO,” said John Rodriguez, Drilling Engineer at Occidental Petroleum (Oxy).
To attain a better understanding of HFTO, Oxy conducted tests in the Delaware Basin from 2018 to 2020 utilizing commercially available high-frequency downhole sensors in various positions along the BHA, as well as an anti-stick/slip tool. These tests also aimed to determine the ideal sensor types and placement of the sensors for identifying HFTO.
“When you’re losing the BHA downhole, that’s something that’s worth millions of dollars. These types of serious NPT events prompted us to investigate HFTO. We wanted to do some field testing to get an understanding of what was going on downhole,” Mr Rodriguez said.
Oxy has shared results from some of the tests that were conducted. In these tests, it looked at three sensor types – a high-frequency “puck” sensor with a vibration sampling frequency of 800 Hz placed in the shank of a 6.75-in. bit; a high-frequency sensor with a vibration sampling frequency of 1,024 Hz that was designed to be run above the RSS on a directional BHA; and an ultra-high-frequency sensor (vibration sampling frequency of 1,500 Hz) installed in a carrier sub run above the MWD.
The data from each sensor was measured against data from the surface. However, the sensors were not necessarily measured against each other in every test. Some tests were conducted to measure the performance of downhole tools that could help mitigate HFTO.
One test compared the performance of the low-frequency and high-frequency sensors on a 6.75-in. BHA with no anti-stick/slip tool. While the low-frequency sensor in the RSS recorded consistent RPM throughout the test, ranging between 100-200 RPM, the high-frequency sensor that was placed above the RSS measured significantly greater variations, between 0-400 RPM, on multiple occasions. Each variation in RPM coincided with an HFTO event recorded during the run, the last of which led to a tool failure. Meanwhile, the surface drilling data stayed consistent throughout the run. The mechanical specific energy (MSE) remained low, top drive torque remained steady, and top drive RPM stayed constant at 175 RPM.
The results from this test led to two understandings, Mr Rodriguez said. First, vibration data from a standard sensor in the RSS cannot capture HFTO events, and second, HFTO cannot be detected from the surface. “HFTO happens within a pretty short time frame and distance. It doesn’t travel all the way to the surface like LFTO. Because it’s a high-frequency event, the travel distance is just within the BHA. We saw in our data sets that you can’t identify it in real time while drilling. Your MSE and your ROP don’t really change. You could be drilling fast and see stable drilling indicators at the surface, but downhole it could be an entirely different picture.”
Another test measured the high-frequency “puck” sensor in a 6.75-in. bit shank and compared it against surface data. For this test, Oxy utilized a 4.75-in. motor above the RSS in two separate runs, one with and one without an anti-stick/slip tool, a device placed above the RSS/MWD and below the motor that is designed to prevent excess torque from traveling up the drill string.
Mr Rodriguez noted some additional findings from this test. First, the high-frequency sensor in the drill bit detected instances of HFTO early in the first run, although the tangential accelerations were less than 20G-acceleration. The bit was pulled for slow ROP and was damaged beyond repair once tangential accelerations exceeded 100G-accelerations.
Second, the anti-stick/slip tool used in the second run reduced the level of tangential accelerations measured at the bit, where tangential accelerations averaged less than 20G-acceleration for the entire run. This indicated that the anti-stick/slip tool could help reduce the level of tangential accelerations at the bit. While this does not eliminate HFTO, it can help mitigate its most damaging effects.
Oxy said it paused this series of HFTO testing in March 2020 following the oil price downturn but plans to resume this project in the future.
Finding links between HFTO, bit features
For the past couple of years, NOV has been exploring the relationship between bit design and HFTO, hoping to eventually create a new bit design that could help minimize the downhole dysfunction.
In particular, the company worked to identify what links observable HFTO with bit design metrics or features, developing tests based on four hypotheses that came out of previous field observations and other studies on HFTO. The first theory NOV considered was around worn cutters. As worn cutters are more susceptible to low-frequency torsional vibration, they could potentially be more susceptible to HFTO, as well.
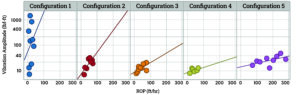
Second, tracking PDC cutters are less efficient than non-tracking cutters, primarily because of the shape of the cut that the PDC makes when interacting with the rock. “Tracking” and “non-tracking” cutters refer to the placement of a backup row of PDC cutters directly behind the primary cutters. These secondary cutters, which help enhance the durability of fixed cutter bits, can be placed either at the same radius as the primary cutters (tracking) or in between (non-tracking).
A tracking cutter will engage with the formation over a long portion of the cut shape with a small depth of cut (DOC); a small DOC is associated with a high MSE. A large shear length to shear area ratio indicates an inefficient cutting shape with a small DOC and potentially contributes to HFTO.
Third, diamond-impregnated secondary components could help reduce vibratons. NOV noted that overly sharp, freshly ground PDC cutters are more likely to cause the vibrations indicative of HFTO compared with cutters that have been slightly used. However, the company noted no instances of HFTO when using impregnated bits, even though they commonly drill at very small DOC in hard rock. This was because rock fails through grinding, rather than shearing, as the cutting face of the impregnated bit slides against the rock with little risk of overengagement.
Part of NOV’s testing studied whether it was possible to manufacture cylindrical components shaped like a cutter made from the same material as the impregnated bits and placed in a secondary cutting location on the face of a PDC bit. This combination of shearing and grinding rock failure could mitigate HFTO.
The fourth hypothesis pertains to the effective back rake angles of the cutter placement on the bit. As the effective back rake angle increases, it tends to limit the DOC and can lead to a greater risk of HFTO occurring.
To test these theories, NOV conducted several experiments at its pressurized drilling laboratory in Conroe, Texas, over the past year. Two 216-mm bits with seven blades and 16-mm cutters were used. The bits were tested on rock cores under different drilling conditions to simulate field tests.
Bit A had 32 face cutters and 18 tracking secondary cutters. Each element of the bit design was chosen to test the theoretical connections between bit design and HFTO: cutter wear, the ratio of shear length to shear area, the choice of secondary cutter material and effective back rake angles. The back rake angles on the face of the cutter were between 19° and 20°. When first used, this bit had wear as received from field testing; the cutters were worn, and the gauge pad had suffered some wear.
Bit B, a new design, had 30 face cutters with the shape alternating between chisel and full round. Further, the cutters were laid out in a star spiral order, with the shape alternating between chisel and full round. The alternating shape and star layout was chosen to improve the ratio of shear length to shear area.
There were 10 secondary cutters in Bit B made from the same material as a diamond impregnated cutter. These secondary cutters were placed in a tracking location. The back rake angles of the face cutters varied from 15° in the cone to 20° near the gauge.
The bits were tested in five separate configurations. The first configuration was used to examine the effect of bit wear on HFTO, with successive configurations changing different elements of the bit to isolate which parameters had the most significant impact. Configuration 1 involved the use of Bit A directly from the field, already having dull and broken round cutters on its primary and secondary blades. Configuration 2 involved the replacement of the dull and damaged cutters on Bit A with undamaged 16-mm round cutters on the primary and secondary blades. Configuration 3 involved the use of non-planar cutters to increase back rake angles. Configuration 4 involved replacing the secondary cutters with cylindrical diamond impregnated material. Configuration 5 involved the use of Bit B.
Each configuration was tested at 10 separate combinations of weight on bit (WOB) and RPM. Before testing a configuration, the hole was prepared by drilling 130 mm into the rock to generate the bottomhole pattern, ensuring that all tests start with similar formation engagement.
Testing of Configuration 1 compared with Configuration 2 showed that worn cutters increase the risk for HFTO. At 100 RPM, the new cutters in Configuration 2 led to a 53% reduction in the amplitude of HFTO. The disparity in amplitude increased as RPM decreased – Configuration 2 saw an 82% drop at 75 RPM and a 97% drop at 50 RPM. This indicated that the PDC cutters should be chosen for longevity and durability in areas where HFTO is a concern.
Configuration 3 had a 39% decrease in HFTO amplitude compared with Configuration 2, indicating that higher back rake angles – the angles of the face away from the end cutting edge of the drill bit – can reduce HFTO for a given WOB and RPM. However, the average ROP also increased 23% from Configuration 2 to Configuration 3. The use of diamond impregnated cutters (Configuration 4) in place of the secondary cutters showed a 12% reduction in amplitude and an 11% increase in ROP.
The differences in back rake angle proved less significant than the other factors tested in determining the risk for HFTO. The data did not support the theory that increased back rake angle would worsen HFTO – in fact, Configuration 3 showed the 39% decrease in HFTO amplitude despite having an increased back rake compared with Configuration 2.
The results from the study indicated that the optimal bit design to limit HFTO vibration magnitude requires the use of durable cutters with either non-tracking secondary PDC cutters or diamond-impregnated cutters and a low back rake angle.
While NOV said it has no imminent plans to turn the learnings from this study into a new product, the company’s ReedHycalog business unit does hope to have a roadmap by the end of this year for developing a product line of bits designed specifically for mitigating HFTO. “Our next goal is to develop an agenda where we can go to our customers and tell them how we’re going to bring about a bit that will help the industry reduce HFTO at the source. We don’t have a product line solely dedicated to HFTO right now, but we do have an agenda,” Mr Centala said.
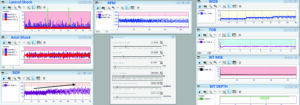
Predicting dysfunctions with a digital twin
Computer-based well planning and drilling dynamics modeling is a standard practice for improving drilling performance. However, it has its limitations.
Primarily, conventional well planning software produces static models of the downhole, which are not useful in analyzing downhole behavior over a period of time. That is key to identifying the risk of dysfunctions, said Mr Gandikota of MindMesh. “What we are missing with the static model is the interaction of the drill bit cutting rock, and how the BHA interacts with the hole while we’re drilling. Can we take a snapshot and use that to explain a movie that’s two hours long, or 10 days long? That’s what we’ve been trying to do.”
Last year, MindMesh updated its RiMo digital twin platform to incorporate real-time prediction of drilling mechanics and downhole dysfunctions. RiMo is a time-domain model, meaning that it analyzes the behavior of the BHA and the drill string as it moves downhole. It integrates predictive models with a near-real-time data stream through a WITSML feed, as well as parallel computing capabilities, so it can update the digital twin during drilling while predicting potential dysfunctions downhole.
Users can build a workflow that automatically recognizes drilling rig states and records quantifiable drilling parameters like shock and vibration, downhole MSE and ROP in near-real time. These events then act as cues for the predictive model. For instance, if predicted bit RPM, downhole MSE and ROP reach a certain threshold indicative of stick/slip, the predictive model will alert users of a potential incident. The model then runs a simulation, known as a “drill-off test,” where users can adjust various operating parameters to see how it affects performance indicators and adjust them at the rig.
Mr Gandikota touted the system’s ease of use, noting that few inputs from the user are required. “As soon as you input the BHA, all you have to do is set up a dashboard. We’ve tried to make this more visual and easier to map with the real-time surface data. At the end of the day, once you’ve installed it, it becomes a routine process. All the information is standardized. All you have to input is what type of bit you’re using and what type of formation you’re looking at, and then you’re ready to go.”
In 2020, an operator in the Permian used the software to improve its drilling operations. The operator was experiencing high frequencies of lateral shock, where the lateral motion of the BHA reaches a high enough amplitude to force the BHA to bounce against the wellbore. This was occurring whenever ROP reached 100 ft/hr, so the operator used the digital twin to examine how it could increase ROP while keeping lateral vibration low.
The predictive model analyzed instances of lateral shock as ROP approached 100 ft/hr, and the operator chose to test the impact of WOB and top-drive RPM on ROP and lateral vibration. The model then ran two optimization scenarios in a drill-off test, one in which the WOB was increased in 10% intervals from the initial WOB measured at the 100 ft/hr ROP, and top-drive RPM was decreased, also in 10% intervals.
As WOB was increased, the ROP increased from 100 ft/hr in the initial scenario to 160 ft/hr in the first optimization and 190 ft/hr in the second optimization. The operator used lateral shock counts above a threshold to indicate severity in vibration over a time interval. In the initial measurement at 100 ft/hr ROP, the model measured 40 lateral shocks. It then predicted 37 lateral shocks in the first optimization scenario and 24 lateral shocks in the second scenario. The operator was persuaded to increase WOB and decrease top-drive RPM to help increase ROP and reduce lateral shocks.
The digital twin platform is currently being used by two operators and two directional drilling companies, all in the Permian Basin. Two drilling contractors are also trialing the platform ahead of potential full-time deployment on their rig fleets later this year, according to Mr Gandikota. DC
Click here to watch a video with MindMesh’s Raju Gandikota discussing the company’s digital twin.